Introduction: Classic GMC Motorhome Repurposed for Elder Care
I gutted the interior of a 1976 gmc motorhome and built my own, this was done to aid in caring for my uncle Neal who has dementia and diabetes.
As far as I am concerned, the gmc motorhome was the single greatest thing that general motors ever created. It's features were ahead of it's time for any vehicle, let alone a motorhome. These included, lightweight jet age construction, low center of gravity, front wheel drive and many more, it is truly a shame that they stopped production after just five years in 1978.
Of the vehicles numerous features, there were two that mattered most to me for this project. One being the low step into the vehicle, for Neal who has difficulty walking. The other being the fact that the gmc, not only has a proper automotive body, but one that was intentionally built to have it's interior finished by non heavy industry third parties. Including a structure of aluminum ribs that have generous flanges for interior use that fit within the confines of 4'x8' sheet goods.
Let me restate that, It's as if General Motors built this thing just for me, or anyone, to make your own interior using normal construction materials.
Add to this, the fact that many of the original interiors were pretty terrible, particularly when paired with such a wonderful chassis. The most egregious insult being the overhead cabinets that cut off the top portion of the vehicle’s marvelous large windows. The layouts ranged from quite functional, to quite dysfunctional. The one we got had a bathroom with this weird child sized tub and shag carpeting under the toilet. Some of them even had a central vacuum system, you know, to maintain that shag carpet,.. I kid you not.
So this forty year old treasure, is uniquely ripe for custom re-imagination by individual makers.
Step 1: Get One, and Make It Run
The gmc was produced in two lengths, 23 and 26 feet, nine out of ten of these were the longer 26. I needed a 23 because it would just barely fit in our driveway. If you need a 23, expect to look a little longer and maybe pay a little more, as they are more rare.
A very good thing is that, for all things gmc related, there is a small industry of folks, selling and even making stuff specifically for the gmc, so getting parts for these is actually not a problem. In fact there are even upgrades that are readily available like rear disc brakes and improved suspension kits. There is also an active community of gmc owners in user groups or with websites sharing information on these wonderful machines, I will provide some links.
A forty plus year old vehicle will likely need more than just the interior worked on. Among many smaller repairs, I had the oldsmobile 455 engine and turbohydromatic 425 transmission rebuilt locally. I also had the final drive swapped for one with limited slip and also lower gears for better hill climbing while towing. Once the mechanic had removed the engine and trans, I had the vehicle towed back home so I could continue working on the interior, while the engine and trans were rebuilt.
The vehicle has ample power and handles well for something this big, I actually enjoy driving it.
Step 2: Gutted Interior, New Floor.
Nothing here put up too much of a fight, I did find that many of the old screws were something called clutch drive, which I'd never heard of, I found some bits at mcmaster car.
Look at that exposed structural aluminum frame supporting both aluminum and fiberglass outer skin panels, how could this be a gutted motorhome? you'd think you were looking at a gutted aircraft hull.
I removed the old holding tank and patched the largest holes in the old plywood floor and covered the floor with a layer of 1/4" baltic birch plywood, glued and stapled, over this I glued a piece of linoleum.
From here you could build one of these out for any number of purposes, motorhome, work van, small bus, ambulance, mobile studio etc. The techniques I will describe could be used and no doubt improved upon for all manner of applications.
Step 3: Roof and Exterior
Before we go any further, let me explain my criteria for every decision made here, which were always for function and speed of construction. It was important that I get this project together in a timely manner so Neal could start benefiting from it's use. I wasn't aiming for pretty, and in some places it shows, particularly where the exterior is concerned.
I removed the old roof vents, roof ac, storage pod, cargo rack etc and removed the top side rails to expose the body seam that lies underneath. Normally this seam would, after repainting the vehicle, be filled with sealant. I chose to do something quick and effective, albeit a bit crude. I found this roof sealant tape called eternabond, I figured this would be very fast and likely effective. I covered the seams and patched all the old holes with this same tape. On the larger holes I used a piece of thin aluminum sheet and covered that with the tape. I cleaned, sanded and cleaned with alcohol all areas to ensure good adhesion of the tape.
I chose the solar panels to fit as much as I could between the two roof vents, I mounted them with simple z brackets and 1/4" bolts through the aluminum roof skin to fender washers and nylock nuts on the inside. I also mounted an in motion satellite tv antenna, new ventilators, and a cell booster antenna.
Step 4: Wire It Up
Plenty of room for wires to pass through the aluminum ribs.
I reused many of the existing holes and drilled new ones where needed and installed new rubber grommets in all.
