Introduction: Design Your Own Logo and Make a Painting Stencil
Lasers and plotters can be expensive! For most of us we would love to have the use of one, it just really isn't an economical choice for the average home user. So how do I get a professional looking permanent stencil for marketing my logo that I can transfer to anything. Stenciling is a great art art tool and it can take any beginning artist and raise their painting level quickly with professional results. Pre-cut stencils can get expensive building your collection; and often they are the boring same old designs that everyone has. No more do you have to be restricted by the cookie cutter designs out there, with simple easy to use techniques you can design, cut, and paint your personality on anything.
"Custom Made Logo Airbrush Stencils"
"Custom Made Logo Airbrush Stencils"
Step 1: Materials and Tools
What you'll learn:
Designing and creating a personal brand, creating a stencil, then transferring it to any medium using paint.
Materials and tools:
Pencils
Paper (Tracing being the easiest)
Tape
Scanner
Printer or photo copier
Stencil blanks (Hobby Lobby sells them at 10 sheets for just a few bucks)
Hobby knife (like Exacto)
Paint (spray paint, airbrush, etc)
A hard surface to cut stencils on
A little drawing talent is helpful but there are thousands of free designs out there that can be traced and modified to your create your one of a kind logo stencil.
Optional Tools:
Adobe Illustrator (or any of the free tools like http://inkscape.org/screenshots/index.php?lang=en , I'm not soliciting or advocating this software just something I Googled for the instructable)
Adobe Photoshop (or open source like http://www.gimp.org/)
Step 2: The Inspiration, Design, and Mockup
The mockup:
First print or trace up your design's inspiration
Second (freehand) place them either in a viewable position, or (trace) tape them to your design table and cover with tracing paper.
Third draw up your design and shade them in
Fourth (Optional) to refine your design I suggest redrawing with tracing paper sometimes several times to get the perfect creation.
The Inspiration:
For the past few months I've been working on a couple of inventions that I'm planning on marketing. I've been studying many types of marketing and production, what I've learned is the most successful products have a personal brand, something simple and easily recognizable. A logo or brand is not something that should be just thrown together it should be representative of many aspects of the product, the company, and/or the personal mission of the creator.
Creating the design:
Sometimes simply drawing up a design is the best way to trulybuild a one of a kind logo that is entirely yours. In my logo designs I often look out to the internet, personal experience, or just start sketching to see if something develops out of the mind. If you find something you like get pics of it and print them out, alternatively you can trace an outline using various programs like Adobe Illustrator and print out the traces to draw up a custom logo from their inspiration. However you achieve it, the object is to get it down on paper so you can digitize it. Using a vector based logo can be re-used in your upcoming projects and place the image in the minds of those who view your work.
"The design was inspired from an ancient museum helmet I had seen in a visiting Irish armory exhibit and recently had seen reproductions on the internet. Because the actual helmet is a piece of history and out of respect for the craftsmanship of my ancestral country, I left out the actual picture of the helmet from this instructable, though it's not a copyrighted image, I still have respect for the artist"
First print or trace up your design's inspiration
Second (freehand) place them either in a viewable position, or (trace) tape them to your design table and cover with tracing paper.
Third draw up your design and shade them in
Fourth (Optional) to refine your design I suggest redrawing with tracing paper sometimes several times to get the perfect creation.
The Inspiration:
For the past few months I've been working on a couple of inventions that I'm planning on marketing. I've been studying many types of marketing and production, what I've learned is the most successful products have a personal brand, something simple and easily recognizable. A logo or brand is not something that should be just thrown together it should be representative of many aspects of the product, the company, and/or the personal mission of the creator.
Creating the design:
Sometimes simply drawing up a design is the best way to trulybuild a one of a kind logo that is entirely yours. In my logo designs I often look out to the internet, personal experience, or just start sketching to see if something develops out of the mind. If you find something you like get pics of it and print them out, alternatively you can trace an outline using various programs like Adobe Illustrator and print out the traces to draw up a custom logo from their inspiration. However you achieve it, the object is to get it down on paper so you can digitize it. Using a vector based logo can be re-used in your upcoming projects and place the image in the minds of those who view your work.
"The design was inspired from an ancient museum helmet I had seen in a visiting Irish armory exhibit and recently had seen reproductions on the internet. Because the actual helmet is a piece of history and out of respect for the craftsmanship of my ancestral country, I left out the actual picture of the helmet from this instructable, though it's not a copyrighted image, I still have respect for the artist"
Step 3: Scan or Photocopy Your Logo
This is probably the most important step of them all because it will determine how your design is used; touching up, colorizing, or just resizing to fit your project.
My suggestion is to scan it to a computer, if you don't have a scanner take it to Kinko's they will scan pics and drawings and put them on a flash drive for you. Getting your design on the computer will allow you to use it in a variety of areas when marketing your logo. However you can always skip digitizing and simply move on the tracing your design to a stencil blank.
