Introduction: Bo Peep's Skunk Mobile - Remote Control Plushy
A remote control car that drives a feminist angle. Bo Peep in Toy Story 4 is independent, smart, kind and really great fun, so I wanted her to join our 5yo son's toy collection - alongside her awesome Skunk Mobile. However, it doesn't exist as an official merchandise, so I converted it from a generic $20 RC car myself - and along the way found some interesting insights into why this was not as easy as you might think...
---
As well as being a proud Dad, I work as a Creative Technologist, I've run workshops and tutorials on cardboard modelling for years and won awards for making engineering and design more accessible to people - but the fact remains most of my commercial work is great but confidential - so I can't show as much of the process as I'd like.
This SkunkWorks Project (pun very much intended), was a nice way for me to have some fun when not working on top secret client work, and also share the steps of prototyping and sketch modelling that might help students, young professionals - and indeed, parents like myself who want to make things which they wish would exist!
The project was made possible after winning the IMechE's Alexander Graham-Bryce Award for 2020, (awarded for making a significant contribution to the encouragement of young people towards a career in engineering).
Hope you like it. Please leave comments/feedback/tips!
---
Part 1: Is the Backstory, and how to prototype in card, and fabric, use photos in CAD, basic 3D Printing tips...
Part 2: The Instructable (DIY guide) - just skip to Step 18 if you're in a hurry, and don't need the preamble!
Parenting & Prototyping
As someone who has worked in the toy industry (LEGO) / product industry (Dyson, Sugru), I saw at least two reasons why Bo's Skunk was, shall we say, 'tricky' [please note: views my own]:
Merchandise is a partnership between Story / Screen Writers and Marketeers, ideally one should elevate the other - making the play 'continue' after the film has ended for the child. Now, although a Bo Peep doll is as available, just as a Buzz Lightyear doll is also, it's worth noting that the Woody + Buzz + RC came as a Remote Control Car set from Toy Story 1, and yet the Skunk Mobile has not been made into a product from Toy Story 4.
I'm not going to speculate as to the internal decision making of Disney/Pixar, but safe to say I personally *wish* that the Skunk Mobile had been made, even if it is clearly more complex (plushy + plastic + RC vs just an RC plastic car), and even though my guess is that the market is likely to be smaller for a Bo Peep toy range than a Buzz Lightyear toy range, I believe we need more role models like Bo...for Boys as well as Girls.
Often there is a 'tension' that a Marketeer will be aware of that making x-thousand units is a high risk, low margin game - and so trying to get a sales bonus from a. Bo, or b. from Buzz, you can see who is likely to be the lower hanging fruit. So this in my non-expert opinion, but I'd wager that this is part of what makes it tricky to see more Skunk Mobiles from female characters. If we set yearly sales bonuses that have societal ethics decoupled from ethics - why should a sales person fight the tide? So... does this means it's only about 'top-down' leadership?
Here's a video of Disney's CMO - Anna Hill speaking about the importance of female characters. (Although I should note that it's currently Mattel who have the license for the Pixar Merchandise - FT Article here). So, whether you share this or create your own toys perhaps making your own Pro-Bo toy, or posting on Social Media is also as impactful, perhaps more so - as if your idea gains traction, this is in essence reassuring Disney/Pixar/Mattel that the people want more of this: Marketeers are made braver and screen-writers bolder, when they see people's views (and wallets) moving in a direction in significant numbers.
In short - your 'vote' counts. The two things are connected. Help support the things you want to see more of. The change might seem too little too late for some, but inside these companies women and men will be fighting against the status quo like you'd never believe for a few percent more female:male dialogue, slightly less pink and better narrative / nuance. Having met some of these people, they are passionate, dogged and driven people, but it needs you, the consumer to validate their efforts.
~
OK, overly-simplistic overview of marketing, and earnest liberal views aside - the other fact we should come back to is the cost/margins/complexity. What I love about this project is that it really does illustrate how making a Skunk Mobile is possible - but is also tricky! So without defending or apologising for there being a relative lack of cool female-role-model merchandise, it is fair to say that making a plastic RC car is relatively tried and tested, but cloaking it in fur (and making it flip open!) is quite another matter...
Also, if you look closely at the film, you'll see how Pixar applied a little 'distortion' the interior space to fit all the characters, and this is not realistic in real life...more on this later, but safe to say, I had to work with the idealised on-screen view, and what would work in reality. This is why we need to prototype a better world for Bo (and your kids), and this is why it's gonna be fun to make yourself, with your kids... or enjoy being a big kid again!
I also got some tips and advice from a few kind folks along the way:
Textile & Animation Designer: Angela Juarez
Maker at TESTED: Sean Charlesworth
Thanks to you both!!
Disclaimer: This instructable is intended for adults to follow and/or supervise, as it uses tools, adhesives and electricity - and the end result is not a certified toy. Should you wish to make it for someone (child or adult), please do be aware you have created something with small parts, potentially sharp edges, batteries, and something which might cause direct/indirect harm if misused, or used in some unintended way. I have endeavoured to highlight any potentially dangerous or notable risks along the way, but I cannot accept any responsibility for any harm that comes to the maker or users as a result of following this guide. Views my own. Legal bit over, hope you enjoy reading this Instructable! Any advice or general questions - please comment/DM me =)
Step 1: Essential Purchases
As can bee seen, I have 'kit-bashed' or 'frankensteined' a RC Car to carry a 3D Printed armature, which is covered in faux fur. The following are the key purchases you'll need:
Remote Control Car:https://amzn.to/2TbAUE6
(the exact model may not be in your country - but try and get one that looks very similar - the useful fact to know about 'Make in China' is that there are likely just a couple of generic RC Car *chassis*, and loads of different coloured 'cabs' stuck on top, so chances are - as it's generic, and will fit. Do share a link if you strike gold. Thx.
Access to a 3D Printer (or a friend with one!)
I use an Ender 3 - 3D Printer: https://amzn.to/3xEn3oD and ERYONE PLA Filament: https://amzn.to/36y3TF8
Toy Story Bo Peep (in set): https://amzn.to/2T5wHSa
Long Hair Faux Fur Fabric: ebay link (you can hand-stitch if now access to a sewing machine).
Later on in the guide I also list the other parts and tools that you may have in a workshop, or should consider investing in (good news - not really expensive tools, just basics!).
In case you need to know the rough cost upfront:
Car ~£16/$20, Fur ~£12/$15, Fixings ~£8/$10, 3D Printing Filament ~£3/$5.
So assuming you have most of the tools (pliers, drill, saw, scalpel, ruler, lighter, etc.), it'd guess the project is about £50/$65 to have a unique toy!
It's also worth noting, that the RC car can be easily changed with just 4 screws, so potentially you could make multiple furry RCs. I have a inclination to re-create Dumb & Dumber's dog car...
