Introduction: Customizable Light Box
With LED being all the rage these days, how cool would it be if you could have your very own lit up art on your bedroom wall? Even BETTER...what if you could easily change that art, especially around the holiday season?! This project didn't start out with that in mind, but while meditating in a hot shower (I am notorious for my long, monk-like meditation showers) I came up with the idea to make my a picturelight box, an illuminated art box. And it's so simple!
This box does require some woodworking skills to build the box, but there's not really a lot to it. If you can make a mitered picture frame with an inset backing, you should have absolutely no problems here. LED light strips are different, yes, but any light strip you find should do the trick. I have done some electrical work on mine, but it's not necessary so long as you don't mind unplugging a wire that hangs out of the box instead of using a hardwired switch.
So...let's make things!
Materials List
- (2) Sheets of ".080" acrylic plastic (UNPEELED!!)
- Spray paint/Other types of paint that will adhere to plastic
- E-Xacto knife or some other type of razor (optional, but helpful)
- (2) 24 3/4" x 3 1/2" x 3/4" piece of wood
- (2) 18 7/8" x 3 1/2" x 3/4" piece of wood
- 24 1/4" x 18 1/8" panel board
- Scrap strips of wood for french cleats
- 18" LED Light strip
- Extension cord (optional)
- On/Off Toggle switch (wired) (optional)
- Mounting cable ties
- (4) #8 x 3/4" Pan Head screws
- (2) #8 x 1/2" bolts (to secure the LED light to the panel backing)
- (3) #10 x 3/4"
Tools I used
- Table saw
- Miter saw
- Router
- Grinder with a metal cutting disk
- Spline Jig
- Drill and Drill press
- Pneumatic stapler
Step 1: Painting Your New Image
Whoa, whoa, whoa!
Before we get started, let's have a little talk. The first thing you'll need to do is figure out how you want your display to work. I listed 2 sheets of acrylic to use, only because I chose to have one float on top of the other. I wanted my first image to pop off the sheet from the second, almost like it's hovering on top, giving it a 3D image. I also wanted the light to only show through the symbol. If you don't want that, you can simplify this project by only using one sheet of acrylic.
Another point I'd like to make here. I've tried to highlight leaving 'the wrappers' on the acrylic sheets. You can use these sheets to your advantage. In the video below, you can see how I cut and spray painted the plastic on the acrylic sheets. By flipping it over, I was able to use 2 different colors of spray paint, one on each side, which really made it easy to create my picture.
Click here for an idea of what I'm talking about.
With that out of the way...with the decision as to how you want to proceed is laid out, find an image you want to cut out and let's move on...
Step 2: Working With the Image We've Selected.
After I found the image on the internet that I was searching for, I used a free, brilliant little program Mathias Wandel put together that will enlarge a picture and allow you to print off that image in sequential order on your printer. After I had printed the pages off, I simple cut away any white edges on the sides of the paper so that I could put the image together and threw some tape on. After the tape was adhered, I cut around the border of the picture and taped that entire picture on the top of my unpeeled acrylic sheet.
It's fast, but this is how I taped my images together, cut and then adhered it to the acrylic sheet.
Step 3: Cutting, Peeling and Painting
Okay, now that we've hunkered down our pattern, I placed my acrylic sheet over a couple 2x4's with an LED light below so that I could see the print through the plastic. Very carefully, I cut parts of the plastic protective film above my pattern with an X-acto knife and a utility knife, peeling away just the protective film. This gave me a protective layer against the spray paint mist that was to come while exposing the parts I wanted painted.
Why not just cut on the print side? I used both sides of the acrylic sheet to do different things. While one side served as the gray paint surrounding the symbol, I flipped it over to the opposite side to cut out the actual symbol. With spray paint, this works really well, so long as you're only using 2 colors. If you're using something different, removing the plastic film and directly tracing or painting would be the smart route.
Once I had a side finished, and spray painted, I waited till it was dry before peeling off the protective layer. I finished the opposite side, allowed that to dry and then peeled that off. I then used a paintbrush and added a touch of glow in the dark paint to cover just the symbol, giving it an eerie glow after the lights went out.
With my second sheet of acrylic, again, optional, I peeled off the protective layer of plastic and spray painted it a solid black color.
Step 4: Second Sheet...Or Optional...
If you want to do what I have done by adding this additional sheet, there's not much to this step. I used a grinder to cut out the shape that would allow the light through. I made sure that the painted side was down when I cut (thereby cutting the clean, unpainted surface) not allowing the cut plastic to dig into the paint. Alternatively, you could use a Dremel (as I did in the 4th picture) to grind out accents or to cut holes smaller holes.
