Introduction: Creating a Transformer With Tinkercad
Transformers are my favorite toys ever. They bring great memories from my childhood, I love to visit toy stores to check for the last generations of this toy, I have a very small collection and even my first experiment with CAD was designing my own transformable robot using the fantastic 123D Design!
Nevertheless, I'm not a kid anymore, I look like a creepy old guy when I go alone to toy stores (at least in this country), nobody gave a new Transformer for Christmas to expand my collection, and 123D Design is gone forever, dragging my dear first design to the Desert of the Obsolete Nothingness.
The solution? I created my very own new Transformer, using Tinkercad!
This opportunity was not only to test my skills in this design application. It was also to test the limits of my new Biqu Magician 3D Printer. After several printing experiments (resulting in a lot of broken or failed prototypes), finally I got an acceptable result.
This is basically a G1 inspired Decepticon that transforms from robot to a military missile-launching vehicle. This project required a lot of test/improve, because I tried three different design approaches for the articulation of every part:
- First, I tried using the Tinkercad connectors to have joints that can detach when too much pressure is added to a piece, system used in almost all new Transformers. This idea failed because the general design was too big for the printing area, and when I tried reducing the scale, the performance of the connectors was affected, being easily breakable.
- Second, I tried modifying the design to be printed already assembled, so I only had to remove the support materials to have a Transformer ready for action. It worked in theory. However, joints were too loose and easily breakable, causing the car to never keep form and the robot unable to stand by itself.
- Third and last, I tried a "hybrid" approach. Wheels and missile launcher were printed already attached to the robot; feet and thighs can be put together by a printed axle, and shoulders and crotch articulation would use a normal iron bolt and nut to keep them in place with enough friction to keep the robot in the intended position.
This instructable shows how I developed the first and second approaches. If you want to download the Transformer for printing, this is the link.
Step 1: Feet
To save time, I only designed the left half of the Transformer, so later I could duplicate and flip it to have a whole robot.
I started with the foot, because it will be the front of the vehicle. I placed two boxes and a roof, then a spinning wheel and a rotating hub connector, and two MetaFillets for the housing of the wheel. Using two smaller boxes, I created the front and back face of the cabin
Step 2: Arm
My inspiration for this design were the Topshot & Flak action figures from the new "Transformers: Siege" collection, as well as the classic G1 mini figures. In most of them, front wheels are in the feet and back wheels are in the arms of the robot.
To save time, I duplicated the foot and move it back to create the arm. Then I added some extra boxes and details to give it shape and create a fist.
Step 3: Thighs
I used a hole box to create the space in the foot. Then I used another box with a modified radius. Also, I fixed connectors to attach the thigh to the feet and to the body (those connectors would be replaced later by cylindrical holes to fit bolts.)
Step 4: Body
After defining the place for shoulders and crotch connectors, I created the body from boxes, adding aesthetic details.
For the face, I used the Skull from the Printable Kits - Skeleton group of shapes. Later I would modify it.
I made a first "duplicate and flip" test, to check how the Transformer was looking in both modes. I didn't like the result...
Step 5: Reducing Weight
The Transformer was looking too bulky in both modes, resulting in possible difficult to transform, waste of printing time and material, and a shape that looked more like a shoes box.
I erased the duplicated side and worked in cutting wheels, foot and arm in half, using hollow boxes. Also, I added new details to cover the cuts.
Step 6: Second "Duplicate and Flip" Test
After reducing volume from the side, I duplicated all the shape and flip it to check aesthetics. The result was more acceptable (however, this wouldn't be the last time I would remove material from the design.)
Step 7: Logo
I wanted to put a Decepticon logo in my Transformer's chest. I found Tinkercad user Bumblebee1794 created a very cool one! So I downloaded it and I imported it to my design.
Step 8: Missile Launcher
Being honest, first I wanted to create a dump truck, Constructicon style. But I didn't like the way it looked, so I replaced it for a missile launcher, using a box and nine paraboloids. Using tubes and a cylinder as axle, the launcher can rise or go down to its place.
Step 9: First Printing
After finishing my first design, I tried to printed it. The design was too big for the printing platform of my Biqu Magician (remember: it's a low budget printer with a small platform), so I reduced the scale to 48%.
