Introduction: Design and Build a Tiny House
EDIT 1:
Several people have asked about seeing more finished product / exterior pictures in the comments. I'm posting pictures of my adventures with the house every few days on Instagram:
https://www.instagram.com/floshack/
@floshack
-----------------------------------------------------------------------------------
Who are you? What did you do?!?
Hi! I'm Luke, and I'm living full-time in a tiny house on wheels that I designed and built from the ground up. It was (and is) one of the most fun, exciting, and profound projects I've ever taken on. I hope you enjoy it!
I don't want to read your stupid Instructable. Just give me some quick details.
- Built on a 14 ft x 7 ft (ish) flat trailer
- About 98 sqft of living space
- Custom SIP (Structural Insulated Panel) construction
- Roughly R18 insulated
- Propane stove for cooking
- Propane "wood" stove for heating
- Large compact fridge
- Fully off-grid solar/electrical system
- Normal "House" outlets
- Fully functional water system with tankless heater and 33gal fresh water tank
- Normal person sized shower
- Cedar paneling on walls and ceiling
- Hardwood Pergo flooring
- Very large custom-sized bed
- Composting toilet
- Cost me about $15,000 total
- Took me about 800 man-hours to design and build
Does this thing have a name?
The house is named the "Flo Shack". My dear friends suggested "the F Shack", but I thought that was a little crude. Flo Shack is also meant to be a parody of Flo Track (a popular cross country and track website). I run a lot, so it all fits together.
What's this Instructable all about?
This is meant to be a brief introduction to the design and construction of the Flo Shack. I'll cover all of the major aspects of the build from a high level, skipping over the intricate details to keep it readable and somewhat short.
Where are all the details?
If you're looking the nitty gritty details (e.g. how did you make a thermostat that didn't turn your house into a propane bomb or what are pros and cons of series/parallel arrangements of solar panels), scroll down to the last step at your leisure.
Why do you have so few pictures of a super detailed project?
At the time of writing this, I have about 700 pictures of the construction process. I thought that would be rather overwhelming, so I took the liberty of presenting just a sample of some of the good ones here. If people are interested in seeing more detailed posts, I'd be more than happy to upload photos of every intricate detail along the way (see last step for more info).
I want to build one! Can I do it? Where do I start?
Sure! I'd highly recommend reading through this Instructable to start. Then research everything forever. Ok not really, but I'd say I spent AT LEAST 100 hours just poking through other people's builds, forums, YouTube videos, etc. before I decided to take on this project. I don't mean to scare you away, but this is a huge project to start. If you don't put enough thought into it initially, there's a better chance that you won't finish in the long run.
You're living in this thing?
Yeah! I'm always working on little projects to improve the house (e.g. putting in a screen door this weekend) but it's fully functional. One of my favorite weekend pastimes is driving my house up into the mountains of Colorado and finding a nice quiet spot to live for a few days. You can also follow @floshack on Instagram to keep up with my adventures!
That's enough intro, get on with it!
Fair enough. Read on! And remember, if you have half as much fun reading this as I had writing it, then I had twice as much fun as you.
Step 1: Motivation
Disclaimer: This section is probably the most boring - all text and no pictures! Boo! Feel free to skip over it and get to the good stuff!
Why build a tiny house? Here are some of the big reasons I chose to get started.
- Exploring
- It's a lot of fun to drive two hours into the middle of the woods, but then it's a drag to have to drive all the way back home. What if you could take your house with you? Problem solved.
- Get Outside
- (See comic above). A tiny house means you'll inevitably spend more time in the great outdoors.
- Not Renting
- Renting an apartment seems like a waste of money to me. Say I live in a decent apartment for the next 12 month with rent at $1,500 / month. That's $18,000!!! And after that year, you don't have anything to show for all that money you spent. You could easily build your own tiny house for $18,000, and then you still own a house!
- Residual Value
- Related to the previous point, a tiny house has pretty awesome potential resale/rental value. Who wouldn't want to Airbnb for a night in a tiny log cabin out in the mountains?
- Environmental Impact
- I was shocked to read that the average American uses 100 gallons of fresh water per day! There's no way I need that much! I planned this house around a daily use of 4.5 gallons of fresh water, net-zero electric use (all power from solar panels), and a small amount of propane for heating and cooking. I'm also switching to biodegradable soaps so everything from grey water to composting toilet products stay away from landfills and septic tanks.
