Introduction: Pocket Watch Display
Recently, I became the steward of an antique pocket watch from 1911. I grew up seeing it atop my Grandfather's desk, under the glass of a display dome. At some point in the early 1990s, my Father became the custodian and it sat atop his desk under the same glass dome. I, nor any other living relative, recall it ever being a functional timepiece.
I know it either belonged to my Great Great Grandfather or his son. I lean towards the elder based on their ages at the time of production, but I have zero evidence - no oral tradition, nor surviving pictures showing the tell tale sign of a watch chain.
Ferdinand Bals [Great Great Grandfather] the guy with the beard
7 October 1856 - 16 February 1937 [Age 55 at time of production]
William Ferdinand Bals [Great Grandfather] 4th son ... maybe the guy in the back row far right?
19 September 1897 – 18 August 1967 [Age 14 at time of production]
It turns out that Clockmakers are a dying breed and the cost of replacement parts, if even available, steadily increase. I was able to find a local jeweler who has a trusted relationship with "a few old timers" in Boston, who also transports items via an insured flesh and blood human courier door to door. The Clockmaker did a full tear down, rust removal, replacement of the broken balance staff, polish, and reassembly. All jewels were intact and I opted to keep the original crystal because though it has some patina, it's scratch and crack free.
Words of wisdom from the Clockmaker and Jeweler: Keep it wound and moving. Don't put it in a drawer to be forgotten and let it seize up with time.
Pocket watch under glass isn't my style. I wanted a simple way to display the watch as a desktop clock, which also made it easy to admire and wind daily.
Technical Specs for Pocket Watch Geeks [Geek being a high compliment]
Movement
Manufacturer: South Bend
Manufacturer Location: South Bend, Indiana
Grade: 215
Model: 2
Estimated Production Year: 1911
Run Quantity: 1000
Grade/Model Run: 9 of 20
Total Production: 20,000
Size: 16s
Jewels: 17j
Case
Manufacturer: Fahys Watch Case Company
Case Grade: Silvaloy - "All Silvaloy Cases Plain Polished"
Material: Nickel Alloy
Introduced: c.1905
Supplies
Spalted Padauk sapwood and Walnut
Renaissance wax
Table saw, drum sander, oscillating belt sander, miter saw, drill press
2" forstner bit, glue, clamps
Step 1: Front Layer
I've had a small piece of spalted padauk sapwood just waiting for the right project and that time has finally arrived.
Based on the overall thickness of the watch, I wanted the front layer to be 1/2" thick. This provides full support of the watch body/case while allowing the crystal to sit proud. The block was ripped and run through the drum sander for quick cleanup.
I used the watch to determine recess placement, marked center with an awl, and drilled the hole using a 2" Forstner bit. Drilled from both sides to avoid blowout and then hand sanded with 150 grit paper.
Step 2: All Layers
My glue up and shaping method is a bit unconventional ... also read as "squirrely". Or maybe you're from Arkansas and do this daily, but I'm just oblivious because I'm originally from Iowa. The verdict is still out.
Anyway ... Midwest calculations said I'd stay golden if I cut the parts to 3 1/4" height. The width is just shy of 3" and I was aiming for a similar depth, but nope - came up short. Have no fear ... accent wood can fix the problem and even look intentional in the end.
I have some scrap padauk, as well as some purpleheart, but Ferd doesn't strike me as a "pop of color" type of fella. He left Germany to come to the US and became a Farmer. I get a feeling walnut would raise his eyebrow with intrigue.
I rolled with the existing 5/16 thickness, cut it close to size, and added it to the pile.
Step 3: Block Glue Up
The angle is arbitrary. It needs to lean back enough for the watch to not fall out, but also not so far back that the face can't be read. Like Grandpa before church, but not Dad on a Saturday halfway through WWE levels of angulation falling towards reclination. Once I was happy, I set a bevel gauge for future reference.
Each layer was slathered with glue, stacked up like miniature books ... then they slipped around as I tried to apply clamps while maintaining some/any alignment. The bevel gauge was used again, but between the glue running down my hands and words flying out of my mouth, I didn't get any pictures.
I decided getting all the glue out of the watch recess was not only smart, but necessary because doing it later would be a nightmare. A plastic scraper removed the bulk of the mess and a small paint brush and water cleaned up all the residue.
As the glue tacked up and the parts weren't sliding around like a toddler on ice skates, I added more clamps.
Step 4: Side and Bottom Faces
Trimming the sides was done using the table saw using a push shoe in my right hand for forward momentum and a push stick in my left hand to apply a bit of pressure towards the fence.
The part was too small for the jointer or drum sander, so I personally deemed this to be the safest method.
For the bottom, I used the orbital belt sander. Miter saw would be another option, but I didn't want to risk tear out along the end grain.
Step 5: Top Face
For the top, I went back to the table saw using a push pad and made the cut in two passes - one from each side to keep the blade as low as possible. Minimal blade marks were removed using the oscillating belt sander.
Step 6: Back Face
To square up the back, I actually did use the miter saw. All of my table saw sleds are 3/4", which would lead to excessive blade height and precarious clamping, so I passed on that. It was a long grain cut, so chances of tear out were minimal.
Step 7: Sanding and Finishing
Finish sanding was done by hand. 150 grit on all faces and for breaking sharp corners, followed by 220 grit.
An oil finish would make the spalting and walnut pop, but I didn't want the yellow hue that sets in over time. I also didn't want a gloss finish. Even a satin water based poly had too much shine.
I opted for renaissance wax because it's a crystal clear with no luster.
Step 8: Glamour Shots
Overall, I'm pleased with the end result. I really like the spalting on the front layer and the walnut layer creates a nice contrasting backdrop when the watch is removed and it's revealed. A different topcoat would add some dimension, but I kind of like how the wood is muted and allows the shine of the watch to be the star. If I had taken a smaller bite on the miter saw, I wouldn't have crossed laminations on the back face, but it's ok. No one other than myself and anyone reading this Instructable is going to notice.
The watch is displayed on a shelf above my desk. Every morning I wind it and enjoy the fact that after five generations and 112 years, it's running once again.
Step 9: 100th Instructable
On an unrelated note, this is my 100th Instructable. Can you believe it? I cannot, but here I am.
I joined the site in November 5th, 2013 so that I could enter my Animal Costume into the annual Halloween contest. The site was a bit different back then - lots of single step Instructables. Dump all your pictures, type up a quick description, and full send. My Buffy The Vampire Slayer Scythe Instructable is still like that actually. Animal didn't place in the contest and I've since rewritten the Instructable with multiple organized steps and far too many details.
Soon after I evolved into multistep Instructables and started interjecting my quirky humor, but wasn't participating in any contests for whatever reason. A nudge from a Community Manager got me to enter my Broken Heart Bandsaw Box into a few active contests ... back then you could enter a single Instructable into up to three contests (it was amazing). I won a First Place slot and as you can see from my profile, I became hooked.
I've see a lot of skilled makers/artists come and go from the site and my own activity has greatly dropped due to all the factors one experiences in life ... adulting, am I right?
Anyway...here is to 100! See ya on the next one.
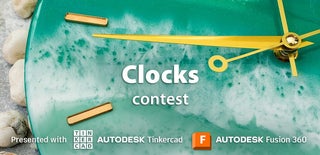
Participated in the
Clocks Contest