Introduction: Cookie Monster - Costume
Cookie Monster has been on my costume wish list for at least a decade, but I've been hesitant due to several factors - subpar sewing and patterning skills, uncertainty of a few design elements, and knowing it would take a lot of time. Historically, I burned a week of PTO for my yearly dose of costuming therapy. Long days in the shop, a few all nighters, racing towards the beggar's night deadline ... and loving every minute of it.
As fate would have it, I experienced a 2023 reduction in force and am currently in what we'll call a "professional transitional period". Obviously, I decided to do the right thing ... put the job search on hold, drop some coin on materials, and spend an entire month creating what may or may not be my best creation yet.
This lovable Monstrosity is a culmination of techniques and design experience I've acquired over the years, plus new skills ... some of which were painstakingly learned/earned.
Note: The step order of this Instructable does not reflect the actual order of fabrication, but hopefully it makes it more organized and digestible because the reality was 3-4 things happening at once. That'll also make it easier for anyone looking for design ideas/options of specific parts for costuming in general and/or easier for people to skip sections.
Note 2: Barge is my contact cement of choice, but I'm just gonna call it Barge for less typing/reading.
Supplies
Costume/Prop Materials
Royal Blue Faux Fur [4 yds]: $120.00 [Fabric Empire via Amazon]
Zipper: $9.97 [Zipperstop via Amazon]
Black Mesh - 4 Way Stretch: $14.50 [JoAnn’s Fabric]
Blue Thread: $2.39 [JoAnn’s Fabric]
1" [x2] & 1/2" [x2] Foam Padding: $71.94 [24"x72" Rolls][JoAnn’s Fabric]
EVA Foam Mats [x2]: $18.98 [Harbor Freight]
5.6" Styrofoam Balls [x2]: $6.38 [Michael’s]
Pex [x3]: $7.44 [Lowes]
Spray Paint: $7.98 [Lowes]
Nylon Straps/Clasps: $0
Total: $259.58 [Pre-tax]
Stage Materials
Pallets [x2]: $0
2x3 [x4] & Strapping [x6]: $19.40 [Lowes]
Drop Cloth: $0
Lights [x10]: $0
Total: $19.40 [Pre-tax]
Consumables
Barge Contact Cement: $32.72 [Amazon]
Sewing Machine Needles: $15 [Amazon]
Hot Glue: $0
Total: $47.72 [Pre-tax]
Grand Total: $326.70 [Pre-tax]
Step 1: EVA Foam: Foot Structure
Speaking of fabrication order, I started with with the EVA foam foot structure because I had the required materials/supplies, had no idea how I was making the body yet, and the fur had yet to ship. I concurrently made some prop cookies, but we'll revisit them after the costume.
After striking a center line on a piece of foam, I traced one of of my shoes and then built a Cookie Monster sized sole around it [Fig.1]. The Cookie Monster sole was cut out, shoe shape excised, and this effectively became my template [Fig.2]. Three layers of this template for each foot and then a solid Cookie sized sole to close the bottom [Fig.3-6]. Edges were then flushed up using the OSS [Fig.7]
Two of the shoe offcuts were reduced in thickness using the drum sander, but it's not totally necessary [Fig.8].
For securing my feet in a matter similar to ski boots, I use reclaimed nylon and clasp assemblies, which came from fleece blanket marketing swag. You could easily use strips of strapping and clasps, but I have these and they were free [Fig.9]. I chose to orient the female connectors to the outside and adhered them to the sole with Barge [Fig.10]. The Vans offcuts were then glued into the pocket atop the straps [Fig.11]. Thought process is that this would help hold them flat and even out the feel as I stand on them.
A test fit proved that my foot/shoe still had a tendency to lift out of the EVA, so I added a dual layer strip around the back and sides, as well as a strip across the toes [Fig.12-13]. I tapered the perimeter and toe strips to get as low profile as possible [Fig.14-15]. It's not pretty, but it works and it'll all get covered in future steps.
If you want less weight and hassle, you could try making the feet more like slippers and forego shoes, but the EVA is only 1/2" so I'd limit that to indoor use. I was outside with rocks, sticks, possible nails, etc.
Step 2: HD Foam: Butt Dome
Initially, I tired making the body as an oversized onesie with a drop crotch, which I would then backfill with padding to fatten it up. The prototype was with cheap cotton fabric, but I just couldn't get the desired shape. On a positive note, it did give me some much needed practice on the sewing machine. I was able to dial in the stitch type and length, machine tension, feed speeds, sewing mostly straight, etc. After three days of floundering with the concept, I decided to make a fat suit first and then let "Future BALES" figure out how to wrap it in fur.
