Introduction: Custom Disney World Bag Featuring Made With Magic Technology
I haven't been lucky enough to catch a live viewing of the World of Color show, but with an upcoming trip planned to Disney World, I wanted to see what I could do to incorporate the lights and control technology into something other than the Mickey Ears. The ears are really fun looking, but for a few reasons, including wanting to be able to see the effect personally, I looked forward to the challenge of installing the technology in something else that made more sense for me. There are a fair number of limitations to reincorporating the electronics unless you start soldering tiny and delicate parts, which I had no interest in. Working with those limitations (battery placement, limited LED spacing), a few ideas emerged, but finally decided on creating a small shoulder bag where I would incorporate the two sets purchased.
All of the effort was worth it and it was a HUGE hit at the theme parks from guests and cast members alike, so I've gone about making this Instructable for anyone to make their own, or to inspire you to make your own unique Made with Magic item. Here's how I went about making this fun-and a bit silly bag.
Step 1: Disassemble the Magic...
Before embarking on this adventure, I did a web search to see if anyone had taken these hats apart to understand what the components looked like before shelling out $50 for two of them. One such link existed with a thorough tear-down and exploration which proved helpful enough to forge ahead. Here's maker Andy's link:
http://stuffandymakes.com/2012/07/08/disney-glow-...
You can purchase the Made with Magic Mickey Ears at Disneyland and Disney World, or via their park merchandise sales at 877-560-6477, where I purchased two.
The process begins by ripping out the inner foam insert which is glued into place inside the hat which protects the electronics which are connected to an arched plastic band. Carefully pry open the two-piece plastic ears exposing the flexible PCB that runs through the hat and has the lights and other electronics attached. You will need a small screwdriver to complete the removal of the ears, and it's fairly likely that this will destroy the ears in the process, but you're making something at least as cool in their place! Make note of where the wires connecting to the battery compartment are so that you can ensure correct relocation. Using a soldering iron, heat and remove the wire connections from the battery compartment. Using a hacksaw or grinder tool, remove the batttery compartment screw holder and the plastic band on either side of the battery compartment. This will leave you with a simple rectangular battery 3 AAA battery compartment. Repeat for both ears.
Step 2: Transfer the Pattern
You'll need the following materials for the bag in addition to a decent sewing machine.
(less than) 1 yard silver marine grade vinyl upholstery material (ebay or marine upholstery site)
(less than) 1/3 yard black marine grade vinyl upholstery material (ebay or marine upholstery site)
1 yard black vinyl cord piping (ebay or marine upholstery site)
2 heavy duty black zippers 8" and 14" (ebay, amazon or sewing site)
Denim needle for sewing machine, matched silver thread.
I designed this small bag based on other small shoulder bags and inspired by vintage vinyl sport bags from the 80's. I have a bag around this size from Coleman that I always have with me at a theme park, and it's the perfect size for snacks or daily necessities. The bag is 7.5" x 10" x 2.5", and so the pattern I created fits on a standard sheet of paper. Because of this, you can cut the fabric into sheets that fit into your friendly inkjet printer and print the front and back pattern directly to the back side. You could also print and trace the pattern onto the fabric.
The logo is the vintage Disney World logo which is beginning to show up again on park merchandise. (I think they should return to using it full time, as I think it's really the best logo they have for the resort). I found a higher resolution of the logo online and rebuilt a vector image of it using Adobe Illustrator, where the rest of the pattern was designed. Keep in mind this logo is property of the Disney company and can't be used for commercial purposes.
Attachments
Step 3: Cut the Bag Parts
Using a sharp exacto knife, carefully cut out the mickey logo silhouette from the silver and the black vinyl. Also cut around the pattern as necessary to reduce the hem to around 1/2" if required or whatever you are comfortable working with. You'll also want to cut the strip for the bag's side. The bag is 2.5" wide, so I cut a long strip at 3.5" wide to allow a 1/2" working hem on each side. You'll also carefully cut the front piece into two along the front pocket zipper line.
Step 4: Sewing the Bag
You may want to adhere the black logo outline to the silver front panel before proceeding. I carefully applied several coats of spray adhesive to the back of the black vinyl outline then even more carefully placed it. The cutout from the silver is slightly smaller than the black outline to keep the edge cleaner, so keep that in mind while placing it. The vinyl is fairly squishy, so you should be able to make required adjustments. I lifted and stuck the outline layer several times to transfer adhesive and increase the bond until it was very well stuck. I had no problems with it removing itself after 5 long days in the parks, but you may want to do a long-spaced stich around the center of the line to ensure it's stuck for good.
Then position the two sections of the front panel on either side of the 8" zipper. You will also want to align the black vinyl pocket lining with the inside top edge of the zipper, so that you can stitch everything together in one pass. I used masking tape to hold everything together while I stitched and it removed easily afterward. THERE IS NO FOLDED HEM along the zippers as the upholstery vinyl cuts cleanly with no unraveling.
Note: You may think your sewing machine is not capable of stitching through many layers of upholstery vinyl, but I was quite surprised that with the proper needle (denim) and being slow and careful, it had nearly no difficulty. The material squishes and stretches enough to allow many layers pass under the sewing machine foot and the needle to push and pull through nicely.