- Uncertain Location
- Also related to renting, living in a tiny house on wheels means you're not tied down to a location. Find an awesome new job across the country? Move out there the next day!
- Good Time for it
- I started this project at 21 years old, knowing I would have the resources of my university's machine shop, professors, and technicians close by. It seemed like if there was ever a time to start this project, this was the time. **If you're not 21 and finishing up college, don't feel discouraged! There's always a way to do what you want.
Step 2: Time and Money
This is a really big project. Big projects require time and money.
All the Details
After painstaking hours of logging every single purchase I made for the Flo Shack, I'm now happy to share with you my entire Bill of Materials (see "Purchased" tab). This is a completely unabridged list of the things I bought to make the Flo Shack possible.
Cost
I did estimate a budget before starting this project, but was way off the final cost. I think this was mostly due to missing the little things. For example, it's easy to see that 5 solar panels @ $200 each will cost $1,000, but what about the small things? Wire, wire connectors, ring terminals, grounding block, fuses, fuse holders, breaker panels, electrical tools....all little things that add up to a significant amount of money.
I documented and categorized every cent I spent (say that five times fast) on this project. It was often tedious, but I'm glad I did it, mostly for future references. I'll mention this in the "Lessons" section too, but my new rule of thumb is do your best coming up with a budget, then double it.
Time
I did not start documenting my hours worked until a couple months into the project. I wish I had from the beginning so I had a more accurate idea of how much labor this took. One thing I didn't anticipate was the amount of time needed to design. Building a stick frame wall can be done in an hour, but adequately planning for it takes a lot longer.
There were also a couple other things that set me back time-wise:
- Missed something in the design and need to redesign
- Something is harder than planned
- Hard to find parts / long shipping time
- Loss of motivation
- Frustration
Similar to the "cost" rule of thumb above, my time rule of thumb is estimate how much time you need for the project, then tripleit.
Step 3: Trailer / Platform
This is probably the most important step in the whole project. Your platform will define and constrain your design.
Trailer or Vehicle?
Here are a couple options for your tiny house platform:
- Sprinter van
- VW van
- Used military surplus truck
- Pickup truck (this would be a really tiny house)
- School bus
- Transit / Coach Bus
- Trailer
This is my biggest regret in this project. I won't go into too much detail, but I wish I had bought an old used school bus and renovated it into my tiny house. Instead, I went with a trailer that I can tow. It seemed like the more conservative option at the time.
Some of the reasons I decided to go with a trailer over the other options:
- Vehicles break down. Especially old vehicles. Trailers have a lot less that can go wrong.
- Less up-front cost.
- Separate house and vehicle
- You can leave your house and drive somewhere else
- If your car/truck breaks down, your house is still fine
- Little to no insurance hassle
- Less risk (you don't know what you're getting in an old used vehicle)
What type of trailer?
- Size - how many square feet do you need to live?
- Width - trailers are generally a maximum of 102" wide. Wider trailers can be harder to drive and have a higher deck, but give you more room per length.
- Height - how high off the ground do you want your house? Keep in mind the overall height of your planned house for aerodynamics, getting under underpasses, and physically stepping into the house.
- Maximum Weight - houses can be heavy. Make sure you get a trailer that can support your house. Also make sure you'll be able to tow it.
- Material - steel or aluminum? Aluminum is lighter but more expensive. Steel trailers are also much easier to find and offer more options.
- Axles - More axles means more maximum weight, but also more weight you have to tow.
- Trailer Brakes - I believe any trailer over 3,000 lb requires its own brakes. Just one more thing to complicate your towing experience.
After a lot of shopping around, I ended up buying a Worthington aluminum ATV 166" deckover trailer.
Step 4: Planning
Draw lots of ideas! Make a hundred floor plans! Build stuff out of cardboard! A good plan goes a long way towards a successful tiny house.
Not sure where to start planning? Try these:
- Hit the internet.
- See what other people have done, and steal their ideas.
- Decide on your Budget and Time Limit
- Realistically, how much money can you spend on this project? How much free time will you have to work on it?
- Determine your constraints.
- Do you have a maximum weight, height, width, and length?
- List your must-haves and desires.
- e.g. I needed a shower, but only wanted a washing machine. This makes decision making easier.
- Determine what's practical.
- Solar panels and tiny houses work well together. Washing machines not so much.
- Determine your lifestyle.
