Introduction: DRILL-POWERED SPRAYPAINT CAN SHAKER
I do quite a bit of spraypainting, and as part of that, can-shaking. I wanted to make something that would ease up my life a little bit, so decided to design this simple mechanism to shake my cans for me, by means of a drill. If you haven't already guessed, this tool is a bit of a joke, as no one really needs something like this; most tools that need to be invented already have been. But, it proved to be fun, and now I have a submission for the "Build a Tool" contest. Enjoy!
ALL 3D-PRINTABLE COMPONENTS:
Supplies
Essentially everything that I used in order to build this was purchased from ServoCity:
(2m) 5mm OD Latex Surgical Tubing
(1x 2-Pack) 8mm ID 45mm L Linear Bearings
(2x 2-Packs) 1/2" ID 3/4" OD Non-Flanged Bearings
(1x 300mm) 8mm OD Steel Shafting
(1x 150mm) 8mm OD Steel Shafting
(1x 9") 1/2" OD Steel Shafting
(1x) 1/2" ID Clamp Collar
(1x) #8 x 1" Torx Screws
Step 1: BASE
MATERIAL(S):
For the base, I wanted manufacturing to be as simple as possible, so I decided on a basic rectangle for shape. The rectangle measures 24" x 4 1/4" to best fit the space the mechanism takes up. I chose pine just for its ease of manufacturing, and general strength.
Step 2: CAN CLAMP
MATERIAL(S):
(6") 5mm OD Latex Surgical Tubing
(1x 150mm) 8mm OD Steel Shafting
(1x 2-Pack) 8mm ID 45mm L Linear Bearings
(1x 2-Packs) 1/2" ID 3/4" OD Non-Flanged Bearings
(11x) #8 x 1" Torx Screws
(1x) 1KG HATCHBOX PLA 1.75mm Black
(1.5") 1/2" OD Steel Shafting
I first realized I needed a basic pivot for the spraypaint can to rest along in order to oscillate the can up and down. To attach the can to the pivot, I designed a "cradle" that clamps the can along its length using surgical tubing. A small pine board runs along the base of the cradle, connecting the second part of the pivot to the clamping cap at the end. I used a "plasticy" foam to secure the can in place while being shaken. Two linear bearings are fastened along the bottom of the pine board using two printed bearing clamps, one for the piston rod, and one for the clamping cap.
Step 3: "PISTON" COUNTERBALANCE WHEEL AND BRACKET
MATERIAL(S):
(1x 2-Pack) 1/2" ID 3/4" OD Non-Flanged Bearings
(1x) 1KG HATCHBOX PLA 1.75mm Black
(6x) #8 x 1" Torx Screws
(1x) 1/2" ID Clamp Collar
As the main component of the "piston" mechanism this design relies on to oscillate the can, I designed and manufactured a glorified wheel that rests upon a large bracket fitted with bearings. The output shaft runs out of the bracket, and through the wheel. To act as a counterbalance, I designed the wheel as more of a "cheese wedge," with the piston rod attached to the lighter end. The wheel is approximately 9" long from end to end. To fasten the output shaft to the counterbalance wheel, I screwed into the shaft through the side of the wheel, and then ground off the screwheads.
Step 4: PISTON ROD
MATERIAL(S):
(1x 300mm) 8mm OD Steel Shafting
To link the can clamp and counterbalance wheel, I designed a simple link. The link pivots on the light end of the counterbalance wheel, and attaches to a long rod that runs through a linear bearing on the can clamp. The long rod is pressed into the pivot using a pipe clamp.
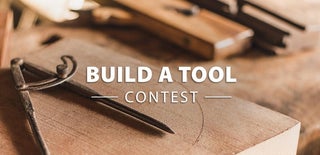
Participated in the
Build a Tool Contest