Introduction: Floating Pyramid Lamp With 108 Spiritual Symbols
Hello Instructables community! Thank you for checking out my 2nd Instructable. I know what you must be thinking.. 'That's a cool looking lamp!' Yes indeed. Before I go into writing about how to make this lamp, I want to mention that this lamp exists because of my client Barbara Thompson and her vision to create this lamp. These are the written words from Barbara describing how this project all started and describing the meaning of this lamp:
"I dreamed of a lamp. Although the lamp didn't have a shape, I envisioned symbols. My inner voice told me that these symbols would guide to resplendent character, wisdom and purpose. Suddenly, I began to be transfixed by the number 108. Research on this number led me to the 108 Buddhist principles, the adages of character that provide guidance to strengthen against earth's corruptibility and allows cosmic self-realization.
Each step of the way, I was led and synchronicity existed in this journey from start to finish. The lamp kept calling to me to make sure it realized form. I needed someone to engineer my vision. I placed an ad seeking an artist to bring the lamp into form. Kevin answered the ad and his words that he now understood the significance of his grandmother passing the knowledge of bowing 108 times before he entered a Buddhist temple. Kevin turned the vision into reality. The shape of a pyramid came to him and his form represents the struggling human creature seeking to reawaken spiritual knowledge.
The Paradigm Shift lamp is born and its purpose is to be a constant beacon, a faithful reminder of the personal choice to build impeccable character and live it as a shinning example of one person at a time modeling peaceful co-existence where without prejudice everyone is our brother and our sister."
I know..It's deep. Maybe some of you guys are moved. Let's get to it!
There are mainly 4 parts into making this lamp:
1. Engraving 108 symbols into clear acrylic and cutting them into regular triangles
2. Building the triangular-based pyramid top housing.
3. Building the "levitating" base.
4. Soldering and connecting the light source to RGB control panel to power.
Materials needed for..
Part 1:
a. Clear acrylic -1/8 thickness / 32 x 18in.
b. Mirror finish acrylic - 1/8 thickness / 24 x 12in.
c. Acrylic Solvent
d.. Syringe w/ plastic bottle
e. Gila RTK500 Window Film Application Tool Kit
f. Gila LEG361 Heat Control Residential Window Film
Part 2:
a. 3M Clear Tape
b. 80 & 120 grit sand paper
c. 6 x Brass strip 0.16 X 1/4 (0.41mm x 6.35mm)
d. 3 x Brass strip 0.16 X 1/2 (0.41mm x 12.7mm)
e. 80 & 120 grit sand paper
f. Epoxy
Part 3:
a. 12 gauge steel sheet metal (Lower Base)
b. 16 gauge steel sheet metal (Upper Base)
c. 1 inch steel pipe with 1/8 inch wall thickness
d. 1/2 inch architectural bronze angles (x3)
e. 1/4 inch steel scraps (for the false base)
f. Silver solder (for brass)
g. White (flat) spray paint
h. Lacquer spray for Brass
Part 4:
a. RGB Led Strip Light
b. Power Adapter (12V, 2A)
c. RGB Touch Panel Controller
d. Soldering iron
e. Solder
f. Spools of Hook up wires 22Gauge (black, red, color)
g. Helping hands
h. Female DC Power adapter - 2.1mm jack to screw terminal block
Let's dive in!
Step 1: Inspirations (pyramid & Symbols)
Pyramids have been built by civilizations in many parts of the world. For thousands of years, the largest structures on Earth were pyramids—first the Red Pyramid in the Dashur Necropolis and then the Great Pyramid of Khufu, both of Egypt, the latter is the only one of the Seven Wonders of the Ancient World still remaining.
At the spiritual level the pyramid is a symbol for the integration of self-and soul. In dreams the pyramid can stand for the death, but it also contains rebirth.
The base of the pyramid stands for the body, the sides show the spiritual attempts, the point symbolizes the harmonious union of the human with the ‘higher self-‘ (God). The primary purpose of the great pyramids was a place for spiritual initiation. It was in the sacred confines of the great pyramids that initiates would undergo the process of attaining real illumination.
The pyramids were chosen because they are an outer symbolism of man’s inner quest. The spirituality of ancient Egypt was concerned with initiates seeking the Divine within themselves. Unfortunately, over time, the spiritual initiates who guarded the secrets of realization, lost influence and over time, the pyramids became used for different purposes. This is why it is hard to find evidence of these early spiritual practices.