Step 2:
Step 3: Skunk Research & Pixar Perspective
In the movie Bo's Skunk Mobile is a 'so overt - it's covert' means of getting around undetected as a toy. The Skunk is so well known and feared for its stinky spray, that in America most people will instinctively run away (without looking more closely at the RC toy) - clearing the way for Bo to 'drive' through the crowd!
Whilst googling to see if this had been done already (at time of writing, not as Merchandise) - I suspect that the Pixar team were inspired by Tom Mabe's version, as this pre-dates the movie (even factoring in pre-production times). So this may be the first DIY Skunk Mobile - woo!
I was watching the movie frame-by-frame again, and took screen shots of the profile and front of the skunk mobile. I especially liked that someone on Reddit pointed out that the nose/face was modelled from an Oil Can. You gotta love Pixar for these details, not to mention the blue glass 'eyes' stuck on it also!
Anyway, the great thing about CGI and Animation is that Pixar does not need to always obey Physics... This is why when you look at the scale of Bo + Woody + Billy/Goat/Gruff + McDimples', as well as the RC Handset + Scissors + Tape -- this would NEVER fit into the Skunk interior. Although this pedantry is uncalled for in the general enjoyment of the film, it is a real issue if you're trying to make a scale replica of a Skunk Mobile, which it turns out is physically impossible to make at the scale the movie implies!
The solution was to try and strike a balance between
a. what RC Car is readily available that can carry a fair weight of skunk plushy on it, and
b. that can also carry a Bo Peep doll, working with what is commercially available: a 9" doll.
Lastly, I have never made a plush toy before, but had done GCSE Textiles at school, and so can work a sewing machine (kinda), so seemed a good excuse to have a shot at this!
Step 4: Sketch Modelling Basics
As mentioned, I host a website on the subject of Design Modelling. I'm not going to re-cap everything here, but the techniques are all listed there in 1-3 min videos. Check out Techniques and Tips & Tricks in particular.
The key principle I used was to look at what was 'stable' in the chassis. I removed the 'cab' (4 screws), as shown in later steps, allowing me to build a cardboard 'base' on top. From this base I could explore the 'flip-open cage' as shown in the movie.
As mentioned, the movie rather conveniently does not depict Bo, Woody and the gang all getting in and out, and so for simplicity I focussed on Bo, as it is her Mobile after all! The essential dimension/arc was to avoid hitting her head whilst opening, and leave room for her legs, but avoid touching the tyres.
I made a simple hinge using ABS plastic tubes, which one fit inside the other. You could do this with drinking straws or even rolled-up paper. It does not need to be very durable - it just needs to help you understand the dynamics of the model, and of course ensure it's easy for the user to operate.
Although I've 'skipped' a lot of steps, the general principles in card are almost identical to the assembly in 3D printed plastic - so follow those, and you'll get the idea!
Step 5: Collision-Proof / Child-Realistic
After a couple minutes of imagining what my son would do with a Skunk Mobile, it's very obvious crashes will happen. Arguably a mix of accidental bumps, and pleasure in being allowed to 'total' a toy...so I figured adding some shock absorption would be wise.
To do this I simply used a few springs from an assorted spring set. LINK. (The sizes are ~9mm diameter, by ~35mm in length).
I had not made the 'Oil Can Nose' at this point, so you can see the rough shape made in card, was as much to test how the force would translate (ie would the springs fly off or not be strong enough, etc.)...all this makes sense to prototype, before spending 10x times longer in CAD, and much longer in print.
There are only a few occasions where I skip card modelling, and that is when the success of the prototype is dependent on precision, or a subtle mechanical movement/component/fit/etc. In most cases, if it works in Card it'll work better in Plastic.
Step 6: Bo's Ergonomics
In the movie, shockingly, Bo does not wear a seatbelt. Shame on you Pixar!!
Jokes aside, this posed a problem of how to secure Bo? I didn't want to just zip-tie her legs in, or seat her in BluTack, so the only option was to make a seat for her. The 'belt' was an elastic band, and perhaps, I'll make something more Nascar when I get a moment.
When creating a seat for Bo, it was actually more tricky thank I was expecting as she has wide hips and a slim waist...we can discuss later if this is fair anatomic representation / body positive, but from a prototyping perspective this has the effect of making my initial effort of a 'lap-strap' seatbelt not very effective - as her torso shifts too much when in motion. As with so much in Design - women need better representation in automotive design - be it real cars or Skunk Mobiles... If you feel like jumping into this rabbit hole and furthering your awareness, checkout Invisible Women by Caroline Criado Perez. It has some truly astounding research into how card design really is far from optimised for women's bodies. Possibly the most important book a designer could read right now, perhaps jointly with another favourite: Design for the Real World (link).
Back to the prototype: Attention to the open/close arc is key here, and arguably is slower to do in CAD - as often what looks good in CAD does not always feel good. Working in Card allows you to 'dial-in' the size and feel of things. Not to be underestimated. Aside from this, my son was not going to give feedback with my CAD, so Card was essential.
Step 7: Transport / Size-Reduction
I previously made a Card loop the loop, and seeing how large the construction was getting, I made it divide into quarters. This has been a useful consideration in my toy design, as one often has to tidy-up, pack-away, or carry toys (parent or kid), so making this efficient is worth doing.
In this instance, the tail was a big cumbersome thing, when not being driven. So making a quick 'socket' was a nice touch, and if anything, if I were to wager that some kid/friend will snap it, it means it can be easily replaced.
This was done with wooden dowel, and later was 'upgraded' to metal rods in the final version.
Step 8: Preparing to Go From Card to CAD
Once I was happy with the Card Model of the Skunk Mobile, I took pictures of it at top/front/side/etc. This was so I would have a reference in CAD by importing the images to use as a guide.
I covered how to do this in another Instructables, making a Hairdressing Tool. Or you can of course look up numerous tutorials of "how to import images into a sketch plane - in [your CAD software of choice]".
Disclosure: I'm very kindly sponsored by SolidWorks.
If you need help with some editing, please DM me and I can try and help out.
Step 9: Photos in CAD - a Guide to Iterate From...
This first image is the 'real world' picture of Bo sitting a the right angle.
The second is the image in CAD, on a sketch plane - with a model made 'on top' of it.
The third is the model only (sketch and photo 'hidden').
---
I then proposed to do similarly with the Photos of the Card Skunk Mobile. I took some care to assemble the 3 perspectives carefully on the planes, but when you try this don't worry if they don't line-up perfectly, as this is just a viewing error, as the camera sees perspective, but the CAD software has 'infinite perspective'. In either case, the trick here is to just be approximate - after all, this is a guide, not a plan.