The pattern is an upsized version of a dome available from Evil Ted and the foam is 1" high density foam from JoAnn's Fabric - available in 24" x 72" rolls. It was traced onto the foam four times and the parts cut out [Fig.1-2].
Using Barge, the parts were glued up as pairs and then as a full assembly [Fig.3-4]. Preliminary leg holes were cut into what I'm calling the "butt dome" and an EVA foam ring added to force it round [Fig.5-6]. These last two details will change, but it was a start.
Step 3: HD Foam: Chest/Back
The chest/back is comprised of 1" foam and in my case it's 8" width x 58" length [Fig.1-2].
The narrow ends were glued to the front and back of the dome - center seam used for alignment [Fig.3-4].
The location of my sternum was marked on the front and the strips glued together from the dome to that point. I added gaffers tape in an attempt to prevent separation/ripping ... hot glue was added ladder for additional re-enforcement [Fig.5-6].
Step 4: HD Foam: Side Infills
The side infills are also 1" foam and lacking a proven patterning method, I did it haphazardly. EVA strips were used to hold the form in some kind of shape, while HD foam was pinned to the back and bottom reference edges. This allowed me enough access to push out the belly and mark a rough reference line on the inside face with a sharpie [Fig. 1-2].
The shape was fine tuned and a poster board template made to ensure I had symmetrical sides [Fig.3]. The pieces were glued up in three stages - back edge, bottom edge, front edge [Fig.4-6].
Step 5: HD Foam: Belly Shape & Darts
I now had a working torso, but the overall shape needed some finesse.
The EVA ring wasn't rigid enough, so I swapped it for 1/4" PEX. The seam/join is re-enforced with a scrap of threaded rod on the inside, which is locked in place with hot glue [Fig.1].
The center of the belly had an odd flat spot where the strips met the dome - a combination of the geometry and all the converging seams. My solution was to cut a disc out of some scrap foam and then a smaller diameter circle out of the belly [Fig.2]. Once glued in place, it naturally created a dome [Fig.3].
The chest was too blocky, so I added some darts in order to round out the shape and pull it in closer towards the arms [Fig.4-6].
Step 6: HD Foam: Arms
For the extremities, I switched to 1/2" HD foam because I wanted more flexibility/movement. Each 24"x72" roll is enough material for an arm, a leg, a foot topper, and half of the head if you lay it out economically.
For the arm shape, I enlarged an older pattern from my Oscar the Grouch costume.
Note: If you have the storage space, I highly recommend saving patterns because I find myself going back to them now and again.
The pattern was traced onto the foam, cut out and then test fit to the body with straight pins, so that I could mark necessary material removal. It was then glued in place with Barge starting at the top center and working my way towards the edges.
Instead of rolling/gluing the entire arm into a tube, I left the arm pit open on the bottom. I found that this not only made the foam suit easier to put on and take off, but also increased the range of motion.
Step 7: HD Foam: Legs
The legs are a simple tube - 24" length x 27" circumference in my case. One end of each tube was rolled down and back on itself in order to make a sort of flange - hot glue to lock it all in place [Fig.1-3]. The leg holes were then enlarged to accommodate the actual tube size [Fig.4].
Initially, I was going to use this flange as a larger gluing surface against the butt dome, but a test fit changed my mind. Having the legs permanently attached made the costume too difficult to climb into and pull up onto my body. The alternative was to keep them detached, which would resolve that issue and also be a storage benefit.
The test fit also proved that a 2 layer HD flange wasn't enough to keep it from falling/popping out of the leg hole. The solution was to add an additional EVA foam ring - also adhered with hot glue [Fig.5-6].
Step 8: HD Foam: Feet
The foam foot topper was another design on the fly/no plan operation. A rectangle of 1/2" foam wide enough for the EVA foam foot and let it run long. The edge was then fused to the EVA with hot glue - starting with the front edge and working my way down both sides towards the back [Fig.1-3].
The centered slice was made to elevate tension in the foam, so that it could form to the contours, but it's also necessary for access to the clasps [Fig.4].
Excess foam was removed from the back edges as necessary and the seam closed with Barge [Fig.5-6].
Step 9: HD Foam: Head Shape
The head pattern is the same one I used for Oscar and it was created by Mike Moore of puppetbuilding.com [no longer an active domain]. I enlarged it using Excel and if you'd like granular details on that process, please reference my Oscar the Grouch Instructable.
350% enlargement for the 1/2" foam template
380% enlargement for the fur template
Note: I'd upload the Excel file, but it's not a supported file type on this site.
