Introduction: Back to the Future Flux Capacitor
I’m a huge Back To The Future fan and have watched all the movies many times.
A little while ago I called into a `pop culture’ shop about an hours’ drive from where I live. These types of shops sell all sorts of memorabilia from TV shows and movies, some of which I use to watch as a kid. Shows like Lost In Space, Voyage To The Bottom Of The Sea, Thunderbirds, Batman and of course Back To The Future.
While strolling through the shop I noticed a new addition to the BTTF section – a full scale model of the flux capacitor. It was fairly impressive, but it just had that `manufactured by the 1,000’s’ look about it. What was more impressive however, was the price tag of $600!
My hobbies are tinkering, DIY projects and making things, so I decided to make my own Flux Capacitor because there was no way I was paying $600. After doing some research on the Net I came across quite a good Instructable on how to make a Flux Capacitor and found some links to other sites that were useful as well.
Supplies
I have attached three files here:
DRAWING SET.pdf contains fully dimensioned drawings for all the parts that I made, along with assembly details.
MATERIAL LIST.pdf is the materials list, including suppliers.
RELAY LABEL.pdf contains 4x labels that you can print full size (with one extra just for good measure!).
Step 1: The Enclosure
During my research I found out that the enclosure is a Stahlin J1210HPL and on their website these cost around $170 + postage. I did find them on another site for around $130, but I decided to make my own enclosure instead. I downloaded the spec. sheet and created my own drawing from that. Any unspecified dimensions on the spec. sheet could now easily be determined from my drawing.
The Enclosure is basically a deep, rectangular box with two small mounting flanges top and bottom and a wide `boss’ all around the front face.
To make the Enclosure I cut the shape for the back panel from 6mm MDF. The four side panels are cut from 3mm MDF and fixed into position on the back panel using PVA adhesive. For extra strength I fitted 12 x 12mm mouldings all around the inside of the side panels.
The boss on the front face is made from pieces of 20 x 8mm moulding. All outside fillets can be achieved with careful sanding, and to get the inside fillets I applied some ready-to-use multipurpose filler with my little finger. You can then sand the filler with a piece of sandpaper wrapped around a dowel with a slightly smaller radius. It’s amazing how good the inside fillets look using this method!
In each corner of the enclosure is a square of 12mm MDF with a Ø6mm hole in it. On the other side is an M5 nut which gets fixed into a counterbored hole (concentric with the Ø6mm hole) with two-part epoxy adhesive. These are to hold the backing board in position.
The lid front face and sides are made from 3mm MDF. The corners are shaped from solid blocks of pine and all are fixed in position using PVA adhesive.
The paint colour used for the enclosure is `Battleship Grey’ and after much searching I found a brand of spray paint called `IronLak’ at Officeworks (www.officeworks.com.au) that had a colour called `Battleship’. It’s actually really good quality spray paint - and only $6.99 a can! I also found the same spray paint at an art shop called Eckersleys (www.eckersleys.com.au), although it was $9.99 here.
The enclosure and lid then received 1 coat of undercoat and a few coats of Battleship.
The rubber gasket that runs around the face of the boss is made from 4 flat strips of rubber 1.5mm thick. To achieve the outside radius on the rubber I simply used scissors and for the inside radius I used a leather punch.
Fitting the window & rubber seal
The window in the lid is cut from 3mm thick Perspex sheet that I bought on eBay and is about 3mm smaller all around than the cut out in the lid. Fitting the rubber seal and the window into the cut out proved to be very tricky indeed and took quite a while. I actually had to do it twice because on the first attempt I cut the rubber seal about 5mm too short. The next problem was that the rubber seal didn’t take too kindly to being shaped around such a tight corner, so it buckled quite a bit. To solve this problem, I heated the rubber with a hairdryer to make it more pliable. I then used some masking tape to push the rubber down while it was hot in order to remove the buckling. I had to repeat this process no less than 5 times to completely iron out the buckling.
Hinge
The hinge for the lid is a bit of continuous hinge I had left over from a toy box I made. I just had enough to cut two equal lengths of 100mm. The hinges are fixed in position using contact adhesive, as there was is not enough clearance between the lid and the box for screws or rivets. The hinges cannot really be seen anyway.
Catches
The catch I used was an over centre fastener that I found in Bunnings. Like the hinges there is not enough clearance for mounting screws, but because the catches are visible, I cut the heads off some screws and glued them into the mounting holes of the catch just to make it look realistic.
Step 2: Relays
Relay Base & associated components
The relay bases are Ø49 x 30 thick and I guess I could’ve bought a Ø50 hole saw and cut these out from a block of pine or something, but I didn’t want to buy a Ø50 hole saw just for a one-off. Instead, I made the relay bases by laminating 2 x 12mm and 1 x 6mm blocks of MDF together and cut the circular profile roughly, then sanded them smooth using my drill press as a lathe (well, it works!).
The Relay Saddle and the Saddle are made from a 1mm thick strip of aluminium. Bending the Relay Saddle into the required shape was a little bit tricky, and I had to make a special jig to do this. Bending the Saddle to shape was a much easier task.
I used gold coloured spray paint to finish the Relay Bases and Saddles.
To fix the Relay Saddle to the Relay Base I used a countersunk screw which was sprayed with the gold colour. To fix the saddle in position I used PVA adhesive.