I find that once I have worked on the first CAD model, and 3D printed it, one gains an affinity for what bits 'work' in Photos and what parts come out less accurately. As a rule, stuff in the middle of the picture has less distortion than the edges, etc. But once you've done this once you'll get a feel for how it works in practice.
Step 10: Keep It Blocky
Now you're ready to 'build upon' your Photos.
I felt it was worth showing the end result - but also the starting point: The Chassis.
I modelled the Chassis in very quick 'blocky' units. My goal was to be 'good enough' on stuff that didn't matter (ie not treads or hubs needed on wheels) but accurate on details like mounting points, and where the wheels would move with regards the suspension.
The 'red block' on top is where the maximum height of the cables inside the RC Car are. Unless I was working to a very high tolerance, I realised it was not important to model each wire, or even the PCB. It sounds obvious, but I've both made this rookie mistake of modelling too much detail too soon, and also mentored people to get a feel for what is the minimum viable detail in CAD. Hope this helps you be more selective...
Step 11: Testing in Real Life - RC Climbers Are Great!
One thing is for sure, CAD is all well and good, but plonking a bunch of Card on a RC Chassis and driving it around a bit is what matters most! It is also HUGE fun!!
It also served a key function - to ensure the RC car could handle the weight, but also that it didn't tip over all the time (I was aware the Skunk would make the toy more top heavy than the original product intent, so it needed to be tested). But it was also key to test with my son - and check he thought it was fun, and know what bits he likes best.
The irony was that even though the Skunk Mobile was slower than many fast RC cars my friend owned, he really enjoyed the 'animalistic movement', as the 'feel' of the Skunk was right. The tail wagged, the nose skimmed the ground nicely, the whole thing felt 'skunky' - and that's what matters. It also climbed some pretty serious slopes, and went on grass nicely.
The technical term for this type of RC Car is a 'Climber', as they are not super fast, but have high torque, and can climb steep things. This also means that when you can essentially 10x the payload, they don't give up, the way a more speedy direct drive motor would. Of course some direct drive RC cars would also handle a Skunk on top - but - they are more like $400+, rather than ~$20, as this one is!
Step 12: First 3D Prints
I perhaps picked this up from working with engineers - but I tend to fixate on the thing that 'scares/bothers me most', first...
This is a clear example, as the [ Chassis Mount x Flip-Cage x Seat x Bo Peep's Head ] is a key interaction to get right. I modelled it first in Card, and I printed this assembly first in PLA plastic too.
If you are using this Instructable holistically (ie for the tips, rather than to make a Skunk Mobile), I high recommend this approach. It's very easy to work on the fun bits first, but often you see more experienced engineers tackle the tricky bits head-on, knowing the rest is 'downhill' after that. As with any 'Rule', there are exceptions where I deviate from this (experience design being one), but generally it holds true.
Step 13: Prototyping in Textiles
You'll have noticed a theme here, in my work - prototype quick 'n' dirty - then do it better with more care, and the benefit of hindsight the second time.
I'm not an expert in textiles, so I needed to get an approximate fitting of the fabric. Although there are 3D tools like Pepakura which can create 'nets' from 3D shapes, these are rather 'academic', when dealing with something as unusual as a Skunk plushy, as Faux Fur does not behave like a simple 'surface' - as it both thick, and quite stretchy.
To get a first approximation, I used some old jeans that were worn out. I realised I regretted not washing them, as I was working closely with remnants from the unwashed seat of my jeans...hmmm.
You of course don't need to do this step, as I've done it for you, but I included a few pictures to show how it progressed, and how once I was more or less happy with the shape - I'd then unpick the pattern, and flatten it again, and then transfer to paper.
If you're looking closely - you'll see I actually used an office stapler to 'stitch' these pieces together, as it was quicker (and more adjustable) than sewing it and unpicking it. As I said - quick n dirty...and stinky.
"But Boys Aren't Supposed To Do Textiles and Sewing Class!"
It's not lost on me that alongside this narrative of women like Bo doing more making, I'm also championing more men doing 'textiles'... On a personal note, for the younger folks at school having to do an 'arts subject' at GCSE or equivalent - may I recommend Art Textiles. When I did this, I was one of two boys in around 30 girls. Safe to say it was not 'cool' and you can imagine the schoolyard comments. But the fact is, it's really expressive, technical and challenging - as well as creative. I loved it. Textiles have been an integral part of the Industrial Revolution, and so it really is a hugely influential part of our lives and culture, and of course the history of it is as tragic and scandalous as it is ingenious. So if like me, you are not great at drawing and painting, consider it.
The other point to make is that if you can endure the snipes and sniggers from your peers - being the black sheep has its advantages, as I ended up winning over my textiles teacher, who was openly very 'anti-men' - which, rightly or wrongly is still worth seeing things from her perspective! (and no, I don't consider this a 'double standard'). Some of her perspectives were pretty frank, even if cloaked in humour, but it challenged my perception of status, control and bias even at that formative age...sometimes your teachers impart more impactful things than their lesson advertises!). 2 years laters, she awarded me the top of class mark. In many ways she was a huge influence on my realisation that you can excel simply by not being 'the norm', and that my not playing by the 'rules', you can reset them by playing to your strengths/view on things.
I'm not saying this is so simple as my experience is an 'inverse' of what women go through. I've never had a #metoo moment, and my 'outsiderness' was still embraced by my tutor. Indeed, most of the major fashion legends have been men. But having come from a family of women in leadership and business, and having sought out working for companies with strong female leadership (Sugru, Elvie, Bare... to name a few) I've often found opportunities beyond what a homogeneous 'bro-culture' can offer.
Later in life I had the pleasure of seeing Hella Jongerius at in London Design Festival, and watching documentaries on Alexander McQueen, and brainstorming with Zyen over shoe concepts... I recognise looking back, that the outsiderness and independence of Bo is a non-preachy way for me to show my Son options and alternatives that are increasingly viable and liberating on many levels.
Step 14: Expert Advice: Angela Juarez
I realised that although I was muddling through my first plushy toy, I would benefit from some tips and tricks from someone who'd made plush animals before. I spoke with a friend Sean Charlesworth from TESTED, and he suggested I get in touch with a highly accomplished designer, prop maker, and artist - Angela Juarez. (See their links in the Intro).
She gave me some great pointers on how to approach the task, including how I might divide up the pieces for easy assembly, and also to keep the Skunky shape!
Anything that is not quite right here, is certainly my error, not Angela's - so please so check out her work, and other examples if you want to 'level-up' this Plushy. But for now, having done this twice, it seems to work pretty well.
Thanks again, Angela!
Step 15: User Testing - Video
Essential part of the design process.
Certainly things like the spring-nose felt a wise addition after seeing my Son drive this!!