- Will your house always have access to electrical/water supply or do you plan to be off-grid? Traveling or stationary?
- Research standards.
- There's a reason houses are built with 2x4 walls with studs spaced 16" on center. You don't have to do that, but if you conform to standards, you can take advantage of all of the products that work well with those standards.
- Example: my house has walls with 2x3 studs spaced irregularly. The walls work as intended, but cutting insulation was a pain because the fiberglass bats are all sized for 2x4, 16" OC studs.
Finalizing Plans
I used various software packages (mostly Solidworks and Google Sketchup) for illustrating ideas, but all of the final plans were done with paper and pencil on graph paper, drawn to scale. It was definitely time consuming, but spending all that time meticulously planning on paper made construction super easy - as easy as following instructions for Legos.
Step 5: Exterior Construction
The exterior construction was one of the unique, defining features of this project. I chose to create my own SIPs (structural insulated panels) to save weight and add a thermal barrier.
Stick-frame Walls
The stick-frame walls were built similar to conventional homes. I used 2x3s instead of 2x4s to save weight. I also spaced them much farther than the recommended 16" on center. The spacing was partially determined by features (e.g. one stud on either side of the door) and then spaced evenly from there. It averaged out to about 36" on center spacing. The bottom of each wall was anchored through the aluminum trailer frame with long 3/8" carriage bolts.
SIP Construction
This was probably the most difficult part of this project. The general process was this:
Fiberglass on Inner Surfaces
- Make a wall out of foamboard. Tape together pieces of 4' x 8' board to make bigger walls. Cut to size and cut out windows, doors, etc.
- Lay woven fiberglass cloth down on top of the foamboard wall. Cut to size and get all the wrinkles out.
- Very carefully pour epoxy resin on top of the woven fiberglass. Use pieces of cardboard to spread it evenly without creating wrinkles in the cloth.
- After a couple minutes, with the epoxy still tacky, put the foamboard wall into place. Secure into studs with cap nails.
Fiberglass on Outer Surfaces
- After all the walls were attached to the studs, fiberglass the outside. Wrap a continuous piece of fiberglass cloth around the outside, using duct tape to hold it in place. I had to use two rows because it was only 50" wide (and the walls are >50" tall).
- Pour resin on the edge of the roof so it drips down the walls. Carefully use pieces of cardboard to smooth it against the cloth.
- The roof was somewhat easier because it was nearly flat. Pour epoxy on the upper edge and smooth it down with whatever you can get to it with. I used a paint roller to get the hard to reach spots.
- Cry because you got resin in your hair.
Pro tip: don't get resin on your skin. It'll stay there for a long time or until you get impatient and scrub the top layer of your skin off accidentally.
Paint
The epoxy resin I used yellows in the sun, so it needed to be painted. I used a cheap roller and put on a coat of primer on all of the surfaces (walls and roof). After that dried, I painted a coat of flat white exterior paint. A couple months later, I found this cool video on painting faux wood grain and thought, I can do that! It wasn't nearly as easy as the video suggested, probably due to the surface texture and orientation, but I'm pretty happy with the final look! The "wood grain" was done in two steps: first, a solid coat of a cream color, then a second coat of dark brown, textured with a rocker grainer.
Step 6: Electrical System
I wanted a robust, off-grid solar electrical system. I won't get into a lot of detail here, just give an overview.
Main Components
- Energy Generation - 5 x 150w, 12v Renogy monocrystalline panels
- Energy Storage - 2 x 120 Ah, 12v Apex sealed AGM batteries
- Battery Charge Moderator - Outback 60A MPPT Charge Controller
- Battery Over-Discharge Protector - Victron 220A Battery Disconnect
- Energy Conversion - 1000 W, 12v Bestek inverter
- Energy Distribution (12v DC) - Blue Sea Systems Fuse Block
- Energy Distribution (120v AC) - 70A, 6-circuit breaker box
- Energy Monitor - Bayite Energy Meter
Wires
- AC wiring - 14/3 AWG romex wire
- Solar Panels - 10 AWG with MC4 connectors
- Tying together Batteries, Charge Controller, etc. - 6 AWG stranded welding wire
- DC wiring (to circuits) - 14/2 AWG romex wire
Series or Parallel?