While I made no drawings for this project, I knew where all of the major components would be, like the batteries, inverter, pumps, fans and lights and ran wires accordingly. Naturally there are a few that I over looked or later wished I ran to a different point, but not much.
The fanciest thing I did was provide for a two way switch so that Neal could operate the lights from either his bed or his chair, which worked out very nicely.
Step 5: Cieling and Walls
In addition to the ribs, gm also provided a tang at the top and bottom of the walls and on either edge of the ceiling, that were used with 1/8 plywood door skins that were captured by these and popped into place. I wanted thicker material more solidly mounted to the body, to which I could mount lights and other things. So I didn't use the tangs and instead mounted plywood to the ribs with 10-24 screws. A drill bit in one cordless drill and a tap in another, I would drill and tap right through the wood and into the 1/8" aluminum and install a screw. I used pre finished 1/4" birch plywood for the walls and 3/8" bender board for the ceiling.
The place I get the 1/4" birch plywood from has two flavors, birch and baltic birch, the former is also available with a finish, At first I used the finished stuff wherever I could because I wanted to save time finishing, if I were to do it again however, I would use only the baltic birch which is a full 25% thicker than the other stuff (even though they call them both 1/4"), and higher quality with thicker outer plys, and then just brush or roll clear water base verathane, like I did on the ceiling and elsewhere. I have found that the pre finished finish is very thin and goes to crap at the smallest amount of moisture, and also splinters more easily.
The ceiling has a tighter radius at the sides so I decided to use the bender board, which was only available in 1/8 or 3/8 so I went with 3/8". The bender board is not as hard or dense a wood as the other but it bends like crazy in one direction.
I've seen pictures of other gmc's with sprayed in foam, ours has individual pieces of eps planks, which I thought was great because these came out cleanly leaving the hull exposed for wiring and other work. I put these back in where I could and used some soft insulation to fill in where needed. I'm sure that sprayed in foam would be better insulation and perhaps more sound deadening, but I didn't want the mess and I like the fact that I could remove it if ever needed.
I removed and rebuilt the the windows with new rubber and installed them with rtv, which is more permanent than I would like, but it allowed me to eschew the original window retaining hardware and plastic interior window casings. Here's what I did, I installed the plywood on the interior wall and then cut out the window opening with a router and pattern bit, running the router bit bearing directly on the aluminum window frame, this worked great.
Step 6: Panels Panels Panels
I built all the panels, every shelf, counter, dividing wall etc. as a
stressed skin panel. These are a composite of 1/4" plywood and eps foam.
A stressed skin panel is an incredibly efficient engineered scheme, in which the structural material is only placed where it can do the most good. I have made benches, tables, this motor home interior, and a 4000 sq/f building, from stressed skin panels of various types. I believe that most of the panels in the world would be better served if they were built as stressed skin panels. Here in particular it is great to have such strength without so much mass, a motorhome is heavy enough already.
I am already set up for making these particular panels because my wife and I make these upholstered benches and sell them at our website, SpiralConeLegs.com I make the bench panels and the legs and she does the upholstery. I have included a photo of one of these benches, sans upholstery, with over a thousand pounds of gravel stacked on top to illustrate the strength of these panels. I've also made an instructable for the benches.
A stressed skin panel consists of a structural skin and a lightweight rigid core, like a surf board, hollow core door, or airplane wing.
I make these panels with 1/4" plywood, 2lb density eps foam and wood glue, I use titebond 2 or 3. We make the benches in lengths from 3-feet to 8-feet. I use the same 1/4" ply for each but a different thickness foam, this gives me a thicker stronger panel for each progressive bench length, just by adding more foam. I use a notched trowel, which is fast and that's important as you need to get the glue spread and the panel assembled before the glue dries. You can pile a bunch of flat heavy stuff on top in order to clamp it while the glue dries, or make some sort of clamping fixture, my latest is 2-feet x 8-feet, made of 6-inch thick ssp's and utilizes pipe clamps.
Along all exposed edges, or anywhere I foresaw the need for an anchor, is solid plywood. This makes for a robust solid wood edge with that beautiful birch ply edge grain and makes for internal solid anchor points for later assembly. Of course building all of this on the fly and just in my head, I later needed to anchor in a number of places that were not solid, so in those places I used the attachment hardware that I have developed for the benches which have no solid cross section.
Step 7: Crapper
To conserve space and to meet Neal's needs, we needed a wet bath with as low an entry as possible, A wet bath is one with the toilet doubling as the shower seat.
I placed the bathroom on the side at the smaller rear window, which is in between the wheel wells.