Step 16: "Pixar Projects": Made in a Shed, in London, in Lockdown
So...I hope this little preamble was useful? Please say in comments if you're prefer more info on something - I'd be happy to help. I wanted to just point out that this project was done in about 15 days, but spaced out over probably 6 months (with 4 months just being crazy busy with client work), and yet it helped me stay fresh on work, and enjoy spending time with my family on this. I highly recommend doing projects like this, even if you are not sure what the commercial value is in them. They often are small on their own, but build to a critical mass / theme as a collection.
The often get called "Passion Projects", but I've since dubbed them 'Pixar Projects', (Skunk Work puns were a close second), but I've always loved the Short Films at the start of Pixar Feature Films, as aside from being an art of short storytelling, they usually have a technical motivation - for example, if you look at Piper, about a small bird gaining courage in the waves of the ocean, it's a great story - but it was also a technical text of Pixar trying to develop realistic water movement, from the flow, foam and spray, as well as the optical or 'caustic' look of the scene.
So this is why I do these projects, occasionally I connect with a good sponsor to help with funding, but mostly (case in point here), I'd do them regardless. For what it's worth, they often serve as a discussion piece with future / prospective clients, so the benefit is not always immediate... I've sharpened my CAD skills, re-connected with my enthusiasm for textiles, and of course had a great time being Dad. Certainly one of the best part of being a Dad is having the excuse to be a big kid, but also as a freelancer, it's interesting to note - Kids are quite interesting 'clients' in their own right...they have a different hierarchy of 'needs', and as much as adults focus on 'sensible' metrics, kids often are concerned with what is fun, initiative and re-mixable - play that can be different every time, depending on their mood. It's rare to have one toy 'do it all', but Bo Peep's Skunk Mobile has certainly got me thinking why there are not more toys like this, on the market, or available to download...
Good luck, and hope you enjoy making either this Skunk Mobile, or something entirely different - please share with anyone you know who might also enjoy making this as a creative parent and/or designer.
Step 17: The Video Diary
If you're a Design Student, or young professional wanting to know about the process, I took a series of short videos as I made it. Click on the above Playlist to watch the sections that might help you with your projects. Subjects include:
- Researching Concepts
- Creating a story behind a product
- Kit-Bashing
- Card Prototyping
- CAD Modelling from Photos
- 3D Printing tips
- Working with fur fabric
- Simple Electronic Hacks
- User Testing
- Iterative Design / Refinement
Hope it's useful!
Here's the Vlog series: LINK
Step 18:
Step 19:
Step 20: 3D Printing / Soldering & Inserts / Adjustments & Adhesive
I've put these tools in roughly the order you'd need them for the assembly.
3D Printing:
M3 Bolts: The majority of the build can be done in M3x6mm bolts (with a Hex Head) - I think there is about 40x in the build, although I tend to buy these separately (as they are my 'go to' size for a lot of 3DP work with Brass Inserts), I'd suggest you simply get an M3 assorted box, as you also need 4x M3x20mm for the Chassis, and 4x M3x12mm for a few thicker profiles. Safe to say you can use M3x10 or M3x8mm if you are short.
Soldering & Inserts:
Hex Keys. I'd imagine you can use any generic M3 Brass Insert, eg LINK, but personally I think the ones from RS (Allied in the US), are best performance in 3D printed work from trial an error. They are also easier to remove if you make a mistake. Tip: BluTack is also handy to hold bolts on in fiddly places!
Soldering Iron & Solder will be needed if you want to solder in lights to the Skunk's eyes, and they are of course useful to insert the Brass Inserts. I'm a fan of a great value Hakko 888 (Link). However, it also works fine to use a Mini Blow Torch too (but needed care when doing so!). Pliers are also handy to hold the hot parts if you're less experienced working with heat like this.
Adjustments & Adhesive:
Rotary Tool - Proxxon (slightly more expensive than Dremel, but better build quality). Bosch Glue Pen is a great handy size. Obviously best to use goggles when using tools, and glues. The rest are pretty generic, and I'd say any cheap-but-good equivalent is fine (e.g. you don't need the fancy Nipex side shears for this project!).
Also shown: Diamond Files, Bastard File, Scalpel, Marker, Callipers, Drill, 3.5, 4.0mm drill bits, Ruler.
Please feel free to comment if you need a link to something I've missed / is hard to source...
Step 21: Download CAD Files
Step 22: STLs to Print
It's perhaps worth saying that although you might consider sending this to a 3D printing shop, unless you are really short on space, or good with machines - it'll cost as much (if not more) than buying a 3D printer. As mentioned the Ender 3 is $200, so worth considering. Either that or ask a maker friend... ;o)
I've uploaded all the STLs here ready to print.
The exception/addition is adding the Cover Plate, as if you have some minor difference in your RC Car, you can edit the file yourself. SolidWorks Part File. Please consider re-uploading in comments, if you say have a popular equivalent in the US, etc. Thanks for helping others out =)
PS - This is an open-source project, and as long a you give due credit that this was "Designed by Jude Pullen", and link back to my website judepullen.com - you are most welcome to sell this on Etsy, eBay or offer 3D printing services at fair rates, to help people out who don't have access. Like Instructables 'Be Nice' policy applies ;o)
Attachments
Bo Seat Backrest.STL
Bo Seat Floorplate.STL
Bracket - Clasp Side.STL
Bracket - Hinge Side.STL
Central Cage - Back Arch.STL
Central Cage - Clasp.STL
Central Cage - Front Arch.STL
Central Cage - Hinge Top.STL
Cover Plate.STL
Ear - Print 2.STL
Fur Side Clips - Optional - Print 2.STL
Nose - Fur Clamp Plate - plus Battery Holder.STL
Nose - Spring Back Plate - Body Side.STL
Nose - Spring Front Plate - Nose Side.STL
Nose Oil Can - with Lights.STL
Paw Spurs - Front.STL
Paw Spurs - Hind.STL
Rear - Back Plate.STL
Rear - Tail Plate.STL
Tail - Reduced Weight.STL
Tail Bracket.STL
Tail Rib - 50mm.STL
Tail Rib - 70mm.STL
Tail Rib - 90mm.STL
X - Central Cage Top Brace - Print 2.STL
X - Central Nose.STL
X - Central Top Nose.STL
X - Front Side Bracket - Print 2.STL
X - Rear Central Twin Bracket.STL
X - Rear Lower.STL
X - Rear Side Lower - Print 2.STL
X - Rear Upper.STL
Cover Plate.SLDPRT
Step 23:
Step 24: 3D Printing Orientation / Clean-up / Tips
Most of the parts are pretty straightforward to print and are relatively obvious to orientate - ie print them on the plane they's naturally fall on if you dropped them on a table and fell 'flat'.