The template is traced twice (one for each hemisphere), cut out, and glued using Barge. I glued the darts on each half first ... then joined them to form the head. Just be mindful of the neck and mouth edges, so that you don't glue those by accident.
I'd added a picture of the full foam suit for fun.
Note: I added length to the neck because of how the head will sit on my head [Fig.2].
Note 2: The head foam is a different color because it's from older stock. Not sure if it was always green instead of teal or if that happened from oxidation and being stored in the attic.
Step 10: Head: Jaw
The 1/2" foam head is malleable and easily conforms to simple framework, so whereas Oscar has a pretty round head, Cookie's needs to have a "flattened" look. I achieved this with two PEX rings.
The PEX was cut to a length of 35 1/2", bent into a ring, and the seam/join re-enforced with threaded rod and hot glue.
One ring was inserted into the head through the mouth, foam rolled around to form a lip, and a glued in place. I start with a central tack and the two the edges before I start bisecting and filling in until the entire opening is glued - similar to tack welding.
Once complete I repeated the process with the second ring and remaining lip.
Note: I removed some foam before rolling the top lip because I wanted a wider open mouth.
I was pleasantly surprised to find that the two rings naturally rested against each other and actually formed a natural spring effect. I could pull the top lip down and it would spring back to the "closed" position. Since I liked this happy accident, I only attached the top ring to the back of head at one central point. The bottom ring just freely floats.
Note: A smaller diameter PEX ring will result in a rounder head.
Step 11: Head: Eyes
A key feature ... if not THE key feature of Cooking Monster, is his goggly eyes. The original/existing design is simple and effective, so I just scaled it up.
The eyeballs are 5.6" Styrofoam balls from Micheal's. A few minutes of hand sanding to remove ridges from the injection molding process was the only required labor.
The pupils are 1 1/4" diameter discs cut from 3/16" thick acrylic. I traced a washer, cut close to the line using the bandsaw, and sanded to the line using the disc sander [Fig.1-4].
The central point on a line 1/4" in from the disc's edge was marked and then drilled using the drill press. Hole size isn't imperative ... it just needs to be larger then the nail being used [Fig.5].
Discs and nail heads were spray painted black [Fig.6].
Installation is as easy as threading the nail through the hole and pushing it into the center of the Styrofoam ball. I used the manufacturing injection point because it's there and I didn't have to overthink the placement.
Note: Don't drive the nail home tight or the pupils won't "google."
Note 2: Add some hot glue in the nail hole to hold it in place. Mine did back/fall out during fabrication, so I learned the lesson.
Step 12: Head: Eye Connection
Eye location can and will ruin a costume. Too low or high and/or too close or far apart just has a way of looking "off." After much deliberation, I decided on a 4" spacing a tad forward of the top central point. Left to right plane was marked with a line and the screw locations marked 2" to the left and right of the front to back glue seam [Fig.1]. Holes were punched in the HD foam with an awl.
To keep the eyes from drooping and/or tearing out of the 1/2" foam, I made a mounting plate. It's a 4"x8" rectangle of EVA foam floor mat. Center lines and screw locations were marked and then drilled using the drill press. To keep the screws from chewing up the foam and/or rocking, I used sprinkler tubing as bushings [Fig.2-3].
Screw + washer feed through the EVA + bushing, through the hole in the HD foam, and screwed into the Styrofoam ball [Fig.4-6] .
Note: I used the molding ridge as a screw location since it's 90° from the injection port/eye nail location.
Note 2: I drilled a pilot hole and threaded the holes prior to assembly.
Step 13: Head: Palate
Cookie's head needs to sit higher up on mine to accommodate visibility through the mouth. A simple spacer block wouldn't work because gravity would result in a round head and also make it too tipsy based on the balance point. My first idea became the solution which rarely happens, but I like it.
An 11" EVA foam disc with a 7" central disc removed - resulting in a 2" wide, 11" diameter ring [Fig.1-2]. This by itself worked, but was uncomfortable. The improvement was a lamination of 1/2" HD foam - adhered with Barge [Fig.3-4].
This "palate" feeds through the mouth and with a bit of persuasion, press fits above the top lip. It sits high on the head, is nicely padded, and even covers up the eyeball mounting plate for a finished look.
Step 14: Head: Mouth Mesh
In my opinion, the best material for one way visibility as it relates to costuming is 4 way stretch mesh. It's available in multiple colors so if you need something other than black, it might be a viable option. Fiberglass screen works as well, but it's not flexible enough for compound curves.
Two layers of black mesh (folded back on itself) were tacked with hot glue on the inside of the head behind the lips. The edges were then wrapped around the lip to the outside of the mask and further tacked. The fur will hide the edge and give a clean look.
