Introduction: Cheap & Easy Sand Blaster Nozzle
Tired of blowing through nozzles for our sandblaster and throwing money away, we needed a good solid answer for a better way. A member at Techshop (thanx Ken) gave us a great idea that gave us both a money saver and a longer lasting alternative.
Step 1: Getting Ready
Stuff Needed:
Old nozzle
Calipers
De-burring tool
Tapered end mill
Steel tubing
V-block
Access Needed:
Horizonal Saw
Jet Mill
Thanx TechShop for the access
Step 2: Bringing It In
Using the calipers on the old nozzle, I took the dimensions of it, and ordered the correct size tubing from a local vendor (thanx speedy metals). For our blaster, I needed a .25 ID and a .500 OD tube. Since this was a test I only ordered a 9" piece.
Then I was off to the saw to cut my pieces to length.
Step 3: Working the ID Form
Next, it was off to the mill. Using the Vblock, I clamped the part in and used my tapered end mill to give me a relief at the back end of the nozzle.
Step 4: Boom There It Is
Use the de-burring tool on the ID and that's it. The form on the front is for looks, so there is no real reason for me to pretty our version up. Our nozzles went from costing just over 3 dollars to just under 2 dollars and they last longer with equal wear on the ID.
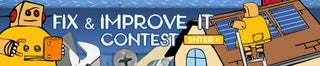
Participated in the
Fix & Improve It Contest