-------------------------------------------------------------------------------------------
A symbol is a person or a concept that represents, stands for or suggests another idea, visual image, belief, action or material entity. Symbols take the form of words, sounds, gestures, ideas or visual images and are used to convey other ideas and beliefs.
Heinrich Zimmer gives a concise overview of the nature, and perennial relevance, of symbols.
"Concepts and words are symbols, just as visions, rituals, and images are; so too are the manners and customs of daily life. Through all of these a transcendent reality is mirrored. They are so many metaphors reflecting and implying something which, though thus variously expressed, is ineffable, though thus rendered multiform, remains inscrutable. Symbols hold the mind to truth but are not themselves the truth, hence it is delusory to borrow them. Each civilisation, every age, must bring forth its own."
In the book Signs and Symbols, it is stated that A symbol is a visual image or sign representing an idea -- a deeper indicator of a universal truth.
Symbols are a means of complex communication that often can have multiple levels of meaning. This separates symbols from signs, as signs have only one meaning.
Human cultures use symbols to express specific ideologies and social structures and to represent aspects of their specific culture. Thus, symbols carry meanings that depend upon one’s cultural background; in other words, the meaning of a symbol is not inherent in the symbol itself but is culturally learned.
Symbols are the basis of all human understanding and serve as vehicles of conception for all human knowledge. Symbols facilitate understanding of the world in which we live, thus serving as the grounds upon which we make judgments. In this way, people use symbols not only to make sense of the world around them, but also to identify and cooperate in society through constitutive rhetoric.
-------------------------------------------------------------------------------------------
*I have attached a PDF file of all 108 symbols and their meanings.
Attachments
Step 2: Part 1. Laser Engraving and Cutting
Laser cutting is a technology that uses a laser to cut materials, and is typically used for industrial manufacturing applications, but is also starting to be used by schools, small businesses, and hobbyists. Laser cutting works by directing the output of a high-power laser most commonly through optics.
*You need to have an access to a laser cutter, and basic knowledge in illustrator in order to finish this part.
I have attached pdf. file of general instruction on how to use Universal Laser System laser cutter & file of 108 spiritual symbols.
Every laser cutter has it's own dedicated software so the laser cutter that you are using might require different settings than what I did. I used Universal Laser Systems for this part.
Other Informative Instructables in Laser Engraving and Cutting that you can reference:
https://www.instructables.com/id/10-Tips-and-Tricks...
https://www.instructables.com/id/How-to-Use-a-Laser...
Materials you need for part 1:
a. Clear acrylic -1/8 thickness / 32 x 18in. ($23)
b. Mirror finish acrylic - 1/8 thickness / 24 x 12in. ($18)
Steps:
A. File Preparation
1. Open the symbol laser cut Adobe Illustrator file I have attached (This file can open from CS5 and up)
2. Double check to see the file is in RGB. And also check to see if all the lines of symbols are in color blue for engraving (0,0,255) and triangle lines are in red for cutting (255,0,0)
3. Clink on "Print" and make sure the orientation of the file is horizontal.
4. The laser cutter file should show up in Universal Laser System software.
B. Laser Cutter Preparation
5. Turn on the laser cutter, air compressor and filter.
6. Open the lid of the laser cutter, and gently place your clear acrylic sheet. Material has to be flat in order to properly focus and cut. Use tape to hold material flat on cutting plane if needed.
7. You MUST FOCUS THE LENS with a z-axis indicator. Focusing the lens is imperative for successful engraving & cutting.
8. Click focus view button, then click on any open area in the bed to place the lens where you can measure the proper distance between the lens and the material.
9. By pressing z-axis indicator (which is up and down arrow) in the laser platform interface panel, bring the bed upto proper level between the lens & clear acrylic sheet.
10. Close the lid and you are ready to go!
* You need laser safety glasses in any situation where it is possible that your eyes could be exposed to direct, reflected, or scattered laser radiation. So protect your eyes by wearing laser safety glasses.
C. Engraving & Cutting
10. Double check your file, and double check your file for engraving & cutting (find out setting) and make sure the air compressor & filter machine are both on.
11. Press "play" icon in the software and run the laser cutter.
12. Make sure to monitor when the laser cutter is operating because It pose a fire hazard. Laser cutters use a high intensity beam of laser light that can produce extremely high temperature as it comes into contact with the materials it is engraving, marking or cutting. NEVER operate the system unattended.
