Introduction: Bespoke Shoes
This guide summarizes the process of making entirely bespoke shoes; from creating a last, to pattern making, to assembling the shoe. This guide isn't designed to show you how to make a specific type of shoe, but rather serves as a general guide for the footwear making process.
Step 1: Tools and Materials
Tools
Sewing Machine or Sewing Awl
Tracing Wheel
Fabric Scissors
Flat Nose Lasting Pincer
Skiving Knife (or similarly sharp blade)
Hole Puncher
80-Grit Sand Paper
Materials
Most of the material choices for the upper are dependent on what shoe you are attempting to create, which is addressed later. As for the sole of the shoe, you'll need.
Smooth-On polyurethane rubber
All Purpose Rubber Cement
Step 2: Creating a Last
A last is a mechanical form that approximates the shape of the human foot. The last provides the shoemaker the basis for building the shoe around. Thus, the first step to making bespoke footwear is to obtain an appropriate last.
Lasts are specific to the type of shoe being created. As an example, a boot last is typically taller and built to create a closer fit than a sneaker last. It's important to determine the type/style of shoe before purchasing or creating a last.
While classical lasts are made of wood, modern lasts are typically made of a high density recyclable plastic. Lasts may be purchased online, but additive manufacturing offers an alluring option for those with 3D printers available to them. Various lasts are available online for free use. This is made doubly beneficial for those with CAD experience as the lasts can be customized via software such as Autodesk Fusion 360.
Image 1A is a render of the last model in Fusion. Image 1B is the physical print.
Step 3: Understanding Shoe Construction
Shoe construction is an intricate process, further complicated by various construction methods and industrial equipment not available to custom shoe makers. Deconstructing shoes is a great means of learning about all the different components used, and their purposes. By breaking up a shoe into its individual parts you can learn how the shoe was assembled and what components may be simplified to eliminate steps from the construction process.
Used running shoes, which can no longer be used, are a good possible option for disassembling. The first image above shows the general grouping of shoe components upon disassembly. The lower two images show two lengthwise cross-sections of oxfords. Note the variances in lining, padding, and stitching.
Step 4: Selecting Materials
Different shoes, and different parts of shoes, call for different materials. While you can purchase materials online, a well stocked fabric store will most likely carry the leathers, such as suede and nubuck, and the synthetics, such as neoprene and polyester, that you need. Getting material samples allows you to see/work with the material outside of the store prior to making a purchase.
You'll also most likely need to purchase the structural components of the shoe. This includes toe puffs, heel counters, and cellulose board. While these components aren't seen, they provide support and structure to the shoe shape. A local shoe repair shoe may also have these components for direct sale.
Step 5: Sketching
The first step in determining your design it to create 2D sketches. You can find useful reference pictures from footwear design books and websites such as Pinterest. Profile and overhead views will allow you to envision your design. In this process, think about how each component is sewn together and how the components will interact with one another in motion.
Step 6: Pattern Making: Part 1
To transform your 2D drawing into a three dimensional form you will need to translate your sketches into 2D patterns which will collectively form your shoe upper. The picture above illustrates the process of taping and sketching on the newly wrapped last. Ultimately the new tape wrap is removed from the last and separated into individual components.
Step 7: Pattern Making: Part 2
Using masking tape from your local art supply or hardware store, begin taping your last. Start from the heel and use the tape to cover the last from heel to toe. Lay the tape as smooth and flat as possible, overlapping half the width of the tape as you move downward. Use a ruler or a flat instrument to smooth the tape over the curved surface of the last. Mark a straight line along the length of the last and use that to define the center of the last. After that, start to transfer your 2D side view to the taped last by sketching directly on the newly wrapped last. As long as your shoe is symmetrical lengthwise, you'll only need to create the pattern on one half of the last.
Step 8: Pattern Making: Part 3
Use an X-ACTO knife or a box cutter to separate each part of your design and then peel the tape off the last. Tape each part of the design onto a piece of stiff pattern paper or a manila folder. Remember to leave 1/4 to 1/2 of an inch offset from each pattern part for sewing allowance. Leave approximately a 1 inch offset for all edges that will connect to the bottom of the last.
Step 9: Sewing and Lasting
Use a silver pen or fabric pencil to transfer your paper pattern to your upper and lining fabric. If your design has a stretchable lining, than cut each piece slightly smaller than your appearance fabric. Follow the shape previously drawn for sewing and be patient. Before you sew each part together, use rubber cement to glue two edges together of the part. Let them dry and sew them together on your sewing machine. Go slowly and make sure each stitch goes through both pieces. The sewing process can be accomplished by hand but doing so requires a sewing awl and takes significantly longer.
After sewing all the parts together, place the lining and leather upper on your last. Use your footprint pattern to cut out an insole board from the cellulose board. Use nails to secure the insole board to the bottom of your last. The shoe lasting process takes time to ensure your fabric is smooth with no overlapping. Nail the lining as shown in the pictures above and place permanent glue to adhere the lining to insole board. Hammer it down, then repeat the same process with the leather upper.
Step 10: Lasting Continued
The picture above shows some of the tools I used for lasting the shoes. If you don't have access to professional lasting tools, a hammer and a pile should also do the job. Sand the excess material on the bottom of the last and fill the gap using cork sheet until the bottom is flat and smooth. Make sure the glue is dry and then push both pieces together. If necessary, you can put weight on the last to ensure adhesion.
Following the lasting process remove the last from the shoe. If your last has a hole through the top, this is best accomplished by using a metal rod as a lever to pull the last from the shoe.
Use the leather hole punching tool to punch eyelet holes and stitch on any external components as necessary.
Step 11: Creating a Sole
There are as many ways to create the sole of the shoe as there are to create the shoe itself. I wanted to exhibit a way to create a fully custom sole without utilizing high cost machinery or carving polyurethane foam by hand. To achieve this, I created a sole model in Autodesk Fusion 360 based on the dimensions of my 3D printed last. This is best achieved by taking general dimensions from an already existing sole. I then 3D printed the sole to check the dimensions of it relative to the shoe. After ensuring that the dimensions were appropriate I created a reverse mold in Solidworks, and 3D printed it.
I then used a pour-able polyurethane from Smooth-On and cured the sole in a vacuum per directions. Following the curing process, remove the sole from the mold and cut/sand away any artifacts of the molding process.
Given the inherent difficultly of this process, using a donor sole from another shoe or purchasing a new sole are also good options.
Step 12: Joining the Upper and Sole
Using liquid cement or an equivalent adhesive, apply the adhesive on the open faces of the upper and sole near the heel. Apply the adhesive to 1/4 the length of the shoe at a time, allowing the adhesive to partially dry as you move forward. Prior to allowing the adhesive to fully dry, check along the edges of the upper to see if you missed any spots throughout the process; apply more adhesive as necessary.
Congratulations, you've just assembled a complete bespoke shoe.
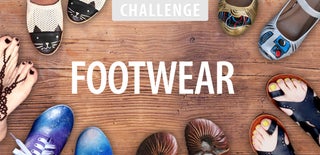
Runner Up in the
Footwear Challenge
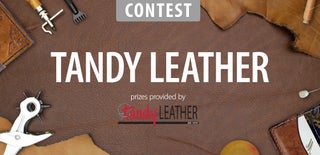
Participated in the
Tandy Leather Contest 2016
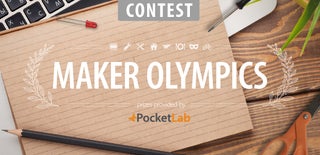
Participated in the
Maker Olympics Contest 2016