Introduction: Crusader Cane – Railroad Spike Warhammer…err…Cane
I have known my best friend since we were about 10. That’s a long time since we are now in our mid 40’s.
He is like a brother to me. About a year ago he got in a bad car accident and was burned pretty severely, has some issues with muscle and nerves as well and now he uses a cane to get around better. Currently he has a blackthorn cane which I guess is cool in an Irish shillelagh kind of way but I thought it could be improved upon.
My sons and I were tromping around on a friend’s property one day and found some railroad spikes that were partially buried near a creek (DISCLAIMER: as cool as this project turned out don’t go taking spikes from active tracks - unless you want to meet the wrong end of a railroad man’s club. It is apparently theft)
Anyhow, we found some spikes in a perfectly legal way nowhere near railroad tracks. They were treasured by my sons, for like a day, and then I found one laying in the grass by hitting it with the tractor. At that point they became mine for projects, I knew they had a home…in something.
Moving on about 2 yrs. My buddy needs a cane.
I was looking at pics of medieval weaponry one day – don’t ask why – OK I was making Sauron’s Mace – but I also came across warhammers. They were brutally effective against armored foes by concentrating (as I think Robin Williams may have said about them) PHENOMINAL CRUSHING POWER over an iItty bity surface area.
These man-bashers of old looked vaguely familiar to me. Like a giant nail on a stick. One of each I had.
And thus I justified spending a day in the garage with welder and anvil to recreate an ancient Warhammer…but make it more useful…cause it’s a cane.
Supplies
Railroad spike – sustainably and legally acquired
Sched 40 steel pipe nipple or chunk cut from a 10ft stick
Stick welding rods
Ball peen hammer
Old church pew or other suitable handle material
Cold blue – because I cold blue everything
Copper wire and a piece of pipe – because I’m going for fancy
Snake skin – because I’m going for pimp fancy
8P nails
Epoxy
Step 1: The Business of the Business End
First off grind down or wire brush the spike depending on how rusty it is. This one was not too bad considering where we found it so I just gave it a quick once over.
Now take the steel pipe and cut or file a spike shaped groove across the top. It needs to be as close as you can make it but it does not need to be pretty – cause you’re gonna weld over it.
Make sure the fit is as good and square as you can make it though, welding has a tendency to warp things if there is too much slop. And sometimes even if the fit is tight it still warps if you don’t do it right. Welding machines can be fickle mistresses.
FWIW I decided that the center of balance should be close to the center of the shaft...this was arbitrary having no experience with warhammers or canes, but with the way it turned out, i think it was sound logic. I found the center of balance using a highly calibrated finger scale.
Tack weld it together first on all sides to keep it from moving around. Then clean those tacks up and pound the round pipe flat to the spike all around. Weld each opposite side in turn. Make sure you get good welds from the spike to the pipe. You don't want it flying off when you are...walking around.
Try not to weld your clamps to your project too many times. But it happens, sometimes often.
After welding I ground the welds down smoother and then roughed the whole thing up on the anvil with a ball peen hammer to give it a little “forged in fire” character.
Finally I drilled some holes in the head to really secure it to the haft and cold blued the whole thing 2x’s.
Step 2: Holy Shaft of Supporting +4
I mean, you don’t HAVE to make the Warhammer…ahhh… cane shaft from an old church pew. But if you do it is +4 against the undead.
I lucked into a bunch of cheap ash church pews. (see what I did there) They were like 8-10ft long and solid ash. $10 each. The ends were 1970s ugly though. So they became fodder for my hobbies. So far I have made a 7ftx4ft dining room table, 2 benches, a full bar, a Warhammer shaft, and… a better looking church pew. All in all, I deem it money well spent.
For this project the only problem is the back of the pew is ¾’’ flat ash and I need 1.25’’ round ash.
So I cut down 2 pieces of the right length then glue laminated them together with grain patterns opposite. I think this gives it more strength and makes it less likely to warp.
Then I cut it down to a 1.25’’ x 1.25’’ square.
How do you square a circle? Good question.
