Introduction: Computing Pipe Joints in Blender for Camp Stoves
Computing the interface between two pipes has long been a problem (at least for me). In High School we leaned how to do this using something called "Surface Developments". This was taught during "Advanced Drafting" classes back in the early 80s. The technique involved drawing the interface in a couple of views and then bouncing lines around the drawing so that the interface between objects could be drawn when rolled out flat.
Anyway, I stumbled on a similar method using Blender 3D. The idea is really simple - just draw the two objects stuck together. Then, tell Blender to find the intersection of the smaller pipe onto the larger. Blender will break the smaller pipe into two objects. One new object will be outside the larger pipe and other object will be what remains on the inside of the larger pipe. Just delete the unneeded new object on the inside. What remains is a beautiful blended (no pun intended) pipe interface joint between the two original pipes.
Next, turn on "Edge Length" display in Blender. Blender will now display a numeric value for any edge length highlighted. Bingo!
By drawing all the pipes to scale, Blender will display numeric values you can use strait away. To get more accuracy, if needed, the original pipes can be drawn with any number of vertices (or edges). The pipe in the attached pictures were drawn with 32 vertices, as an example, but this could be easily changed when first creating the pipe.
The next step is to take note of those magic numeric values by writing them down on a scrap of paper. This is were too much accuracy is a pain to deal with. Coping down 32 numbers is not to bad and gives good accuracy for me. The values will then be entered into your favorite CAD program. Most any drawing program will do as long as the printer output is not scaled. In other words, if I draw a 1" line it better come out of the printer exactly 1" long. I used LibreCAD for this project.
I've attached both the Blender file and the LibreCAD file to this step if you want to play with them.
Note, both Blender and LibreCAD are free! While free to use and enjoy, I find I must donate each year so as not to feel like a turd.
Attachments
Step 1: Results
Below are a couple snapshots of my Wood Gas - Camp Stove. These stoves are fun to play with but they need a little muffin fan action to really get cooking!
The first stove, in the attached pictures, had a simple interface between the cans. The problem with this design was too much heat. The inner firebox can gets cherry red hot and the radiant heat makes the muffin fan too hot.
For my next attempt, I decided to get fancy and tilt the muffin at a cool angle (pun intended). The muffin fan can is tilted up 60 degrees and rotated (relative to the large can's center axis) by 15 degrees. This was also my weak attempt to get the air to swirl into the larger can. While the swirling action may not be the best, the radiate heat problem was fixed. Note, there is only a relatively small hole in the larger can to let the air enter the stove. Most of the tin wall was left in place on the larger can. This provides a heat shield for the muffin fan.
Well, hope this helps folks sort out their pipe interface ideas,
Jim
PS: What more Wood Gas - Camp Stove pictures? Come to my web site: www.ph-elec.com I've got a ton more build pictures on my site.
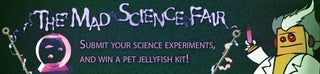
Participated in the
The Mad Science Fair
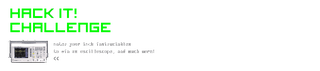
Participated in the
Hack It! Challenge