Introduction: Championship Belt
I run a weekly Impro-Standup show in Melbourne: FNComedy.com.au
The comedians compete for championship belts and, here, I will share my techniques for making them (the belts, not the comedians, they do that themselves).
For this particular project I am making the "All-Australian" belt for a State of Origin series we are about to commence.
The belts take about 2 days to complete and use about $120-$150 in materials.
I'm not fully tooled-up to do everything I would like to do with these but each one is better than the previous.
Enjoy the ride.
Step 1: Design
Supplies:
Computer.
Printer
Thin card (I use old manilla folders)
Scissors or your preferred cutting tool.
Method:
Design the belt on the computer. My designs are deliberately derivative because FNC is a comedy show which has a look and feel of a wrestling show. If you are making belts for a Wrestling show, I would advise that you be a bit more original and creative in your design.
Keep the design to black and white. We will be making a resist mask and grey tones just don't work that well. High resolution is good but for this design I used a lower resolution to give more jagged lines. This gives the appearance of age.
I always design using 2 side plates. Some wrestling belts only have 1 and some have 4. I like 2. You are free to like whatever perverse thing you like and I won't judge.
Print out the design. I always make it to fit onto an A4 sheet as most of the materials and equipment I use can fit that as a maximum.
Cut out the paper plates and draw around them on the manilla folders to create a template for your leather.
Remember that you should only draw one half as the belts are symmetrical.
Cut out the design in full.
You should now have a complete paper mock-up of the belt.
Step 2: Preparing the Brass
Supplies:
Laser printer (not a Brother, they don't work)
2 A4 sheets of 1mm brass (I've also used copper, no difference)
A4 sticky vinyl sheets
Acetone
Soap (I use Solvol because it cuts through oil)
Synthetic steel wool pad
Laminator
Kiln brick
Heat gun
Leather gloves
Method:
Reprint the paper templates of the plates. This time flipping the image horizontally. Always print out a test image on paper and double check that it's correct. It's a real pain when you don't do this.
Also see if you need to make the image in negative. The black bits won't be etched and will be the raised bits. anything white will be etched.
Now that you've double checked that. (you did do that right?) it's time to make the resist mask.
I struggled for quite some time using the classic PNP Blue. Sometimes it worked and sometimes it was really fiddly and always it was really expensive..
Here's my trick: I use the backing paper from sticky vinyl. I have a vinyl cutter (we'll be using that later) and the backing paper works easy and perfect every time.
You can't use the paper from vinyl you have cut on the cutter because it will have very slight slices in it but the sheets cost me about 50 cents each (PNP costs me 7 bucks) and I use the vinyl anyway.
Carefully separate the vinyl and backing. Save the sticky vinyl. I conveniently have a not quite finished time machine in my workshop which is good for hanging the bits of vinyl on. You can use something else.
Print your flipped image onto the shiny side of the backing paper and put this aside where it won't get damaged. It will scratch and ruin the mask if you're not careful.
Now to my least favourite stage. You need to make sure there is no oil on the brass. This includes the oil from your fingers so latex gloves work well here. Wash the surface with acetone to get rid of the majority so that it doesn't just get spread around in the next step.
The surface of the brass needs to be fairly well scuffed to give the toner something to bind to. I use the steel wool and soap to scuff it and cut through any remaining oil.
And now on to my next trick. I preheat the brass to get it up to toner melting temperature before I laminate it. Hitting it with the hot air gun for a few minutes does the trick. Before you start pre-heating it make sure that your laminator is up to temperature, you need to get it in there pretty quick.
The difficulty here is that you only get one shot to drop the printed mask onto the hot brass. If you don't get it in one, it's back to the acetone/scuffing stage for you.
As soon as you have the mask and brass together, feed it into the laminator and give it 4 or 5 passes. Use the leather gloves unless you're made of asbestos (and if you are, don't come near me)
The laminator doesn't really like having sheets of brass going through it but, hey, I don't like umbrellas. Build a bridge laminator, build a bridge.
Let the brass cool so that the toner will solidify and carefully pull off the paper to reveal the masked piece.
Now take the piece of vinyl you put aside earlier and stick it onto the back of the brass sheet. This will stop the brass being etched from the back.
Also if you have large areas of unmasked brass on the front side, use some vinyl to mask it off to save using the potency of the etchant. You can just use plastic packaging tape if you don't have yards of spare vinyl strips like I do.
What do you mean you want to hear more about the time machine? If you behave, I'll give you another glimpse at the end.
