Introduction: Cheapest Wireless 3D Printer - Boltz Megatide
Introducing Boltz Megatide - A $140 Reprap Printer
With a semi-recycled frame and zero printed parts, Boltz Megatide offers a cost-effective solution for 3D printing. The machine can operate efficiently even after printing each part upgrade for more than 20 times. Additionally, it can continue functioning without upgrading to plastic parts.
My inspiration for this project came from the Ewaste $60 Reprap (which can be found on Instructables). However, Boltz Megatide offers significant advantages. For just a slightly higher price, you can enjoy an eight times larger print area.
Stay tuned for more details and let's embark on the journey of building Boltz Megatide, a cost-effective and efficient 3D printer.
Step 1: SpeciFications
+Type - Core XZ.
+Printing Speed- 20 mm/s To 100 mm/s* (* Can Go Further Up. But Maybe can Ruin Print Quality).
+Printing Resolution - 0.05 mm To 0.2 mm (tested With A 0.4 mm Nozzle ).
+Printing Area - 210*210* 290
+MK8 Extruder.
+Bowden System.
+All Metal Hotend with 260 degree c Capability.
+Frame Material Wood (Mostly).
Step 2: Bill of Materials.
you will need the following materials:
Recycled:
1. 0.5-inch wooden sheet (70cm x 60cm) or a wooden table
2. Support planks (2.5 inches x 1.5 inches x 1 meter)
3. 3mm wooden ply sheet
4. Paper clips
5. Small flat metal pieces
6. Ply mica/paint (optional)
7. Screws, nuts, and bolts
8. Waste CDs
9. Steam punk-type waste relay
10. Ties
11. 4mm ID pneumatic pipe
12. Old PC's power supply
Non-Recycled:
1. GT2 timing belt
2. Ramps and A4988
3. Arduino Mega
4. 5 x Nema 17 stepper motors
5. All-metal hotend
6. MK8 extruder with gear
7. 10 K thermistor
8. 6 x endstops (optional)
9. 2 x radial bearings (8mm)
10. Smooth rods (8mm)
11. 2 x GT2 pulley
12. PTFE tubing or pneumatic pipes
13. Heatbed
14. 2 x stepper motor clamps
15. M6 to 4mm pneumatic fitting
16. 8mm linear bearings
17. Filament (ABS or as per your preference)
18. 8mm/5mm threaded rods with compatible nuts
19. 40 x M4 screws and nuts
20. 25 x M3 screws (plus 5 extras)
21. HC-05 Bluetooth module (optional)
The total cost for these materials should not exceed $125. Additionally, you may need an extra $15 for any desired customization, wires, screws, or the optional HC-05 Bluetooth module.
Please note that the availability and prices of these materials may vary depending on your location.
Step 3: The Frame.
To build the 3D printer, you will need the following tools and materials:
Tools:
- Drill
- Screwdriver
- Hammer
- Soldering iron
- Epoxy
- Super glue
- Nuts and bolts
- Saw
- Metal sheet cutters
- Nails
- Ribbon wires
Materials:
- Big sheet for the printer base
- Thick wooden plank for the Z-axis support
- Z-axis rods
- Wooden plank for the Y-axis support
- Small metal plates
- 3mm plywood
- Springs
- Screws
- Block or a 3-4cm smooth rod for the bearing holder
- Relay with a solenoid
- GT2 gear
- Motor clamp
- Belt
- Bearings
- Upgradable parts like hot end holder, fan holder, belt holder, belt tensioner, T5 idler for the X-axis bearing
Here are the steps to assemble the BOLTZ Megatide 3D printer:
1. Place the big sheet to create the printer base.
2. Install the Z-axis support by cutting the thick wooden plank according to the desired printing height. Use an 8mm drill bit to drill holes in the sheet to install the Z-axis rods. Make sure the rods are parallel to each other and perpendicular to the Y-axis.
3. Build the Y-axis by cutting the wooden plank into five equal parts of 4cm each. These parts will act as supports for the Y-axis smooth rods. Install them between the holes on the bed's corners using small metal plates and screws. Use 3mm plywood to drill holes and attach the bed with springs and screws. Install a block or a 3-4cm smooth rod as a bearing holder. The block or rod should be linear to the motor and perpendicular to the X-axis. Install the GT2 gear on the motor and then attach the motor to the base, aligning the gear and bearing linearly. Install the belt accordingly, making holes at the end of the belt and attaching it to the bed with screws. Install bearings on the bed.
4. Once you've built the printer, you can upgrade essential parts like the hot end holder, fan holder, belt holder, belt tensioner, and T5 idler for the X-axis bearing.
After completing these steps, you will have assembled the 3D printer. Remember to follow the instructions carefully and take necessary precautions while working with tools and materials.
Step 4: The Heart of Machine (Maybe)
1. X Idler:
- Cut a piece of wooden plank with a length of 75mm.