Solar panels can be arranged either in series, parallel, or some combination of the two. With an MPPT charge controller like the one I'm using, the voltage coming in doesn't have to match the battery voltage because the charge controller adjusts it. Here are some pros and cons of each:
Series
- Easier wiring (less components and less wires)
- Higher voltage = smaller wires and less voltage drop
- One shaded panel (or even cell) can knock out the power output of the whole array
Parallel
- Shading not as much of an issue
- Can use simpler and cheaper charge controller
I ended up choosing a series arrangement. I have 5 panels in series producing nominally 60 V or 112.5 V OC (open circuit voltage). Part of the problem with my setup is that I have 5 panels, which isn't a great number when you need things to work in pairs. In hindsight, I wish I had gotten slightly larger panels (like 200 W) so that I could have just used 4 of them, and put them in a series-parallel combination at 24 V.
Step 7: Propane System
There are three things that the Flo Shack uses propane for:
Tanks
The propane comes from two 20 lb propane tanks (like the kind your grill uses) that sit on the front of the trailer. The tanks are connected to a changeover regulator. This does two things: (1) lets gaseous propane out of the tanks at the correct pressure, and (2) draws from only one tank at a time, then switches over to the 2nd when the first tank runs out. This is handy because you can just take the one empty tank out, exchange it for a full one (~$14 at Walmart), and you're back in business without ever completely running dry!
Propane Plumbing
The propane is distributed from the tanks to the appliances with mostly 3/8" copper pipe and brass flare fittings. The majority of the piping is under the trailer and covered by pipe insulation to protect it from debris on the road. The copper pipes come up through the floor very close to the appliances they feed.
Cooking Stove
This one is pretty self-explanatory. It works like any old gas stove: turn the gas on, light it with a match or lighter, and cook some food. I made a giant dutch oven full of black bean soup last night!
Water Heater
I use a tankless water heater as opposed to the more traditional tank style water heater.
Traditional Tank Heaters
A tank style water heater (like the one you most likely have in your not-so-tiny home) works by heating a fixed volume of water (say, 50 gallons) at a time. When you take a hot shower, you pull some of that hot water out, and over time the water heater replaces it with cold water and heats it back up. The disadvantage here is the heater is always working to keep your water from cooling off. Another disadvantage is a limited amount of hot water at a time: if you take a 30 minute long shower at lava temperatures, you'll empty your tank and the water will suddenly go cold.
Tankless Heaters
A tankless water heater works instantaneously: when you turn on the hot water, it starts burning propane inside of it and gets really hot. Water passing through the heater is heated in just a couple seconds, and then you have "unlimited" hot water - providing you don't run out of water or propane! So far, the Ecotemp heater I'm using has worked better than expected. It's reliable, easily adjustable, and gets my water really hot, really fast (in a good way).
Heating Stove
This was by far the most complicated part of the propane system. I originally set out to find a heater that:
- was not way too big for my well insulated 98 sq ft
- was direct vented (meaning the combustion products go outside instead of into your living space)
- had thermostat control (automatically turns on and off to maintain a specific temperature)
- was reasonably priced
- looked nice
I looked for a long time and couldn't find one. So, I decided to build my own.
I started with a Nu-Way 2000 propane stove. It has a simple control that lets you vary the size of the flames (and thus heat output). This was a good start, but then I had to design a control system for it. Here's the rough outline:
- Arduino Uno does all of the logic processing
- Thermocouples measure temperature inside the house, outside the house (not really relevant, but nice to know), and inside the stove, to ensure the pilot light is still on.
- A pilot light with a needle valve provides an ignition source. This is always burning when the stove is maintaining the temperature.
- A 12v DC brass solenoid is actuated by a solid-state relay. This allows the Arduino to turn the flames on and off.
- The Arduino code is pretty straightforward and centers around redundant safety. The ultimate goal is to never have a situation where gas is flowing with no flame. That creates a lot of flammable gas in an enclosed space, also known as a bomb.
- A smoke detector and carbon monoxide detector offer extra safety for detecting problems.
There's obviously more detail to the thermostat system than is written here, but for the sake of this overview Instructable, I'll keep it to that for now.
