Introduction: How to Make a DIY Steel Tongue Drum From Scratch
This is an instructable on making a steel tongue drum with your own shapes.
A steel tongue drum, or tank drum is a round steel slit/tongue drum originally fashioned from a propane tank.
I've owned a tank drum for few years. It sounds beautiful & so much fun to play with. The sound of the instrument has a great calming effect. It gives a meditating experience and I love playing it. Few months after getting the drum, I had a chance to take a sheet metal shaping class at my school. I connected the dots and decided to make my own version of the drum!
There are a lot of manual work involved with many different sets of tools. Therefore:
*You will need an access to a metal shop in order to make your own shape for the drum.
Step 1: Steel Sheet Metal
We have to start the project by cutting 2 circles of steel sheet metal.
Steps:
1. Get a 48' X 96' 21 gauge (thickness: 0.0329 inch) standard sheet metal.
2. Cut the sheet metal in half using a sheet metal shear.
3. Use a compass & fine sharpie to draw 2 circles that you are going to cutout. (Mine was 18')
4. Bring the sheet metal to the bandsaw. If the bandsaw table is too small, make sure to have a support underneath the sheet metal in order to make a stable cut.
*Wear a safety eyewear
5. Make the cuts. (Go Slowly)
6. File & Sand (to get rid of sharp edges)
Step 2: Forging
Forging is one of the oldest known metalworking processes. Forging is often classified according to the temperature at which it is performed: cold forging (a type of cold working), warm forging, or hot forging (a type of hot working).
I could've work on it cold, but I decided to work with the latter two, because the material is steel and it is very resistive. In order to save time, to save effort, I worked on it hot using a die. By heating it, you are bringing the metal into a glass state (Glass transition is reversible transition in amorphous materials from a hard and relatively brittle state into a molten or rubber-like state). That way, you are able to shrink the molecules faster and more easily.
Forging changes the grain structure inside the molecules. It is a lot of work, but the act of keep hitting the material, makes the metal resonate more. Because you are compounding & compacting to make the metal more dense. Your objective here is to get out the rough shape.
*DONT BURN YOUR SELF:
Forge can get very hot. (somewhere around 1400 degrees). It gets hot and you sweat but it's part of it.
Prep:
Make sure you wear right safety personal protective equipment:
A. Safety glass or Face shield
B. Gloves
C. Leather Jacket
Steps:
1. Pre-heat the circle in the forge
2. Put the circle of sheet metal in to the forge and heat the middle of the surface.
3. Get the metal into a glass transition point (takes about 5~10 mins).
4. Grab the piece with a long plier (don't get too close, because it will burn your gloves and eventually your hand) Place the piece on a steel die in a shape of a bowl. (which is clamped) and hammer the middle first.
5. As you hammer the steel, change the grip and rotate it so you get even amount of hammering on the surface.
6. Once the steel is red hot, it will be easier to hammer out. But as the steel cools down it will be harder to work with it.
7. Every 5 mins you have to put the steel back into the forge in order to get it hot and continue working on it.
Once you got the rough shape out, It's time to match the top & bottom and smooth out the bumps.
Step 3: Match the Top & Bottom Part #1 (Planishing)
Planishing is a metalworking technique that involves finishing the surface by finely shaping and smoothing sheet metal. This is done by hammering with a planishing panel hammer or slapper file against a shaped surface called a planishing stake that is held in a vice or a mounting hole in a blacksmith's beak anvil, or against hand-held, shaped, metal tools that are known as Dollies or Anvils. The shape of the stake or dolly has to match the desired work piece contour, and so they come in a variety of complex shapes. Alternatively for my project, I planished the metal by the use of an English Wheel. Planishing is a hand-driven process used in auto body repair and sheet metal craft work such as medieval armour production. (Source: Wikipedia)
In short, planishing is smoothing. If forging was to get out the rough shape, planishing is to get little bumps out of the shape.
You are either planishing on concavity against a anvil or planishing on convexity against different kinds of dies.
Steps:
1. Use your eye, and fingers to see where the bumps are on the steel surface.
2. If you want to push a bump inward from outside, place the bowl under a die (underneath the bump) and hammer the spot inward. (control your power)
3 If you want to push out a bump from inside, place the bowl against a anvil and hammer the spot outward.
4. Have the diameter of your drum drawn on somewhere flat. Place the bowl on top of the drawing and see where you are. Decide which parts need to stretch or shrink in order to have both sides match.