Step 15: Fur: Pattern Draping
My second trial by fire with the project ... foam fat suit being the first ... was creating patterns for the fur to fit onto the foam body. I reckon even a novice seamstress would be able to drape this form in a snap, but it took me the better part of two days. Tons of overthinking, redoing, frustration, etc. In the end, I just pinned a sheet onto the form and started cutting little by little to sneak up on my desired shapes [Fig.2-4].
That method worked well enough for the body front, body back, and arms. However, the butt dome was an additional struggle. I tried to pin, drape, and add darts, but just couldn't wrap my head around it. I ended up just overlapping scraps of sheet around one side/hemisphere of the dome and sticking it together with hot glue. In effect I used a paper mache method or a simile to the foamsmithing duct tape technique.
I took the best half of this abomination and flattened it with the help of an iron and a dart [Fig.6-7]. Frankensheet was then traced onto paper, which in turn become a pattern for 1/4 of the butt dome.
I'm sure a skilled seamstress could also make a full or half pattern with darts, but my brain doesn't see it ... at least not yet. Due to fur direction, a full pattern wouldn't actually be beneficial, but a half pattern would've eliminated the seam in the front of the costume.
Note: Reusing the initial dome templates wasn't an option because the foam stretch and/or compressed as it was formed into the torso.
Note 2: I purposely located the dart within the leg knowing that are would be removed later on, so the seam wouldn't be an issue.
Note 3: Poster board for templates is my preference because the large rolls of paper continuously roll up (it's in the name after all). Store were closed at this point and I didn't want to spend more time and money to get poster board anyway.
Note 4: I was told 5/8" is a standard seam allowance. I bumped it up to 7/8" to ensure the fur would fit over the foam suit. Better a tad loose than failure point tight.
Step 16: Fur: Patterns & Cutting
A Tale of an Aspiring Seamstress
As previously mentioned, my sewing skills up until this point have left a lot to be desired.
My attempt to sew felt components for my Animal costume in 2013 was a complete failure. Major tracking issues, bird nests (tension), jams (bobbin threading mishap), and then I broke every needle I had. I waved the white flag and surrendered to hot glue.
My second run was sewing faux fur Oscar the Grouch in 2015. I worked through jam and tension issues, broke 2 needles but had extra, and did better with tracking. If you turn the costume inside out for inspection, you'll definitely see wandering stitches, but the seams are still holding strong.
Third run was Marvin the Martians hands. The sewing looks fine, but the hands overall could use more puff.
This year I dedicated an entire day to practice on scrap faux fur. Tested different stitch types and lengths, dialed in the tension, and worked on overall technique - feed speed, tracking, back stitching, turning, rotating with a stopped needle in the down position, etc. I even purchased a 15 pack needles in three different sizes - only broke one all season and it was during the practice day.
This Year in Fur
With the material fur side down, I placed EVA foam mats underneath, so that I could pin the patterns through the fur and into the dense foam to keep them from moving. I added plywood offcuts for additional weight to keep the paper flat. The patterns were then traced with a sharpie.
Note: Faux fur has a direction, so be mindful when laying out and orienting patterns.
Note 2: If you need symmetrical parts, remember to flip your pattern. Examples: sides of the head, front and back of hands, left and right side back panels.
When it comes time to cut out the shapes, I find a sharp razor knife and light touch to be the best implement. Too much pressure and you'll start cutting through fur. Another technique is to run scissors through the fur and tightly against the backing material, but I personally don't get great results and end up cutting fur.
Sewing Machine Settings
Machine: Singer HD 105 C
Stitch: Straight
Stitch Length: Setting D on a scale of A-E
Tension: 5 on a scale of 9
Step 17: Fur: Legs
When it came time to sew, I started with the simple pieces and worked my way up in complexity. For sewing education, I'm not your Huckleberry, but I will share the techniques which work for me.
Fur Tucking: Push as much fur away from the seam to be sewn as possible. This will make the stitch easier to run and it'll look better because you'll be able to brush the fur out to hide the stitching.
Pinning: A combination of binder clips and straight pins to hold the seam where you want it. I'm not shy with them - the more the better IMO.
Stitching: I generally start about 1 1/2" in from the edge [Fig.1]. Manually lower the needle into the fur, lower the foot, run a back stitch to the edge, run the full stitch forwards, and end with another back stitch.
Speed: I run the machine slow because I'm a novice and find it gives me more control.
The fur tubes were slid onto the foam tubes up to the EVA flanges and adhered around the top edge with hot glue [Fig.3].
