Introduction: DIY Surfboard From a Hot Tub Cover and Curtains
"Hey Chris, do you want this old hot tub cover, I am just going to throw it out anyways"
Uhh, YES!
Those words started my latest journey in making stuff out of stuff that isn't really meant for making the thing you are trying to make. It's really one of my favorite things to do! Anyway, this time I decided I would try to make a surfboard using the discarded hot tub cover, some old curtains, and some wood glue. I would be using a technique called "poor man's fiberglass" and I had no idea if it was going to work for a surfboard, but hey, there's only one way to find out! Spoiler alert, it actually worked pretty good.....
A lot of what I learned about poor man's fiberglass (PMF) came from this instructable I ran across. It has tons of great information on using PMF, so definitely give it a read!
Step 1: Free the Foam!
The first thing to do is get the foam out from inside the hot tub cover. Usually, there is some sort of zipper to open it up, but if this cover is heading to the garbage, it's probably O.K. to just cut it open:)
From what I have seen, most hot tub covers have a sheet of EPS foam inside them. The denser the foam, the easier to shape, and the stronger the finished surfboard will be. The size of the foam will be the limiting factor on the surfboard's dimensions, so the bigger the hot tub cover, the better!
*As a side note, there are a lot of other potentially useful parts in an old hot tub cover! There's a really long zipper, some plastic sheeting, and some long aluminum "U" shaped pieces to add stiffness to the cover. You never know when one of those things might come in handy!
Step 2: Get Some Other Stuff
Supplies you'll need:
- Discarded hot tub cover- the one I had was about 8 feet long and was nice dense EPS foam.
- Enough fabric to cover the board at least once each for the top and bottom. I used some curtains and some scrap fabric I had around, but I have also heard bedsheets and painter's canvas drop cloths work quite well.
- Titebond 2 wood glue (paid link)- I used a gallon jug and had a little left when I completed the project.
- Some fine wood dust (I collected it from my sander) or some wood flour or 3M glass bubbles or microspheres (paid links) - Used for filling in little holes and general smoothing.
- A strip of thin plywood the length and thickness of the board to use as a stringer. I used 1/4" plywood.
- Polyurethane Glue (paid link) to glue the stringer to the foam. I used Gorilla Glue brand.
- Sandpaper: 80 grit and 150-180 grit
- Surform: (paid link) A tool that kind of looks like a handplane and a cheesgrater's offspring. Used for shaping the foam blank.
- Paint: Make sure it is for exterior application
- Squeegee: Can be a used gift card
- Fin and Fin Box: I 3D printed mine, but easier would be a glue-on fin base with removable fin (paid link)
Optional Supplies
- Epoxy resin: If you use a fin box, it will work best for a strong bond with the foam.
- Leg Rope Plug
- Airbrush or spray paint: Great if you want to add a design to your board.
Please note, some of the above links are affiliate links, and I do get a small commission if you buy through these links. It doesn't cost you any more and it helps me out!
Step 3: Design the Board
Obviously, the length, width, thickness, and rocker of the board are going to be limited by the dimensions of the foam from the hot tub cover. My foam was 8 feet long, so I designed my board 8ft long x 26 3/4" wide and 3" thick. This is much thicker and wider than a normal surfboard, but I gave it these large dimensions for two reasons:
- I was going to be trying to surf on a lake near me, which meant very small mushy waves so I would need as much flotation as I could get.
- The thicker the board is, the stronger it will be, and since I am using materials from the garbage, I figured they would likely not be as strong as traditional materials.
I got lucky because the foam was a bit compressed in the middle yet was thicker at each end, so that allowed me to have a little bit of rocker in my board (rocker is the curvature of the bottom of the board from nose to tail)
I designed the board's outline and profile using the trial version of AkuShaper , which is a digital board designing software. It's not necessary but saved me the time of messing around, drawing out templates by hand. Once the template is designed in AkuShaper it gets printed off on a household printer and all the sheets of paper taped together for the complete template.
Step 4: Cut the Foam in Half
If you tried to make the surfboard using just the solid sheet of foam from the hot tub, it would flex too much and likely snap in half the first time you stood on it. So, to give it more strength, you need to add a "stringer" down the center of the board. This is going to be a piece of 1/4" plywood.
In order to add the stringer, we need to cut the foam down the center in as straight and vertical a line as possible. If I had access to a big table saw or bandsaw, this would have been easy, however, I used a circular saw, which didn't cut deep enough to go all the way through the foam sheet.
After making the cut partway through with the circular saw, I finished it off with a handsaw, trying as best I could to keep the cut straight and vertical. Sadly it wasn't perfect and I spent a lot of time trying to get it smooth and flat with some coarse sandpaper.