Most of the pieces have been designed to make use of the fact that FDM printers layer the plastic as shown, and so this is the strongest way to print them, and also requires no build support.
I used CURA Software to print with an Ender 3, and most of the build can be done in 3-4 prints on a 'large' 1mm nozzle. Again - I designed this to work at low resolution for speed of making. You can of course print at smaller nozzle sizes like 0.6mm, but lower seems pointless.
The one big exception to the file are the side supports (see last picture), which need to be built 'vertically' or 'end on' - such that the 'triangles' face upwards. This is because the strain of the weight of the Skunk is best applied in this orientation of the print - think of it like wood grain... this is stronger this way in flexing.
NOTE: In the next section I'll show you how to add Brass Inserts. These are almost [!] always in these 'ribs' or 'X-pieces' as they are in CAD, but note there are a few which do not need them, so I'd suggest reading through thoroughly first, or simply adding them as you go.
Tip: The second picture shows me rapidly moving the blowtorch over the surface of the print. This is to partially re-melt the plastic, and means the white/matt discolouration goes black again. Have a go, and you'll see what I mean. It does not need to linger, as this will melt and deform the piece - just a quick flash is all it needs.
Step 25: Pre-Drilling
For most of the 'ribs' or 'X-Pieces', these do not need pre-drilling - in order to insert the Brass Insert into. However, there are a few exception like the Spring Plates in the nose. Or if you find it a tight fit. To do this measure the 'collar' of the Brass Insert (the slimmest part), and use a drill bit that size to pilot the holes.
Tip: As a general rule, I was taught to make most 3D printed holes slightly smaller than needed, and then drill out / allow a tight fit / melt in thoroughly. This is not precision injection moulding, and so the edges of holes are often inaccurate even on good 3D printers, and are inherently weaker as they are at the edge of a layer. So this is a good design rule to apply to your designs if you do a lot of this in future.
Next are two ways to insert the Brass Inserts...
Step 26: Brass Insert Insertion - Method 1: Soldering Iron
Heat up soldering iron to a relatively 'cool' temp of 250C, and load a brass insert on as shown. To avoid burning your fingers, consider using pliers to pick up. The insert usually sticks to the tip slight as it heats up, and so quickly position it into the hole in the 3D print. Press gently and allow it to sink in. Remove. Press the insert/part on a flat surface to ensure it is flush.
-
This is arguably the most typical way to do this. However, I would admit that using a high quality soldering iron tip (like shown) is not especially wise unless you're very accurate and never touch the plastic with the tip, as the melted plastic will mess up the tip. (In truth, this is not on in these pictures). So if your soldering iron is over £20/$25, I'd suggested you get a cheapo one, or use a 'messy tip' just for this, or use the second method...
Step 27: Brass Insert Insertion - Method 2: Blow Torch
This is not for the novice! Practice with Method 1 first.
The reason for doing this method is because using a bolt allows you to precision align the insert, whilst the plastic is cooling. Using a soldering iron is nearly always less accurate (unless you made a custom tip - which is not actually a terrible idea now that I think of it!).
Start by screwing on the insert perhaps 1-1.5 turns. Apply blow torch for a few seconds, at the tip of the blue flame (not in it). The brass should every so slightly darken in colour - remove heat. Insert into Print. Push slowly into until flush. Use the screw as a 'level' to ensure the bolt (and hence insert) is perpendicular to the print surface. Once cooling down, gently unscrew the bolt - taking care not to shift the insert too much. Press the print against a flat surface to ensure it is flush. If you have any excess - you can give this a quick 'blast' with the blowtorch to soften - and then press flat again.
HOW TO REMOVE A BRASS INSERT?
If you make a mistake - heat the tip of the bolt, screw into the insert, allow the heat to dissipate - and the insert will melt the surrounding plastic - then gently pull out. This requires some knack, but if worth trying on a piece of scrap/failed print, as it's useful to know.
Step 28:
Step 29: Ready Your Chassis
Unscrew the 'Cab' of the RC Car as shown, leaving the chassis.
It's worth noting the aerial position - and to make sure it is free to move.
My RC car also needed the wheels 'trimming' to re-align properly - do this by moving the small white wiper underneath as shown.
Step 30: Assemble the Following Parts...
I've added some note - click on image to read them.
Prepare and add inserts as shown in the diagram.
Step 31: Prepare Chassis Mount Plate
Ensure all the Brass Inserts are done, as shown.
Check the wires are clear of any bosses or pinch-points, and gently press down as shown.
Then click one side of the piece, then the other.
If it is a little tight, either file off any excess from the printing, or use the blowtorch to soften slightly. The Chassis Plate should snap into place, and not feel loose.
Step 32: Screw Down Chassis Plate
Screw in the 4x M3x20mm bolts.
These (in my model) 'friction fit', and 'self tap/thread' as they go. However, if you're struggling, try drilling out a 2.5mm hole, or if too loose, then add a bolt on the other side to ensure it 'clamps down' firmly.
It's worth realising that this is what EVERYTHING is built off - this is the 'foundation' for everything you do next, so it's worth making sure this part is spot on.
If in doubt, ask Bo to take a look...
Step 33: Preparing the Hinge
Using the M4 Threaded Bar/Rod (eg LINK), drive it into the holes of the hinge - and pull back-and-forth to remove any swarf/excess from the inside.
File off any excess on the perpendicular faces of the hinge(s), as shown.
Assemble as shown, and using some masking tape (easier to see than pen), mark the distance to cut the rod. Remember to leave around 4-5mm either side for the nuts to screw on.
Tips: I used Nyloc (Nylon Locking) Nuts at either side, but you can use a normal nut, and simply add a dot of superglue or epoxy to hold in place. Indeed, if you don't have threaded bar, you can also use some other appropriately sized bar, and create a 'fix' on either end. I've done it this way, as I always work on the assumption I'd like to re/disassemble models, but if you doubt you'll do this, just glue it.
Step 34: Cut Threaded Bar
Safety First - Wear Googles!
Most Rod will be shipped in lengths of 300mm or even 250mm - so from this you can get the 140mm hinge rod, and 2x 50/60mm pieces for the tail inert (see later). Keep these to one side.
File off the burrs from the ends, so as to ensure the nuts screw on nicely, and there are no sharp edges, which can cause cuts.
Pro Tip: I tend not to try and 'cut in 1', but rather rotate the bar against the grinding disk. I leave just a tiny central 'stalk' in the middle, which will snap off with a little bend/flex. This takes practice, and if you're a novice, I suggest you just clamp it for safety instead. However, learning this method gives a better finish and allows better threading of the nuts. Only do this at your own risk, and if you are very experienced with rotary tools, as free-holding work can suddenly snag and throw the piece in a dangerous manner. Wear a face visor.