13. Once the job is finished, don't open the lid right away and wait for few minutes for the plastic fumes to ventilate through the filter.
*There are burn marks on the edges of acrylic because I set the cutting speed too slow and the power was too strong. You can prevent this by placing scrap acrylic pieces (same thickness) underneath the main 18 inch x 36 inch acrylic and focus the lens to the raised height. Luckily the burn marks are thin enough that It can be covered by brass strips on top.
Step 3: Part2: Building the Housing (Pyramid)
This is a great forearm exercise! Ideally you should make a custom jig and cut the acrylic in 30 degree angles on a table saw. But since we are only making one pyramid, I decided to manually do this. Plus I really wanted to make my forearm buff.
A miter joint (mitre in British English), sometimes shortened to miter, is a joint made by beveling each of two parts to be joined, usually at a 45° angle, to form a corner, usually a 90° angle. In this case we are making 30 degree angle miter joints.
*Make sure you ventilate your working space well and make sure to wear a N95 Respirator since you don't want to be breathing in plastic particles. Personally I kind of like the smell. But not recommended. Sanding the panels this way is similar to sharpening a knife. It will get SHARP. Wearing gloves is highly recommended.
Materials:
1. Clear Tape
2. 80 & 120 grit sand paper
3. N95 Respirator
4. Good breakfast and much time to kill.
Steps:
1. Tape rougher (80 grit) sand paper to a working table.
2. Place the acrylic panel in an angle and start sanding!!
3. Sand side to side. Sand it up and down. Sand diagonally. Get creative.
4. Once you find that it's close to 30 degrees (on all panels), then replace the sand papers to 120grit.
5. Go slower this time to really fine tune the angles.
6. Occasionally place the panels into a pyramid form to check where you are.
7. Once the edges are looking sexy and you are happy, then you are done!
Step 4: Adding Brass Strips to Add Elegance!
You wouldn't want to have a plastic looking pyramid laying around in your living room with all the rough edges showing would you? Nooo. If it's going to be breathing in your living space, it should look sexy!
Sure, It's extra work but It will be worth your time doing this in the end.
Materials:
1.Brass strip 0.16 X 1/4 (0.41mm x 6.35mm)
2.Brass strip 0.16 X 1/2 (0.41mm x 12.7mm)
You can get these from BlickArt or order directly from K&S Metals (www.ksmetals.com) Item # 8231 & #8235
3. Epoxy
4. 3M clear tape
5. 80 grit sand paper
Tools:
1. Something sharp (to scribe on the strip)
2. Scissor (to cut the brass strip in proper length & angle)
3. Flathead Hammer (to flatten the end of the strip)
Steps:
1. Lay the half an inch strip along the bottom edge of the acrylic panel.
2. Using a sharp tool, gently scribe on the strip to mark where you are going to cut.
3. Use a scissor to cut where you marked.
4. Scissor will cause the end of the strip to curl up. And you don't want that. Use flat head hammer to gently tap on a flat surface to bring the curl down.
5. The end of the strip will be pointy and sharp. Gently sand down the tip. (You don't want to sand down too much)
6. Place the strip back on the edge of the panel. Line it up nicely.
7. Tape right above the brass strip. (This step is to prevent epoxy from going over the brass strip after you apply the glue)
8. Apply epoxy on the underside of the strip.
9. Place it right under the tape (#7) and carefully line up the strip to the panel.
10. Cut longer tapes to hold down the strip (using it as a clamp)
11. Repeat the process 2 more times but repeat with 0.16 X 1/4 inch brass strips for the sides. After that, you are done with one panel. Repeat the process 2 more times and you are done!
12. This is a very important step. You should flip all the panels and sand down the opposite side of where the half inch strip was glued (frost effect). This should be done to prevent LED strip reflecting and exposing individual LED light. (it will make the lamp look cheap) Also by sanding down the opposite side let's you not see the glued side of the strip.
Step 5: Applying Acrylic Solvent
We are going to use acrylic solvent to glue the acrylic panels together. Once the solvent touches plastic, the cement melts plastic and evaporates pretty quickly. While plastic in the state of melting and evaporating, the bonding happens in between the two states.
Materials
1. Acrylic Solvent
2. Syringe w/ plastic bottle
3. Clear Tape
Steps:
1. Tape all the sides as tightly as possible.
2. Put the solvent into the plastic bottle.
3. Tile pyramid housing in an angle.
4. Place the tip of the syringe at the vertex point inside.
5. Only few drops are all you really need for each edge.
6. Tilt base side towards you and let gravity do the work.
7. Within a minute, you should have strong bonds in all edges.
8. Remove all tapes.
Step 6: Adding Reflective Film to the Mirror Finish Acrylic.