5. Repeat the process by keep flipping the bowl back and forth and hammer the surface to get rid of all the bumps & match the diameter.
Steps: (English Wheel)
* DONT GET YOUR FINGER CAUGHT between a lower anvil and an upper wheel. It will crush your finger.
1. Once you got rid of all the bumps, take it to a English Wheel for more smoothing.
2. Place your shape between a lower anvil and an upper wheel.
3. Tighten the space between the anvil and the upper wheel. (Just enough pressure so that you can move around your piece & smooth out the bumps)
4. Push and pull the shape to smooth out all the bumps. It will take at least few hours for each shape.
Step 4: Match the Top & Bottom Part #2
This step is needed before brazing.
Steps:
1. Draw a line with a scribe that is 1/4 inch from the edge.
2. Clamp a flat die. Adjust the height so that the edge of a die goes right below the line.
3. Firmly hold your drum and hit the outer surface over a die to stretch the metal back out.
4. Rotate the bowl and repeat the process until the outer edge is all flat.
5. Place the shape on a anvil and hit the outer edge down with a hammer to make it completely parallel to the surface.
6. Once you got the edges all even in 180 degrees, put the two shapes together to see if they match nicely.
7. Grind, File & Sand the edges.
Step 5: Brazing
Brazing is a metal-joining process whereby a filler metal is heated above melting point and distributed between two or more close-fitting parts by capillary action. The filler metal is brought slightly above its melting (liquidus) temperature while protected by a suitable atmosphere, usually a flux. It then flows over the base metal (known as wetting) and is then cooled to join the workpieces together.
In order to obtain high-quality brazed joints, parts must be closely fitted, and the base metals must be exceptionally clean and free of oxides.
Flux
In the case of brazing operations not contained within an inert or reducing atmosphere environment (i.e. a furnace), flux is required to prevent oxides from forming while the metal is heated. The flux also serves the purpose of cleaning any contamination left on the brazing surfaces.
Different ways to apply the flux:
a. brushing
Brushing is an effective method of applying a thin film of paste to the joint itself and to surrounding component surfaces. Dipping Brazing flux may be applied by dipping one or more components of an assembly into a container of flux. This is most effective with a paste of a thin consistency.
b. hot rodding
This is a technique in which a warm brazing rod is dipped into flux powder and the flux adhering to the rod is transferred to the joint area. This is an effective fluxing method but difficult to achieve good penetration of capillary joints. A refinement on this technique is the use of flux coated brazing rods.
c. dipping
Dipping Brazing flux may be applied by dipping one or more components of an assembly into a container of flux. This is most effective with a paste of a thin consistency.
Steps:
1. Find a middle point of the bottom and drill a 1.5 inch hole. (Place for the heat to leave)
2. Pre-mix the flux
3. Put flux where the two surface meet.
4. Clamp the whole thing in position.
5. One at a time, weld small tacks which is a little spot of brazing. You don't want to put too much heat too soon. Putting too much heat can cause warpage. It can start to come apart.
Weld little tack, go to the coldest, farthest side and tack. Same thing over and over until you get 4 points. Then you tack another 4 points to get 8 points. You do this until you have about 1 inch equal distance part space.
6. Braze weld from a point to the next point.
You go from one tack to the next tack. Go to the opposite side (cold side). Weld from one tack to the next tack. You are always going to stay away from the heat and work on the coldest point you can find and add heat to join the metal. This way, you are not risking the metal to warp.
7. Chip off all the flux.
When the flux cools, it turns into a crystal & ceramic like consistency and you can just chip at it.
8. Grind, File & Sand it. You have to get rid of the flux otherwise the metal will react to it.
Step 6: Tuning Part #1
I have drawn 1:1 ratio diagram of the cuts for you to save and print.
Steps:
1. Draw or print the tongues on a (preferably semi-transparent) A4 paper.
2. Tape the drawing on the drum.
3. Hammer a scribe into each vertex points for indications.
4. Take the drawing off the drum.
5. Using a ruler and a scribe, connect all the dots to get the guidelines.
Make a custom drum holder so that you can clamp the drum down to a table. (for tuning & polishing)
MDF works great.
