Introduction: CNC Arcade Cabinet - Built From a Nintendo Wii!
Welcome! I'm Dylan, a Grade 9 student attending LHS in Fall River, Nova Scotia, and I built a fully functional arcade cabinet - with a Nintendo Wii!
The Nintendo Wii was my first and favourite console. Some of my earliest and fondest memories include it. I even have a YouTube channel dedicated to the Wii, hence my username. I've always loved the console, especially due to its wide availability of controllers and games. Not to mention, everyone seems to have one! But the console is getting old, and I wanted to add some new life to it somehow. So I decided to build a full-size arcade machine to house it.
This arcade cabinet contains a specially modded Wii that plays almost any retro game you can imagine - NES, SNES, N64, GameCube, it's got it all! It has been built to support the GameCube controller, with ports easily accessible from the top so you can plug and play instantly. This arcade machine adds new life to the old console, but it also eliminates the mess of tangled wires and cords.
Unlike a traditional arcade machine, this cabinet doesn't have built-in controllers. That's because the Wii has such a vast and amazing library of controllers, and it would be unfair to build the machine only to support one of them!
As for the technical details, it was built out of scrap plywood and MDF. It runs on a 125V power supply and requires a single plug. The machine has no back, so you can easily access everything inside.
This idea is new to the Instructables Website. I haven't been able to find an arcade machine with a game console (or a Wii) inside of it, which surprised me. I chose the Nintendo Wii because it has sentimental value and is widely available, unlike high-end game consoles and Raspberry Pi. I'm glad I was able to build something unique :)
The project can be almost entirely completed through CNC. I have designed the pieces through Fusion 360, an Excellent 3D Design Software for both beginners and experts. However, this is also fully accessible to those without a CNC machine! All the steps and instructions support both CNC and from scratch.
I have included a TON of documentation for this project. This is a very long build, and perhaps challenging for some, so you'll want to take advantage of this extra documentation. NOTE: If you are unable to access the images on your network, A PDF is below that contains this entire instructable and all the images.
Now, let's begin building!
Supplies
This Project assumes you have basic knowledge of woodworking and 3D Printing. You need to know the types of saws, how to properly cut wood, types of wood, safety skills, and more.
This Machine has been built to involve as few materials as possible.
Here's an in-depth supply list. (note: these links are affiliate, meaning I earn a commission if you buy from them.)
Part 1: The Machine ($20-50 USED)
x1 Nintendo Wii (RVL-001)
You will need an original Nintendo Wii. RVL-001 is the codename for the launch wiis. If the lids on the top will open to reveal GameCube slots, you have an RVL-001. You must have this model! The cover to the ports must be taken off before building.
x1 SD CARD (At least 2GB, but no more than 32GB)
The Wii is only able to accept SD cards up to 32GB due to older hardware being used. Use this one for best results.
x1 USB Drive (32 GB or more recommended)
This is the one I used. The Wii can be very picky with these so I recommend you buy this one.
Part 2: Homebrew ($0)
To run emulators and games, you need to softmod your Wii. You CAN work without homebrew and use discs, but you are missing out on many awesome features. I recommend you download emulators like FCE Ultra for the NES and Nintendont for the GameCube.
Part 3: The Cabinet (Free-$80)
The cabinet was the hardest part to build, but the cheapest part of the project. Don't buy the materials new, as they are costly. Just salvage them from somewhere else.
- 1/2 inch plywood sheets (roughly 5 sheets 60 in. x 30 in. in size)
- 1/4 inch MDF sheets (5 sheets 60 in. x 30 in. in size)
These must be very polished and good-looking, as they are what covers the machine.
- Scrap 2-inch thick plank
- 2 Scrap baseboard pieces (30 in. long)
- Water-Based Paint of your choice (optional)
- Scrap Plexiglass (55x11cm)
As mentioned below, this cabinet can be built by CNC or by hand. The material list doesn't change. If you are using CNC you will also need a large CNC Machine.
Part 4: 3D Printed Section
As a final polish, I designed a custom cover for the Wii's GameCube ports. These are 3D Printable, made with Fusion 360.
- 3D Printer (100x100mm or more)
- Filament with your choice of colour
Part 5: Cords, Wires, and Extras ($40-150)
- wii2hdmi adapter (best option)
You should use the one provided as some adapters have very poor image quality.
