Introduction: DIY Tinfoil Ribbon Speaker
Hello everyone,
In this Instructable I'd like to share with you how to make a simple ribbon speaker with tinfoil as the ribbon diaphragm.
I started this project to see if a ribbon driver design like this could be a viable candidate for some ribbon headphones that i'm planning on building.
They can also be used for a high frequency driver instead of a regular tweeter.
The results that I received greatly exceeded my expectations.
Join me on my journey of creating these...
What is a ribbon speaker?
"These speakers are based on the same principle as cone speakers, i.e. the interaction of the magnetic field of a magnet with that of a wire through which the signal coming from the amp passes. However, the wire is not coiled around a cylinder extending from the diaphragm. The diaphragm itself is the signal conductor, taking the form of a rectangle held by two of its sides. The electronic circuit is drawn on top, trying to spread it as evenly as possible so that the magnetic force is uniform. The fact that the voice coil and the diaphragm are combined in a single piece makes the moving section lighter, thus avoiding, at least in theory, the displacement of the diaphragm. The conductor is spread across the entire surface, exercising a more homogeneous motive power than a voice coil which has to drive a cone at one end." - audiofanzine.com
Step 1: What You'll Need:
To replicate this Instructable you will need the following:
- Access to a 3D printer.
- Approximately 5m 3D printing filament.
- A piece of new tinfoil (aluminium foil) that does not have a lot of creases.
- 6+ 10mmx3mm round neodymium magnets ( This can be other shapes and sizes but the printed holder will need to be altered )
Amazon - 10X3mm Neodymium magnets 100pcs
- 6mm Copper foil tape with adhesive.
- 2 part CA glue or 2 part epoxy.
- A wide gear with quite aggressive teeth .( 3D printable file available )
- Some speaker wire.
- Soldering iron.
- Solder.
- A very sharp hobby knive.
- Foam art sheet or soft rubber sheet
- Some Blu Tack.*
- To drive the speaker you'll need a suitable transformer or a series resistor, I used a 5ohm 40W resistor in testing (links to come)
Step 2: 3D Printing:
First we will need to get the main body of the speaker printed.
I designed it using Fusion 360, it can be easily modified to either use different magnets or change the dimensions of the speaker.
Moving forward for using these as headphone drivers I will alter the design to fit lower profile bar magnets so that I can reduce the overall thickness and i'd duplicate and merge the design so that there are two speakers next to each other.
I also made a quick horn/wave guide to see if it would have a major impact on the volume, but for the intended use I decided to ditch it.
Everything was printed in ABS filament to avoid any deformation from the soldering heat. But PLA and PETG filament would also work.
Printed at 0.28 layer height with a .6mm nozzle.
Attachments
Step 3: Assembling the Magnets:
Now that we've printed the main body we can start assembling the magnets.
Orientation of the magnets inside the body is very important, if one of the magnets is not facing the correct way it will cause major issues with the sound.
To start I stacked all the magnets on top of each other so that I know they are all facing the right way,
Then you want to take a marker and mark the top of each magnet making sure not to flip them over as you go.
Next I place the printed part on it's side on a metal table, this will keep the magnets in place while gluing, now add a drop of glue in each of the indents on the one side of the body and slip a magnet into each indent, the mark you made on the magnets should be facing upwards.
Now if you are using 2 part CA glue you can give it a spray of activator, now you can flip it over and glue in the magnets on the other side. This time the mark on the magnets need to face downwards.
With all the magnets in their places I took a spare magnet and just double checked that all the magnets are facing the right direction, then I just added a layer of glue over all of the magnets to make sure they don't come loose as it would destroy the diaphragm if it did.
Step 4: Assembling the Electrical Connection:
I did a lot of thinking of how I would make an electrical connection between the foil and the speaker wire.
Using copper tape seemed to be the easiest way, it's flat so the very fragile tinfoil lays against it without distorting, already has an adhesive backing which made installation a breeze and because it is copper it's an excellent conductor and easy to solder to.
All I had to do was cut off a strip of about 5cm and wrap it around each side of the main body as shown in the picture.
Easy as that!
Step 5: Making the Tinfoil Ribbon Diaphragm:
Start by placing your piece of tinfoil on a flat cutting surface, then using a new sharp hobby knife cut off a strip that is just narrower than the centre slot of the main body ( 13-14mm wide ) and about 10cm long.
I suggest cutting a few as forming the ribbon may take a few tries .
Next I went through my box of salvaged gears to find one that is wider than the strip of foil and has an aggressive tooth profile that would create a nice deep crease in the tinfoil.
EDIT: Included a 3D printable gear to use
Now lay a strip of tinfoil on your foam/rubber sheet and start rolling the gear from one side with enough pressure to create a deep crease being careful not to tear through the foil. Uneven pressure on the gear tends to make the foil strip curve to the side, It took me 3 tries until I got a good even strip.
Attachments
Step 6: Assembling the Tinfoil Diaphragm:
Now that you have a formed tinfoil ribbon we can attach it to the main body.
I had to do this step twice as the first time I just attached it directly to the main body, this caused a distortion at higher volume as the ribbon started to vibrate against the hard plastic.
To stop this from happening I smeared a tiny amount of Blu Tack against the corner where the ribbon meets the main body, this instantly solved the problem and tightened up the sound.
Cut the ribbon you made to ~65-70mm (If you did not change the dimensions of the main body)
To attach the ribbon to the main body I added a small square of the copper tape to each end of the ribbon, then stick the ribbon in the centre of the main body as pictured.
You want to add slight tension to the ribbon but not so much as to unfold the creases that you made.
Luckily the ribbon is never completely attached to the main body ( it's only held on by the copper tape on the ends ) so it is easily replaceable if it is damaged.
If you have a multimeter it would be a good idea just to make sure you have an electrical connection between the ribbon and the copper tape on the main body.
Step 7: Soldering:
The only thing left to do is solder on the speaker wires!
Because we are soldering on plastic I let the soldering iron heat up completely, added a good amount of flux to the copper tape and then quickly put a blob of solder on each side of the body where your wires will attach.
Wait for the for the places to cool down and then tin your speaker wires and quickly solder them to the main body.
..............Now the time has come
Step 8: Enjoy!
Now you can sit back and enjoy your creation...
Because ribbon speakers have very low impedance you will need either an impedance matching transformer or a suitable resistor in series to connect it to your amplifier.
Unfortunately I'm still waiting on a transformer to arrive so I had to use a resistor, using a resistor has a large negative effect on the output of your speaker so I would highly recommend getting a suitable transformer when making these.
The sound really surprised me, I knew they were going to sound clear and open but I did not expect the amount of bass I got too. They are really nice full sounding drivers and I think will make excellent headphone drivers!
The YouTube video is a sound clip of the speaker playing, they do sound a LOT better in person as it is really difficult to record low volume audio on just a phone mic.
I hope you guys enjoyed this Instructable and share your creations with me.
Happy making!
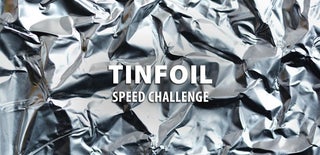
Grand Prize in the
Tinfoil Speed Challenge