Step 35: Central Roll-Cage
The assembly of this is relatively straightforwards, but do take care to align the sides so they are 'square'.
Once happy, glue them in place - taking care not to get any on the threaded bar.
I used superglue 'activator' to speed things up (only do so in a well ventilated area).
Step 36: Attach Roll-Cage to Chassis Base
The side screw holes should align nicely with the supports - screw in as shown.
I also added some M3x10mm screws to 'locate' the two connecting faces of the Cage 'door'. These could be any small rod/stick if no screws to hand.
I also used a drill to widen the locating holes as shown. Cage 'door' should close easily, without careful alignment, as when covered in Fur, it's hard to see, so it needs to be done 'blind'.
I'm beginning to think Bo Peep should have had a modified Allen/Hex Key in stead of a Shepherd's Crook. Perhaps if anyone at Pixar is watching, s/he'll 'upgrade' it for her to have the extra functionality.
Step 37: Roll Cage Braces
Screw in the cross braces for the Roll Cage as show.
(I did this at a later step, but suggest doing it now).
Step 38:
Step 39: Print & Prepare the Paws
These *just* fit onto the Ender 3 print-bed. Use the 'free rotate' feature to set them on the bed.
Using a Needle File which is triangular - and hence sides have a 60 degree angle, this is the perfect profile for the 'Dovetail Socket/Joint' - clear these so they fit nicely onto the corresponding Dovetail on the Chassis.
Step 40: Dovetail Together
As shown, the feet should slide in snugly, and screw into place securely.
It can be easier to do this from the underside view, as Bo demonstrates. Watch and learn...
Step 41: Assemble Front and Rear Paw Supports
You may be wondering what the difference is between the front and the back paw supports?
It's very subtle, and for the rear unit - look for these little bumps. Click on the photo - and Bo will show you in detail...
Step 42: Bend Paw Supports
I'm usually a fan of creating 3D prints which are 'finished' so the user has no variation from my original design. However, in the case of the Paw Supports I really can't see a better way to do this than post-process as shown...
I suggest getting a mini blowtorch (or lighter works also) and briefly warming up the PLA to the 'inside' of the 'bumps' as shown.
Carefully bend this so as the shape forms a near right angle.
I suggest trying on a piece of strap PLA, as it can be surprising to work with: Initially it seems like nothing is melting, then you stop heating, and then a few seconds later the plastic is then super soft. In short there is a delayed effect between heating the surface and the heat permeating the thickness of the material in order to flex. So heat less than you think and do a little at a time.
I also found that raising the Supports a little to make a every so slight 'V' was good for clearance - ie the Paws do not scuff on the wheels/tyres. (The last picture illustrates this point - though not severe, it makes sense to avoid upfront).
Although I have shown this step with the Paw Supports attached to the chassis, if you are less experienced with blow torches I suggest doing this with them detached to avoid heating anything else accidentally - like the wheels of the RC car!
Step 43: Seat
Print the base and backrest of the seat.
These print 'flat', but need to be 'bent' into shape - like the Paw Supports, this seemed the most structural way to do it....
Lightly heat the edge of the 'wings' of the seat, and then press to around 60degrees, on a flat surface. It should 'fold' nicely along the broken line/gaps.
Assemble, and add some superglue to hold it in place.
Screw into the Chassis with bolts as shown by Bo.
Step 44:
Step 45: Assemble Parts
Print Parts as shown. Clean up, and add any necessary inserts as shown.
The 'Ribs' on the Tail can be printed as you need them.
Step 46: Add Rear Section
I have not shown this step by step, but generally speaking assemble it as it appear in CAD.
It's worth noting that the holes in the Roll Cage plate (rear) does need some pre-drilling for the Brass Inserts to fit in nicely. You do not have to add 2x per side, but I still felt like this build is a prototype, so leaving options to modify supports made sense.
Step 47: Tail Armature & Tail Socket
As mentioned, the Tail benefits from being detachable, as when you need to compact the Skunk Mobile, it helps to remove the tail!
I did this by using the leftover M4 threaded bar, and inserting as shown. I suggest pre-drilling out the holes in both pieces as shown, as this allows easy assembly - even if the tail side should contain the screws and have them glued in.
Safety Tip: Do not glue the rod in the other way around, as this is more dangerous, as they point 'upwards' when resting, if left in the skunk body side.
Step 48: Add Ribs to the Tail Armature
Showing the end result first, it can be seen how the ribs contour / sweep from small at the base, to wide at the topmost edge, and then recede again to the tip of the tail. This is my best effort, but you can of course take more time to get this just right, but strike a balance between perfection and what will be seen when cloaked in fur!
Once happy - tack in place with some Hot Melt.
Step 49:
Step 50: Assemble Parts
I actually redesigned the Ears here, but these are open to improvement... I'm no sculpture artist!!
Step 51: Spring Mount
This is hard to explain, but will become obvious once you try: Try to 'screw-on' the spring to the stud, try both directions, and you'll see the spring flex and slide on better in one direction. If still struggling (the tight fit is deliberate) try using pliers to carefully 'pull on' the spring edge to the stud.
Press the assembly vigorously to ensure the springs stay in place no matter what.
Step 52: Check Alignment
This may seem excessive, but any misalignment will be 'magnified' by the time the Skunk Nose is added, so it pays to make the effort now to ensure a good alignment that is central and even. There is no easy guide to this other than you fiddle around with the springs and press them until it moves into place!
Step 53: Add Front Section
Add the X-Pieces as shown, paying attention to where Brass Inserts are needed. Note - these have a few which are not needed in one side of the X-Piece. See Image 2. (Click image).
Step 54:
Step 55: Night Vision Skunk Powers
As my Son gave me some 'design feedback' here, in the video - that we need lights. So I made a quick hack to put in some LEDs. It's far from 'industry standard', so if you're want to improve on this, go ahead.
Safety Tip: One thing I would say is that with Coin Cell type batteries, which are 3V, they are actually quite dangerous if swallowed (having read some sad reports on this online). So please take care if your are making this for a child, and you feel they would be unattended, etc. Our Skunk Mobile is only taken out with Mommy/Daddy, and kept safely out of reach when not in use. So please take all care.
Anyway, assuming you're all prepared - on with the build!
Step 56: Prepare Components
File down the top of the LED a little. This not only makes it fit better, but also diffuses the light better.
Twist the Legs together (long & long; short & short).
Solder wires to the appropriate legs. Positive/Red is the long one. If in doubt - touch to the battery.
Wire up the Switch as shown. I've used a push-latch button, but frankly you could add any switch here, and just adjust the hole in the Nose as required.