This is the false base that will hide the wirings & LED strips. After applying reflective film, the underside (mirror finish acrylic) and top surface (reflective film) will both have reflective elements in the panel. This will give the panel's edges infinity mirror effect once the light source (LED strips) hit the side edges. Also top surface will reflect 108 symbols exactly downward. In short, adding this reflective panel will make the lamp look way more intriguing.
Materials:
1. Gila RTK500 Window Film Application Tool Kit
http://www.amazon.com/Gila-RTK500-Window-Applicati...
2. Gila LEG361 Heat Control Residential Window Film
http://www.amazon.com/Gila-LEG361-Control-Resident...
Steps:
Follow the instruction video I have attached. Follow the same steps except you are applying the film on the mirror finish film.
Step 7: Modeling the Parts in CAD Program (Solidworks)
CAD (computer-aided design) software is used by architects, engineers, drafters, artists, and others to create precision drawings or technical illustrations. CAD software can be used to create two-dimensional (2-D) drawings or three-dimensional (3-D) models.
Softwares specialized in surfaces : Alias and Rhinoceros 3D. I hear more of Rhino in France.These softwares are very good at surface design but not parametric. If you need to iterate a lot on your model it can oblige you to redo several time the same operations. It is very oriented for industrial/product designers.
Parametric modelers like Solidworks(what I used for this instructables), CATIA, CREO, Unigraphic, Autodesk Fusion 360 are used by quite all engineers and also used by many designers.
Simplified 3D modeling like Google sketchup and 3DVIA shape are evolving. It is nice for architecture and quick model research.
I used Solidworks in this case to visualize the model that is to be made, it subassemblies and the constituent parts. CAD software helps designer in synthesizing, analyzing, and documenting the design. All these factors help in drastically improving the productivity of the designer that translates into fast designing, lower designing cost and shorter project completion times.
Step 8:
Step 9: Part 3: Building the Stand (Preparing the Lower & Upper Steel Plates)
The purpose of this stand is to hold the LED strips as well as the pyramid housing. By having two plates and a steel tube in between, the form can achieve levitating effect.
*You will need to have an access to metal shop with proper tools to complete this process.
Materials you will need:
1. 12 gauge steel sheet metal (Lower Base)
2. 16 gauge steel sheet metal (Upper Base)
3. 1 inch steel pipe with 1/8 inch wall thickness
4. 1/2 inch architectural bronze angles (x3)
5. 1/4 inch steel scraps (for the false base)
6. Silver solder (for brass)
7. White (flat) spray paint
8. Lacquer spray for Brass
Steps: (Bottom Plate)
1. Scribe a triangle to the dimension (9 inch regular triangle w/ 7.8 inch height)
2. Scribe a 90 degree angle to have a reference
3. Cut the line with Jigsaw. (make sure the clamps are tight and use plenty of oil)
4. Clean the oil off and grind down edges to keep it flat. (give a minute for the metal to cool down)
5. File the edges ( Watch your fingers! The edge could be very sharp)
6. Mark the hole by using the center line as a guide.
Steps: (Top Plate)
1. Do the same as the bottom plate w/ different dimension (12.25 inch regular triangle w/ 10.61 inch height)
2. Also don't forget that It's a thinner sheet (16 gauge)
3. Use straight edge for jigsaw to follow.
Step 10: Preparing the Steel Tube
The purpose of this steel tube is to give negative space between the lower and upper base to achieve the floating effect of the lamp. The hole in the back of pipe is for getting all the wires out (R,G,B, & 12v power) so that wires won't get in the way plus aesthetically the lamp will look cleaner and more elegant in the end.