** This is probably the most critical step to get right. In hindsight, it would have been worth it to seek out someone who could make a perfectly straight cut all the way through the board. I ended up with a not perfect cut which meant I had some gaps when I glued the halves together.***
Step 5: Cut Out the Stringer
- Take the stringer profile created in AkuShaper and trace it onto a long thin scrap of 1/4 inch plywood.
- Cut out the stringer with a jigsaw or handsaw, cutting as close to the pencil line as possible without actually cutting away the line.
- Check that the stringer fits completely within the bounds of the side of the foam sheet.
Step 6: Glue the Stringer - Part 1
Now it's time to glue the stringer to one of the foam pieces. I recommend Gorilla Glue, which is a polyurethane glue. Polyurethane glues cure when exposed to moisture in the air. They also tend to foam up a bit, but don't let the foamy goodness of the glue fool you- that foam, while it may fill in some cracks, makes a weak joint, so it is important to have tight surface-to-surface contact if you can.
What does this mean for this little project? It means clamps, lots of them. I don't have a lot of giant clamps around my garage, but I do have quite a few tie-down straps, so I used them to loop around the foam and stringer to create pressure. Of course, the foam will get crushed by the straps without protection, which is why I added a strip of wood on the outside edge of the foam and used blocks of wood over the top of the stringer. I also laid a sheet of plastic wrap between the stringer and the wood block to keep the block from accidentally being glued to the stringer.
The reason you can't just use some of your big jug of Titebond II glue to glue the stringer in place is that TBII dries through evaporation, and the foam creates a pretty airtight seal against the stringer so while the exterior bit of glue would dry, any in the center where it isn't exposed to air could take weeks to dry.
**Definitely set up a dry run of your clamping system before gluing, as you will not have a lot of time for messing about before the glue cures.
- Place the stringer on the center edge of the foam sheet, making sure it aligns well and fits on the foam.
- Flip the stringer over and apply a generous amount of polyurethane glue onto the stringer, spreading it out with a piece of scrap wood.
- Depending on the humidity, you likely will want to spray the foam with a little bit of water. If you are somewhere quite dry, this will give the glue the water it needs to cure, however, it will also make it cure faster, so be ready to get clamping quick!I glued my blank on a rainy day, so there was plenty of humidity for the glue to start bonding.
- Flip the stringer over again line it up on the foam. Then put all your clamps on just like you had them on your dry run. Tighten those clamps like crazy.
- Wait until the glue cures (24 hours) and then remove the clamps.
Even with all the tie-downs I had, I still could have used a few more.....
Step 7: Glue the Stringer - Part 2
Gluing the other half of the foam to the stringer is pretty much the same as the first half, lots of glue, lots of clamps...
Because of my not entirely straight cutting of the center line of my foam, I created a little problem for myself: there were a few places with gaps between the stringer and the foam. It is important to fill any gaps otherwise the air from the gaps will expand when out in the sun, creating internal pressure in the surfboard, possibly causing the PMF skin to delaminate. I poured some epoxy resin mixed with glass bubbles to fill in those gaps after I finished shaping the board.
Step 8: Draw and Cut the Outline
- Lay the printed template down on the new surfboard blank and trace around it. Use a marker so the line is very visible.
- Cut out the shape. I used a combination of jigsaw and a hand saw, again, because the jigsaw didn't cut deep enough to get all the way through the foam.
- If you are not confident about getting a nice perpendicular cut, you can cut outside of the template line and then shape it down to the line afterward.
Step 9: Shape the Blank
Surfboard shaping is a pretty in-depth topic to try and cover, and this Instructable is more about using alternative materials than how to shape a surfboard, so I won't go into that here. There is a lot of information just a quick Google away if you need to learn.
Once I had the shape cut out, I used a surform to do most of the major shaping, and a sheet of 80 grit sandpaper wrapped around a short piece of 2x4 to finish up and smooth out the board.
Step 10: Sanding Time
Once shaped, sand the board as smooth as possible with 150 grit sandpaper. It will be impossible to sand out all the little holes made from beads pulling out, but those will get filled in later.
Step 11: Sealing Coat
Here's where the Poor Man's Fibreglass (PMF) comes in. I stumbled on it a couple of years ago while I was making my plywood canoe, and it intrigued me so much, that I kept it in the back of my mind, just waiting for the day I would get to use it. In fact, I first saw it on this foam kayak Instructable here. It's a cheaper, less toxic alternative to the traditional fiberglass materials normally used on surfboards. The main ingredient in this process is Titebond II wood glue. (Not Titebond I or III, as TBI is not waterproof, and TBIII doesn't stick well to itself)
I have only ever seen PMF used on XPS foam, the kind that is usually blue or pink and used in building insulation, whereas I was using EPS foam. EPS foam is a lot more porous than XPS so I decided to give it a quick coat of thinned down TBII to seal those little pores to keep the foam from sucking up too much glue later.