Steps:
1. Measure the diameter of your drum.
2. Using a bandsaw, cut a rectangular base to the diameter size of your drum.
3. Cut the sides to the height (right below the outer edge) of your drum.
4. Cut 6 triangles for supporting the sides.
5. Use wood glue & clamp all the pieces in place for few hours.
6. Clamp the drum & the holder on a table
Now you are ready to tune!
Step 7: Tuning Part #2
Things you'll need:
A. Dremel
B. Fine file that is thin enough to go into the drum.
C. Earplug (it will get loud)
D. Protective eyewear
E. N95 respirator
F. Digital tuner ( I used an app called Cleartune. It worked perfectly)
Steps:
1. Tape (draft tape works fine) the surface of the drum except the area you are tuning.
You want to tape other areas so that you can only hear a single pitch of a single tongue.
2. Cut a horizontal line.
3. Have your digital tuner ready.
4. Start cutting into the sides in equal distance on both sides.
Set the speed of the dremel in half speed. Hold the dremel firmly but don't put too much pressure into the drum. Let the machine do the work.
5. Once the side cuts are long enough to resonate the tongue, you will be able to hear a certain pitch.
6. Keep hitting the tongue (preferably with a mallet) to see where you are.
The general idea is that the wider and deeper the slits are, lower the pitch is going to be.
7. If you are trying to tune a tongue as a note A3, and your tongue is somewhere around A3#, then MUST USE A THIN FILE to fine tune the tongue down to A.
Dremel is a great tool in the beginning, but once your tongue is closer to a note that you want, you don't want to use it. It cuts too fast and you won't be able to get the tuning right.
8. Move onto the next one.
*This instructable shows a different way of tuning the drum.
Step 8: Trouble Shooting
So..this is my first drum. And yes, I messed up tuning the drum. I made a mistake of tuning
A. without taping the other slits.
B. too fast by only using a dremel. (didn't use a thin file to fine tune)
So my instructor Adam helped me by welding the side cuts of 5 tongues that were out of tune.
As you can see in the picture, the metal got too hot and warped all over the place. The only access into the drum was 1.5 inch hole in the bottom. So we had to make a customize stake with a welded die at the end to planish the face of the drum.
Step 9: Polishing & Finishing
Now it's the time to make your drum shine.
Things you'll need:
A. 6mm angle grinder (w/ range of sandpapers 80 to 220)
B. Earplug
C. Protective eyewear
D. N95 respirator
Steps:
1. Place the drum on the holder you made earlier.
2. Clamp the holder & the drum down to a table.
3. Connect 6mm angle die grinder to an air hose.
4. Attach 80 sandpaper onto the change disc.
5. Start polishing from the darkest spots.
6. Once overall shape is brightening up, change it to a finer sandpaper.
Don't polish too much with a rough sandpaper especially where the tongues are.. because it will thin down the material and It could change the tuning of the drum.
7. Repeat the process until you are done with 220 grit sandpaper.
You can make the drum even shinier by wet sanding it. Here is a great tutorial.
*The drum will not stay shiny.
I used a crystalline wax polish as a finish to keep the metal from rusting.
I highly recommend this product.
A good way to maintain a steel drum is to wipe the drum with a soft rag and a light dab of coconut oil 1-2 times per month.
Coconut oil will help protect your drum from harmful oxidization and allow it to age and change color at a pace that does not effect the sound of the drum.
Step 10: You Have a Beautiful Instrument!
So this drum took many many months to make. It was a long journey but It was definitely worth it. The drum resonates like crazy and it is so much fun to play with!
By the way, I'm Kevin Yong-Moon Lee and I'm a graduating senior majoring in Industrial Design at Pratt Institute. Here is a link to my website for some of you who might want to check out my other design works. I plan to design more of steel tongue drums in the future.
I also have been DJing for the past 7 years and I post my mixes on my soundcloud. I mix all kinds of genres and blend them nicely.. so If you have time, check them out! You can download all of them for free.
On a finishing note, I want to thank my instructor, Adam Apostolos for helping with me throughout the entire process of the project. I hope this proejct & my first instructable can be helpful to you.
Let me know if you guys have any questions about the project. I'll try to answer them with my best knowledge.
Thank you for your time! :)
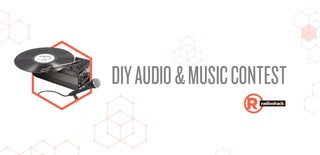
First Prize in the
DIY Audio and Music Contest