The result? after several attempts playing with scale and settings, hours of printing and wasted material, I only got a bunch of incomplete pieces, broken connectors and a headache.
hen I realized I had two challenges: improving the design and finding the perfect settings to print something of that complexity in my small 3D printer.
Step 10: Enter Second Approach
After the failure with the connectors because they don't work very well on small scales, I tried approach Number 2: printing the model already assembled. I modified the pieces removing the connectors and adding axles, using solid cylinders and hole cylinders. The result was better than the first approach. However, and as I said in the intro, the joints where very loose, making complicate for the transformer to keep the form in any of both modes. On Step 14 you can compare this approach with the final result.
If you want to experiment with this completely-assembled/loose-joints transformer, be my guest!
Step 11: Third Approach and Best Printing Settings
After a lot of trial and mistake, I created a solution were some mobile pieces are already attached to the main parts, like the missile launcher to the body and the wheels to feet and arms; and the other parts are printed independently.
I modified the design and download a SRT file of every piece to print separately. If you have a bigger 3D printer, probably you can print all the pieces at the same time and you can try different printing settings. But I have a small one. After some investigation on internet and a lot of printing mistakes, finally I found the perfect settings to print in Cura for Biqu Magician:
- Scale: 48%
- Retraction distance: 3 mm
- Retraction retract speed: 50 mm/sec
- Prime speed: 25 mm/sec
- Z hop when retracted: enabled
- Max Z speed: 120 mm/s
- Z hop height: 1 mm
- Travel speed: 200 mm/s
- Layer height: 0.15 mm
- Print temp initial layer: 200 degrees (for good bonding)
- Main Printing Temperature: 180 degrees for main print temp
- Overhang: 30 degrees
- Brim: enabled
- Support Pattern: Grid
- All the other settings: default
- Material: PLA
(Thanks to Andrew Mayo from the BIQU Magician - Delta Owner's Group in Facebook for finding out most of the best settings)
Step 12: Printing and Assembling
After more of 14 hours printing, finally I got all the pieces, with great results.
Carefully I removed the support material and filed and cut some parts that had excess of printing material.
The feet were attached to the thighs using two plastic rods that were printed with the rest of the design. Legs ere attached to the body using a nut and a bolt. Each arm was attached using a screw.
Step 13: Decepticon Assembled!
Here you can appreciate the transformer after being assembled. Of course it has room for more improvement. Some of the things that must be corrected in future versions are:
- Rocket launcher becomes a heavy backpack in robot mode, making very hard to keep the robot standing up (center of gravity is too high). It could be replaced by a crane arm, a smaller weapon or removed for good.
- Rocket launcher could launch some spring-powered missiles.
- Robot needs more weapons, or at least one that could be put on the arm.
- In the design I had to cut in half, improve, duplicate and flip too many times, resulting in a printing line in the center of the body. Even after correcting the design, the line still stays in the printing. Now with the experience of this first Transformer made with Tinkercad, next time my design will have less issues.
But still I love this little one!
Step 14: Comparing With Previous Prototypes
In total, I made three working prototypes:
- Blue: scale 50%, fully assembled, printed using a Flashforge Finder 3D Printer. Joints were too loose. The ugly parts are because it got broken in some parts and I tried to correct it using a 3D pen. Bad idea.
- Green: scale 48%, fully assembled, printed using my Biqu Magician 3D Printer. Same problems with the joints of the Blue prototype.
- Green and Black: scale 48%, printed piece by piece using the Biqu Magician ED printer and assembled later. Problem with the joints was solved.
One of the valuable lessons I learned during this process is that when I need to print wheels, it's better if they located parallel to the printing tray (horizontal). In prototypes Blue and Green, the wheels look more like eggs, because the hot printing material was affected by gravity. In the third prototype, wheels are completely circular.
Step 15: Some Paint And... Ready to Go!
Using acrylic paint, I painted the wheels black, windshield blue and missiles red. Also, I painted the metallic screws. I defined the face, using red and green.
And it's over! Building this transformer was a long experience where my patience was tested several times. But I learned a lot about Tinkercad and 3D printing.
But don't get me wrong, my dear family and friends: you can still buy me a new Transformer for my next birthday!
:-)
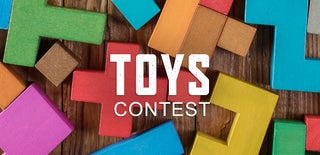
Judges Prize in the
Toys Contest