Introduction: Building a Stave Snare Drum
Playing drums for years i've always wanted to make my own drums. Over the past couple of years i really started researching different methods. I finally came across stave snare drums. Instantly loved the look, sound, and quality of these drums being built in garages all over. I was on a mission. I am going to show how i built my 7"x14" snare drum from scratch. I will try my best to include links and such to the different sites i used for reference during the build. I wish i would have taken more pics of the entire process in detail. If you have any questions feel free to contact me and i will assist the best i can.
Wood, Hardware, Stain, Drumheads ect. Cost around $300ish total, (Heads and Hardware made up around $230 of that bill). You can find old used snare drums and strip the hardware off them for your trial build for very cheap. You can even use scrap lumber. Hardwoods are the best option in my opinion for snare drums. I already had the tools used for the build. I put in around 20/25 hours into this build minus waiting for glue, stain, and sealer to set. It can be done much faster once i get it down. I double/triple check a lot..
Links i used for purchase, research and such.
Hardware: https://www.drumfactorydirect.com
Calculating Staves: https://www.notsomoderndrummer.com/not-so-modern-d...
Lug layout mat: https://picclick.com/Custom-Drum-Builder-Template...
Koko's Jig, https://pdgood.us/drumshed/koko.html
Circlamp Jig video:
Supplies
Tools and materials used: Table saw, Miter Saw, Router/Table/Bits, Drill/various bits, 8' 1x3 oak wood, 8' 1x3 poplar wood, wood glue, painters tape, sandpaper, cognac stain, polyurethane spray,
Hardware is from Drum Factory Direct, 10 - double ended tube lugs, 20 - tension rods, 1 - 10 lug batter side hoop,1 - 10 lug snare side hoop, 1- air vent, 1- throw off/strainer, 1- adjustable butt plate, 14" - 42 strand snare wires, 1- 14" snare batter head, 1- 14" snare side resonant head.
Step 1: Cutting and Ripping the Staves..
First step in this process is cutting the wood. Being as precise as possible is a huge help. I included pictures from a site i used to help reference the cutting angles. Since I'm making a 14" diameter drum i had to make sure the staves were wide enough on the outer side of the drum to round down to the actual size of the drum. a 14" drum is actually around 13-7/8". I'm making this drum using 20 staves.
Getting the angles - First i divided 360 degrees by 20 staves to get 18 degrees. Since the 18 degree angle is going to be shared between two staves, i then divided 18 by 2 to get 9 degrees on each side of the stave. i set my table saw to 9 degrees and checked the angle first using a scrap piece of wood.
Getting the width - Outside diameter (14") multiplied by Pi (3.1415) divided by the number of staves (20) = (2.19905) I rounded up to 2.245 to add room for error when rounding the shell.
Ripping the wood - I recommend ripping the wood using the longest pieces possible to keep from getting my hands too close to the blade. I ripped the oak and poplar down one side each board and checked my angle to be at 9 degrees. Then i adjusted my fence on my table saw to have the outer with be at 2.245 using a scrap piece first to make sure it was accurate. I then proceed to rip the other sided of my boards to get all the staves equal in width.
Chopping the staves - I wanted to make a 7" deep shell for my snare. I used my miter saw, set a block on the saw at seven inches and checked my length using a scrap piece. I then cut the oak and poplar wood down into 10 pieces each at 7" long..
Step 2: Glueing the Staves..
Once you have the staves cut to size its time to arrange and glue them.
I alternated the 20 staves Oak/Poplar moving them around until i found the pattern that pleased me. Once the pattern is determined i laid them all down with the wider side facing up. Placed them against a straight edge and put one strip of painters tape across the center of all the staves.
I then stood them up and pulled them together into the rounded shape making sure all angles were together. Once all the angles were touching and lined up i wrapped painters tape around the entire outside of the shell sealing it completely.
After taping the entire outside i cut the tape at on joint and laid the wood out with the narrow side of the staves facing up. I used a brush and added wood glue to every joint making sure to cover every angle entirely on both sides.
As soon as i had the glue applied i stood the staves back up and put them back into rounded position. adding painters tape again at the seam i cut to glue the wood. I adjusted the staves to make sure all the angles were tight and placed large hose clamps i linked together on the outside of the shell. I put a clamp on the outer edges as well as the center and tightened them down making sure the staves stayed in line.
Once glued and clamped i cleaned up the excess glue at the seams and set the shell aside for 24 hours with the clamps in place to make sure the shell dried completely.
After the glue was set. I removed the clamps and the painters tape and proceeded to round the shell..
Step 3: Rounding the Shell..