Steps (Steel Tube):
1. Make where you are going to cut the pipe to length. (1.9 inch height)
2. Cut with bandsaw (Make sure to use safety glasses for you eyes)
3. Deburr the edges so that wires won't get caught or rip from the edges being to sharp and rough.
4. Mark a straight line to the pipe.
5. Mark the holes where the cutouts are going to be.
6. Use center punch for drill to follow later.
7. Clamp the steel pipe in place underneath a drill press.
8. Drill slowly and drill all the way through. (Add plenty of oil)
9. Let is cool for a minute.
10. Chamfer top & bottom. (For hammering later)
11. Clean the metal with acetate.
Step 11: Welding Everything Together
Steps (putting it together):
1. Hole for the top plate is drilled all the way through.
2. Hole for the bottom plate is drilled half way through.
3. Make sure the angle between the pipe and the plate is square. (90 degrees)
4. Tack weld from bottom (one tack)
5. Filp it over and check to see if it's square again.
6. Do 4 tacks this time. (for it to be very secure and stable)
7. Fill it and grind it.
8. Hammer the top plate so that the steel pipe goes through.
9. Make sure the top pipe is 1/4 inch extruded. (for the false mirror finish acrylic to sit on)
10. Do the same thing to the bottom plate.
11. Make sure both planes are parallel. (1 tack in the bottom -> check the angle -> 4 tacks)
12. Spray with primer then spray with flat white as the final finish.
Step 12: Building the Brass Angles
Purpose of building this brass triangular angles is to protect the acrylic housing as well as to hide the LED strips.
Adding the brass angles looks aesthetically more elegant plus the design language matches the brass strips on the acrylic panels too.
I have attached a video on how to solder brass. It's a very good tutorial so watch it and use it as a reference if needed.
Steps (Making the brass angles):
1. Set up Angle grinder to 30 degrees.
2. Set up piece of angle iron against the bench grinder 30 degrees facing the grit.
3. Take the brass angle and slowly push it in using angle iron as a guide.
4. Check the angle. (30 degrees)
5. Repeat the process 2 more times to end up with 3 identical pieces.
6. Check to see if they are identical by lining them up.
7. Silver solder and propane torch was used to solder the pieces.
8. Clamp the the angles on a table.
9. Apply the flux from the top (inside of a cut) and wait for the flux to crystalize.
10. Apply heat from from the bottom with the propane tank.
11. Add the silver solder
12. Once the triangle is made, sand the outer edges.
13. Use scotch bright (synthetic Steel Wool) to clean up the solder and give the angels matt finish. Sand the surface of the brass in one direction.
14. Apply one coat of Lacquer. Wait 30 mins. Repeat the process 3 more times. Apply total of 4 coats.
Steps (Applying epoxy to the stand & brass angles):
1. Clean the working area of dirt, grease, oil, paint, rust etc.
2. After removing the replaceable cap, squeeze equal amounts of resin and epoxy onto a disposable surface and mix thoroughly.
3. Apply with appropriate tool in an even coat on the top surface of the brass angles.
4. Carefully place the brass angle underneath the top plate of the stand.
5. Use 3 scraps of wood with even heights and clamp the brass angle to the top plate.
6. The epoxy set in 5 minutes. Don't remove the clamp until it fully cures (1 hour)
Step 13: Part 4: Soldering LED Strips
Generally LED strips come in a roll. Which means it only comes in a linear manner. So we have to cut the LED strip in proper lengths to the base and place / solder the strips in a triangular manner.
This is a great Instructable on "How to solder" :https://www.instructables.com/id/How-to-solder
Use it as a reference if you are not too familiar with soldering.
Also you should know the basics on electronics before proceeding this process.
Here are some informative instructables on basic electronics:
https://www.instructables.com/id/Basic-Electronics/
https://www.instructables.com/id/Basic-Electronic-c...
Materials:
1. RGB LED Strip Light
http://www.amazon.com/SUPERNIGHT-Waterproof-300LED...
2. RGB Touch Panel Controller
http://www.amazon.com/Wall-Mounted-Channels-Contro...
3. Soldering Iron
4. Solder
5. Flux
6. Hook up wires 22Gauge
7. Helping hands
Steps:
1. Unwind the LED strip roll, and measure to proper length.
2. Cut where the scissor icon is located.
3. Repeat the process 2 more times, and lay down the strips on the upper base. Make sure the direction of the LED strips are going in the same direction. It's easy to mess this up!
4. Most LED Strips have a weather proof finishing. Therefore, you need to use a exacto knife to cut away the weather proof finishing at the end where you want to solder.
5. Using a wire striper, expose the wires at the end.
6. Cut the wire to about 1inch to 1.5 inch in length.
7. Dip the wires lightly in flux.
8. Using helping hands, hold the LED strip in place.
9. Place your soldering iron to solder. (Just enough so that it will form a tiny ball)
10. Place the exposed wire on top of the copper coated dot. (R,G,B, V+)
11. Carefully apply solder.
12. Repeat the process until all the strips are connected. Red to red. Green to green. Blue to blue. Voltage in to Voltage in.