I bought the Binding Posts from Jaycar (www.jaycar.com.au) and cut the ends off them so that they could be fixed to the relay base with PVA adhesive.
The wire clip is just Ø1mm copper wire carefully formed then sprayed black.
Tube Assemblies
I spent some time sourcing the Perspex tubes and eventually found a supplier that would sell me such small lengths of tube. I already had some leftover Ø12mm Perspex rod in my bucket of bits, so this came in handy. All the other components, including the Perspex sphere I bought at www.smallparts.com.au , which is a site that I have used a lot for other projects. It seriously has everything that you could ever need to keep your project moving.
I cut all the Perspex tubes to size and rounded the edges where required using fine sandpaper.
I read on another Flux Capacitor Instructable that you can `polish’ the cut surfaces of Perspex and bring them back to clear. The way to achieve this is to firstly sand the surface with extremely fine sandpaper, then polish using special plastic polish. Specific plastic polish like `T-Cut’ was specified, but I decided to try `Silvo’ – silver polish that gets the tarnish off all your old silver cutlery that you inherited from your Grandma!
It certainly took some doing, but constant polishing with Silvo did bring the cut edges back to scratch free and clear - as if they were never cut. I thought this was amazing!
The perspex spheres have a flat on three sides and this took a bit of careful sanding to get them all to be somewhat perpendicular and parallel with each other. There is also a Ø3 hole drilled halfway into the sphere on one of the flat faces and I had to make a jig in order to drill these holes in the centre.
The support post is a short length of Ø12 perspex rod and fits into the centre hole of the Relay Base.
All the items for the Tube Assemblies were fixed together using Loctite.
I drew the Relay Label up in my CAD program and printed it out on normal photocopy paper, then laminated it with clear contact. To fix the label onto the Relay Base I used some double sided sticky paper that I got from Lincraft (www.lincraft.com.au).
I was very happy with the way the Relays turned out.
Step 3: Light Blocks
These are made from 12mm Perspex and have 4 blind holes drilled on the underside that line up with the LED’s in the backboard. Both sides only are sprayed with an aluminium colour.
Step 4: Spark Plug Leads
The spark plug leads connect to the top of the Relays and, as I discovered during my research, are Accel 3009 Yellow and Orange right angle leads. These were fairly expensive, so I checked out Supercheap Auto (www.supercheapauto.com.au) to see if I could find something similar. I found some Bosch right angle leads that looked pretty good – I just had to spray them yellow and orange!
To fix the Spark Plug Leads onto the Perspex spheres I cut a small length of the Ø12 tube that I had left over from the Tube Assemblies and pushed that into the lead. I did it this way because it was a very tight fit and I didn’t want to risk damaging the relays if I had to push the lead onto the tube if it was already in situ on the relay.
To complete the leads, I masked them up and sprayed with yellow and orange paint.
Step 5: Installing LED’s and Wiring the Backboard
The Backboard is the part that holds all the components and is made from 3mm MDF and sprayed with Battleship. It is held in place with 4 M5 screws and washers that I also sprayed with Battleship.
The light circuit consists of 3 branches of 5 chasing LED’S – 4 in each light block and 3 in the centre. I started looking around on the net to find a circuit for a 5 LED chaser and eventually discovered that a 10 LED chaser circuit could be reconfigured to chase any number of LED’s 1 through 10.
I looked on eBay and found a 10 LED chaser module for dirt cheap. In fact, I bought 3 modules because I wasn’t sure whether the output of the 4017B could drive 3 LED’s. These 3 kits, with postage, cost $3.74, and this included the circuit board! If I was to buy all the components separately from the local electronic supplier store this would have cost $100!
I constructed one module and found that each 4017B could in fact drive 3 LEDS, so this was good, and instead of reconfiguring the circuit to make it a 5 LED chaser I just used every second output of the 4017B to drive my LED’s.
The LED’s in the module were red, but I needed white for this project, so I looked on eBay and bought a packet of 25 cool white LED’s for under $10!
The wiring on the backboard isn’t pretty, but it didn’t really matter. I secured all the LED’s and wiring in position using a hot glue gun and mounted the LED module on standoffs using 2 part epoxy.
Now, I had been thinking about how to turn the Flux Capacitor on and off, and I was hoping to install a switch on the back of one of the 90° elbows, but the wiring would be visible. I found a tiny little slide switch in my box of bits, so I carefully made a cut out for it in the bottom of the enclosure and painted it with Battleship so it would be as inconspicuous as possible. I fixed the 9V battery in the enclosure with double sided tape.
Step 6: Final Assembly
The Light Blocks were fixed into position on the backboard using 2 part epoxy and for the Relays I used PVA adhesive. The small tube that I had already installed in the spark plugs was fixed onto the Perspex spheres using Loctite.
There are 3 text labels on the Lid that are printed with a Dymo label maker, but I really didn’t want to buy a label maker and the label material just to print out 3 labels. I did a bit of searching on line and to my astonishment I actually found a label set on eBay for about $22 (including postage)!
The two 90° elbows were sprayed with an aluminium colour and then fixed to the enclosure using 2 part epoxy.
It’s taken me about a year to finally complete my Flux Capacitor project. It was very enjoyable to make and I’m really happy with the way it turned out.
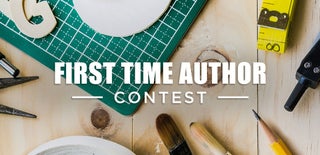
Participated in the
First Time Author Contest