The length of the fur runs longer than the foam [8" longer], so that it can overlap the top of the shoes. I left it long so that I could have some adjustability. That adjustability comes in the form of Velco. A 1"x4" strip up inside the leg and a 1"x1" square along the cuff edge. This was done at four equidistant points around the circumference of the leg [Fig.5].
Note: The adhesive backing of the Velco wasn't strong enough, so I added hot glue.
Step 18: Fur: Arms
Arms are just like the legs - one long stitch [Fig.1]. They also run longer than the foam by 5-6".
During a test fit of the foam suit, I determined the foam arms were too long and impeding wrist movement. The surplus was marked and removed with a straight edge and razor knife [Fig.2].
The excess fur length is rolled around cuff and up into the arm [Fig.3-4]. This hides the foam, but also provides some adjustability.
Step 19: Fur: Hands
Hands are a bit time consuming and finicky because of their size - especially trying to tuck all of the fur back into each finger.
My working method is to start pinning at the fingertip and then work towards the palm alternating sides of the finger with each pin. If you try running down just one side all the fur tends to pop out of the other ... like when you bit into a pizza roll and all the filling just ejects via the opposite end.
When it came to stitching, I was able to make the turns around the fingertips, but when I made it to the palm, I would stop for a reset. I'd run the needle to the central point between two fingers, stop with the needle down, lift the foot, rotate the piece, lower the foot, and pick back up with the stitching.
Note: As you can see, the 7/8" seam allowance has to be abandoned for the hands/gloves. I'm probably at around 3/8"[Fig.4].
For a clean edge at the cuff, I use what I call a "hot glue hem." Short line of glue, roll the backing fabric onto itself, hold it in place while trying not to get burned [Fig.5]. Faux fur doesn't run or fray per-say, but the edge isn't finished and hair will pull out.
Note: Be mindful of hot glue strings because if that gets into the fur, it could be a mess.
Step 20: Fur: Head
The head seems daunting, but it's not if you take it in sections.
I start with the darts - pin them, start the seam from the outside edge running towards the convergence. At the end I run a short back stitch, but then I also cut some excess thread so that I can tie it off by hand [Fig.1-2].
Next I pin the two sides together and run the shorter chin seam [Fig.3].
Lastly, I run the long, back seam. The only difference here is that the long stitch will cross over the dart stitches. I'm not sure how a seamstress would do it, but I take it slow so I don't get jammed up and break a needle. In regard to the dart stitch, I just flatten it out the best I can so the end product isn't lumpy.
Note: When I flatten a seam, It's like pressing open a paperback book.
For edge clean up, a hot glue hem was applied to the upper lip, lower lip, and neck hole [Fig.4].
The fur head gets slipped over the foam structure and slid around until properly aligned. Hot glue is used to adhere the fur to the foam lips. The only other place I applied glue was on the back of the head - near the bottom edge and centered [on the foam glue seam][Fig.5].
Note: Be mindful of excess glue so as not to make a mess of the fur and black mesh.
The biggest struggle was reattaching the eyes because it was difficult to hold the the part still while I tried to locate the existing foam hole and the run an awl through it to pierce the fur. Once I pulled that off, I then struggled with holding the head and mounting plate as I tried to thread the screws up through the fur. First they would catch on the backing material ... then fur would start wrapping around the threads and getting jammed up. It was frustrating, but the end result was worth the pain [Fig.6].
Step 21: Fur: Butt Dome
The butt dome is similar to the head as it starts with pinning and sewing the dart within each quadrant [Fig.1-2].
Next the quadrants are sewn into a front and back pair. These are directional so alignment matters - I had them marked from when they were patterned and cut [Fig.3].
Lastly, the front and back pairs are sewn together. It's a single run, but there are three seams over which to cross - I just took it slow and flattened them out [Fig.4].
Step 22: Fur: Zipper & Vest
The last subassembly is the upper body, which I'm calling the vest, and that starts with a zipper.
The zipper is 36" long and the color match is surprisingly perfect, so it basically disappears. While researching how to sew in a zipper, I found a lot of people using basting tape. I didn't/still don't have basting tape, but I do have Killer Red VHB tape and it seems pretty similar to me [Fig.1].
Killer Red was applied to both sides of the zipper tape. If your zipper only has one pull like mind, be sure you have that facing out towards the fur side [Fig.2]. The VHB backing was removed from one side and the zipper and was then pressed onto one of the vest back panels. I chose to align it flush with the top of the neck and let the excess run past the bottom.
Note: I added some pins to the zipper track as well, but apparently failed to get a photo.
Two adjustments were made to the sewing machine for Operation Zipper.
