Introduction: DIY CNC With Simple Tools
10 to 12 years ago I conceived the idea of building my own CNC machines for Foam cutting and routing, and after moving to Europe for a few years, then a career and the lack I space I benched the idea for a while but kept buying parts for the machines. About two years back a friend and myself were chatting and he said he has space by him let's build it. The Foam CNC requirements changed over the years, so the plans changed as well, but the CNC router, was still a go. Bearing in mind I had an idea of what I wanted and there are no plans for the machine changes are inevitable.
The top of the table is 1250mmX650mm projected cutting area is 950 by 500mm.
We started assembling the machine frame this was done by gluing & screwing 22mmX48mm planks to a 22mm Marine Ply Base. Here there are 4 side to close all the side and then three spaced evening in the center so I can add a vacuum to the machine at some point. On top of this is a Replaceable 20mm MDF board. The feet / base legs were made from 22mm Marine ply. All the wood was cut to size by the local timber merchants, so all we had to do was glue everything together. We used Jowat PU adhesives. Once set all sides were trimmed using a flush cut / trimming blade on a handheld router.
Having the table Framed we added the Legs, to make sure both sides are perfect these were clamped together and then drilled the holes for the bearing rod on a drill press. Framed the table and put the Gantry base on. All the alignment is perfect.
Its somewhere at this point where I glued the frame together for the gantry base, so I decided to just fit it upside down.
Step 1: Turning the Lead Nut and Making Anti Backlash Nut
The backlash nuts were turned on a 50 year old Unimat I restored, slow going. Clearly the vintage of the Lathe shows in the pictures, because some of the cuts are not smooth, this is mainly because the lathe is not stiff enough and the motor is not strong enough. I made the Nuts myself because at $20 each it made more sense to buy the tap for $40 and make as many as I wanted. At some point I got a great offer for my unimat, which was complete with all the fitting and I decided to sell it and bought a nice new SEIG C3 mini lathe, definitely not a decision I regret, this made the turning of nuts and anti backlash nuts really easy. the anti Backlash nuts are made from Delrin or and Industrial Nylon, they work a treat. But more on that later. The Brass Nuts were made from 30mm diameter brass and 50mm long, over kill but why not.
Because I used 12mm TR12 3D Acme / Trapezoidal lead screws I imported tap from Marchant Dice in the UK via eBay you should also be able to source it directly from China too, but Kevin has shipped me loads of stuff and I recommend his services and products this is the link to their TRM12x3D Right Hand Tap Acme Leadscrew I left a small piece of brass so I could tighten it in a vice, and Later, I cut this off with a Parting tool.
Step 2: X-Axis
I made a jig to grind down the ends of the lead screws to 8mm which is the meat left just after you remove the thread part of the screw. Both ends are supported by a flange bearing with two grub screws this is then connected with a flexible aluminium coupler to the stepper motor and the compensation "goody". These are long extension nuts or whatever they are called.
At this point I decided to upgrade to the project with "Supported" C-Linear bearings underneath, which was initially only supported only at the ends. When I originally thought about the design I used flange bearings See Image, problem with this approach was that as the X-axis travels through to the center of the machine it starts to sag on the X-axis. Obviously this will happen more if you use a heavier tool or Router. So the idea was to replace the bearing on the bottom with a open bearing and support the entire length of the bearing rod. This was be done by drilling holes in the bearing rod and making a supporting rail for the rod from wood, in which I used Epidermix (industrial grade epoxy) to glue the rails, and used 4 cap screws to make sure it never moves. Simple Solution to suit the current design. In hindsight it was not the best / idea design, but with no real plans it will now work.
The rod is now 100% bolted to the table and supported throughout. is super stiff with no lateral play. All the bearings have now been changed to c-bearing's this has made a huge difference.
I cut holes in the Gantry Base, so I could fit the Any backlash nuts, this proved to be an excellent solution, and really works will.
Step 3: Y-Axis
First I started to build a Bearing block that holds the bearing for the Y & Z axis. I did it this way round because it less complicated and takes up less space, allowing more free movement of that axis. I also decided to make the parts from 12mm Plexiglas. I must say the Perpex (Plexiglas) is very nice for this. I had it on hand and it's really stiff, but surprising more pain in the butt to work with than wood. I used 16mm x 40mm bearing blocks
Once I drilled all the holes that hold the bearing blocks I cut the block to the correct size, once again on the Unimat, i had to make two cuts on top one bottom but ti worked. All Caps screws are stainless steel 4mm.
Step 4: Z-Axis
The Z-axis in once again made from 12mm plexiglas, the two end were clamped together and drilled together on a drill press making then near identical. The Stepper motor is once again fitted with extension nuts, and 5mm stainless steel cap screws. The here anti-backlash nuts are square and made from nylon block, to remove any backlash they a are forced apart and then they are screwed to the plexiglass.
Step 5: The Electronics & Wiring
These are 6 wire Nema 23 300oz steppers in kg's I think that is 20kg holding torque, these were imported from Wantai motor.
The steppers were wired using 7 cored trailer with, I removed one strand, the reason why I used this wire is because it's colour coded and readily available. These were fed through the carrier chain and connect to the board using 6 pin audio plugs
I ordered a 30v 10amp power supply for the controller board, the controller board is a HobbyCNC that I assembled 14 years ago while living abroad. and it works flawlessly,
Step 6: Closing, Costs and Requirements
You should be able to cut pretty much any soft material and non-ferrous metal, with cutter head cooling (via compressed air) and multiple passes. When cutting a Nylon block may melt and clog the cutter if cooling is not applied at all. The stiffer the machine at the end of the day the harder the material you should be able to cut. I would stop at Aluminium though with this one. I have figured it out how to cut at 400mm a minute, with which I am very happy.
Price wise in this build would be a little misleading, because I have purchased many parts over a few years, but I compiled a list of the items. Many are imported and some were bought locally, so the prices exclude shipping.
MDF, Pine and plywood $110
Sundry screws and Adhesives $30
20mm Flange Linear Bearing X 4
12mm Linear Motion Bearing X 8
8mm Metal Pillow Block Bearing with Flange X 3
25mm Bearing CNC Aluminum Rail Linear Motion Shaft Support Series Slide X2
20mm Linear Rail Shaft Support SHF Series X 4
Stepper Motor Flexible Coupler X 3
12mm TR12 by 3D Trapezoidal lead screws Acme 1250mm, 665mm, 350mm was available locally but only to 1000mm, So I imported the longer ones.
12mm Nylon nuts & 12mm flanged Brass Nut X 3 (12x3 Trapezoidal I have the Tap for these so I make them myself)
NEMA 23 Dual Shaft Stepper Motors 270oz - 300oz
HobbyCnc Stepper and Driver board And Power Supply
20mm linear bearing Rod 2500mm
12mm Linear bearing Rod 665mm locally Sourced
I am using Mach3 and LazyCAM for generating the GCode. Key to the speed is also making sure you have all the rapids correct and that each movement makes a cut.not so easily done always but with practice it works. I should try to start learning a new CAM program but as yet I have no clue which one I should try next.
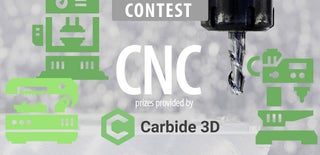
Participated in the
CNC Contest 2016