Introduction: Custom Knife Handle
A friend wanted a new knife handle on knife that has been in the family for quite some time. He tried his hand at making one in the past, but did not like the outcome. This is the journey I went on to create something he would be proud to use on a daily basis and want to reach for when preparing the family meals.
Backstory - My friend tried his hand at woodworking over the years and accumulated many good deals on nice equipment. I have been wanting to get into woodworking but have not had a shop in order to start working with the equipment needed. I have done everything from visiting friend's houses, family shops, and even paid for local shop time at a community center in Northern Virginia in order to process wood I need for projects. Well, I recently bought a house with plenty of shop space (my side of a two-car garage) and asked if he wanted to sell any of his equipment. In true friend fashion, he past along the great deals he got along the way and gave me a huge opportunity to buy his tools for a really great price. All he asked was that I make him a cutting board and upgrade his family's knife handle. Now lets get to the knife handle portion of my debt to him.
If you want this or any other service, please visit my Shopify store.
Supplies
Please note there are many substitutes to some of the tools I used during this process. Everything performed in this process can be done with simple hand tools. But here are some lists of the stuff I used.
Tools
- Bandsaw
- Drum sander
- Epoxy (I used this 5 minute option)
- Spring Clamps like this
- Assortment of files
- Assortment of sand paper
- Hand Sander
- Metal cutting hand saw
- Tape measure
- Utility knife
- Drill bit sized for the brass rods
- Drill press
Materials
Step 1: Select Section / Cut / Smooth Out the Stock Material for Knife Handle Blanks
- I started by selecting the most desirable section of the wood he gave me and measured out enough to cut 2 complete book-matched handles in case I messed up the first one.
- I cut enough material to fit the knife handle with a little extra around to cut off the excess during the later shaping process.
- I then ran the blanks through the drum sander to make everything perfectly flat and smooth to a 320 grit.
And just look at that pattern, simply beautiful.
Step 2: Cut Brass Rods and Drill Holes
- I used the metal handsaw to cut a few pieces of brass rod so that there would be extra rod on either side of the wooden blanks to ensure there were no tool marks on the sections touching the wood.
- In my case, I also used a file to create a sharper tip to make it easier to push the pins through the wood, metal, and wood layers.
Step 3: Epoxy Everything Together
- I cleaned everything thoroughly and then mixed up enough 5 minute epoxy to evenly coat one side of the wooden blanks.
- I lined up the pieces, sandwiching the knife handle in place and then pushed the pins into position.
- Clamped the assembly up using a few spring clamps
Step 4: Shape and Sand the Handle
This is the part that takes the most time to complete. There is no right or wrong way to do it either. This is because your personal preference for the person that will be using the knife. It matters how large/small the person's cutting hand is, how the weight is distributed across the knife, how it feels in the hand, if you like sharper/rounder edges, etc. Just take your time with this step and try to do the best job you can. Whatever the process, make sure to examine your work constantly to make sure everything is square and in line with the overall shape you intend to make. I did this:
- Taped up the cutting edge with many, many layers of tape to prevent accidentally cutting myself during the shaping process.
- Used the bandsaw to remove the most material possible without running into the metal. (I may have bumped it once or twice by accident...)
- Used aggressive files to take away the most material possible without touching the metal.
- Used sandpaper and fine files to get right up against the metal without scratching deep grooves in the metal.
- Used sandpaper to slightly add a round-over to remove the sharp edge from the handle
- Once the shape is almost complete, work your way to around a 320 grit all around.
- Water Pop - lightly wet the handle all over and let dry. Once it dries, you will notice the fuzz and particles you did not prior to this step. This is very important.
- Then sand with 320-400 grit all over again. In my case, I used 320 again, did the water pop, and then sanded with 400 grit to get everything very smooth.
Step 5: Apply Finish
- I applied mineral oil with a fine particle paper towel to ensure the wood would soak in as much oil as possible without introducing dust. I did this for around 10 minutes to ensure even distribution of oil that soaked into the wood.
- I applied 2 coats of the Odie's wood butter. Applied 1 coat almost like you would when waxing your car, leaving a layer of butter visible. Leave it alone for around 45 minutes and then wipe/buff off the excess. Repeat the butter step if you need.
Step 6: Admire Your Hard Work
I took a moment to sharpen the knife for him. I wanted to make sure it worked and felt as nice as it looked. So I cut up a shallot that would be later used in a french onion soup my wife and I wanted to eat for dinner.
Just look at the results. The knife looks fantastic and also cuts the onion like the knife is brand new.
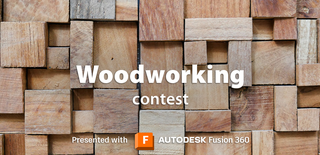
Participated in the
Woodworking Contest