Step 8: Water System
Water is pretty crucial to staying alive. I like to have lots of it on hand. Here are the main components of my water system:
- 33 gallon fresh water tank (this is your supply of water)
- 33 gallon grey water tank (this is where the shower and sink drain to)
- 12v DC pump (this pushes the water out of the fresh water tank to the places that you want it)
- Water filters (takes out sediment and chemicals that you don't want to drink)
- Water heater (heats up water when you want it hot)
- Shower
- Sink
Water Tanks
The water tanks are mounted underneath the trailer so that the top of them are just underneath the floor. They're somewhat rigid plastic tanks, stuffed inside a well-insulated wooden box, and covered with roofing tar (roofing tar is cheap and protects/insulates the boxes). The boxes are secured to the trailer frame with two 16 gauge steel straps each. For reference, a full water tank with the box weighs just under 300 lbs! Hence the steel straps.
Filling Da Tank
The fresh water tank is filled with a hose, bucket and funnel, spout, etc. You just pour water into the port on the outside of the house, and it goes through a tube into the tank. Pretty simple stuff. I opted to skip the pressurized, RV-style water hookup because I didn't plan on using RV water hookups - just one more thing to tie you down. So far, so good!
Emptying Da Tank
There's a large valve attached to the bottom of the grey water tank (there's one on the fresh water tank also, but I don't empty my fresh water very often). When it gets full, you open the valve, and the grey water comes out. I've been using only biodegradable soap, so my grey water contents are: fresh water, vegetable-based biodegradable soap, dirt, and food waste that comes off the dishes. No dumping of chemicals for me!
Where's the black water tank?
I don't have a black water tank, thanks to the composting toilet. No regrets there.
Pump
I have a Shurflo 4048 12v DC pump. It's super simple and works great. Connect it to 12v power and water lines, and it will automatically turn on when it needs to. It maintains water pressure between 55 and 65 psi.
Water Filters
All of the fresh water goes through a 1 micron sediment filter, then a combination lead-flourine filter. I think this drops a good amount of water pressure, but it's nice to have good clean water.
Water Heater
This was discussed in the propane section, so I won't repeat myself here.
Shower
Following lots of other RVer / Vanlifer suggestions, I got an aerating shower head and added in a shut-off valve. These work together to give you a nice shower experience while using way less water. The aerating shower head uses water at a slower rate (1.5 gpm) than a standard shower head (2.5 gpm), but sprays it in a way that gives you good pressure and good coverage. No complaints from me there. The shut-off valve was a great $3 investment. It lets you leave the temperature exactly where you want it, but have the ability to quickly turn the water on and off. Get in, get wet, water off, soap up, water on, rinse off, water off, shampoo up, water on, rinse off, water off. I usually use about 30 seconds of water per shower, which equates to about 0.75 gallons.
Sink
Not much special about the sink/faucet. It's a stainless steel double sink (~33" wide x 22" deep) with a pretty standard pull-down kitchen faucet. I like that the faucet has two modes: a "spray" one that I use mostly for dishes, and a "normal" one that I use for brushing teeth and filling things.
Bonus: Water Consumption Stats
I selected 33 gallon tanks as the amount of water I anticipated using in a week. Now that I've been living full-time for a couple months, I can confirm that I've been pretty close most weeks! I shower every day, frequently two times a day, wash a lot of dishes, and drink a lot of water. I have to be very usage-conscious to make it to a week on just 33 gallons, but it works! For reference, the average american uses 100 gallons of water per day! That's 700 gallons per week!!! (I think a lot of that comes from flushing a toilet).
Step 9: Toilet
Toilet Types
To me, a house needs a toilet. Here are the main options I looked into:
- RV toilet with black water tank
- Marine chemical toilet
- Composting toilet
I strongly dislike the idea of having a black water tank. You lug sewage around with you and need special equipment and a specific place to dump it. It doesn't sound like the light weight, off-grid design I was looking for.
A marine chemical toilet falls into a similar category as a traditional RV toilet with black water tank for me. It's just that you store your chemicals in the toilet instead of an external tank.
When I first discovered composting toilets, they seemed too good to be true. No tanks to empty, no bad smells, good for the environment, cost-effective, no water usage...what's not to love?
Composting Toilet Options
- DIY / Homemade
- Airhead
- Nature's Head
I was very tempted to build my own composting toilet. The parts would have been around $70, as compared to the $1,000 even that most commercial composting toilets cost. That's a huge difference. After a lot of deliberation, I just sucked it up and bought one. I love a good project, but didn't want to have to be troubleshooting my toilet while my only living space smelled like...toilet. It was a lot of money, but I think I made the right choice.
The two toilets I was deciding between were the Airhead and Nature's Head. They're very similar, but I choose the Airhead because (1) it has a larger liquids tank that you dump less frequently and (2) you can pull the liquids tank out without opening up the solids tank, unlike the Nature's Head.