I needed a rather narrow shower pan, I found one, sierra #235 that that was close enough, with modification, to save me from making my own. I glued it to a piece of plywood with spray foam and built up one side with laminated plywood and bondo and then sliced it to a smaller width removing the turned up edge, with a circular saw, this gave it a sturdy finished edge.
No vertical room for a p-trap here, so I installed a running trap normally used for condensation lines, I figure if this fails to be a sufficient trap, I can always just stopper the drain in between showers.
Bathrooms are inherently complicated because of all the plumbing, I simplified this greatly by using a purchased composting toilet. This saved me from having to add a black water tank and macerator, I refuse to have one tank for both black and grey water, if you poop in it you cannot dispose of it as easily.
The interior of the bath is lined with frp to increase water resistance. the shower head bar is also a safety grab bar that is centered in front of the toilet.
Step 8: Electrical System
I wanted to use a regular electric refrigerator for ease of operation and to avoid damage from less than level parking, like in our driveway, so I made as big a system as I could, or was willing to fit.
Two, 340 watt solar panels, you can never have too many solar panels, and here it is a matter of how many can you fit along with other things competing for roof space.
Four L16 batteries, again, where to stop 2,4,6,8? 4 of these weigh 460 pounds and they are big, so I stopped at 4
A 4000 watt pure sine wave inverter that puts out 110/220 vac with built in automatic transfer switch and 115 amp battery charger. It's charger/switch requires a 220v input, so I also installed a separate 110v powered battery charger so I can hook up to either 110 or 220v shore power. the inverter's output hooks up to a regular household circuit panel with both 110 and 220 breakers. There are no 220v loads on board but I can steal juice from the motorhome to help power other things, like my cabin in the woods.
A 12v automatic switching relay with remote control for combining the starting and house batteries for charging while driving, or if necessary for jump starting.
Blue seas makes some very useful things, like these dc fuse panels, you can get them with or without ground bus and covers, I installed one at the main electrical compartment and another at the water system area, powered by a 2ga wire running back to the main compartment via a 150amp fuse.
The main electrical compartment is also the platform for Neal's bed, the mattress flips up and leans against the wall and the cabinet top leans similarly on a piano hinge.
Step 9: Overhead Shelves
I wanted to fit some storage overhead without blocking the windows in any way. Plastic bins on a shelf, no doors, very simple, fast and functional.
I purchased a few different plastic bins with dimensions that I thought I could work with and chose one, an akro bin #30255, then built the shelves to fit this bin. The bins come in different colors, which could be handy for organization but I got them all in black. I built four shelves, two in front and two in the back bedroom/dinette. These shelves could accommodate 13 of these bins, I use fewer than that with some of the shelf space used for blankets and such that don't fit so well in the bins.
I made the shelf panels with an extra lip of solid plywood to keep the bins contained. The shelves are anchored to the ceiling ribs with steel brackets that I accidentally made shorter than intended which caused the shelves to tilt slightly towards the wall, which looks intentional and I like it just fine.
Step 10: Back Bedroom
The back area converts from a double bed into a dinette.
You fold the center bed panel in half via a piano hinge and lift and place it onto the wall brackets and prop the other side with a leg which stows in the overhead shelf.
This rear dinette arrangement makes sense to me because of the compartment wells on either side of the rear of the rig, which are under the seats of the dinette.
Step 11: Kitchen
I made a mistake here in the kitchen, I did not consider the stove/oven dimensions when I chose a fresh water tank. The height of the tank determined the height of the lower shelf, if the shelf were a bit lower, then the original, or new equivalent stove/oven combo, would have fit. I decided to just put a stove top in with no oven for now, we really don't do a lot of cooking here anyway.
The counter panel is supported with angle brackets on the wall side and steel posts to the lower shelf and topped with formica. I recently added the safety grab bar made of 3/4" steel water pipe.
Step 12: Water and Space Heat
I am making a hydronic system, which is to say that the water heater will power not just shower and sink needs but also space heating needs, it will also allow me to pre heat the engine coolant for easier starting in extreme cold.
In the meantime I have temporarily installed the water heater and pump etc in a more traditional arrangement, and am using a portable propane space heater.
When I do complete the hydronic system I will add to this section and maybe make another instructable just for that.
I will include some photos of the tank and heat exchanger that I have built for this as a teaser.
Making this hydronic system is the most self indulgent part of the project. I just really wanted to do this, I am going to make a much larger system for our future home and shop, (under construction now for about half my life), and this allows me make a micro version of some of it's components. Also it is being made after the gmc has been pressed into service, so it is not causing a delay there.