- HDMI Cable
- 24" HDTV or monitor with HDMI (best option)
- Wii Power Cord (best option)
- Wii Sensor Bar (best option)
- Gamecube Controllers or Classic Controllers (best option/price)
- Plug Extender (with at least 3 plugs)
- USB-to-plug adapter
- Gaming Printout (the lighted banner for the front of the machine)
- 1M light strip
TOTAL COST: $60-280USD (much cheaper than I expected!)
Part 6: Tools
Multiple Tools were used in this project:
- Table Saw
- Handheld Buzz/Circular Saw
- Hand Saw
- Measuring Tape
- Nail gun (with 1-inch nails)
- Phillips Screwdriver
- Multipurpose Saw (not needed for CNC)
- Hot Glue Gun (and glue)
- 1" Screws and Cup Washers
Step 1: Designing and Planning the Arcade Machine
Roughly 2 weeks of planning and designing went into this project. Here was the design process!
Step 1: The Idea:
The idea for this machine started on Instructables when I found a design for a bartop arcade machine with Raspberry Pi. This was a brilliant little machine, but I had a problem. Raspberry Pi's are out of my budget (up to CA $150, yikes!) However, the Nintendo Wii is VERY cheap to find used. The one I used was a mere $15. I knew this would be perfect for a machine within my Budget. The Wii is widely available, and since the project was meant to repurpose old wood, it would fit very nicely into a repurposing project.
I also did not want to build custom controls for this machine like a regular one - I preferred the Wii's controllers over arcade controls. I didn't want to have to do any wiring or circuitry either.
Step 2: The Design
I would design this through diagrams. Some things turned out differently. For example, I intended to put a small cabinet into the machine, but I decided not to.
I drew everything, including the front, back, sides, shell, and insides. It's important to plan everything out before building because you never know what problems might occur during the build process!
Step 3: Design Requirements
I wanted to build this project to meet five criteria:
- The machine will be interchangeable with all Wii controllers. (this part eliminated the possibility of building built-in controls)
- The machine can be played by all ages (meaning the machine has to be low enough for children to reach, but big enough so adults can put it on a table and play it that way)
- The machine should resemble some aspects of a retro arcade cabinet (minus the built-in controller)
- Fusion 360 would be used in the build. I decided to make the machine CNC and 3D Printable.
- The machine would be able to be CNC'd or built by hand. This also filled the Fusion 360 criteria.
Step 4: Plan as you go
Things like measurements and what materials are used for what would all be done as it was built. In total, this project was built over 5 afternoons with two people, taking about 20 hours to complete. The instructable took about 15 to write and edit. So in total 45 hours of work. Yikes! I and one other person (a woodworking expert) built this project.
Step 2: Choose CNC or From-scratch
I wanted this project to appeal to both CNC users and DIY enthusiasts without CNC machines - so I made two options! You can either build this project with a CNC machine or you can build it completely from scratch. Keep in mind a lot more planning goes into the "from-scratch" version.
The CNC build is completely designed through Fusion 360. The build is exactly to scale.
If you are building the CNC version, many steps are not required to complete. They will be indicated as such. You need a very large CNC machine to build this. (the largest piece is roughly 55in. by 21in.) The CNC version is recommended for those who want a very nice-looking and polished machine. You can download the files either by looking below each step or going to the final step and downloading them all at once.
Some people do not have access to such a large and expensive machine. Since I wanted to make the project accessible to all, I decided to write the instructions to be compatible with making the machine fully by hand. Many more tools and saws are required, however, they are commonplace in any workshop.
Step 3: Build the Monitor Frame (by Hand)
Let's start building! (this step cannot be completed with CNC, as your monitor likely has different dimensions than mine)
When I first started, I figured it would be best to start with the monitor frame to find the width of the machine. I am using a 24" monitor. You MUST use the same size monitor.
Step 1: I measured the width and height of the monitor. (with the bezels) I marked this on a piece of small plywood.
Step 2: Then, I marked a bezel on each side as shown. The total measurement came to 73.5cm x 44cm. You must have that measurement. Here is a diagram of the layout.
Step 3: I cut the wood at the bezel point with a table saw.
Step 4: I marked out the size of the "box" on the back. This is different for all monitors. The hole would be slightly larger than this, so the monitor would be able to fit right on the front.
Step 5: Finally, I used a circle saw to cut out the monitor hole.
Step 4: Building the Walls
The walls are a crucial part of the machine. It supports the whole build, so you must have these walls built right.