So far, my composting toilet experience has been great! For those of you that will want to ask, no, it doesn't smell =) at all. There's definitely a learning curve, but I feel that I have it worked out completely after only a month.
Step 10: Insulation / Interior Walls
SIPs (Structural Insulated Panels)
All of the walls and ceiling included 1" thick rigid foamboard insulation in the custom sheathing panels, so that gave me R5 to start out with. More details on this can be found in the previous "Exterior Construction" section.
Fiberglass Insulation
Rather than panel over empty walls (empty space between studs), it was a pretty easy decision to add insulation. Low weight, moderate cost, and huge benefits in heating/cooling savings. I did some research first and came up with two main options: spray-in foam insulation and fiberglass. Spray-in was considerably more expensive and would only give me marginal benefits, so I went with fiberglass.
R13 Fiberglass Roll Insulation
Most fiberglass is made for 2x4 walls and I have 2x3 walls. Forums on the internet agreed that compressing the insulation into a smaller cavity than it was meant for isn't ideal (i.e. you'll get less than the rated R13), but still an effective insulator. I went with this idea because 2x3 fiberglass insulation is really difficult to find. The result is that the walls and ceiling have an R-value of ~R18, or probably slightly less due to compression of the fiberglass.
Floor Insulation
I glued pieces of 1" thick rigid foamboard insulation under the subfloor of the trailer. I also put down a layer of 3/4" thick foamboard between the subfloor and the finished hardwood flooring. Assuming each layer of wood has an R-value of 0.5, that gives the floor a total R-value of 9.75.
To clarify, this is the floor construction from bottom to top:
- 1" rigid foamboard
- 5/8" marine grade plywood (subfloor)
- 3/4" rigid foamboard
- ~3/8" Hardwood Pergo flooring
Paneling
I really like the look of wood paneling. Cedar was my first choice because it smells nice and is moisture and rot resistant. I plan to leave it unfinished (as opposed to finishing with polyurethane or similar) because I think it looks and smells nicer unfinished.
Choosing the specific paneling was tricky. I wanted something low cost and low weight but still relatively sturdy. I ended up choosing these: Lowe's Cedar Planks. A lot of people complained in the reviews that many of the pieces were poor quality. I ended up buying 26 packages with 6 pieces each. There were certainly less than perfect pieces, but I think the imperfections add to the cabin look. Some pieces were warped and others slightly broken, but it was thin enough to bend into place. I used about 95% of the pieces I bought. Only one package had boards that were too warped to use.
Step 11: Interior Construction - Kitchen
Perks of a tiny kitchen: it comes together awfully fast when you're building it!
The kitchen counter is 51" wide by 24" deep. On the surface there's a double stainless steel sink with a tall pull-out faucet and a two-burner propane stove. Underneath the counter is a 3.1 cuft compact fridge, the tankless water heater, supply/drainage water lines, and access to the fresh water tank. My garbage can also lives in the space under the sink.
Step 12: Interior Construction - Pantry
The pantry is essentially a giant closet (giant being a relative term here) for storing all kinds of good stuff.
The "ground" shelf holds all of the electronic components: batteries, charge controller, inverter, fuse boxes, etc. All of the other shelves are a mixture of food and cooking supplies. I cook (and eat) a lot, so the pantry is always well stocked! The top of the pantry is open and houses one set of ambient LED strips, a bunch of wires going to different circuits through the house, and occasionally storage for large items (like one of those 6 foot subs!).
As a side note, this was the first piece of "furniture" I built. It was incredibly helpful for tool and parts storage while the house was still coming together.
Step 13: Interior Construction - Shower
The shower was pretty straight-forward to build. I mostly use it for showering.
The three walls are 1/2" furniture-grade plywood, sealed with Thompson's Weather Seal, which makes water drip right off instead of soaking in. I was hesitant to make an all-wood shower, but so far so good. I'm not crazy about the color of the stain. For future builds, I'll go with a clear or light brown color.
I borrowed the floor design in part from a bathroom remodel I saw online, and part was inspired by my love of outdoor showers. The floor is simply pressure-treated 1x2 furring strips spaced out evenly. Water goes between the wood strips, collects in the dark grey vinyl basin, and gets funneled to the drain.