In a bit of a 'fudge', I created a housing for the battery which also holds the wires in place. It's a bit makeshift, and if you prefer to install a proper battery housing, please do what you feel best. For me this was a quick on-the-fly hack to entertain my son, and I felt it was worth sharing that much of prototyping is about getting it to work with what you have to hand, and in as little time and cost as possible.
I was pretty brief about the steps to do this, as I figured if you're this far you can probably handle it, but do let me know if you need more detail, and I can add it. =)
Step 57: Head Assembly
If you're paying close attention, I actually initially used some LEGO pieces as eyes, whilst I was waiting for the Glass Beads to arrive. I felt that as this was my homage to Pixar, I wanted the authentic Glass Eyes, but of course you could go Googley Eyes, or anything else to hand.
The Switch is simply held in with some Hot Melt, as are the LEDs.
The Back cover is then Hot Melted into place also.
Step 58: Eyes On
Glue on the Eyes, ideally with the lights on - so you can centre in line with the light from the LEDs.
Step 59: Fix Head on Body
Add Brass Inserts as shown to the back plate of the Head.
Then align to the Sprung Body Plate, and screw in place as shown.
In later steps you'll use this 'Clamp Plate' to hold the Fur Fabric.
Step 60: Ears
Add Ears as shown. It may require some filing/sanding to fit.
Step 61:
Step 62: Faux Fur Fabric - a Quick 101 Primer
Perhaps the most important thing to note in pattern making with Faux Fur, is that it has 'direction' to the fur. Faux Fur is not 'woven', but rather it is 'knitted'. As you'll see from the second picture - but has these chevron patterns. Either way, what matters is that one direction is more stretchy than the other, and also the fur naturally 'rests' in this direction.
The easy way to identify this, as to shake the fabric vigorously, and see where it 'rests', or where it is when you get it out of the packaging. You can see from the third picture that one side has more 'overhang' of fur, and this is where it 'rests'. ie you can this side to be 'hanging down' or 'facing towards the rear'. If this still makes no sense - so stroke a Cat or Dog from head-to-tail and then from tail-to-head, the latter will not feel smooth. This is what we're aiming to do with the Skunk's fur, so keep this in mind when working.
This should be kept in mind when working with the Patterns for optimum effect of the Fur.
Chances are you'll be able to get Faux Fur in your country, but eBay is a good place to start, as often you can pick up a bargain from factory surplus, etc. I ordered a 'Fat Quarter' of Black Fur (500x750mm) and a 'Fat Eighth' of White Fur (500x370mm). The length of the fur strands is about 70-80mm long. (LINK)
Step 63:
Step 64: Fabric Patterns - to Print at Home
Attached are the PDF files you can print at home.
I have outlined them in A4 and US Letter size, given the international audience on Instructables. You lucky people!
The images here are for illustration, and use the PDFs for 100% scaled printing. There may be some variation in printing, which is why I've made the Pattern 'generous', so even if it were out by say a few millimeters, you'll have enough slack to cope. As with most things, start large, and tailor in as you need it.
If you've not used Patters for textiles, they usually have two lines
- the outer here in Red - is for cutting.
- the inner dotted black line is where you'll ultimately sew it together. This is generally 10mm or 1/2 inch inset. And although you can of course mark this stitching line with tailors' chalk, the reality is you usually end up guessing it within a few goes. This is a Skunk Plushy, not a suit, so it'll cope if you lines are a little off.
As with so many things - practice on a scrap(s) first to get the feel of it. Fur Fabric is pretty bulky and a bit fiddly to get familiar with, and you'll need to reduce the presser-foot pressure/height on your sewing machine, and likely adjust the tension wheel to work effectively with it, even if you are experienced with other textiles.
Step 65: Transfer to Fur
In hindsight one could get a shorter fur for the Black as I ended up trimming a lot off, but it kind makes for a fun process, and gives it a 'natural'/shaggy animal look. Your call.
Hopefully you can see from the layout, the Patterns fit nicely on the two pieces respectively. The only faux-fur-pas, is that I left out the Paws on the black fur - so be sure to add them, but they do fit, but it's tight.
You will likely have more White Fur left over, so use this as a practice run.
Step 66: Cut Out Fur Sections
I'd highly recommend either a super sharp pair of textile scissors, or a fabric cutting wheel. Either is about £15/$20 - and is a very worthwhile investment. Do not cut paper with them even. Just keep them for fabrics.
I also recommend keeping a vacuum cleaner to hand, as you'll want to suck-up all the fluff that accumulates as you go, unless you have pets, in which case you know the score...
Pro Tip: If you want to keep fluff to a minimum - I found that sliding the scissor blade carefully just to the 'backing' (non-fury part of the fabric), and cut this, gradually sliding forward. This means you're cutting the backing, not the fur strands. So much less fluff is created/wasted.
I suggest pinning the Patterns to the fabric as shown. It *just* fits on the Fat Quarter of the Black, as you can see in the previous step. Do the same with the white stripes, and set aside ready for sewing...
Step 67: Straight Sewing the Fur (or Gluing If You Prefer)
This is one of those things that I can say 'remember to stitch it inside out' - but it can be surprisingly easy to forget when you're new to this stuff... so the best advice is to pin it together, and turn it 'right side out' again, to check it all makes sense, before you commit to sewing.
Start by doing an 'easy' piece - the white stripes. Place the pieces (with the paper Patterns on) in front of you. Ensure they are arranged correctly - this avoids mistakes in assembly - then un-pin, and remove the Patterns. Bring together the ends as shown, and try to push as much fur 'away from you' (ie to what will be the outside), and then clip/pin/stitch together. Then take this to your sewing machine.
If you have never used a sewing machine, find out how to 'go backwards' with a button press, and ensure you 'double stitch' at the start and finish of each run, as this keeps it secure.
Pro Tip: I used to use pins or tacking thread when I was at school to check the fit of things, but I now swear by these textile-clips (like these - LINK)...and impressed they even work with Fur.
BUT I DON'T HAVE A SEWING MACHINE!
This project can totally be hand stitched - it just takes longer. However, if you don't have access to a Sewing Machine (or access to one - check your friends and family - you may be surprised! I got mine from a charity shop for £20, and it has made parachutes for rockets, gifts, fancy dress and more...), you can of course hand stitch it with needle and thread, but you can also use Glue!...
This is a great little video of tips for working with Fur, as well as using Fabric Glue - which considering you're unlikely to put the Skunk in a washing machine, will be fine (at a push, you could probably use superglue or hot melt).
Lastly, if you're a design student or prototyper starting out, I can honestly say being able to use a sewing machine is a highly underrated skill. I would not have been able to do a load of projects without mine, and the mechanical wizardry in these machines is just amazing, and if you're an 'Engineer' is almost impossible not to admire that these things transformed our lives as much as any other labour saving device. You can pick one up for the price of a meal for two. LINK. You will not regret it.