Step 1: I cut out a large plywood sheet to match the dimensions shown. This took a long time to get correct!
This should be all the dimensions you need.
Step 2: Once I confirmed everything would fit on the monitor's frame, I used a circular saw to cut it.
Step 3: I traced another piece to match this and cut it out with the circular saw.
Now, you have your two walls. I'm starting to see some resemblance in an arcade machine...
Below is the CNC file for the CNC build. Print this model twice.
Attachments
Step 5: Cut Tons of 1"x2"blocks
To attach the walls, we explored many ideas. One was using 2x4s all the way across, but this would make the machine too heavy. I settled on attaching 2-inch blocks of wood on the corners and then putting plywood on top of that. I'm using inches in this step, but the rest of the steps are in cm.
Step 1: Cut a 2-inch thick plank of wood into strips 1 inch wide. We used a table saw to get accurate measurements.
Step 2: Cut these planks into 2-inch cubes.
Now, you have some cubes. These will come in handy in the next step.
Step 6: Build the Top
First, put one block in each of the top corners of both of the walls. Nail these blocks in.
Next, cut out a piece of wood to 73.5cm by 52.5cm. Put this piece on top of the blocks.
Finally, nail this down with your nail gun. Put 3 nails on each corner. In all the following steps, each block needs 3 nails. Here's a picture after I built it. You can see how the blocks work.
Below is the CNC file for the CNC build.
Attachments
Step 7: Attach the Monitor Frame
Step 8: Build the Front
I didn't have a piece large enough to reach down to the bottom, so the result was different than what we wanted. However, the measurement I have given will reach down to the bottom. I first measured out that piece, which was 60cm by 73.5cm.
Then, I cut that piece out.
Next, I nailed 4 2-inch blocks to the corners. These will hold the front frame. Finally, I nailed down the piece.
At this point, we were finished for the day, leaving some of the frame built and a lot more details figured out. We picked up the project again a few days later, after a lot of snow, rain, and wind. It's a difficult time to build due to the weather, but thankfully temperatures are supposed to warm up! I couldn't help but realize how big this thing was - it's hard to visualize the size when planning. Believe it or not, I went into this project thinking it would be a tabletop. Was I ever wrong 😂
Below is the CNC file for the CNC build.
Attachments
Step 9: Build Other Surfaces
Now, there are three surfaces left to build, not counting the back and banner. We did not make a platform for the bottom, as this thing was getting very heavy, and we didn't want to add extra weight.
First, we'll start with the aft panels as shown below. All we have to do is measure out the dimensions of the platform and cut a piece to match that dimension. Then, we have to nail 2-inch blocks into the four corners with 3 nails.
Finally, we'll nail the platform into those bricks. Make sure it is perfectly arranged.
And that's one of three done!
For the next two surfaces, apply the same steps. Simply measure out the dimensions of the panel, cut out a piece to match that, nail in two-inch blocks, and nail the panel in! Depending on how you placed the Monitor frame, the measurements can slightly vary. As such, I will leave it up to you to get the proper measurements.
And now, everything but the back and the front banner panel has been built. It's certainly coming along!
Below are the 3 CNC files for the CNC build.
Step 10: Build MDF Covering
For the CNC, all you need to do is print the files below. However, the MDF sheet for the monitor frame must be cut by hand.
I realized at this point how beat up my plywood was. So I decided to use thin sheets of pressed cardboard called MDF. This material is very light, and it's a lot nicer-looking than plywood. Plus, it can be painted over. The MDF covering was very simple. Just trace the surfaces and cut the sheet out with a circular saw, and smooth it with a hand saw.
And finally, nail it in with 2-3 nails in each corner. This is the difficult part. You must angle the nail gun sideways. This must be done because this size of nail gun has smal naill heads, and when nailed in flat, will just rip through the boards. Don't worry if the boards still become loose, we'll fix that on step 16.
Repeat this for all surfaces except the back and TV frame.
Now, let's move on to the TV frame. I didn't have any MDF wide enough for my frame, so I had to split the piece in two. However, the same steps apply. Just trace out the back and cut it out with a circular saw.
Now, the machine has been covered. It's looking a lot nicer now.
Below are the Files for the CNC build. As mentioned before, the Monitor frame must be cut by hand.
Step 11: Cut Out Console Hole
This step is not needed for CNC, as the files already come with the console hole cut-out. However, the 2-inch brick must be removed for the console to fit. Depending on how you nailed it in you may have already done that.