This process has many different styles found online. The Jig i built for this drum is similar to Koko's Jig as its called in the forums I've found online.
Building the Jig - I used two 2'x2' pieces of MDF plywood, cut a channel out of the top for the router to slide on and a section out of the middle for the router to round the inside of the drum. I used bed rail angle iron for the track to set the router on. I will be creating an intructable when i build my new jig. for now i will include links to some jigs for you to reference on your own.
Rounding the outside - I first cut two circles at 13-3/4 inches to mount on the outside of my stave shell. I cut blocks and mounted them on the inside of the circles i cut to hold the drum evenly in place. Placed a 3/8" bolt through the center to clamp the circles in place on the shell. Placed the round circles on sealed bearings in my jig checked it to be rolling evenly and began the cutting process.
When rounding the outside it is important to have a sharp flat cutting router bit. I put my router on the rails next to the edge of the drum and set the blade depth to barely cut the corners off of the stave angles. i would roll the drum by hand on the bearings while moving the router over slightly until i made a complete pass over the entire drum. i repeated this process over and over cutting very slightly deeper each pass until i got the outside to a 13-7/8" diameter. Cutting very shallow helps prevent burning the wood when stopping. Learned this through trial and error..
Rounding the inside - I removed the round plates i mounted on the drum shell and adjusted the jig to fit the shell itself. Now that the shell is round i placed it directly onto the bearings and moved the router and rails to the inside of the jig. repeated the process for rounding the outside increasing the depth of the bit slightly and moving the router until completely passed over. Repeated the process until i had the inner shell rounded and the shell at 3/8" thick. The Two videos below are of myself rounding the outside and inside of the drum with the jig i used..
Step 4: Bearing Edges, Sanding, Staining and Sealing..
After the shell was rounded i proceeded to cut the bearing edges
I first put a 1/4" round over bit in my router on my table. I cut the outer edge of the shell on both sides to get my rounded over portion of the edge. this is for the drumhead to make even contact when placing on the shell. I tested the depth on a scrap piece of wood first before cutting the shell.
After the outer edges were cut. I swapped out the round over bit in my router table with a 45 degree angle bit. I set the bit shallow on my table, tested the cut on a scrap piece of wood and then ran the entire inside edge of both ends of the shell to cut the 45 degree inside edge.
Once all the cutting was done i hand sanded the entire inside and outside of the shell starting with 100 grit and stopped at 220 grit sand paper.
After sanding i cleaned the wood with mineral spirits. once it was clean and dry i hand rubbed the entire shell with a custom blend keda dye red color i made.. it came out pink... I then sanded it back down and started over using a cognac stain.. much better.... cleaned up the excess made sure it was evenly coated i then let the stain set.
after setting i lightly sanded it one more time just to bring out the grain a little. after it was where i wanted it I cleaned up the shell and applied a very thin layer of crystal clear spray polyurethane. I let the poly set and repeated this process three times lightly wet sanding between poly coats until the third and final layer.
Step 5: Installing Hardware..
This part is critical making sure the hardware is lined up. it honestly depends on how many lugs, what type, and such to how its laid out.
Making a template - I used a compass to draw a 13-7/8 circle. then marked every 36 degrees around the circle to get the center marks for my lugs. I placed painters tape from top to bottom of each stave on my shell that i was going to drill. Lined the drum up in the circle of the template with the center of the oak staves lined up with my marks on my template. used a square and drew a line on each of the ten staves from top to bottom.
Lugs - I measured the distance from center to center on the mounting holes of the tube lugs i used. Then found center on each stave between the top and bottom of the drum and marked the mounting holes centering the lug on each stave.
Throw off and butt plate - I used the template that came with the hardware and marked my holes accordingly directly across from each other.
Vent - Marked center of the stave and drum for the vent.
Drilling - With all of my marks in place on the painters tape, i started drilling for the hardware. I first used a tiny punch to indent the wood to keep from walking when drilling. i started with a 1/8" drill bit on all holes and increased the size of the bits by fractions on every hole until the required hole size was met. I did this to prevent damage from drilling too large of a hole and causing splintering. Also remember to let the bits work themselves do not push them hard to prevent splintering on the inside of the shell.
Once every hold was drilled i then removed the painters tape and cleaned the shell.
After it was clean i installed all of the hardware, greasing the threaded holes on the lugs for smooth operation.
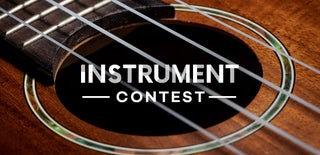
Runner Up in the
Instrument Contest