- My machine has three needle positions - left, right, and center. I moved it to whichever side placed the needle in the center of the zipper tape.
- I shortened the stitch length. Maybe not necessary, but I was feeling saucy.
After the first side was stitched [Fig.3], I freed the other side of it's VHB backing, pressed it onto the vest, added a few pins, and ran the stitch [Fig. 4].
Note: The only downside to using the VHB was that some of the adhesive would transfer to the needle and make it a gummy mess. I had to take the needle out of the machine and clean it with Goo Gone after each side was stitched.
With the zipper installed, it was time to join the front and back. Binder clips and pins ... backstitch, run the stitch, backstitch. I did the shorter should/neck seams first and the side seams second, but that was just preference.
Step 23: Fur: Body Assembly
Merging all of the subassemblies was the sewing step I dreaded the most ... so I started with the bit I deemed the hardest - butt dome to vest.
Due to the difficulty of pinning up this specific seam, I felt that trying to run a continuous stitch around the entire body wasn't a necessary labour. Those are for Hercules ... I'm just trying to sew here. I decided to pin up the back first [Fig.1]. The BALES stitch order formula was applied and when I got to the zipper, I got a close as possible, backstitched, reset on the other side of the zipper, and ran a new stitch [Fig.2].
Note: I've seen people sew right over a zipper, but I'm not that confident, so not this time.
Note 2: I started inside of the dome and vest side stitches.
Once the back was done, I pinned up the front and ran it through the machine. The only difference here is that I started on the back side of the converging dome and vest side stitches, so that I could lay them flat and lock everything together. Then at the end of the stitch, I went past the converging stitches [Fig.3].
I took the same half of the ring approach for the arms. It was more manageable than trying to pin the entire thing and roll the entire costume without stabbing myself and/or breaking a needle [Fig.4]. The aspect that always makes me stop and think when connecting arms is the fact that the arm needs to be right side out and inserted into the cavity of an inside out body. It computes better if I think of it as fur to fur [Fig.5].
Step 24: Fur: Toes
The fur journey ends with the feet ... which in this instance starts with furry toes. I never thought I'd says this, but I made a toe template. A cardboard mock up of graduated triangular tootsies if you will. [Fig.1].
This template was pinned to fur, traced, and cut out with a razor knife [Fig.2-3].
Note: Since the toe sizes change, the template has to be flipped so that you get the correlating mirrored image piece.
I did try sewing the parts, but because of the size and tight angles, it was a mess and looked terrible. Hot glue was the winning solution [Fig.4-5].
The row of toes was then hot glued to the front of the EVA foot structure. I opted to align them with the bottom edge Fig.6-7]. In hindsight, I would extend the back/flat edge for more material and align them with the top edge of the EVA ... or possibly centered.
Step 25: Fur: Feet
For the foot fur, I decided to take another shot at draping with sheet scraps. I gotta tell ya ... the second time around was a little smoother and less of a suckfest [Fig.1-2]. After a bunch of chicken scratch and design clean up, I had a working poster board template [Fig.3].
Parts were clipped/pinned, traced, and cut out - remember to flip the pattern for the mirrored side [Fig.4-5]. Sewing machine work included a back seam and a tabbed seam above the toes for each foot [Fig.6].
The fur was slipped over the foot assembly like a boot cover and hot glued to the bottom perimeter of the EVA foam. I started at the back and worked my way forward. Once I got to the front there was extra material, which need to be removed Fig.7-8]. I could've accounted for that on the template, but figured it's be quick and easier to just deal with it on the fly [Fig.9]. Once excised, I finished gluing the side up to where it met the toes. The remaining top/front edge was glued to the exposed EVA foam above the toes [Fig.10-11].
For closing the access flaps on the feet, I used more Velcro. 1"x1" squares at the top edge and then 1"x1/2" pieces at three lower locations [Fig.12-13].
Step 26: Fur: on Body & Leg Holes
Last but not least was getting the fur suit onto the foam body. I struggled at first, but once I got it positioned onto the butt dome, i was able to breathe a sigh of relief [Fig.1]. The arms were a second and third struggle - the key was just going slow and not pulling on the foam so as not the rip it [Fig.2-3].
The most time consuming task turned out to be the leg holes. Once located, I determined that the easiest course of action was not to cut the fur, but actually just use a seam ripper on the dart seams. From there I just slowly rolled the fur around the exposed leg hole foam into the body cavity and adhered it with hot glue. Some areas required trimming of excess fur, while others required some darts to relieve tension. The biggest challenge was that I had to do this from the outside because when I tried from the inside, the foam deformed and tensions/angles changed. It was just a matter of time and patience. Admittedly, the inside is a bit ugly, but very few people will ever actually see it [Fig.4-6].