- Drill two holes with an 8mm drill bit, separated by a distance of 30mm between their centers. Ensure that the distance matches the one on the X-motor end.
- Take a piece of hard metal sheet (iron works fine) and weld a nut onto it. Make sure that when the threaded rod is inserted into the nut, it is perpendicular to the metal plate.
- On the ends of the strip, drill 3mm holes to screw it onto the shaped plank.
- After screwing it to the plank, use a 14mm drill bit to drill through the plank from one side (preferably the left side, away from the X-axis rod holes).
- Insert two linear bearings into the drilled holes.
- Keep the screws joining the nut and plank slightly loose to prevent z wobble.
2. X Motor:
- Cut another piece of wooden plank with a length of 55mm.
- Drill holes for the X-axis.
- Create another nut support and screw it in place.
- Use a motor clamp to attach the motor to the plank.
- Install the gear on the motor.
- Drill 14mm holes for the Z-axis bearings and install the bearings.
3. X Carriage:
- Take another piece of wooden plank with a length of 55mm.
- Make two holes through the plank with a 14mm drill bit, keeping a distance of 3cm between their centers.
- Install bearings into the drilled holes.
These instructions will guide you in creating a wooden X-end for your 3D printer, providing unique aesthetic and potential design advantages.
Step 5: Assembly
Once you have completed the assembly of all the parts, follow these final steps to finish building your 3D printer:
1. Join all the assembled parts together and install the rods.
2. Set up the motors and attach them to the base using superglue or epoxy. It is recommended to use superglue as it allows for adjustments later by scraping off if needed.
3. Create a hotend holder as shown in the provided instructions and screw it onto the carriage. Set up the extruder.
4. Install the bed and make sure to wire everything up according to the Ramps 1.4 schematics.
5. If desired, install lights and add any additional aesthetic touches to beautify the printer.
6. Wire everything up following the appropriate connections.
7. Install the power supply. To make it work, connect the PSU's green wire to GND.
8. If everything has been assembled correctly, you are now ready to start printing.
By following these steps, you should have successfully built your 3D printer and can now begin using it for your printing needs.
Step 6: Installing the Soul
To ensure your 3D printer functions properly, you will need to configure and upload the firmware. Here are the steps to do so:
1. Select the appropriate configurations for your printer. This includes details such as the type of controller board, stepper motor drivers, thermistors, and other hardware components you are using. Refer to the documentation or specifications of your printer to determine the correct configurations.
2. Download the Repetier firmware from the provided source. Repetier firmware is a popular choice for 3D printers and offers a range of features and customization options.
3. Additionally, you can consider downloading a preconfigured firmware if one is available for your specific printer model. This can save time and effort in setting up the firmware.
4. Download the Arduino IDE (Integrated Development Environment) from the provided link. The Arduino IDE is a software tool used for writing, compiling, and uploading code to Arduino-based boards, which are commonly used in 3D printers.
5. Install the Arduino IDE on your computer following the provided instructions.
6. Open the Arduino IDE and configure it for your specific printer. This includes selecting the appropriate board type and port from the Tools menu.
7. Open the Repetier firmware in the Arduino IDE. Make sure to select the correct firmware file that corresponds to your printer's configurations.
8. Review and modify the firmware settings as necessary. This may include adjusting parameters such as motor steps per unit, endstop configurations, PID values for temperature control, and other printer-specific settings. Refer to the firmware documentation or guides for guidance on making these modifications.
9. Once you have made the necessary changes, compile the firmware by clicking on the "Verify" button in the Arduino IDE. This will check for any syntax errors in the code.
10. If the verification is successful, connect your printer to your computer using a USB cable. Ensure that the printer is powered on.
11. Upload the firmware to your printer by clicking on the "Upload" button in the Arduino IDE. This will transfer the compiled firmware to the printer's controller board.
12. Wait for the upload process to complete, and then disconnect the USB cable from your printer.
By following these steps, you should have successfully configured and uploaded the firmware to your 3D printer. The firmware is essential for controlling the printer's movements, temperature regulation, and overall operation. It acts as the "brain" of the printer, enabling it to interpret commands and produce accurate prints.
Step 7: Callibrate and Download the Host
Step 8: Enjoy
Setup Everything Left.
Am I Still missing something ? PM me for Improvements and Help.
Step 9: Updates
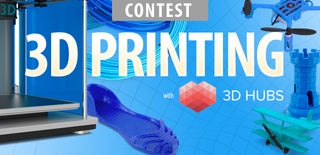
Participated in the
3D Printing Contest 2016
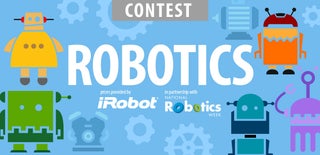
Participated in the
Robotics Contest 2016