- Mix the TBII with water in a 50/50 mix.
- Paint the mix onto the board with a paintbrush and let it completely dry.
- Once dry, give it a really light sand with some 180 grit sandpaper, just to remove any roughness.
Step 12: Fill a Million Holes
EPS foam is made from a whole bunch of little foam beads all squashed together, so in the shaping process, some of those beads get pulled out, leaving little dimples everywhere. You don't want those little gaps to become air bubbles when the cloth goes on the board so it's time to fill them.
I had some wood sanding dust that I collected from my palm sander that I used to make a filler.
- Mix fine wood dust, 3M bubbles, microspheres, or wood flour with undiluted Titebond II to create a paste with a peanut buttery texture. (I also used 3M bubbles, and they worked even better than my wood dust)
- Use a gift card to spread the paste over the board, filling all those little holes.
- It's important to scrape off any excess that doesn't fill the holes as you go so that there is minimal need for sanding once the paste is dry.
- Fill the holes once, let it dry and then fill them again if they need it.
- Once it is all dry, give the board a light sanding to remove any roughness.
Step 13: Curtain Time
I had an old curtain that was destined for the dumpster that I used for this step. I have also heard of bedsheets and painters canvas drop cloths working well. The thing to think about is, the thicker the material you use, the more glue will be needed to saturate it, and the heavier (and perhaps stronger) it will end up.
- Protect the floor from glue drips with some paper or plastic.
- Set the surfboard top side up on some stands.
- Drape the cloth over the board.
- Cut around the board leaving the cloth hanging a bit past the bottom edge of the board when viewing it from the side.
- Fold one half of the fabric back and pour undiluted TBII glue on the exposed half of the foam blank.
- Spread the glue around with a squeegee or gift card until there is an even layer of glue. Don't spread the glue over the edges or it will start dripping all over the floor.
- Fold the fabric back on top of the glue and use a gift card to squeegee out any wrinkles or bubbles in the fabric.
- Repeat for the other half of the top of the surfboard.
- Trim the overhanging fabric around the edges of the board so that they reach just over halfway down the side of the rail.
- The rails don't have glue on them yet, so now go around lifting up the unglued fabric around the edges and paint glue on the foam with a paintbrush before smoothing the fabric down with a gift card. Sharp corners can be tricky and you may need to cut the fabric to allow it to fold around the corners. For my board, the only place I needed to cut the fabric was at the point of the nose.
I used approximately 1/2 quart of Titebond II to glue the fabric to the top of the board.
Step 14: Second Glue Coat
- Allow the glue adhering the cloth to dry, then spread a second coat of TBII over the fabric with a squeegee or gift card, saturating the fabric completely.
- It makes the next step much easier if you spread the glue just past the cut edge of the fabric so it coats a little bit of the foam. This will harden and protect the foam when you sand the edges.
- Let it dry completely.
I used another 1/2 quart of TBII for this step.
Step 15: Clean Up Edges... Aka Getting a Bit Pedantic....
This step is completely skippable, but I wanted to see if I could make my PMF surfboard actually look kinda good. Although my family has pretty much become accustomed to being seen in public with me and my random projects, I would rather not embarrass them on the beach with a surfboard that looks like it was made out of papier-mache! That means trying to get everything as smooth as possible.
I used a scalpel to carefully trim the edge of the cloth and then sanded that edge to get the transition from cloth to foam as smooth as possible. This wasn't the easiest to do, in fact, it was decidedly un-easy! Though the bottle of TBII says it is sandable, it also seems to stay a little flexible, so sanding is a bit tricksy. I had to sand slowly so as not to heat the TBII and make it go rubbery, all the while watching that I didn't sand into the foam.
Step 16: Cover the Bottom
Now it's time to cover the bottom. That's done exactly the same way the top was covered.
Step 17: Second Coat for the Bottom
Once the glue for the bottom is dried, fill the weave of the fabric the same way you did for the top.
Step 18: Reinforce the Top
Where you stand on the top of a surfboard gets the most abuse, so I figured if one layer of fabric is good, two would be even better. I added a second layer on the top, but only on the back half of the board so as to save as much weight as possible.
Again, the same technique as the other layers.
Step 19: One Last Coat
At this point, all the fabric layers have had 2 coats of TBII glue.
- Spread one last layer of glue over the entire board, one side at a time, and let it dry.
- Once dry, sand the board lightly to remove any roughness.
Step 20: A Little Filler
This step is another one for the pedantic among us and is not necessary for a workable surfboard.
- Mix some 3M glass bubbles or wood dust with TBII to make a paste and use that paste to create smooth transitions between the edges of the fabric layers.
- Apply the paste with a flat stick, let it dry completely, and then sand it smooth.
