Introduction: Cast a Pewter Han Solo in Carbonite
Pewter is a great way to try out metal casting with minimal investment. It has a low melting point so you don't need to use a foundry, just a heat plate or gas burner. This allows you to easily remelt the pewter and try again if things don't turn out the way you want.
Step 1: Gather Your Supplies
In order to do this casting you need several things, most of which can be obtained at thrift shops or around the house. The first thing you need is the pewter. You can order ingots online but I went the thrift store route. This is harder than it sounds as most things that look like pewter are actually a different type of alloy that has a much higher melting point that you can achieve with this method. These pieces look and feel like pewter and are just as soft but they never melt with just a regular flame. The second picture shows several pieces that I swore were pewter but weren't. If it doesn't have a stamp stating Fine Pewter or Genuine Pewter just pass it by. I did find this candle ring that had the stamp I was looking for and later I found a mug that had also pewter stamp.
The second thing you need is a way to melt the pewter. I used the side burner on my propane grill and a stainless steel pan I picked up at Goodwill for a couple of bucks.
Now you need to make the mold. I made a small frame from some scrap wood and screwed on some 1/4 inch plywood on both sides. using screws is important as we will need to remove both panels during this process. As for the material to make the mold, I "borrowed" some of my kids moonsand. It is a fine sand mixed with a binder such as corn starch. There are a few tutorials on this site that tell you how to make your own or you can look in the kids section of your local retail store. Moon sand works great as it is designed to hold its shape and it can be reused.
Step 2: Repair
Since my 6 year old son is now obsessed with Star Wars (like his father before him), I went digging at my parents house for some of our old toys and I found this gem. It is my younger brother's Han Solo in carbonite that came with his Boba Fett's Slave 1 toy. The only issue is that some of the plastic near the head had broken off. I used a technique to fix it that has worked well for me in the past. Cover the part you want to fill in with painter's tape and then apply a layer of 5 minute J.B. Weld. Once it is dried, peel off the tape and you have a nice flat surface to work with. Make sure you give the repair a full 24 hours to fully cure before you start making molds with it as the repair will be a bit flexible until then.
Step 3: Make the Mold
Screw on one of the plywood panels and place what you want to cast face up in the middle of your frame. You want your frame to be deeper than what you are casting. Mine was just deep enough and if I made another one I would make it about a 1/4 inch deeper to give me a bit more room. Fill in the area around what you are casting with the sand making sure the sand is compacted and there are no voids. Carefully scrape off any excess sand from the top of the mold and screw on the second plywood panel making sure it is flush to the to top of your frame. Flip your frame over and remove what is now the top panel. You should see the bottom of what you want to cast and you can remove it with a pair of fine tweezers right before you are ready to pour. This should give you a nice mold to work with.
Not pictured, because I did it on a later pour, is that you should give what you want to cast and nice dusting of cornstarch to aid in the release from the mold. Just sprinkle it on and blow it off making sure you do not have any clumps anywhere as that will be reflected in the final mold.
Make sure your sand is dry. If not, gently warm it up with a heat gun on the low setting. If there is moisture in the sand it will turn to steam during the pour and bubble through your cast and cause the pewter to splatter when the steam hits the surface. This will ruin your cast and potentially splatter you with molten metal. You have been warned.
Finally, make sure that the work surface your mold sits on is level. If it isn't then your cast is going to be lopsided on one end or corner when you are done.
Step 4: Melt the Pewter
Here is where we will discuss safety. You will be melting and pouring metal. This can hurt if you get it on you. Wear closed toed shoes, preferably leather, leather gloves, long sleeve shirt, and long pants. Also wear eye protection in case of splatter.
Place what you want to melt in a metal pan that you will not ever use for cooking again. Light up your heat source somewhere well ventilated (outside preferred) and starting heating your pewter. You don't want to heat it up too hot or it will start turning a yellow color. You will see what look like dirt floating on the surface of the melted pewter. This can be skimmed off with a metal utensil such as a spoon or a piece of bent wire (I believe this is called drossing). When the pewter has melted and is flowing, pour it into your mold until it reaches the top. Immediately after you finish pouring, give the work surface that the mold sits on a firm hit with your hand. This will assist the molten pewter to flow into the smaller spaces of your mold.
Step 5: Finish
Let it cool. You can remove the cast around 30 minutes after you pour if you wear leather gloves because it is still going to be pretty hot. Insert a metal or wooden rod into the sand and pull the cast over. Then use a nylon brush to clean off the moon sand. Don't use water on the cast until it is fully cooled.
I ran out of pewter on my first attempt only filling the mold 2/3rds from the top. I also had some wavy edges. The nice thing about working with pewter is that if it doesn't turn out the way you want it to you can just throw it back in the pan, melt, and try again with a new mold. The last picture is my 5th try using the same pewter. It has really good detail and will probably be a keeper.
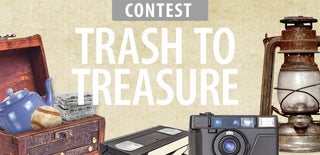
Participated in the
Trash to Treasure Contest 2017