Introduction: Custom (coloured) Plywood + 3D Map
Hi everyone,
and welcome to my second Instructable.
In this instructable I will explain how you can make your very own (coloured) plywood. I'll give you some tips on material, grain direction, glue and clamping options.
As an extra I'll show you how I made a 3D map out of my custom made coloured plywood.
If I missed anyhting or if you have any questions or suggestions feel free to send me an e-mail: info@atelierqube.be or catch me on Instagram https://www.instagram.com/atelier_qube/
You can watch the entire process in this video:
Happy Building!
Supplies
* Veneers of your choice
- You can buy some
- Or make it yourself. If you like to make it I can suggest one of my video's on Youtube:
* Glue
* Salt
* And a press, or something to press your veneers with. (More on that later)
* Extra for the map only: A CNC or a router if you want to make a 3D map out of your custom plywood ;)
Step 1: Veneer, Glue and Salt, Yes Salt!
First things first! Veneers
You're going to need some veneers. These can be as thin or as thick as you wish, but one important first thing to know: The number of layers has to be uneven (3,5,7,9,....) Or it wil cup
You can buy some veneers at a local wood dealer or some vendors even offer it online. (If you want some coloured veneers I can suggest http://Rainbowwood.be but there are some other suppliers depending on where you live.)
Once you have all your veneer, try and shape them to the right format keeping in mind a second important aspect: The grain direction has to change between each layer! Or it wil cup!
Second: Glue
As far as glue goes there are a lot of options.
Normal wood glue, water resistant glue, titebond II or III, epoxy or if you're after the real deal - Urea Formaldehyde Powder. This last one is used in professional plywoods, but it is not needed to get a good result.
I've used pretty much all kinds and to be honest in the end the differences are minimal. Just pay attention to whether it has to be water resistant or not.
Last: Salt, yes salt!
As a tip: use some normal salt between each layer while glueing everything up. It doesn't need a lot, but it will prevent your veneers from slipping around while clamping.
One exception though: don't do it if you want to use the veneers for woodturning afterwards.
Step 2: Clamping and Drying
Clamping
As with glue we have a couple of options.
After glueing everything up you can go with:
!!! Make sure the grain direction changes between each layer !!!
* Vacuum pomp + bag: Put everything in the vacuumbag on a flat and stable board to suck all your veneers to it, to get a nice finish.
* Normal clamps: Put the veneers in between 2 strong, stable and flat panels and clamp everything together as good as possible.
* Jig: as you can see in the second picture or third picture there are some really handy and easy to make jigs for clamping down veneers.
* Bottle jack press: If you can weld or if someone can weld for you, then I can definitely suggest this last method. It's basically a strong frame with 2 torsion boxes where you can put your veneers in between. With the power of 1 or more bottle jacks you can then squeeze everything together for a perfect fit. This is my go-to method when it comes to glueing and clamping. If you want you could make this frame out of wood as well.
Drying
I didn't go over this in my video, but when it comes to drying my biggest suggestion is 'better safe then sorry'.
You're better of letting it sit too long then taking it out of the clamps to fast and having the whole thing bend or cup on you.
How do I calculate?
I go (if I'm using normal wood glue or titebond) with a minimum 1 hour per layer of glue and then add the amount of layers:
So 3 layers: would make 2 layers of glue (2 hours) + 3 layers of veneer (3 hours) = 5 hours minimum
5 layers: 4 layers of glue (4 hours) + 5 layers of veneer ( 5 hours) = 9 hours minimum
Next to that I'm always considering: more glue = more moist = longer clamping.
Epoxy?! Ofcourse this doesn't count for expoxy since this is a chemical reaction. Be sure to read your instructions when you're working with epoxy!
Step 3: Bonus: How to Carve a 3d Map
I'm not going over the entire process of making a topographical map in Fusion 360 or any other 3D software. But I will go into more detail on how I took on the process.
1: Find a map you can use as a template.
2: Make a drawing in your favourite software over the map considering what areas you want to be carving.
For example: I wanted the streets, the fields and the forests, the river and the inhabited areas to be different.
3: Determine what colour you want to give each area.
For example for me it as:
Light green: inhabited areas
Green: Fields, forests and such
Brown: Streets
Blues: The river, pools and everything water related
4: In your 3D software change the depth of each area so it matches your predefined colour.
You can easily measure this once the custom plywood is made.
I knew each layer was 1.5mm so I put the depth of each colour in the middle of that range.
0-1.5mm : depth 0.75mm
1.5-3mm: depth 2.25mm
...
5: Start CNC'ing and let your map come to life!
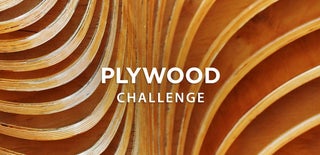
Participated in the
Plywood Challenge