Introduction: Black Ram Hand (Robotic/Prosthetic Hybrid)
The Black Ram Hand was designed not to be a replacement for current prosthetic hands, but to be an assistive technology tool/platform for allowing someone to design and use their own specific manipulators for individual tasks specific to that person. This is in the same way that Robotic grippers and end-effectors are designed for a specific goal. I designed this hand for the 2016 3D Printing Competition. As the competition is about 3D printing I designed with this in mind. Except for the Velcro straps, all parts are 100% fully printable (including bolts and nuts).
The Black Ram Hand is designed to help those with missing fingers. It is wrist powered and requires that the wearer have enough palm to push against the device. It converts the rotation of the wrist into a linear sliding motion to activate the end gripper. When the wrist is bent down the slider pulls back, closing the hand. When the wrist is straightened the slider pushes forward and the hand opens.
The Gripper heads are removable so that the user can change them and reconfigure the device to suit their needs. I have created 2 Claw types, Tri-Claw (for picking up or catching objects) and Two-claw (for open shut grasping of objects). New claw or manipulator types can be attached with 2 screws on the hand piece. Within these you can add any flavor of gripper suitable. I have added a few grippers as extras for people to try. I recommend that you start with the Simple Claw to get the feel of the device before printing the other variants.
The multi-joint finger requires the user to tune the fingers. There is a sequence of loose and tight bolts that needs to be determined to allow for the correct articulation of the fingers when opening and closing.
If anyone has the chance to print it out and give it a try I would love to hear your feedback on how it can be improved and updated. The design could be much smaller and more secure with the use of metal bolts which would be part of future design versions. Feel free to use the CAD to design your own gripper or claw which can suit your needs, I look forward to seeing your results.
Step 1: 3D Printing
I have printed all my parts for the Black Ram Hand in PLA and have tried to optimize the fit, clearance and tolerances for this material. I used the following settings in Cura for my prints:
- 3D Printer - FABtotum
- Material: PLA
- Layer Height - 0.2 mm
- Shell Thickness - 0.7 mm (Nozzle: 0.35 - 2 Shells)
- Top and Bottom Thickness - 0.8mm
- Fill Density - 15% (IMPORTANT NOTE: For Bolts and Nuts use 30%)
- Filament - 1.75mm
- Support Type - Everywhere
- Platform adhesion Type - Raft (IMPORTANT NOTE: For Bolts and Nuts use brim)
I have used a starting temperature of 210 Deg C for the first 2 layers of my raft and then drop the temperature down to 195. This suits my machine well however you should use the best settings for your 3D printer. I have used a 0.2mm Layer height to reduce the build times of my prints. I have not used retraction as my 3D printer has issues with this function.
My 3D printer is not very good at keeping within tolerances due to its design and age. If you have issue with the fit of the parts in your assembly (too tight), then I suggest giving a light sand or file (as seen in the picture) on the sections where the parts interface.
I recommend that you print the bolts and nuts individually (unless your retraction function works well). This will allow for a well formed threads. It may be tedious but you will get a much better result on your assembly. Also the FILL Density should be at least 30% on Bolts and Nuts to make them strong and able to handle tension.
Refer to each individual assembly step for the STL files for Printing.
Step 2: Assembly of Hand and Gauntlet
This is the base assembly for the Black Ram Hand and is used on all variations.
For this you will need to 3D Print following parts:
- 1 x BRH5-Hand - This is the large piece that will fit over your hand.
- 1 x BRH5-Gauntlet - This is the large piece that will fit over your forearm/wrist.
- 1 x BRH5-Tendon - This is the central long piece that activates the slider mechanism.
- 3 x BRH5-Bolt - These are the assembly bolts.
- 3 x BRH5-nut - These are to secure the bolts.
- 1 x BRH5-tool - This is a small assembly aid tool for the bolts (the handle is hollow inside).
To complete the assembly you will also need:
- 3 x Velcro strip - The assembly accommodates Velcro strips as wide as 28mm (opening is 30mm). You will need enough strip on each to wrap your palm or arm.