Having a basic knowledge of sewing or even bag construction will likely help understanding these sewing instructions. My apologies if any part is less than clear. Contact me if you would like clarification of any step.
After the front panel is totally assembled, split about a 12" section of the silver vinyl for the edge in half. You'll want to sew the top zipper into place, though you will only need about 10.5" of it. When it it sewn in, you can cut off the unused end of the zipper.
Create two bag strap loops from the black upholstery vinyl. Mine were about an inch wide to accomodate the Metal D rings I had. I simply folded strips widthwise to reinforce the fabric, folded them in half lengthwise to make a loop and stitched them together.
Then face the zipper panel and the remaining edge panel together along the short edge where the top zipper begins, sandwiching in the bag strap loop and sew them together. Align the top zipper panel up with the front zipper panel and begin to sew that panel to the front as well as sandwiching in the cord piping in along the edge. Keep in mind that you are working inside out and to mind which way the cord piping should be placed. The edge panel should stop around on the other side where the front zipper aligns. sandwich in the other strap loop before connecting the side panel together with the end you began with. You should have the front and the side of the bag completely assembled at this point and it should look like the photograph below.
Be sure the top zipper is open and continuing to work inside out. Sew the back panel onto the back, sandwiching in the cord piping again as you did on the front.
Step 5: Adding the Glowing Logo
http://www.adafruit.com/products/414
You can cut the sheet down or into many shapes as long as the connector is still attached. you could also keep it rectangular, but trimming it just larger than the logo cut-out to preserve battery power. I can further suggest masking out the the unwanted area with anything opaque like electrical tape or a plotter-cut vinyl decal. This will prevent light leaks through the silver vinyl.
There are a variety of inverter and power options available for a panel this size, including those that flash. I tried a few options, but like the solid illumination the best, and that a 12 vlt (8 AA battery) option worked nicely with extra long life.
Masking off the the shape of the logo, I once again used several coats of spray adhesive applied directly to the EL panel. I then carefully slid it it into the front pocket and using the previous adhesion method, secured it to the inside of the front cut-away. I then removed the protective masking on the logo and stuck on the globe decal cut using a vinyl plotter. I then lined the back side of the EL panel with another fitted section of black upholstery vinyl. This was also stuck into place with carefully applied spray adhesive.
Naturally, there are better methods I could have used to affix the EL panel into place and seal the lining in, but those thoughts and ideas didn't surface until after it was too late to utilize them!
Step 6: Adding the Glow With the Show Lights
http://www.actionlighting.com/universal-te40-caboc...
I soldered a few extra inches of wire to extend the electronics to the battery packs which would be positioned at the bottom of the bag.
Using a thin, firm plastic sheet material (I used a pvc sheet called Sintra), I created a single framework running down the interior sides and bottom. This gave me something to more firmly attach the Fun-Light capsules. I determined the placement for the lights on the bag and cut two slits just large enough to slide the flexible PCB through, exposing just the LED, or the LED and IR sensor on the outside of the bag. The Fun-Light fixtures were positioned around the LED's and the locations of the two drilled holes are marked, then drilled. Using bolt with rubber washers, the Fun-Lights are secured into place. The version of the Mickey Ears I am using have a touch sensitive metal post, which I poked through a pin hole and hot glued in place. This became a nearly invisible switch just above the top lights.
Step 7: Finishing Touches
In the process of sorting out the materials for the shoulder strap, a strap from an old computer bag was found to be a perfect fit. Otherwise the nylon webbing and hardware is easy to find on Amazon, Ebay and sewing stores, etc...
Also added to the bag is another piece of the same plastic sheet bent on one end with a pice of velcro. This fit perfectly along the bottom of the bag on top of the battery packs and inverter. If I spent a little more time, I am certain I could have reduced the batteries down to some extent, but it wasn't heavy or cumbersome, and it will all run for at least an evening if not several.
I got to take my boyfriend to Disney World for the first time and this bag added to the many special experiences we had. It was thrilling to see it controlled for the first time with the Wishes fireworks show at the Magic Kingdom. Sadly, I didn't record any footage of the bag during the show. Each individual light operated individually and together with the other three. The programming was really well thought out. It was really cool and so many people were very curious about it or wanted one of their own. I can not wait for the opportunity to see the World of Color show in person at Disneyland in California. The show looks spectacular and it will be fun to see the bag Glow With The Show, as they say.
UPDATE: You can now control the lights to some extent with Disney Parks new "Sorcerer Wand" which has a "paint pallet" mode to change the color patterns on these lights.
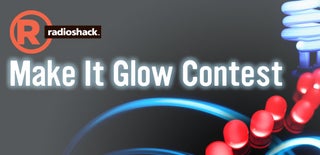
Participated in the
Make It Glow Contest
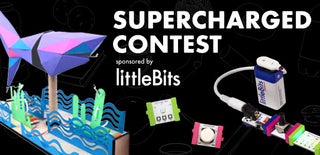
Participated in the
Supercharged Contest