Introduction: CNC Controlled Paint/glaze Spraying
In this instructable we'll see how we can start from a CNC table and turn it into a computer controlled spraying station in order to create specific patterns.
In order to do this, we created a system powered by pressured air.
----
This project is part of sprayramics, a collaboration between my studio, Mekanika and Biskt to develop a spray system for ceramic glazing. It was supported by the creathriv grant and was co-funded by the European Union’s Single Market Programme.
Supplies
CNC Machine : we used a mekanika evo S
Paint/Glaze container : for this we used a swimming pool filter container. We knew such a container can wisthand pressure.
Tubes and fitting: in our set-up we used 6/4mm diameter for compressed air and 4/2mm diameter for paint/glaze.
compressor: a compressor able to deliver 2Bar
Nozzle: this is the tricky part, we sourced ours from aliexpress but you might have to choose a special one depending on the material you are trying to spray. We also tried with an aerograph which gave really nice results.
Paint: For our test, we used water based paint, and iron oxyde which worked well. We also tried clay slip, but it ended up not working and clogging the nozzle.
Attachments
Step 1: Modify the Machine to Protect the Electronics and Add a Receiving Container for Sprayed Paint/ceramic
To begin adapting your CNC for spraying operations, focus on protecting sensitive components and setting up an efficient workspace:
1- Electronics Protection:
As a first step we modified the placement of the elements of the CNC to make sure that nothing was in the way and to place the electronic case on the side.
2- Spray Receptacle Installation:
Install a container below the spraying area to catch any excess paint or glaze. This container should be easy to clean and made of a material that can withstand the chemicals in the paint or glaze.
We went through different iteration concerning the receiving containers, notably using a big plastic box in order to be able to remove the excess easily. Eventually we ended up with a custom wood version that felt a bit cleaner, however, this proved very messy when using less viscuous paint.
Step 2: Create the Compressed Air System
The system we devised to create the CNC sprayer is relatively straightforward.
The air comes out of the compressor at 2Bar and then goes to the automatic valve that is controlled by the CNC (starting and ending it when job is finished). -> this step is optionnal and will not be explained in details here. Alternatively, you can open and close the air flow of your compressor, or use a manual valve.
From the automatic valve it is separated in two, one goes into the paint/glaze container and the other directly in the nozzle head.
Another tube start from the paint container to go to the nozzle head.
It is important to have both air and paint going to the nozzle since it is what ensure the pulverisation/spray of the material through what's called the venturi effect.
Step 3: Create Your Drawing (DFX)
The point of this tutorial is not to cover CNC machining as it is quite a big field. I can recommend these tutorials if you want to get started.
Now you can create a drawing in DFX (using Fusion, illustrator, inkscape or any other software...) that will be read by the CNC, alternatively, you can create an operation on fusion360 controlling the height of the nozzle (be carefull not to crash it in your base material).
Step 4: Run the CNC to Draw
You can then upload your dfx on planet CNC (or your CNC software) and print it directly.
You can experiment with the feed speed and viscuosity of your paint to get various result. More viscuous paint will allow you to go slower and have sharper corners while having less viscuous paint can have a nice dripping style. We also experimented a lot with the aperture of the nozzle which control the paint flow.
In our opinion we had the best result with relatively low pressure (1,2Bar) a small aperture and a relatively high speed (between 10000 and 20000mm/min).
Step 5: Obligatory Safety Precaution Step.
Using a CNC and solvent can be dangerous for your health on the short and long term. Please be cautious and use proper protective equipment.
Safety Precautions
Personal Protective Equipment (PPE)
- Respirator Mask: Always wear a respirator mask to protect yourself from inhaling harmful vapours and particles. This is particularly important when working with paint or glazes that can release toxic fumes.
- Safety Goggles: Protect your eyes from splashes and particles with safety goggles. Ensure they fit securely and provide a seal around your eyes.
- Gloves: Use chemical-resistant gloves to prevent skin contact with paint and solvents, which can cause irritation or allergic reactions.
- Hearing Protection: Operating a CNC machine and compressor can be loud. Use earplugs or earmuffs to protect your hearing.
Machinery Safety
- Machine Guarding: Ensure all moving parts of the CNC machine are guarded to prevent accidental contact. Never bypass machine guards or disable safety features.
- Emergency Stop: Familiarise yourself with the emergency stop button's location on your CNC machine. Ensure it is easily accessible during operation in case of an emergency.
- Proper Training: Before using the CNC machine, especially after modifications, ensure you understand its operation fully. Incorrect use can lead to accidents.
Compressed Air Safety
- Secure Connections: Check that all hoses and fittings in the compressed air system are securely connected and in good condition. Loose parts can detach under pressure, causing injury.
- Regulate Pressure: Always use a pressure regulator to control the output pressure of the compressor. Never exceed the recommended pressure for your equipment and materials.
- Avoid Direct Air Streams: Never point an air nozzle at yourself or others. Compressed air can cause serious injuries if directed at body parts, particularly the eyes and ears.
Handling Chemicals (when using glaze or non water based paint)
- Ventilation: Work in a well-ventilated area to avoid the accumulation of toxic fumes. If indoors, use fans or an exhaust system to maintain fresh air circulation.
- Proper Storage: Store all chemicals, paints, and solvents in a cool, dry place away from direct sunlight and heat sources. Ensure all containers are properly labelled and tightly sealed.
- Spill Management: Have a spill kit readily available in case of accidental leaks or spills. Know how to use absorbents and dispose of hazardous waste safely.
Step 6: Optionnal - Connect Your Valve to Planet Cnc
In our configuration, we used the mist function in planetCNC to open and close the valve at the beggining and end of each job through a relay and a 24V valve similar to this.
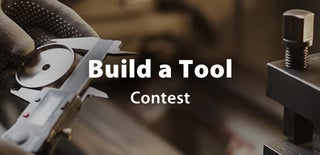
This is an entry in the
Build-A-Tool Contest