Introduction: Design and Machine-Embroider Iron-On Patches
Want to make a patch that you can sew or iron onto a bag or jacket or anything you can sew or iron onto? Have access to an embroidery machine? Sweet! I will walk you through the whole process of making a machine-embroidered patch, from design stage to finishing.
This patch is the logo of the Burners, a gang of freedom fighting teenagers with fast cars, from the cartoon Motorcity on Disney XD (which you should ABSOLUTELYWATCH if you get the chance). This particular patch is a commission for someone who's going to be cosplaying Chuck, the Burners' programmer.
This patch is the logo of the Burners, a gang of freedom fighting teenagers with fast cars, from the cartoon Motorcity on Disney XD (which you should ABSOLUTELYWATCH if you get the chance). This particular patch is a commission for someone who's going to be cosplaying Chuck, the Burners' programmer.
Step 1: Stuff You Need
- a design
- a vector graphics editing package like Illustrator or Inkscape
- embroidery software (I'm using DRAWings and old Husqvarna VIP software)
- a USB drive (or whatever hardware you need to get your embroidery files onto your machine)
- an embroidery machine (I have a Husqvarna Viking Designer Diamond)
- embroidery hoops that work with your machine
- stabilizer (I'm using water soluble Aqua Magic)
- fabric (I'm using white flag nylon)
- polyester embroidery thread
- polyester bobbin thread
- iron on backing (I'm using stuff from Colman and Company)
- parchment paper
- scissors
- an iron
- some damp paper towels
- a heatproof surface of some description (I use a small glass mirror I got for $5 at Michaels)
- a hotknife (essentially a woodburning tool with a small chisel tip)
- a vector graphics editing package like Illustrator or Inkscape
- embroidery software (I'm using DRAWings and old Husqvarna VIP software)
- a USB drive (or whatever hardware you need to get your embroidery files onto your machine)
- an embroidery machine (I have a Husqvarna Viking Designer Diamond)
- embroidery hoops that work with your machine
- stabilizer (I'm using water soluble Aqua Magic)
- fabric (I'm using white flag nylon)
- polyester embroidery thread
- polyester bobbin thread
- iron on backing (I'm using stuff from Colman and Company)
- parchment paper
- scissors
- an iron
- some damp paper towels
- a heatproof surface of some description (I use a small glass mirror I got for $5 at Michaels)
- a hotknife (essentially a woodburning tool with a small chisel tip)
Step 2: Creating Your Design
I have chosen a design from the show Motorcity, but you can create your own design or get something off the internet if you like. First thing you need to do is get your design made into a vector drawing. There are lots of tutorials out there on how to use Illustrator and Inkscape, so I'm not going to cover that here. When you've finished vectoring your design, make sure you scale it to the real-world scale you want, since it is much easier to scale a vector file than it is to scale a stitch file.
Once you've created your vector drawing, you may need to save it out as a legacy format or a really old version of your usual format if your vector to stitch software gives you error messages. I generally save my .ai files as the oldest version, Illustrator 3, to keep DRAWings happy.
Once you've created your vector drawing, you may need to save it out as a legacy format or a really old version of your usual format if your vector to stitch software gives you error messages. I generally save my .ai files as the oldest version, Illustrator 3, to keep DRAWings happy.
Step 3: Turning Your Design Into Stitches
I'm using DRAWings, but there are lots of other types of embroidery software out there. Just google for embroidery software. Since there are so many different pieces of embroidery software out there, I'm just going to give a general overview of what I do, rather than detailing how I use my particular software packages. They were pretty easy to figure out with some trial and error and reading the built-in help docs.
I import my vector file into DRAWings and it turns it into stitches. If you see any errors in your stitchout here, you may need to go back into Illustrator and fix any open paths or other issues you may have. You can also do some minimal editing in DRAWings to change the type of fill stitch you use on an area, the stitch pattern, underlay stitching, and whether or not there is stitching at all. If you can't delete an area of stitches in DRAWings, you can delete it in the next step when editing the stitch file directly.
I import my vector file into DRAWings and it turns it into stitches. If you see any errors in your stitchout here, you may need to go back into Illustrator and fix any open paths or other issues you may have. You can also do some minimal editing in DRAWings to change the type of fill stitch you use on an area, the stitch pattern, underlay stitching, and whether or not there is stitching at all. If you can't delete an area of stitches in DRAWings, you can delete it in the next step when editing the stitch file directly.