Step 21: Adding the Finbox (optional)
Next comes the question of the fin. I decided to attach the fin to the board using a fin box, so that I would be able to remove the fin, as well as try different fins.
It was getting very close to the day that my family was planning to go to the lake to try the board out, so I didn't have time to order a fin and fin box and have them delivered. Instead, I quickly 3D printed them.
I used a router to rout out a slot slightly wider than the fin box, using a jig I made from some scrap plywood. My plan was to use a few layers of fabric and TBII to line the inside of the slot and then glue in the fin box, however, once the slot (which included a big chunk of the stringer) was routed out, I could tell that the structure of the board was weakened considerably. I decided that I would need to use some epoxy mixed with fibers to glue in the box because that would cure to an incredibly strong piece, reinforcing the board in the process.
It made me sad to have to do this because my original plan was to use all materials that are readily available, however, I also didn't want to have wasted all my time and have a board that snapped right away.....
If you don't have a 3D printer, and don't have access to some epoxy, and don't want to cut into the PMF you just lovingly created, I think probably a better option would be to use a glue-on fin base with a removable fin, kinda like one of these here (Paid Amazon Link)
Step 22: ...and Leash Plug (also Optional)
The leash plug was also something I 3D printed just because of time restraints, but I would really suggest for the couple of bucks they cost, it would be worth just buying a pre-made one.
I installed it the same way as the fin box, routed out a hole a little bigger than the plug and used epoxy mixed with fibres to fill the gap around the box.
Step 23: Find Some Old Paint and Get Painting
In keeping with the recycled theme of this project, I went to our basement paint pyramid and did a little search for some useable paint to give the final seal for the poor man's fiberglass. The important thing is that the paint is made for exterior use, seeing as it is going to be used in the water. As luck would have it, I found an old, rusted can of white exterior house paint that was left by the previous owner of our house. Perfect.
- Give the board 3 good coats of paint, allowing it to dry between coats.
- You can either brush or roll the paint, but I found the roller gave a much nicer, consistent finish.
Step 24: Make It Fancy (Optional, But Fun)
Obviously, we all know that a plain white surfboard won't surf as well as a well-decorated one, so I got my family to put their design skills to work and we came up with some fun graphics for the top of the board.
- Grab some painters tape and airbrush or spray paint, and get to sprayin'
** Make sure the base coat of paint is totally cured before you apply tape to it. You don't want the tape to pull up the paint when it is removed.
Step 25: Go Surfing!
Take your board out and give it a try!
To be honest, I was half expecting the board to snap in half the first time I stood up on it, however, after a couple days of pretty hard use, I became more confident in the board's strength. It worked as well as could be expected on the small, messy waves at the lake, and I was grinning from ear to ear for the chance to be surfing again in the middle of the Canadian prairies! Thanks, old hot tub cover!
Step 26: Some More Thoughts
A couple of things I learned from this project:
- When TBII cures it doesn't become brittle, but rather a tough, somewhat flexible material. Normal surfboard resins become much harder than the PMF, so my surfboard had much more flex, and less strength than a standard board. My board also got lots of dents on the top surface from my feet.
- The bond between the first layer of fabric and the foam is really important. If I was to do this again, I would apply a thicker layer of glue for that first layer.
- The board is susceptible to heat. I noticed a couple of places on the board where the PMF bubbled up when left in the hot sun for 20 minutes. My belief is that those were spots where the bond between foam and fabric wasn't good enough. Also, perhaps using XPS foam instead of EPS would reduce this problem.
- After a few months, the PMF seems quite a bit harder than it was originally, which is a good thing from my perspective.
- EPS foam does absorb water, so it is important to fix any cracks or holes in the PMF as soon as possible.
All in all, I was happily surprised by the end result of my poor man's fiberglass surfboard experiment. Not only did it work, but it also looks good enough that most people wouldn't suspect it was homemade. Of course, the most important thing is that I was able to make a surfboard without having to worry about using toxic materials in the process. After five years without seeing the ocean, an old hot tub cover enabled me to have the joy of riding a wave once again, and that made it all worthwhile!
Obviously, I can't guarantee the same results if you make your own version of this PMF surfboard, due to the differences in reclaimed materials and techniques. One thing I do guarantee is that you will learn something in the process!!
Thanks for hanging out with me!
If you'd like to see more of my projects you can find me here:
Subscribe to my Costume Making YouTube Channel
Subscribe to my "Everything Else" YouTube Channel
Follow me on Instagram
Check out my pattern shop
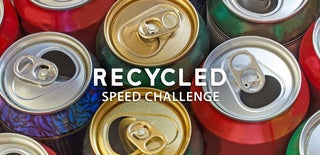
Grand Prize in the
Recycled Speed Challenge