Step 68: Curved Sewing
It may seem daunting but in many ways 'curved' stitching is not quite as complex as you might imagine - as even though the Skunk is '3D' - it's Patterns have been created to be sewn flat. This is the essence of much of dressmaking.
The best way I find is to start at the 'critical' end - which is the face, and make this the best aligned face of all the edges of the fabrics. All being well, they should line up, but better to have a wonky bottom than a wonky face, right?
Clip the adjoining pieces as shown. Feed through slowly as you can, until confident. Once you have done one side of the 'body' of the Skunk, add the other. (Ignore my scribbles on my Patterns btw - go by what's correct on your print outs!).
Once you have done the 'spine' or white back stripe, do the 'darting' - which are the 2x 'V' cuts in the sides.
The same process applies to the Tail, but a key difference being I used more clips to hold the tighter curve in place, but again these pieces should flatten to be sewn.
Step 69: Zippers (Body & Tail) + Adjusting Length of a Zipper
So truth be told, I kinda just put the zipper in 'cowboy style'... I have since seen that there is a better technique, on writing up this Instructable! (the keen eyed among you will note - I've made 2x Skunks). So if you want to watch this - it's better than my effort! (LINK).
As much as it's nice to strive for perfection - it also must be said that the zippers are inherently so well hidden (ie under the tail and at the rear of the skunk's body) that it also had to be said that just sewing it in 'parallel' is also adequate. Again - this is not a fly on your trousers, or a pillow that will get a lot of stretching, etc. So it really is just a means to fit the Fur over a 3D printed object which is larger than the end 'opening' of the Plush covering.
I personally found it easier to make the main 'body' or 'tail', and cut in the place where I wanted the zip. For reference you can use the Patterns - see the blue double dotted lines as a guide.
You can either hand stitch roughly in place, or use clips. Then with the zip correctly orientated (think carefully about this - inside out!), sew on the sewing machine. Once done, allow the fur to cover over the zip.
One tip I did realise was that as I purchased a 'job lot' of Zippers some time ago, or assorted colours and sizes, I didn't have the luxury of buying the exact length I needed. So I had to figure out how to shorten it. I found you can do this by using a flathead screwdriver to pry-up the pins of the 'stop clip', and then carefully re-crimp it at the new 'end', with pliers. Finally, cut off the excess.
It's a small thing, but I'm quite proud to have figured this out, as it means I can reuse zippers from old clothes more easily now if needs be.
NOTE: I didn't draw the hole on at the end of the zipper for the Tail to 'plug into', but safest to say it's best to fit it to wherever it ends up fitting best to your Skunk Mobile.
Step 70: Paws
So the aim of the game is to have the underside of the paws made from a material that is not going to get caked in mud, the way the fur will. And also that it must not be furry - so as to get caught into the mechanism of the motors, etc.
I've uploaded an example of some Leather for £2.50 - bargain. And because of the nature of the project, the 'defect' on some leather may be even cheaper.
A good thickness is 2mm.
If you are using your sewing machine, I suggest driving it 'by hand' - where you are just turning the flywheel yourself, rather than powering with electricity. This means you're less likely to break the needle, or stress the machine too much.
The process is reasonably simple - cut out the leather and fur, and ensure you assemble them 'inside out', tucking the fur fibres 'in' as much as possible. Clip, then sew. The Patterns are slightly oversize, so this means you can trim them down to a snug fit, but also to trim away excess Leather, so as the 'Paw' turns inside out better, as shown.
Lastly, trim the fur length down a bit, so it's not too shaggy. We'll be doing this with the body soon, so this is good practice...
ALTERNATIVES TO LEATHER PAWS
You do not need to use leather to do this. I happened to have some remnants - again purchased as a job lot on ebay for various projects, but you could also use PVC sheet, Funky Foam, or even plastic from a margarine tub / veg punnet if you like (see final picture!). The key is low-friction, and that you can sew it to the Fur (yep - even the plastic will work, so long as it's thin!).
Also, if you are vegan, you can opt for fake leather, or even this made from Pineapple waste! PinaTex.
Step 71:
Step 72: Fur On: Body
As shown, working from the back of the Skunk, add the Fur on.
The reason for doing this is it is simpler, and you have not yet affixed the fur to the head yet.
Work along the body, checking the fit as you go...
...Once you get to the head, there should be enough excess Fabric to 'poke' into the clamping plate, between the head and the body. (I've removed the head to show this more easily in pictures). Essentially you want to tuck in the material around the head to a snug fit - and then tighten up the screws to 'clamp' it.
Step 73: Fur On: Tail
If you've not already done so - add the 'ribs' to the Tail, and trim into a good 'flowing' form.
Check the fit with your Fur Tail, and then insert. You will need to 'shake it' about as it does in, to avoid snagging.
Lastly, check the alignment of where the Tail plugs into the Body, and cut a small hole here. (I've removed this for easy demonstration, but just cut in situ).
Step 74: Skunk Hair Cut
There is no easy way to shave a skunk.
What I can recommend is doing it outside, or if indoors having a vacuum cleaner to hand at all times!
I tried to do a mixture of pulling the hair to a given length and cutting it at a given point, and working systematically along the body and tail in this matter. As always - start long, get confident, then go shorter.
KEY TIP: I trimmed the black fur, but left the white fur full-length, as this made it less 'wide' in the body, but make it quite 'punk' / wispy in the tail - a bit like a soft mohawk haircut! Style as you wish.
Lastly, I took it outside and gave it a good hairdry (on cool shot - not hot! this may melt it?!). A good shake also does the trick.
Step 75: Finishing Touches / Troubleshooting.
1. Add Paws. Slide on, and tack in place if needs be with some hotmelt. Check wheels turn freely.
2. If your suspension is 'soft' - add some 'clips' to compress the spring, and make it a harder ride.
3. If the Red wheel rims bother you - pain black or colour with a marker.
4. If you have not already fitted the Paws on, do so now - and fix with a spot fo hot melt glue, or stitch.
5. Also, if not already - add the Seat as shown.
Step 76:
Step 77: Plush Rush!!!
And you are done!
Wow - thanks if you made it this far, and please do post if you actually made it (or are making it and have questions / suggestions). Please comment and/or share if you liked it!
Lastly, please do check out my other work and get in touch if you'd like to commission any fun projects like this. I hope it's an engaging narrative about building, process - but also the points about why this project started might inspire something in you also. On thing's for sure, there has never been a better time to reimagine new play and experiences for kids. What will you make?
Best wishes,
Jude
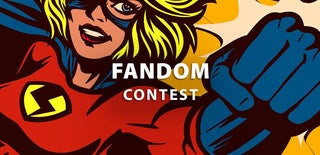
First Prize in the
Fandom Contest