Step 13: More Details
Neal's chair and the front passenger seat I got on ebay, a rear pair from a late model toyota mini van, these were chosen because they have a recliner function, Neal needs to elevate his feet for medical reasons, and also because they have built in seat belts. I built a simple steel base and topped that with a seat swivel that I modified to have two locking positions, one facing forward and one rearward for watching tv.
Neal has good and bad days, and as his condition has declined, a bad day now means he is incapable of walking, so I modified an aluminum ramp I got from harbor freight, so if necessary, I can wheel him in or out with a wheelchair. The ramp folds lengthwise and will stow on the rear bumper, I'm still working on that.
I removed and stored the original rear bumper and built one from a piece of 4" sch40 pipe and welded it to the frame. This was done to provide a sturdy hitch receiver for use with a toad and a utility trailer. It also provides a nice steel place to mount something, like the wheelchair ramp holster.
The lights are all led's, four small puck lights that are on one circuit and cover everything that Neal would need , (chair, bed, bathroom), these are controlled by two way switches at both Neal's chair and bed. I also placed two big flat panel lights which provide entirely too much light, in case I need a lot of light, for something like servicing Neal's insulin pump, or potentially bandaging a wound. There is also a small light that I can reach from over my shoulder when in the driver seat with a switch right on it, and two more lights in the back bedroom.
I installed a security camera from nest to keep an eye on Neal, like when I'm in a store and he's in the gmc in the parking lot. I also use these in the home for the same purpose and they are a life saver. I can see from my phone that he's ok, it also alerts me when there is motion. The camera connects to a network provided by a cell type internet device, I don't have this one camera on the cloud storage plan so as to save on bandwidth. I installed a roof antenna and powered cell booster from wilson for connectivity for the camera.
Step 14: And More Details
The safety grab bars, other than the one in the shower, are all made from 3/4" steel water pipe. This has a diameter of just over an inch so it's big enough for a comfortable grip. In most places I made these from just the pipe and weld tabs.
On the overhead shelf I added a safety bar that attaches to the already too short shelf brackets. I replaced the nut and washer with a weld nut which left enough threaded rod to then attach a coupling nut and then attached the pipe to these with a 1-1/2" screw, voila.
So far there are two of these grab bars on either side of the interior of the door, one on the edge of the kitchen counter, the one on the overhead shelf and two at the entrance to the rear dinette.
On the outside of the door there is a grab bar that I got from Ragusa who make some very nice cast aluminum stuff specifically for the gmc, like the step at the door and the license holder/step that I also installed.
Step 15: Well, How Does It Work? Was It Worth the Effort?
This was a large project and I certainly wondered at times whether it was the right thing to be doing. It was Neal's money and my labor, a not insignificant amount of each, and until it was largely complete, it was of no benefit to him.
Now that we are using it, those fears are long gone. It is absolutely wonderful, it frees me to leave the house without either leaving Neal alone at home, or having him simply sitting in a regular car seat without entertainment or facilities. It is easier for Neal to get in and out of than a regular car or truck, primarily because of the low floor and full height door. The floor is much lower than most motorhomes, as the original promo material said, you don't have to climb to get into a gmc, you step into it.
Even for errands around town or doctors appointments, it is the vehicle of choice. We have everything we need. Need to use the toilet? it's right there, change of clothes, take a nap, shower, watch tv, eat dinner, hell we even have ice. It is of particular value when we are at the cabin where a trip to town is an all day affair, I think without this vehicle, the cabin would simply be unfeasible. It is quite adaptable and I will continue to add things as needed, for instance the wheel chair ramp is the latest addition.
Step 16: Links Links Links
This list is by no means comprehensive, please recommend other gmc related links and I will add them.
In no particular order,
GMC motorhome - Wikipedia
GMC MotorHome: A New Standard in Motor Home Performance original promotional video, good stuff
Rubber Router Guide it's actually urethane
Mcmaster-Carr great resource for all things industrial, good usable website and fast shipping.
Shop4seats.com Swivel for Neal's chair
superbrightleds.com I got many of the led lights from here, and also some from amazon.
mannystransmission.biz Torque converter
Sierra engineering Shower pan #235
thegmcrv.com/blog Absolutely incredible gmc redo by fellow instructabler JustinB312
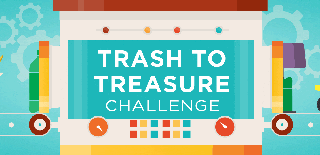
Second Prize in the
Trash to Treasure
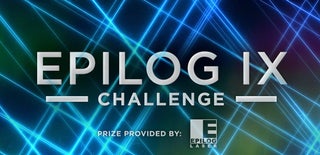
Participated in the
Epilog Challenge 9