13. Take all the wires through the pipe we created earlier. (Yessss. Now is time all the hard work that went into creating the pipe pays off).
Now you are ready to hook up the power and test the LED strips.
Step 14: Powering the LED Strips. Almost There!
We came a long way! Congratulations if you made it this far...haha. I know this instructable is a long one. This is the moment when all the hard work pays off.
Materials:
1. 12V 5A Power Supply
2. Female DC Power adapter - 2.1mm jack to screw terminal block
https://www.adafruit.com/products/368
Steps:
1. Connect all the wires to corresponding inputs and outputs in the back of the control panel.
2. Output (B,G,R,V+) <---connected from LED Strip. Input (V+, V-) <----connected from Female DC Power adapter.
3. V+ is power and V- is ground. Screw in red wire for power and black wire for ground to the control panel.
4. Connect the power supply into the Female DC power adapter.
5. Now everything is ready to go.
6. Fire away by clicking the power button of the RGB controller.
7. Word! The LED strip works. Great.
8. Now let's put all the components together.
9. You are done!
Step 15: Clean Up the Wires by Using Shrink Tube!
Materials:
1. White Shrink Tube
http://www.homedepot.com/p/Raychem-1-4-x-3-in-Heat...
2. Masking Tape
Steps:
1. Use a masking tape to mark R,G,B, & V+ in each cable to not get confused later.
2. Push the cables inside of the shrink tube and cut to the appropriate length.
3. You can use a lighter to shrink the tube but It will leave black burn marks. And you don't want that. It's recommended to use a hair drier, which will take much longer but the tube will be very clean.
4. Using an epoxy, place the female power adaptor underneath the LED control panel. Use tape to "clamp" the adaptor in place.
5. Remove the tape and connect red wire V+ (Voltage in) and black wire V- (Ground) from the adaptor to LED control panel.
6. Reconnect R,G,B, & V+ back to the LED control panel.
7. Congrats! you are done!
Step 16: Experimentation With NeoPixel From Adafruit
At first, I used the very basic RGB LED Strip, then decided to see how the lamp will look with NeoPixel RGB LED Strip to see how the lamp and the symbols will illuminate.
It will be helpful to read this guide underneath that was provided by Adafruit and also you need to know some basic knowledge of Arduino.
Neo Pixel Guide: https://learn.adafruit.com/adafruit-neopixel-uberg...
Here is a great introduction to Arduino:
https://learn.sparkfun.com/tutorials/what-is-an-ar...
Materials:
1. Adafruit NeoPixel Digital RGB LEG Strip
https://www.adafruit.com/products/1461
2. Arduino Uno
http://www.amazon.com/Arduino-Board-Module-ATmega3...
3. 5V 2A Power Supply
http://www.amazon.com/Gikfun-100-240V-Converter-Ad...
Steps:
1. Do the exact same steps as Step 12 in my instructable but swap the simple RGB LED strip to NeoPixel RGB LED strip.
2. The wires are going into Arduino Uno instead of RGB control Panel.
3. Connect D in (Date In) to Pin 6.//// V in (Voltage In) and + (Plus sign in the adaptor) and one groud (-) to Arduino and another ground (-) to NeoPixel RGB LED strip.
4. Download and Install Adafruit_NeoPixel Library
https://github.com/adafruit/Adafruit_NeoPixel
5. You must use 5V power supply instead of 12V. If you use 12V, it will fry the strip LED.
6. Upload it in Arduino Uno software and fire it away!
Step 17: Conclusion
I want to mention again that I couldn't have made this product without my client Barbara's vision. I feel grateful to share this Instructable to this amazing community. I tried to be detail oriented and thorough as much as possible but I feel that this Instructable can be way better. I will be keep coming back and I'll keep editing and improving the instructions down the road. I hope this lighting design can inspire people to create incredible objects throughout the world. Thank you for reading this Instructable!
P.S. I'm entering this Instructable to Full Spectrum Laser Contest! If you enjoyed seeing the process of making this lamp, please don't hesitate to vote! Once again, thank you so so much guys!
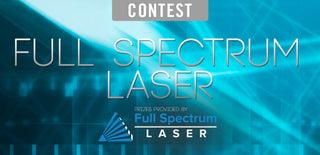
Runner Up in the
Full Spectrum Laser Contest 2016