Step 27: EVA Foam: Cookies
From the beginning design stages, I knew Cookie Monster was going to need prop cookies - made from EVA foam. I also knew I'd have an outdoor display and although that idea hadn't hatched, I figured a giant cookie wouldn't hurt.
The giant cookie is 22.5" in diameter, which is the largest disc I could get out of a single foam mat. It's also a 2 layer lamination for thickness [Fig.1]. A beam compass was used to draw the circles and a razor knife to cut them out. The layers were fused with Barge and I used a wooden skewer as a center alignment pin [Fig.2].
The small cookies are 5" in diameter - single layer. I traced a roll of tape for the circles and cut them out with a razor knife. Edges of all the discs were cleaned up/flushed using the oscillating belt sander. Edges were tapered and texture added with a drum sander on a Dremel [Fig.3].
Random chunks of foam were cut and glued to the top using Barge. These are to simulate chocolate chips [Fig.4-5].
Finishing the cookies was what I'd call quick and dirty. I heat sealed the EVA foam with a heat gun, applied a base coat of putty colored spray paint, followed by a dust coat with white spray paint for highlights [Fig.6-7]. The chocolate chips were painted with brown acrylic, which was applied with a brush [Fig.8].
Step 28: EVA Foam: Oven Front
I finished the costume with several days to spare before Halloween, so it was time to finalize a Trick 'r Treat display. I already had prop cookies and the Warden was going to dress as a baker, so a bakery seemed perfect. Seemed reasonable that a fake bakery needs an EVA foam commercial oven - a double oven with a control panel.
Note: I'll list all the dimensions below so as not to bog down the text.
Each door panel was cut from a single foam mat. A center vertical line was marked, as well as a 2" offset from all four edges [Fig.1]. These lines create two internal boxes which were then cut out with a razor knife.
To create a recessed panel look without actually using multiple layers, I turned the large panel upside down, used a piece of 1/4" acrylic as a spacer in the cut out area, and reinserted the smaller foam panel [Fig.2]. Hot glue is run around the perimeter to lock the parts in place [Fig.3-4].
Note: I should've made my layout lines on the back of the panel so they wouldn't have been visible in the final product. That's a lesson I guess I need to learn a few times.
The control panel used the same techniques as the door - just on a smaller scale. For control knobs, I made 2" discs. Traced using a section of PVC pipe, cut out using a razor knife, and rounded using the disc sander and OSB [Fig.5-8]. The knobs were attached to the control panel using Barge [Fig.9].
The door handle brackets are two layers of foam laminated with Barge. Edges flushed and sized using the OSB, then a 5/8" centered hole drilled 1layer deep [Fig.10-12].
The door handles are 1/2" Pex, which are hot glued into the bracket holes once everything is painted [Fig.13-14].
Finishing was not as quick as the cookies, but still as dirty. Gray primer on all of the parts [Fig.15], followed by a black base coat [Fig.16]. Recessed panel and knobs were masked off with paper and tape [Fig.17] and multiple passes of metallic spray paint applied [Fig.18]. If you get greedy and go to heavy with metallic spray paint, it gets blotchy - sometimes the can actually starts sputtering and/or leaking. It's best to go with several light passes and save yourself the frustration. Masking was removed and I stepped back to admire the results [Fig.19]
Part Dimensions
Door Panels: 20" H x 22" W
Door Recesses: 16" H x 7" W [2" trim offset]
Door Handle Brackets [2 layers]: 1 3/4" D x 1 5/8" W
Door Handles: 1/2" Pex x 18" L
Control Panel: 5" H x 22" W
Control Panel Recess: 2 3/4" H x 6 1/2" W
Control Panel Knobs: 2" Discs
Step 29: Backdrop
This year's display/stage/diorama is by far the largest and best looking of my "career." Cookie Monster looked too cool to just stand in a driveway or atop the retaining wall with a few LED up-lights, so I casually spent the part of two days on this presentation.
Day 1 - Monday, October 30th
It rained all day and night, so I worked on the platform/stage in my workshop. Lowes is a stone throw from my house, so I sourced three pallets. One was cannabalized for planks - reciprocating saw down the sides, pry bar for the middle, hammer/punch/cats claw to remove all nails [Fig.1]. The planks were then ripped to width on the table saw and used to fill the gaps on the remaining two pallets. A pneumatic brad nailer made quick and easy work of attachment [Fig.2].
