Introduction: Birdcage Awl
An Awl is a super useful tool for starting or marking holes in wood and can be as simple as a sharp point on an old screwdriver. There are however some better options such as the 'Birdcage Awl' which has a square design to the shaft, this allows you to even drill holes with the Awl by twisting it. It's called a Birdcage Awl because people used it to drill holes in sticks to make bird cages.
You may not be planning to make a bird cage but it's a super useful little tool that's very easy to make. It only took me about two hours to make two of them including stopping to take photos etc...
The diameter of the screwdriver shaft is the size of the hole it can drill, so feel free to make a few different sizes.
Supplies
- Old Screwdrivers
- File
- Sandpaper
- Gas torch or Fire
- Grinder (optional)
- Drill (optional)
- Lathe (optional)
- Expoxy Glue (optional)
Step 1: Prepare the Metal Shaft
You don't have to use an old screwdriver, it was just the easiest and cheapest way for me to get a couple of different size shafts that are decent-quality metal.
If you want to keep the existing handle that's fine, just skip straight to the grinding step. Though due to the hardness of the steel you probably won't be able to file it.
I recommend making a custom handle if you can because you can shape it to be a little bigger to fit your hand better.
I started by sawing off most of the old plastic handles and then knocked the remainder off with a small hand axe. I then softened the steel by heating it red hot with a gas torch and allowing it to cool slowly. If course if you don't have a gas torch you can just put the screwdriver into a fire.
Once the metal has cooled down give the shafts a light sand to remove any old rust or flakey chrome.
Step 2: Shape the Shaft
Use a grinder to shape the end of the shaft into a tapered square. If you don't have access to a grinder you can do this entirely with a file just as long as you softened the steel in the previous step.
Regardless I like to finish off the Awl with a file as you have more control over the shaping of the final tip. If you look carefully at the photos you should be able to see that the angle of the taper changes at the tip into a much steeper angle. This steeper angle makes the tip stronger and less prone to bending, however the Awl is designed to be quickly sharpened with a file anyway.
Step 3: Adjust the 'flare'
Assuming you used an old screwdriver shaft you can expect to find a 'flared' part of the shaft that is designed to stop the shaft spinning inside the handle. At this stage we are just going to grind an small angle on this to make it easier to drive into the new handle
Step 4: Make a Handle
I used my home-built mini-lathe to turn a simple handle, I added a small section of some old aluminium tube to prevent the handle from splitting. You should be able to notice that the shape of the handle it shorter and wider than a screwdriver, this is to make it fit comfortably into the palm of your hand while you push and twist it into wood.
Now measure the shaft of the Awl and drill a hole the same size or slightly smelling into the handle.
Step 5: Fit the Handle
Measure how deep you drilled the hole into the handle and mark this on the shaft with a small piece of tape.
Mix up some 5-minute epoxy glue and using something thin smear it around the inside of the hole and along the shaft of the Awl. Now clamp the Awl shaft into a vice and gently tap the top of the handle with a mallet until the shaft is fully seated inside the handle.
Wipe off any glue that oozed out and remove the tape you used to make the depth of the shaft.
Step 6: Finish the Handle
Apply a coat of linseed oil to the Awl or if you prefer you can varnish it. You should still lightly oil the shaft of the Awl to prevent rusting.
I also decided to come back and add a few coats of varnish, I think it really finishes them off nicely.
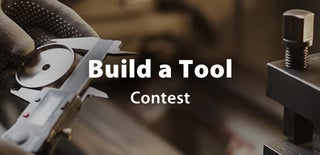
This is an entry in the
Build-A-Tool Contest