This step is more difficult, as you have to be careful. Here is the diagram I created. Mark this on your machine.
Now, use a Jigsaw to cut it out. We originally were going to use a multipurpose tool but the batteries died in it. Use what works best for you. Keep in mind that there is a 2-inch brick behind this and part of it must be cut off.
You should be left with this hole. The Wii should fit in it. Try and clean it up as best you can.
Step 12: Build the Console's Support
Now, we can build the support for the Wii. It's very simple. I will be using inches in this step.
I cut one piece of scrap wood to the required dimension and placed it below the opening. (1in. x 28in.)
Next, we cut a copy of the last piece and nailed it across, so the Wii would be able to sit on it (placed 5 in. from the last piece)
Finally, I cut out a small piece of plywood for the console to sit on. Use the nail gun to nail it down.
All Done! This support works if you are not going to move the machine around. However, you will need stronger support for that. The console will fall off the platform. For now, you can take the console out. You may also need to put a piece of wood underneath the Wii to prop it up, as the platform may not be fully flat.
Step 13: Mount Monitor/TV
Every monitor is different, so the steps to this vary. Here's how I mounted mine.
First, I unscrewed the base to the monitor with a Phillips screwdriver. This might look simple, but I spent almost 15 mins trying to figure out how this comes off.
Second, I fit the TV in front of the machine. It was just too short, so we had to prop it up. I used these little blocks.
I then took my special supports and screwed them halfway up the frame with 2 screws. You must make sure that the HDMI port and Power port are accessible.
Finally, I placed the TV onto those blocks and pushed it back into the frame.
Finally, the TV was supported! My TV isn't designed for mounting, so it will come out if pulled. I have no other way of mounting it, so I will have to work with this mount.
Step 14: Place Back Supports
At this point, I realized how heavy the machine was getting. Another piece of giant plywood for the back would make next to impossible to lift. So instead of building an entire wall, we just put a piece of plywood across and attached it to some 2-inch blocks. We also put a small piece at the bottom. Since the back didn't need to be covered (it was going against a wall anyway) this was a great solution. Plus, I can still access the cables on the back.
Step 15: Silicone Caulking/Sealing
There were some obvious flaws and cracks in the machine, and I was a bit stuck on how to fix these. Until someone recommended I use silicone sealant on the corners. This will seal the gaps (and any imperfections) on the machine and can be easily painted over. Before doing this, Take the TV and Wii out if you haven't already.
All you have to do is run the sealant slowly across the cracks or imperfections, and let it dry for a few hours. Don't run sealant across the hole for the Wii or the TV.
Step 16: Finishing Screws
I was still a little skeptical as to how well the nails were holding in the MDF. But I was a little stuck on how to fix it. Regular Screws would have looked ugly from the outside. But there must be a way to fix this. In shop class, I got my answer. My teacher told me that if you can't hide the screws, you must make them accent to the project. That means I would have to choose a type of screw that would look nice and still hold the project. So I used cup washers on the screws. These things make the screws look much better on the project.
To build this section, you will have to place them in each corner, and one in the middle of each side. Look at the pictures above for guidance.
Step 17: Cut Hole for GameCube Ports
This step is not necessary if you are building this machine with CNC.
One reason I love the Wii is its compatibility with GameCube controllers. Being able to play all my old GameCube games along with the regular games was a huge benefit to me and other gamers. So I decided to integrate this into my cabinet. I will only cut out two controllers, as four people crowding around this machine is next to impossible.
First, take the Wii out of the machine. Make sure the cover of the GameCube ports has been removed.
After that, mark out a hole in this dimension. I've already cut out the hole to show what it will look like. You may notice the hole is slightly shifted left of the hole for the Wii.
Once you have confirmed the hole will be the right size, cut it out with a multipurpose tool. Be careful, as once you've cut the hole out, it can't be fixed.
You should be left with this hole. It's a little rough, but that's okay, as we will 3D Print a cover for it.
Step 18: Print and Place Case
I custom-designed some casing for the Wii's Gamecube Ports to cover the rough edges of the wood. This was fully designed through Fusion 360. This software worked perfectly for both planning and actual 3D Prints. It may not look like much, but this casing is very important for the aesthetics of the cabinet. I should also mention that I'm a complete beginner on Fusion 360, so my final product will not be as polished as a professional. Here are some of my design steps.
First, I used a measuring tape to get the dimensions of the hole.