The shower rod/curtain is much heftier than necessary. The rod is a 3/4" galvanized, threaded steel tube made for high-pressure plumbing. I over-designed it so I could do pull-ups on it! Over 200 pull-ups to date, and not a budge from the rod.
Step 14: Interior Construction - Bed Frame and Drawers
A lot of people ask what size bed I have. Queen? Full? None of the above is the correct answer. It's 87" x 50.5" - longer than a California King, and just slightly narrower than a Full. It sleeps two very comfortably. I have 5 foam cushions instead of a mattress. These fit together to make the rectangle of the bed, or slide out to the sides to become seat cushions and backrests when the bed is in "table mode".
Drawers pull out from the bed frame for storage. I had never built drawers before this. They were challenging, but extremely rewarding to complete. The drawers are very deep at 32". I can easily fit all of my clothes in 4 of the 6 smaller drawers on either side. The other drawers house extra blankets, shoes, and one drawer for all of the miscellaneous things I like to have easily accessible (e.g. extra fan, yoga mat, guitar amp, etc).
Step 15: Interior Construction - Flooring
I skipped a step in the traditional flooring method, but it turned out just fine.
Generally, flooring requires a subfloor - usually a layer of heavy plywood to provide a level, strong surface for the flooring. As mentioned in the "Insulation and Interior Walls" section, this is my floor construction, from bottom to top:
- 1" rigid foamboard
- 5/8" marine grade plywood (original trailer floor)
- 3/4" rigid foamboard
- ~3/8" Hardwood Pergo flooring
Ideally, I would have put in a subfloor between the 3/4" rigid foambaord and the hardwood Pergo flooring. However, I skipped the subfloor to save weight (~120 lbs) and haven't looked back since. The floor squeaks in a few places, but it feels like home nonetheless. The Pergo hardwood was really easy to install. It snaps together kind of like Legos, and a couple taps with a heavy rubber mallet locks it in place.
Step 16: Experiment: the Nose Cone
If there's one thing that fluid dynamics taught me, it's that giant cubes aren't aerodynamic. So, keeping in mind that I wanted to pull my tiny house on the highway going 65+ mph, what did I do? I built a giant cube.
Ok, so this thing actually acts like a sail when towing it and significantly decreases gas mileage, much more so than a smaller but similar weight trailer would. To mitigate this, I decided to build a nose cone. The idea was to make the shape somewhat more aerodynamic and save a little in gas mileage.
Results:
Inconclusive due to lack of data. I drove a "control" run of about 150mi without the nose cone, towing with my 2012 Toyota Tundra (4.6 L V8) and averaged 9.5 mpg. Then I added the nose cone and drove from NJ to Colorado with the same truck, about 1,900mi, and averaged around 9.5 mpg. Some days were better and some worse. To get a real answer, I should have driven the same course under the same conditions multiple times, with and without the nose cone. You win this one science.
Actual Results (Speculation):
I think the nose cone was too small to make a significant difference in the aerodynamics of the flo shack. In the future, I will either spend more time designing and simulating a new nose cone shape, or just deal with the crappy gas mileage.
Step 17: Finishing
This section includes installing the little things that don't fall into any of the big categories. For example, blinds, toilet paper holder, shower curtain, guitar mount, etc. The pictures are pretty self-explanatory here.
One thing to note: the odd-looking aluminum structure coming off the back of the trailer is a bike rack that I whipped up about 12 hours before leaving on a one-way, cross-country trip with my house. It has held my bike without fail over thousands of miles.
Step 18: Lessons and Regrets
I learned a TON of stuff designing and building the Flo Shack - too much to document here in any useful way. So, here are some of the lessons I learned that may prove useful.
- Measure twice, cut once
- A classic saying and pretty self-explanatory. Take the extra minute to make sure you're doing what you intended to do.
- Don't buy stuff until you need it
- I bought stuff before I had finished designing the relevant system more than once, only to discover that I actually needed something else. One example is the water pump - I got excited while putting up the walls and bought an RV water pump. After doing some in-depth design, I realized my water pump was undersized. It was too late to return it at that time, so now I have an extra pump.
- The caveat to this is if you find a good deal, jump on it. For example, I wasn't completely decided on whether I was going to do carpeting or hardwood floor, or how I would install either. Then I was at Lowe's and found about 80 sqft of hardwood flooring that had been returned in an open package. It looked like it was still in good condition, the color was OK, and it was marked down from $240 to $30. It was a great deal, plus it made my decision of carpet vs. wood for me.