Step 3: The Seven Year Etch.
Supplies:
An etching tank like this
500g of Ammonium Persulphate
Water
Acetone
Metal cutting/shaping equipment
Vinyl cutter (optional
Buffing wheels on a bench grinder/polisher
Drill/press
Brass polish.
Sealer.
Method:
After playing around with Ferric Chloride for some time, I happened across Ammonium Persulphate and life became better (and less stained).
Combined with the bubbling tank, this part of the process is now my favourite bit. It's where the magic happens.
Add 5oog of Ammonium Persulphate to 2 litres of water. Mix until the solution is clear. Pour into the tank. Using the heater tube, bring the solution up to around 50c.The etchant does nothing until it's warm. Once up to temperature, I usually take the heating element out. Firstly because it makes room for the sheet of brass but also because, even without it, the solution will increase in temperature. I think it's because of chemical reaction but I suspect it's something supernatural. Wear an amulet just in case.
Put the brass sheet into the tank and let it bubble away for about 20 minutes. Check every now and then for depth of etch. You can pull it out and put it back in as often as you like. I use pointy nose pliers to grab the board. They don't like the etchant much so don't use your mother's best pliers or you'll be grounded for weeks. Note also that the liquid turns blue as it etches. I usually get about 5 boards out of 1 batch of solution before its potency is reduced.
After the brass has been etched, rinse with water and clean the toner off using acetone.
Now cut the plate down to shape. I use a combination of snips, bench sander, disc sander, dremel and the inverted jigsaw type saw thingy shown in the photo above. You can use whatever you feel comfortable with.
Once shaped and edge-smoothed, the next step is to drill holes for the rivets.
Now polish the plate using a sisal buffer attached to a bench grinder. Finish it off with a calico buffer, then some brass polish and admire the shine.
The plates (including the side plates) need to have a curve to them. If you have access to a thigh, I have found that to be about the right shape. I always carry at least one with me at all times so I find that really convenient. Just be careful not to over-bend it.
After that I cut lettering/images to fit on my vinyl cutter. I only do this because any attempt to paint on the brass has failed dismally. I am looking into UV enamelling at the moment but if any of you have suggestions, I'd love to hear them.
Now the plates just need to be sealed. I use a urethane varnish but I'm sure there's something better out there.
The plates are now finished and can be put aside for a while.
Step 4: This Bit's Cut and Dyed.
Supplies:
A fairly decent chunk of leather.
Scissors/shears/cutting knife.
Edge beveller
Scrap of denim
water
Leather dye
Leather sealant/wax
Method:
You'll need a fairly large side of leather. I usually only get 2 out of a side because they have to be cut on the diagonal. The belts are larger than 4ft (1220mm). Also, don't skimp on the thickness. It's the thickness that will give it credibility.
Lay the previously made templates onto the leather and mark around them. I usually just cut the belt out with really sharp dressmaking scissors but you can use whatever you like.
Sand the edges lightly to get rid of any lumps and bumps.
Use a leather edge beveller along the top and bottom of the edge all round.
Apply water to the edge and burnish vigorously with the scrap of denim.
Apply dye as per the instructions on the bottle. I usually use black which is way easier than trying to get an even coating of green as I did on this one. But green and gold are the colours of Australia so green it is.
Seal the belt. I don't really know what I'm doing here but I used some shoe polish/wax and that seemed to do the trick.
In future I would like to add stitching around the edge and probably some fancy tooling but I don't have the gear to do that so, next time.
Step 5: Get It Together
Supplies:
Awl
Leather punch
Anvil (or similar)
Hammer
Rivets
Large press studs
Drill
Method:
Make up a template for marking the positions of press-studs. Do it. If the studs don't match at both ends you won't be able to do the belt up.
Mark the positions with an awl or something pointy.
Punch the holes
Use the Press-stud tool to fasten them. There are 6 rows of Buttons to the right of the belt and 9 rows of catches to the left.
Place the plates on the belt and spend some time lining them up properly.
Drill holes through the leather. Make sure to put something under the plate to push the leather up into the rounded form.
Use the rivets to attach the plates. Real wrestling belts have these attachments hidden at the back of the plate but that's way too much effort and I like the look of the rivets.
That's it!
You were well behaved so I've included a shot of the inside of my time machine (WIP)
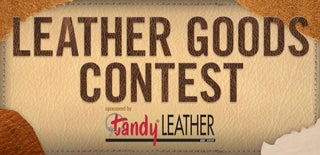
Participated in the
Leather Goods Contest