Assembly:
- Slide Together the Hand and Gauntlet Pieces and align the bolt holes.
- Insert the bolt from the outside into the aligned bolt holes and insert the nut on the inside.
- With your finger on the nut, use the printed tool to tighten the bolt.
- Repeat for the other side.
- Slide the small side of the tendon into the gauntlet center bolt hole.
- Insert a bolt through the aligned holes and cap with a nut.
- With your finger on the nut, use the printed tool to tighten the bolt.
- Flip the assembly and slot the Velcro through the slots so that the soft side faces you and will touch your palm or arm (It is best to start will a much longer piece of Velcro and then trim the excess off when fitting).
- Repeat for all the shown slots.
Step 3: Assembly of Simple Claw (Pinch)
This is the Simple Claw (Pinch) assembly for the Black Ram Hand
For this you will need to 3D Print following parts:
- 1 x BRH5-Tri-Claw - 3 fingered claw base component.
- 1 x BRH5-Tri-Claw-Slider - Sliding mechanism for the Tri-Claw.
- 9 x BRH5-Bolt - These are the assembly bolts.
- 7 x BRH5-nut - These are to secure the bolts.
- 3 x BRH3-pinch_finger - Simple curved claw/fingers.
Assembly CLAW:
- Slide the Tri-Claw-Slider into the Tri-Claw center hole.
- Rotate the Tri-Claw-Slider so that the shaft hole is in the orientation shown in the picture (this needs to align with the Tendon on the final assembly - in the same orientation as the top claw bolt hole).
- Insert the pinch-finger into the slot aligning the Tri-Claw and slider. On the Pinch-Finger the SLOT must be aligned with the Slider and the Hole must be aligned with the Tri-Claw. SLOT-SLIDER & HOLE-TRI_CLAW.
- Insert Bolts though both holes and cap with the nuts (Use the tool to tighten - Do not over tighten).
- Repeat for all Pinch-fingers.
Assembly CLAW to HAND & GAUNTLET:
- Align the Tri-Claw Rail holes with the Hand piece holes.
- Insert one bolt on each side (the Hand piece has threaded holes so there is no need for nuts).
- Align the Tendon Bolt hole with the Slider Bolt hole
- Insert a bolt and cap with a Nut.
Step 4: Assembly of Two-Claw (Pincer)
This is the Two-Claw (Pincer) assembly for the Black Ram Hand. I designed these grippers to hold my favorite coffee cup.
For this you will need to 3D Print following parts:
- 1 x BRH4-Two-Claw - 2 fingered claw base component.
- 1 x BRH4-Two-Claw-Slider - Sliding mechanism for the Two-Claw.
- 7 x BRH5-Bolt - These are the assembly bolts.
- 5 x BRH5-nut - These are to secure the bolts.
- 2 x BRH5-gripper_finger - Center curved robotic grippers (Designed for my favorite coffee cup).
Assembly Pincer:
- Slide the Two-Claw-Slider into the Two-Claw center hole.
- Align the Two-Claw-Slider so that the shaft hole is in the orientation shown in the picture (this needs to align with the Tendon on the final assembly - in the same orientation as the Two-claw bolt holes).
- Insert the Gripper-finger into the slot aligning the Two-Claw and slider.
- On the Gripper-finger the SLOT must be aligned with the Slider and the Hole must be aligned with the Two-Claw. SLOT-SLIDER & HOLE-TWO_CLAW.
- Insert Bolts though both holes and cap with the nuts (Use the tool to tighten - Do not over tighten).
- Repeat for Second Gripper Finger.
Assembly Pincer to HAND & GAUNTLET:
- Align the Two-Claw Rail holes with the Hand piece holes.
- Insert one bolt on each side (the Hand piece has threaded holes so there is no need for nuts).
- Align the Tendon Bolt hole with the Slider Bolt hole.
- Insert a bolt and cap with a Nut.
Step 5: Assembly of Multi-Joint Claw (Adjustable)
The Multi-joint claw is much harder to operate and assemble than the Pinch and Pincer Claws. It is adjustable to open the fingers to grab small and large objects, but you must tune the bolts to apply less or more tension on specific joints for it to operate correctly.