Alternatively if your just looking to make a stencil you can reduce or enlarge the size of your design using a basic copy machine to get the exact size you need for your project
I won't get real detailed with how to use illustrator, however needless to say any program with a live trace tool is a hand drawing to digital scanning must for getting a good vector object that can be manipulated easily. Live tracing is a very simple tool that converts a drawing to a vector object that gives a much cleaner and harder edge to your design.
My suggestion is to scan it to a computer, if you don't have a scanner take it to Kinko's they will scan pics and drawings and put them on a flash drive for you. Getting your design on the computer will allow you to use it in a variety of areas when marketing your logo. However you can always skip digitizing and simply move on the tracing your design to a stencil blank.
Alternatively if your just looking to make a stencil you can reduce or enlarge the size of your design using a basic copy machine to get the exact size you need for your project
I won't get real detailed with how to use illustrator, however needless to say any program with a live trace tool is a hand drawing to digital scanning must for getting a good vector object that can be manipulated easily. Live tracing is a very simple tool that converts a drawing to a vector object that gives a much cleaner and harder edge to your design.
Step 4: Viewing, Printing, and Taping Your Finished Design
Now that we've passed the point of designing your personal image, on to the stencil making!
First step: Look at your finished design and start thinking which pieces of the logo would fall out once the cut begins. This is important to your finished product, there are two ways to complete this task. If your skilled in painting; drawing a few connection lines to those pieces can simplify a stencil cut as you can go back and fill in those lines later during your finish paint. however if this is your first try at the air painting craft; then you'll probably want to make a two part stencils with lining up points to create the pro look.
Second step: Print out the finished product
Third step: Tape a stencil blank to your print out. Another method I've used in the past when I'm out of blanks is to laminate your print outs (however they have a limited life span when painting with rattle can) Tip: Remember if your using a two part stencil it's critical to get your line up points perfect. I will commonly add a few (+) plus signs around the pic when I print the copy twice.
First step: Look at your finished design and start thinking which pieces of the logo would fall out once the cut begins. This is important to your finished product, there are two ways to complete this task. If your skilled in painting; drawing a few connection lines to those pieces can simplify a stencil cut as you can go back and fill in those lines later during your finish paint. however if this is your first try at the air painting craft; then you'll probably want to make a two part stencils with lining up points to create the pro look.
Second step: Print out the finished product
Third step: Tape a stencil blank to your print out. Another method I've used in the past when I'm out of blanks is to laminate your print outs (however they have a limited life span when painting with rattle can) Tip: Remember if your using a two part stencil it's critical to get your line up points perfect. I will commonly add a few (+) plus signs around the pic when I print the copy twice.
Step 5: The Cut's
Cutting a stencil with an Exacto hobby knife can be challenging, tedious, and time consuming, but without an expensive CNC controlled device it's the best way I've found to get the result's cheaply. Be prepared though to make a couple of passes with the hobby knife. No matter how good you get with your knife, you'll never get the exact pressure need to make precise cuts every time. It's been my experience though you'll get better detail making a couple of passes.
The technique is basic; when cutting apply moderate pressure and instead of trying to only turn your hand (like using a pencil) turn the blank as well. Try to make long stoke cuts trying to avoid stopping or lifting the knife as this creates points you'll need to re-cut during the removal of the pieces.
Note: I've seen quite a few stencil tutorials that tell the beginner to use card stock or paper, and it's a great idea for a one time use (maybe even a couple times). Though the nice thing about stencil blanks is that they are resistant to most thinners and they can be used hundreds of times over and over again. As an added bonus the sturdiness of the blank doesn't lift off the project as easily from the paint blast force (creating that cloudy effect around the edges) that you will get from card stock and wax paper.
The technique is basic; when cutting apply moderate pressure and instead of trying to only turn your hand (like using a pencil) turn the blank as well. Try to make long stoke cuts trying to avoid stopping or lifting the knife as this creates points you'll need to re-cut during the removal of the pieces.
Note: I've seen quite a few stencil tutorials that tell the beginner to use card stock or paper, and it's a great idea for a one time use (maybe even a couple times). Though the nice thing about stencil blanks is that they are resistant to most thinners and they can be used hundreds of times over and over again. As an added bonus the sturdiness of the blank doesn't lift off the project as easily from the paint blast force (creating that cloudy effect around the edges) that you will get from card stock and wax paper.
Step 6: Now It's Time to Paint
All done; now it's time to apply the new stencil to your project. Once you've made your first painting pass with the stencil fill in and shadow as needed to finish your custom logo design.
I've included the two pics laptops done with this stencil technique. For those interested in that shadow effect under the Warrior logo on the first laptop, it's very easy trick: Just paint the stencil on as gray or black (once dry) then move the stencil and 1/8 of an inch to the right and paint the top color.
I've included the two pics laptops done with this stencil technique. For those interested in that shadow effect under the Warrior logo on the first laptop, it's very easy trick: Just paint the stencil on as gray or black (once dry) then move the stencil and 1/8 of an inch to the right and paint the top color.
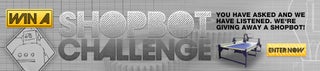
Participated in the
ShopBot Challenge