Introduction: COGBLING Ear Studs
This Instructable is related to the crafting of ear studs from ‘found stuff’ and watch parts.
I don’t use the term ‘SteamPunk’ in my description, because although these are close to that wonderful style, I don’t think they represent enough of the ‘functional’ purpose required of that genre.
Hence my term: Cogbling. If anyone else claims ownership of this term I thank them sincerely for letting me use it.
And so to begin: Picture 1 shows a typical product of this process. It’s not the one we’re making, it’s the one I wear most of the time. Sorry if my scraggly white beard offends those of a more squeamish disposition.
Step 1:
This main resource required, as shown in Picture 2, is a bunch of watch parts. There was a time, a few years ago, you could have scrounged this scrap by the pound, at little or no cost. Well those days are over, and if you want this material you now have to pay a lot of money from a source such as eBay.
Step 2:
When I get my consignment, I go through it carefully, sorting out and putting to one side these plates, Picture 3. These plates are available in all watches, but obviously the larger the watch, the larger the flat plates rendered. The lovely thing about these plates is the wide range of shapes they have. They form the perfect foundation for my creations.
Step 3:
Picture 4, I also purchase another raw material, which is brand new stud earrings. These particular ones come in numerous colours, and are made of resin and surgical stainless steel. They are not expensive, and they are ideal for my purpose as they have a fairly stout stem.
Step 4:
To begin the project I gather a suitable foundation plate, and an ear stud, and sometimes a piece of watch to go under the stud for added texture. Picture 5.
Step 5:
Picture 6 shows the three items being glued together. The use of a ‘third hand’ device, to my mind is an absolute necessity. I use cyanoacrylate (superglue,) though I believe in the USA most ‘jewellery’ makers like something called E600, or E6000. That stuff is fearsomely expensive in dear old blighty, and as I have had great results from superglue, I’ll keep with it for now.
Step 6:
Once the initial arrangement has set solid, I re-arrange the piece in the jaws of the third hand, for continued additions.
Picture 7 shows the addition of a couple of objects. I try to create a 3D affect and texture, by choosing some deep objects, some tall, and some flat. The spring-holding cups work very well to create ‘an arrangement within an arrangement,’ effect.
Step 7:
In Picture 8 I continue to add more parts - the larger ones at the bottom, then smaller ones stacked as required. This is the time when you need to go slow, and consider carefully that looks right and what is going to be too much. Obviously one consideration is the structural integrity, so it’s important to ensure that each item added has plenty of foundation onto which it can be glued. Any item attached over too small an area is likely to be knocked off the piece at some stage, which is obviously an unwanted occurrence.
Step 8:
Picture 9 shows the end result for this particular piece. I have added some particularly small items into the ‘cup’ at the top of the picture, to add depth, texture and interest.
Step 9:
Picture 10 shows the underside of the piece, showing that the supporting plate provides very comprehensive support for the added parts.
Step 10:
Pictures 11 to 17 are other examples of this technique. You can see that depending on the type of watch plate used as a foundation, there is a broad range of sizes and shapes of end products.
You will also see that in the extreme macro photography the ear studs seem to have a slick coating of some sort. This is down to a couple of coats of clear nail varnish I apply as a final process. The varnish adds to the integrity of the end product, and under normal eyesight, in normal lighting, is absolutely invisible. It’s a shame, and frustrating that the macro photography has made these studs look a little weird - I assure you they do not have this ‘coated’ appearance under normal viewing conditions.
I do hope you like these things, and maybe you’ll have a go at making your own.
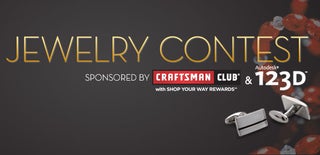
Participated in the
Jewelry Contest

Participated in the
Craft Contest