For this you will need to 3D Print following parts:
- 1 x BRH5-Tri-Claw - 3 fingered claw base component.
- 1 x BRH5-Tri-Claw-Slider - Sliding mechanism for the Tri-Claw.
- 15 x BRH5-Bolt - These are the assembly bolts.
- 13 x BRH5-nut - These are to secure the bolts.
- 3 x BRH5_Tri-finger_a - Center Finger Piece
- 3 x BRH5_Tri-finger_b - Outside Finger Piece
- 3 x BRH5_Tri-finger_c - Finger Tip
Assembly Multi-Joint Claw:
- Insert the Tri-Finger_a Slot into the Tri-Claw Slider Bolt Hole. Ensure that the flat face is facing towards the center of the Slider.
- Insert Bolts though the bolt holes and cap with the nuts (FOR THIS JOINT LEAVE LOOSE).
- Repeat for all Tri-Finger_a parts.
- Insert Tri-Finger_c middle hole (with finger tip facing center slider) into Tri-Finger_a top slot aligning the top bolt hole.
- Insert Bolts though the bolt holes and cap with the nuts (FOR THIS JOINT LEAVE LOOSE).
- Repeat for all Tri-Finger_c parts.
- Insert Tri-Finger_b thin side into the Tri-Claw Finger Bolt hole.
- Insert Bolts through the bolt holes and cap with the nuts (FOR THIS JOINT APPLY TENSION).
- Repeat for all Tri-Finger_b parts.
- Slide the Tri-Claw-Slider into the Tri-Claw center hole.
- Rotate the Tri-Claw-Slider so that the shaft hole is in the orientation shown in the picture (this needs to align with the Tendon on the final assembly - in the same orientation as the top claw bolt hole).
- Insert the Tri-Finger_c into Tri-Finger_b aligning the Tri-Claw and slider.
- Insert Bolts though both holes and cap with the nuts (FOR THIS JOINT APPLY TENSION).
- Repeat for all Tri-Fingers.
Assembly Multi-Joint Claw to HAND & GAUNTLET:
- Align the Tri-Claw Rail holes with the Hand piece holes.
- Insert one bolt on each side (the Hand piece has threaded holes so there is no need for nuts).
- Align the Tendon Bolt hole with the Slider Bolt hole.
- Insert a bolt and cap with a Nut.
Step 6: Strapping In
For all variants of the Black Ram Hand the strapping is the same.
- Strap around the top of the palm of your hand.
- Strap around the wrist.
- Strap around the Forearm.
Once strapped in test to motion by rotating your wrist downward to close the gripper and upwards to open.
Step 7: Additional Grippers
I have designed some additional grippers to go with the Black Ram Hand.
1. The Ball Catcher
I designed the Ball Catcher after testing the Black Ram Hand with the Simple Claw and finding that it was not enough to properly catch and hold a ball. I added side flanges to ensure that a ball could not escape once caught. This gripper could also be used to hold rounded objects in a Two-Claw assembly.
Print 3 x BRH5-ball_catcher and follow the Simple Claw (Pinch) assembly Procedure.
2. Talons
I really design these to look cool. They have no additional function above the standard pinch Gripper.
Print 3 x BRH5-Talon and follow the Simple Claw (Pinch) assembly Procedure.
3. Fat Tips
These were designed to try and pick up smaller objects. The massive tips all come together to squeeze an object.
Print 3 x BRH5-fat_tips and follow the Simple Claw (Pinch) assembly Procedure.
Step 8: Assembly Files to Design Your Own Grippers - Requires CAD Experience
This section is only for those who have CAD experience I have attached an IGS file of the assembly so that you can design your own grippers or make modifications to the assembly to suit your needs.
I would love to see what you come up with or changes that you would make.
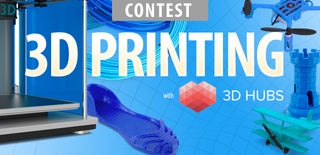
Runner Up in the
3D Printing Contest 2016