- You need more space for building than just what you're building (ideally)
- This is especially true later on in the project. For most of the time, I stored everything and worked exclusively in the tiny house. This got to be really frustrating. For the last month or two of building, I rented a small garage where I could store parts, lumber, and tools. It makes a world of difference.
- Get a pocket hole jig
- If you don't have much experience with woodworking and/or lack fancy tools, get a Kreg Pocket Hole Jig. This is a super handy tool for all wood construction and makes strong joints. I wish I had gotten one at the beginning.
- Finish design completely before building
- Don't build stuff until all the parts of that system
- Take weight constraint more seriously
- Your trailer/vehicle has a maximum rated weight that you can't go over. The weight of all your stuff adds up very quickly. Keep it in mind at all stages of the project and always leave a buffer for the unforeseen.
- Document hours and purchases from beginning
- I recommend including brief notes too, like the category you worked on (e.g. water system)
- Excel/Sheets is a nice tool for this because you can get quick stats and sums. You can't have too many spreadsheets =D
- Start a build blog and update it while working
- Writing this instructable has been fun, but a lot of work. In hindsight, I wish I had written about stuff as I completed it. I could have also gotten feedback and suggestions that way.
- Get a Lowe's/Home Depot Card right away to save money
- You're going to be spending a lot of money at the Home Improvement store (for me on the order of $9,000). I suggest you pick one store and get whatever rewards credit or store card they offer.
- Take the time to do things right the first time
- This one got me again and again. There's always a shortcut, and it almost always gets you back. Don't skip the second coat of polyurethane, half-ass the waterproofing, or use nails when you should have used screws. You will most likely have to go back and re-do whatever it is that you skimped on.
- Planning: double budget, triple time
- Planning is hard. After this project, here are my rules of thumb:
- Estimate your financial budget to the best of your ability, then double it.
- Estimate your time to completion to the best of your ability, then triple it.
- Planning is hard. After this project, here are my rules of thumb:
- Take waterproofing seriously from the beginning
- Buy high quality windows and vents made for RVs or boats.
- Get Dicor Roof Seal. This stuff is awesome for creating water-tight seals.
- Nothing crushes your morale like leaks in your roof. I eventually got them all, but it was a long, frustrating process.
Step 19: Resources, Credits, and Acknowledgments
I want to take an entire step here to thank all of the people that helped and supported me along the way in this project. I have an incredibly supportive network of family and friends, who made fun of me plenty along the way, but never doubted me.
First off, I have to thank my heat transfer professor for getting me started with this crazy idea. I don't know if he expected me to take his idea about a cool composite panel and build a house with it, but he was supportive from day one. I owe him a lot for teaching me about heat transfer, life, and how to be a cool dude.
I'd also like to thank the my university's machinists, who always gave me enthusiastic support and frank opinions. These guys are incredibly talented and tell things like they are.
Special thanks to my mom for doing about a week's worth of sewing in one day so I could hit my move-out day on time. Extra special thanks to my girlfriend for always being supportive and loving, even when I would stay up late logging receipts (boring!) or reading threads on skoolie.net.
Also, as with most things I do, I would be lost without the help of my dear friend the Internet (or, more accurately, the people who post stuff on the internet). Without further ado, here is a comprehensive (organized) list off all of the internet resources I used in this build (see Notes/Links tab). Thank you, internet people!
Step 20: Questions? Concerns? Comments? Huge Donations?
I had a ton of fun with this project. I'd be more than happy to hear your feedback or help you on your own tiny house journey. I have hundreds more pictures and wayyyy more information than is in this Instructable. Post something in the comments section, and I'll get back to you as soon as I see it!
If you made it this far, you're a real trooper, and I commend you. If you enjoyed this, I'd appreciate a vote in Instructable's #VanLife contest, but absolutely don't feel obligated =)
Have a great day and happy building!

Second Prize in the
Home Improvement Contest 2017
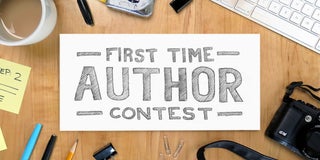
First Prize in the
First Time Author Contest
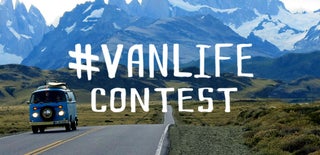
Grand Prize in the
#Vanlife Contest