Step 4: Editing Your Stitch File
Again, since you'll probably be using different software, I'm just going to give a general overview of the steps, rather than a package-specific tutorial. Using the actual stitch editing software, I delete any areas of stitching I couldn't remove in the vector to stitch file conversion step, reorder and merge colors to minimize the number of times I need to change the thread color, and put in trim commands.
Once you are satisfied with your stitch file, save it out as a format that your machine can read and put it on your USB drive or whatever hardware you need to use to get your stitch files onto your machine.
Once you are satisfied with your stitch file, save it out as a format that your machine can read and put it on your USB drive or whatever hardware you need to use to get your stitch files onto your machine.
Step 5: Hoop Your Fabric and Stabilizer
Cut a piece of fabric big enough so that it sticks out of the hoop enough on all sides so that you can grab it and adjust it. Cut a piece of stabilizer the same size as your fabric. Hoop your stabilized fabric, making sure that it's completely taught and free of wrinkles, and attach the hoop to your machine's embroidery arm.
Step 6: Setup Your Machine to Sew
Transfer your design to your machine as per your machine's manual. Thread the machine with the color(s) you need, and set your machine going. Make sure you're using a sharp needle!
Change colors whenever your machine tells you it's ready for the next thread color.
Change colors whenever your machine tells you it's ready for the next thread color.
Step 7: Processing Your Patches
Once your patches are finished sewing, unhoop your fabric and roughly cut out your patches. Leave some border around the edges, we'll trim that later.
Remove your stabilizer (if applicable) as per your manufacturer's instructions. With the stuff I use, Aqua Magic, I run my patches under hot water until all the stabilizer is dissolved. If you're using water soluble stabilizer, wait until your patch is completely dry before proceeding.
If you're using iron-on backing, follow the directions from the manufacturer. With the stuff I use, I set my iron to the wool setting and sandwich my patch and iron-on backing between two sheets of parchment paper with the patch back facing up. I press down with the weight of my upper body for 10 seconds, then flip the whole thing over and firmly give it a once-over with the iron. Then I peel off the backing paper and trim my patch so that there is a small border all around the edges.
Remove your stabilizer (if applicable) as per your manufacturer's instructions. With the stuff I use, Aqua Magic, I run my patches under hot water until all the stabilizer is dissolved. If you're using water soluble stabilizer, wait until your patch is completely dry before proceeding.
If you're using iron-on backing, follow the directions from the manufacturer. With the stuff I use, I set my iron to the wool setting and sandwich my patch and iron-on backing between two sheets of parchment paper with the patch back facing up. I press down with the weight of my upper body for 10 seconds, then flip the whole thing over and firmly give it a once-over with the iron. Then I peel off the backing paper and trim my patch so that there is a small border all around the edges.
Step 8: Hotknifing Your Patches
At this point, you're almost done! Go over to your heatproof surface and plug in your hotknife. While it's heating up, grab a paper towel, fold it up, and get it a tiny bit wet. You will use this to wipe the melted plastic off your hotknife.
Once your hotknife is hot, trim the excess nylon from around your patches. Wipe the melted gunk off your hotknife whenever you finish a cut stroke. You can run a clean part of the hotknife along an edge to further seal it.
Once your hotknife is hot, trim the excess nylon from around your patches. Wipe the melted gunk off your hotknife whenever you finish a cut stroke. You can run a clean part of the hotknife along an edge to further seal it.
Step 9: Patch Get!!
You're done! Enjoy your new embroidered patch! Iron it onto something or sew it onto something, or do whatever it is you do with your patches!
I actually sell these Burner patches here, in case you want one/don't have a machine and are a Motorcity fan. It's pretty awesome what you can do with a bit of equipment and a laptop, huh?
I actually sell these Burner patches here, in case you want one/don't have a machine and are a Motorcity fan. It's pretty awesome what you can do with a bit of equipment and a laptop, huh?
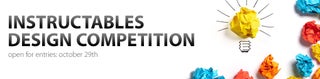
Participated in the
Instructables Design Competition
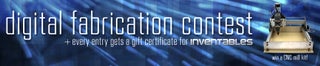
Participated in the
Digital Fabrication Contest