Then, I opened up Fusion 360 and drew out the first measurement using the "create sketch" tool.
Now, I can pull the rectangle up to make it 3D. I brought it up 25mm.
Next, I'll make a slightly smaller rectangle on top. I'll push that down to remove it.
Finally, I'll bring out each top corner 20mm to create the bezel. This is what will cover the rough edges of the wood.
Now, you can print the file below. I used 20% infill, with no supports. My Printer is an Ender 3, however almost every printer is big enough for this Model.
Once you've had a successful print, simply place the print face-up into the hole for the GameCube ports. You will have to slightly trim the edges of the wood to make the piece fit. If needed, hot glue the print onto the machine. I didn't want to make screw holes as I thought it wouldn't look great. I also needed to remove the screw on the left of the cover.
And that's it! While the model was very simple, it looked much better than the rough MDF and fit perfectly. I was very happy with the result! Download the file below.
Attachments
Step 19: Build Banner Frame
This part is a difficult one. I had to find a material that would be wide enough to fit the frame but thin enough and able to be cut. I don't have a glass cutter, so glass is not a viable option. So I settled on plexiglass, which I would have to cut in two. This step should be completed inside, as outdoor elements can cause damage to electronics.
Before I started to build the frame, I placed my light strips facing the banner. This allows the panel to be backlit and adds a nice effect to it.
First, I cut a piece of plywood to this 73.5cm x 17cm. Next, I cut a hole in the wood to 51.5cm x 9cm. There is a 40mm bezel on the top and bottom and a 105mm bezel on the left and right.
Finally, trace this onto an MDF sheet and cut that out. You will be left with two identical pieces.
Next, we will prepare the plexiglass sheet. I used a giant scrap piece. It was dirty, so I cleaned it to make it as transparent as possible. First, make sure your piece of plexiglass is 55cm by 11cm. If it doesn't, cut it with a table saw to match that.
Now, place your plexiglass behind the plywood so it is perfectly in the middle. Drill two holes on the ends but don't drill through the Plywood.
Finally, put screws into the drilled holes and screw into the plywood.
Now, place your graphic onto the plexiglass. I printed out the Nintendo Logo since I'm going to be emulating Nintendo games. I hot-glued mine but stapling it down is also a good option.
Now, place the plywood into the frame of the machine. Nail it in with your nail gun. Put two nails on each corner.
Finally, place the MDF frame onto the plywood and nail it in. You can also use cup washers and screws for this.
All done! I must say that I'm a little disappointed with how poorly backlit this is. So if I could make a recommendation to you, it would be to buy a longer and/or more powerful light strip.
You can now plug in the Wii, TV and USB Adapters. Hopefully, nothing explodes! :D
Below are the CNC files.
Step 20: Paint the Machine (optional)
Well, I originally planned to paint my machine - but I liked the colour of the MDF sheets, so I decided to leave it like this! It gave the machine a true CNC look. Eventually, I will paint the machine because the silicone sealant bothers me a bit... but for now, I'm satisfied. Let me know what colour you did in the comments.
NOTE: If you are painting, you must place tape over the glass panel to prevent accidentally painting it. Take out the Wii and TV as well. Use a water-based paint for best results.
Step 21: Finished!
It took a while, but we have finally built the arcade machine. I added some decor, such as a Mini Arcade Machine and RGB mousepads and lights. I also put a small desk by the machine to put the accessories/controllers on. Now, grab your controllers and start playing! :D
Reflecting on this project, I realize it was a challenging but fun project to make over a few days. It adds new life to my room, which is in the process of being turned into a games room. If I could have any recommendations for you, it would certainly be to work in warmer conditions or a wood shop. It was very cold and windy. I'm not sure what I was thinking, building an arcade machine outside in a Canadian Winter 😂
Post your make if you built it - It's always fun to hear about other people's creations. Please give the project a favourite - this took 30 hours to make, so your support would mean a lot!
My name is Dylan, and thank you for reading/building!
Step 22: All CNC Files
If you wish, you can download each CNC file here. They come in .f3d format, so you need Fusion 360 to open them and convert the file to your needs. Hope this helps! (Print "Wall-CNC" and "WallMDF-CNC" twice)
Attachments
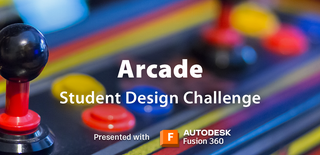
Runner Up in the
Arcade Student Design Challenge