I also painted areas on the backside of the first acrylic sheet that I didn't want light to pass through, further allowing my symbol to have its appealing glow. This is also shown below in the link.
Cutting and Painting Areas I Don't Want The Light to Shine Through
Step 5: Picture Framing
Next I made my frame to fit my sheets of acrylic as well as a backing for the light to sit on. If you've ever made a picture frame, you're good to go. Here I used mitered corners with splines when I made the box because I like the look of a good miter corner and splines make it infinitely stronger. I also wanted the top of the frame to be able to come off and having those splines in place keeps the board from being knocked off the top.
Now, you don't need to use mitered corners. Butting boards right next to each other at the corners and throwing some screws in will work just fine. You do need to run grooves in the wood for the .080 acrylic sheets to slide into. The depth for these cuts I made at about 3/8". The width 3/16" (The way I did that was by using the kerf of my blade (an 1/8") and adding a 1/16" second pass). Between each channel, if you choose to use multiple sheets, I left about an 1/8".
Not something that's absolutely necessary, but I made a small recess on the back of the frame that allowed me to insert a sheet of paneling. If you don't want to recess it, you can always lay it directly on top of the wood frame and glue it down. If you want to be able to remove the sheets of acrylic, remember that the only parts of the frame that will be glued are the sides and the bottom to the back. The top piece must remain glue free.
On each part of the frame I also took about 15 degrees off the front with the table saw, giving the edge of the frame a sloped look. This was purely for cosmetics.
Step 6: Adding the Back and the LED Light
Whether or not you decide to inlay the back panel or to add a switch, this step should be useful. You'll need to either measure the insides of your inlay for the backing or the outside of the box if you plan on gluing it straight to the back. My measurements were 24 1/4" x 18 1/8" for the panel that inlayed in my box. That should be a good approximate to work off of as I had those acrylic sheets in mind...and, well, they fit perfectly in my unit.
Turn your LED light over and look at the keyholes on the underside. I found the dead center and marked a line on my 18" LED bar (which came to 9"), found the dead center and put a mark at the center of width of my 24 1/4" panel (12 1/8") and flipped over the LED strip. I measured from the center mark over to the keyhole on the right side of the LED light, and then the left, and transferred those sizes to the panel, starting from my center line and measuring over on both sides and then drilled holes for bolts to pass through. I placed the head of the bolt in the inside of the box and put a nut on the opposite side at the back of the panel. After I placed the heads of the bolts in the keyholes on the back of the lights, I tightened the nuts until it was secure.
Step 7: OPTIONAL: Notching Out Our Switch
If you choose to add a switch, I'll give you some of the basics to install it. I don't want to get too technical because there are a lot of codes that I could get you in trouble with if you don't do things exactly the right way. This step is easy. We just want to make our switch stick through one of the edges of our box so that we can attach a ring to it. If you don't want to add a switch, run the wire from your LED from the back side of the box to the outlet and unplug it every time you're done looking at your masterpiece.
Step 8: OPTIONAL: Wiring the Switch
This is just going to be a few tips. If you don't know what you're doing, find a youtube video or an electrician to help you out. Wiring a switch is a simple thing, but if you are unsure of your abilities, go the other route and just unplug your LED strip every time you are through. This is a convenience only step.
- Wiring a switch is like wiring a light bulb.
- Your whites (neutrals) are always connected in a wire nut.
- Blacks (hot) are what are connected to the switch. When you hit the switch, you are either interrupting the electricity or connecting it.
- I used a wired switch as it is sealed. The only way you *should* get zapped is if you touch exposed wires which will be hidden in wire nuts.
- After putting wire nuts on, use electrical tape and wrap the wires going into the nut as well as the nut itself. This will prevent wires from moving and becoming disconnected.
After that I used mounting cable ties and tied my wires back before screwing them down to the frame, preventing any movement which could, again, loosen connections in time.
Step 9: Gluing the Back and French Cleats
If you haven't yet glued the back on, go ahead and do that now. Use staples or brad nails to hold it in place while the glue dries. If you don't have staples or brads, use clamps and wait it out. The next thing we need to work on is putting french cleats on the back.
Think of french cleats as triangles that interlock with each other. One triangle section is attached to the wall while the other the back of your wall art. I have made an exclusive instructable video just for this step!
Step 10: Thank You's!
Thank you! If you have any questions or suggestions on ways to make this better, please comment! Follow me here and follow me on youtube!
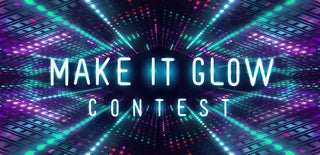
Participated in the
Make it Glow Contest 2018