Introduction: Conductive Rubber: Make Touch Sensitive Robot Skin
Make conductive rubber and use it to create a flexible touch sensitive robot skin. The resulting skin can be stretched across a frame or mounted on solid surfaces. It can also be mounted on curved surfaces or clothing.
It is touch sensitive and will produce an electrical signal no matter where you press on it.
Step 1: How It Works
Step 1 pic shows a 3d exploded illustration of the layers that make up the robot skin. It was made using 123d. Thumb pic shows the edge 0f the finished robot skin.
Ideally, this robot skin could be 3d printed. With a more intricate pattern, the feel and resiliency of human skin could probably be achieved. Unfortunately, 3d silicone printing is beyond the reach of my limited budget, and as far as I know, no one so far is 3d printing conductive rubber.
Oogoo II-A Conductive Rubber
You can make your own conductive rubber from silicone caulk, corn starch, solvent, and graphite powder. This creates a silicone rubber which can be made thin enough to paint on or thick enough to cast into molds.
Oogoo II can be cast into sheets and then laminated to create a layered robot skin that conducts electricity when under pressure. The layers are designed to conduct between two layers, no matter where you press on the surface of the skin.
Step 2: Materials
100% Silicone Caulk from hardware store
Corn starch from grocery store
Carbon Graphite powder- Available from: http://www.elementalscientific.net/
Naphtha solvent from hardware store. Turpentine or Citrus solvent can also be used but they take longer for the fumes to dissipate.
Mixing cup
Popsicle stick
1/32" and 1/16 inch thick plastic sheets
Step 3: Make Conductive Rubber Sheets
Make A Form
Step 3 pic shows the form which is composed of two 1/16" thick phenolic sheets that are taped to a plastic base about 2-3/8" apart. I used phenolic because I have surplus sheets of it, but any kind of plastic can be used. Oogoo and Oogoo II will stick to any plastic but can be peeled off cleanly using medium force.
Mix Conductive Rubber (Oogoo II)
Oogoo II is basically Oogoo with the addition of graphite to make it conductive and a solvent (Naphtha) to make it possible to mix.
To create a sheet of Oogoo II about 1/16" thick x 2-3/8" x 3-1/2", add 3-1/2 parts graphite powder (by VOLUME) to one part silicone caulk to 1/2 part corn starch . A mix of 5-1/4 Teaspoons Graphite to 1-1/2 Teaspoons Silicone Caulk to 3/4 Teaspoons of Corn Starch gives more than enough to cast one sheet.
First mix the graphite and corn starch together with enough Naphtha to make a thick paste of the powders. Then add the silicone caulk and mix it very well with a popsicle stick or stirring rod. You want to end up with a mix about the consistency of smooth peanut butter.
WARNING: Naphtha is a sickly-sweet smelling solvent that wants to dissolve your brain cells if you breathe too much of it. Make the mix outside with good ventilation or
inside under a vent hood. Wear safety glasses and nitrile gloves, as it can be absorbed by the skin.
I tried at least a dozen different solvents. While other solvents can be used instead of Naphtha, it has the advantage that it evaporates extremely fast and most of the odor is gone in a few hours. Other solvents can take a day or two to dissipate and increase the set up time.
Mix in small batches and use it quickly before it starts to skin up. It will typically set up enough in two or three hours to de-mold. Let it completely set up overnight before using it.
Other Mixes
At about two parts graphite to one silicone caulk, the mix starts to become usefully conductive. Adding more than 3-1/2 parts graphite (by volume) to 1 of silicone will reduce the flexibility of the final rubber.
Screed The Sheet
Spread the mix carefully to avoid bubbles and screed it with a stiff piece of metal or plastic and let it set up overnight.
Step 4: Make the Insulating Spacers
Make the Spacer Stencils
The Three conductive sheets are held apart by insulating spacers. Pushing between the spacers creates a conductive path. The insulating spacers are the white dots that are made by screeding Oogoo in the holes in the stencils. The stencils are made by drilling 1/4" holes in 1/16" plastic sheet. The holes are drilled 1" apart with the holes in the second stencil drilled in between the holes in the first.
Screed the Spacers
Step 4 pic shows a small mix of Oogoo (2 silicone caulk to 1 corn starch by volume) being screeded on one layer of Oogoo II.
Step 5: Layers to Create a Robot Skin
Step 5 pic shows the four layers in the order they are laminated:
1. 1/16" top sheet of standard Oogoo which can be colored with artists oil paint. This provides the necessary resilience to the skin and protects the conductive layers.
2. 1/16" Oogoo II with insulating spacers (white dots)
3. 1/16" Oogoo II with offset insulating spacers
4. 1/16" Oogoo II base layer.
Glue Wires On
Before gluing the layers together, wires or conductive thread should be attached with Oogoo II to the edge of the 3 conducting layers. Stranded wire that is flared out works the best for a good mechanical connection. Conductive thread can also be used.
Glue the Layers Together
The four layers are glued together using a thin layer of Oogoo on the top sheet and small amounts of Oogoo on the insulating spacer dots. Do this a flat surface with a weighted flat sheet on top to flatten everything out as the Oogoo sets up.
Step 6: Testing the Robot Skin
The resulting robot skin has a resistance between 300 to 400 ohms when pressed with about 3 ounces of force anywhere on the surface. The top and bottom conductive layers are connected together to create a switch with the middle layer. The resistance is low enough that an led can be directly lit using five volts.
By varying the insulating dot spacing and thickness of the conductive rubber, the pressure of this touch sensor can be adjusted.
Step 7: Other Possibilities
Thinner Skin
This prototype robot skin came out at .4 inches thick. The five layers could be made thinner resulting in a skin about .25 inches thick. Even thinner skin might be made using conductive fabric instead of Oogoo II. The only limitation would be the thin plating on most conductive fabrics that might wear off fairly fast.
If you don't need skin that is touch sensitive everywhere, a three layer skin could be made that is only sensitive between the spacer dots.
Curved Skin
The layers can be glued up on a curved form such as a pipe. For compound curves, the sheets would have to be molded on a form with the proper curves.
Tile the Robot Skin
Oogoo II layers can be laminated behind a continuous sheet of Oogoo to create touch sensitive zones to give a higher resolution of touch sensitivity.
Human Touch Sensitive Skin
A two layer skin of laminated Oogoo and Oogoo II can be made that is sensitive to human touch. The capacitive touch detecting inputs of a Picaxe microcontroller can be used, or you can try this circuit: https://www.instructables.com/id/Curved-Circuit-Board-Art-Make-a-Touchless-Touch-S/
Touch Sensitive Clothing
Two layers of conductive rubber with spacers between, can be glued behind shirt fabric to make pressure sensitive switches for wearable electronics.
Human-Like Skin
Oogoo has a smoothness and texture very similar to human skin. By varying the thickness of the layers and the pattern of the spacers, a robot skin that has the feel and resiliency of human skin could be created.
Other uses
See here for another use for conductive rubber: https://www.instructables.com/id/Make-Conductive-Rubber-Transparent-stylus-iPodiP/
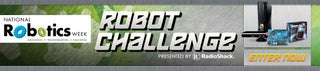
Second Prize in the
Robot Challenge
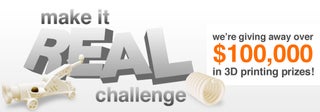
Participated in the
Make It Real Challenge