Note: I generally wouldn't recommend taking pallets from Lowes since they pay a deposit on them, but I know the manager and also occasionally add pallets to the inventory. Maybe get permission first is all I'm saying ... there are usually cameras on the back of the building.
Day 2 - Tuesday, October 31st
I had all day to build the set, which was a good thing because everyone and their mom stopped by to ask me what I was doing and/or why. The pallets were spliced together with 2x4 scraps and then leveled at the end of the driveway.
A 2x3x8 vertical was then screwed to each corner [Fig.3] and 1x2x8 strapping double as bracing and utility needs.
-Two spanning the back top since it's bearing most of the drop cloth weight - sandwiching the 2x3.
-One spanning the back bottom - used for drop cloth clamping.
-One spanning the back middle - added drop cloth/prop support.
-One spanning the front top - used as a lighting truss.
-One cut in half for the side tops - used for drop cloth clamping and additional lighting truss.
The drop cloth was rolled over the top strapping and secured with spring clamps. Tension was pulled and the bottom secured with additional spring clamps. This provided a surprising amount of rigidity and the drop cloth didn't constantly balloon and wave around in the moderate wind [Fig.4].
The EVA cookie, oven, and Om Nom Nom Nom lettering were attached to the drop cloth with straight pins (quick and easy). Ten LED clamp lights were borrowed from the workshop to light this up like an airport runway - six across the top and two at each bottom corner [Fig.5]. The Sesame Street style sign was a carry over from Oscar in 2015 - it's painted 1/4" plywood [Fig.6].
Note: For those concerned about the electrical situation of a cord reel, extension cord, and four power strips ... relax. This was used for two hours, never left unattended while powered, and I'm a Halloween professional. You probably have sketchier situations in your home ... don't lie to yourself.
Step 30: Halloween Party
The annual Halloween Party was on Oct. 28th, so it was my trial run. It was 79 degrees that day and I wore shorts and a lightweight moisture wicking shirt inside the costume. I lasted 90 mins, didn't wear the head the full time, and came out drenched in sweat.
Step 31: Trick 'R Treat
Trick 'r Treat night was a success. We handed out cookies (of course) and had 61 kids visit. Most were accompanied by adults who loved it just as much. Tons of photos were taken with Cookie Monster in the Om Nom Nom Nom bakery and while the Baker tried to avoid pictures, her presence was repeatedly requested.
We were outside from 5:30pm - 7:30pm and it was 48 degrees. I wore thin thermal pants and a lightweight moisture wicking shirt - didn't start sweating until probably the last 20 minutes.
Step 32: Glamour Shots
Here are some close ups of the costume components. Overall, I'm pleased with the results.
Note: The faux fur is royal blue, but depending on the light source. The Trick r' Treat night photos appear brighter, but I think that's due to the ten clamp lights with 5000K LED bulbs and the light reflecting off of the drop cloth.
Taking into account the time sinks of the foam suit and draping fabric for patterning, as well as taking a day to legitimately learn to use a sewing machine, It's not a stretch to think I have 200 hours into the costume.
The foot design in terms of mobility and clasp access exceeds both my Marvin the Martian and TMNT Mikey costume. The sewing on the fur is an improvement over Oscar. Not being able to suit up alone is a bummer and it gets hot, but mobility is excellent. The internals of the head is a great design, which will stay in my toolkit. And the outside display is by far the best yet ... Jack Sparrows sinking ship would probably be second.
The Warden wants me to take it easy next year. Something that doesn't need a handler is the primary request. Aside from a desire to redo Bender, I don't have any ideas - the list has been completed. We'll see what happens ... I might have a job that keeps me too busy and/or be too dang old to keep up the pace.
Packing/Storage
For those interested in how it packs/stores ... all of the body parts fit inside of the torso. The feet go in first - one sole up and one sole down - offset from each other to nest/flat pack. Hands/gloves and 5" cookies next to them in the belly. Then the leg tubes atop the feet [Fig.13]. Head needs to remain separate, but I'm going to display it in my office, so that' fine by me.
The arms can gently be pushed towards the body and it will fit inside of a large contractor bag. If you wanted to use a box - a wardrobe box might work, or two large moving boxes cobbled together. A plastic tote would also work, but it would be rather large and probably expensive.
Step 33: Video
Here is a short clip from Trick 'r Treat night. In time I might make a short "skit" video like I did with Oscar and Marvin, but maybe not. If I do, I'll come back and embed the link.
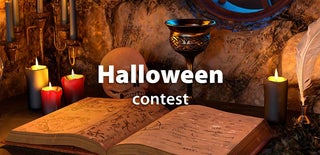
Third Prize in the
Halloween Contest