There’s a couple ways to do this, I will explain the one I have found the easiest. It is however perhaps not the safest if you are not careful.
I used a table saw set to the diameter of the circle I wanted and turned a square into an octagon by cutting off the 4 corners with the blade at a 45 deg tilt. Then I straighten the blade back to 90 deg and cut more corners and turned the octagon into a hexadecagon. From there I turned the hexadecagon into a icosidodecagon… which at 32 sides…is basically round. Sand paper did the final tuning. You didn’t know you were getting a geometry lesson did you?
Step 3: Why Did I Choose So Much Jaunt?
Because I like a challenge and I thought it would look less utilitarian I decided to cut the pipe for the head off at a jaunty angle vs straight across. This left me with a lot more work to fit the shaft to the head. I would suggest using a paper template to measure the exact angle of the head and then transfer that to the shaft. From there it is just the slow and tedious process of chiseling and sanding until it fits and looks good.
This takes time and hand tools. Go slow. I messed it up once and was really glad the shaft was too long to begin with.
Step 4: Everyone Loves a Sexy Accent
Unfortunately, I don’t have one. At least not for my area.
I can however create a sexy accent on this Warham…ahem. Cane.
I chose copper, both because I like the way it looks and because I have a lot of it laying around. You can keep it shiny and polished but I like to let it tarnish down to the dull brown green. It goes well with wood.
My buddy will likely want it shiny…cause…bling.
I chucked in some leftover copper tracer wire into a drill and spun it down to a cool twist. I then grooved up by the head and down by the bottom with a chisel and epoxied on the accent wires and a copper end cap made from 1’’ copper pipe scrap. Turned out pretty sharp if I do say so meself.
Step 5: Pimps Be Jealous
So… I debated on this for a while.
The…warhamm...*cough*... cane… looked pretty plain even with the copper accent. I mean, I liked it and it looks nice but it was missing some flair that I know my buddy would appreciate. So I rooted around in the garage and I found the perfect addition.
Purchased on a whim (I may have been drinking) about 20yrs ago I have some blood red snake skin. I have been waiting decades for a project that would require such pimpitudonously red snake skin.
I read that plain old wood glue (titebond) is the best way to adhere snakeskin to a bow or similar piece of wood so that’s the route I went. I think thinned epoxy would also be a good choice though.
I made a test patch of the skin glued to a board and coated it in spar urethane
It looked awesome. Like something a slit-pupiled demon or Robert James Ritchie might sport around for a night out on the town. My buddy would love it.
Since I had already finished the shaft before thinking about the final touches I had to go back and scrape off the spar urethane where the skin was going to go. It was at this point that I heard my son say something about piss poor planning, and found out they do actually listen to me.
So I made a blue tape pattern, scraped off the finish where the pattern covered, cut out the snake skin, painted on some titebond II, applied it to the shaft and wrapped the whole thing in clear plastic then electrical tape. I have found electrical tape makes a decent clamp for round objects. If you stretch it tight it has a fair amount of clamping pressure. Since e-tape is black I was really hopeful it would turn out good and nothing had slipped out of place when I wrapped it up... but alas that had to wait until morning.
It turned out great. But it looked unfinished. I added another copper twist under the snakeskin and that really did it I think
Step 6: Finishing the Finish
Final fine sanding, some accent painting around the snake skin, and 4 coats of spar urethane completed the process… Witness the glory.
WITNESS IT!
Step 7: Testing The… Cane.
Admittedly this step is not in the order that it was actually done. I actually did my function test pre-application of the redsnakepimpskin. However I thought it made a good way to end the Instructable.
God forbid I gift something out that is not fully capable of doing its duty properly so I geared up in my Sunday best and gave the big nail a whirl. Nothing but some dust to clean off, handled like a dream.
It should make a good… cane. I think he will like it.
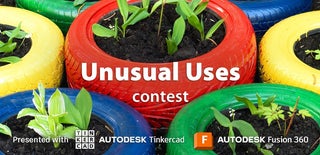
Participated in the
Unusual Uses Contest