Introduction: Digital Manufacturing, Drawing and Importing Templates
This is the sixth in a series of Instructables on how to use CAD (Computer Aided Drawing) and CAM (Computer Aided Machining)
This time we are going to look at making 2D objects such as Templates Stencils & Gaskets.
Templates don't even require a laser cutter you can just print them out and are very useful for marking out material that you want to cut, drill or fold. Or maybe you have seen those neat skeleton cut dinosaurs or toys but thought as I don't have a laser cutter I cant make one, Well you can with a printer and a scroll saw. In fact the dinosaurs and spider were cut out of 3mm acrylic with a scroll saw by a 12 year old.
As computer tutorials don't translate to text very well, for this series of instructables most of the info is in the photos. So click on the first photo and use the arrows to go to the next photo. The boxes in the photos show the location of the icons and have have text in them when you hover the mouse on them.
If you haven't seen project one, take a look as it covers where to get Prodesktop, how to activate the software, how to navigate the screen, what you will need and the mouse functions.
This instructable assumes that you are getting familiar with prodesktop so has has not got the detailed instructions of the first three projects.
We will be focusing more on the design part of the program as common commands, engineering drawings and photo album have been covered in the first three instructables.
Other projects are here
Digital Manufacturing - project one Key tag
Digital Manufacturing - project two desk name plate
Digital Manufacturing - project three 3D printed box
Digital Manufacturing - project four laser cut box
Supplies
Step 1: Learning Intentions and Success Criteria
Learning Intentions
- To work safely in the workshop.
- To design a sheet metal box using CAD and produce a paper template.
- To use hand tools correctly and safely.
- To use sheet metal tools correctly and safely.
- To be a self-directed learner.
Success Criteria
- I understand the safety rules and I am working safely in the workshop.
- I can follow the instructions independently.
- I can produce a CAD design box, and use the paper template.
- I can safely use marking out tools, tin snips, mangabend, spot welder and files correctly.
Step 2: Sheet Metal Box Template
The first Template is for a Sheet metal box. It can be quite difficult to mark out sheet metal, and get everything millimeter perfect, and if you have more than one to make, or you make a mistake folding or cutting you have to start all over again.
This step will show you how to draw a box template, that you can print off and stick to your sheet metal Its then just a case of cutting out your box and folding it up. Of course you can print as many as you need so a mistake are not such a big deal.
This time we are not going to use the "design" part of the program as everything is 2D we will just use the engineering drawings.
Be sure to choose the correct paper size for your printer.
As always on this set of instructables, click on the photo and use the arrow keys on your keyboard and look for the little text boxes
Step 3: Using Your Template
Once you have your template printed out we can start making our box. To make our box we are going to use a few different tools, they are all reasonably safe to use but you still need to treat them with respect. You will need to be aware of the sharp edges of the sheet metal as it can cut you pretty good if your not careful.
- First, cut two edges off your paper template so you can align the edge of the template on the sheet metal.
- You can then use a little glue from a glue stick to attach the paper. Don't you too much as it can be difficult to get off later.
- The guillotine can be used to cut the long straight sides, you can see where it cuts by looking between the blade and the guard.
- The small parts can then be cut with tin snips, this is where you need to watch out for sharp edges.
- It is worth the effort to have a look at the video on how to use snips correctly has it will help with the fit and finish of your work.
- https://www.youtube.com/watch?v=T84RfqaFDp8
Step 4: Using the Magna Bend
The Magna bend use a powerful electromagnet to clamp the sheet
metaldown while you bend it. Again it is fairly safe if you are sensible with it. Make sure you are the only one operating it as you could jam your fingers under a clamp if some turns it on while your setting up your work. It take 2 hands to turn it on so it wont jam your fingers if you operate it without someone "helping"
- To turn on you have to push the green button and pull the handle up at the same time.
- Start with the safety edges first and Align the clamp along the line.
- Turn on the machine and bend all the way up on all four sides.
- Use a block of wood and a hammer or mallet to finish off the safety edge but don't flatten it too far as it will make it hard to do the next step
- Now you can fold up the 2 long sides to 90 degrees.
Step 5: The Last Folds and Using the Spot Welder
The last two folds are the hardest to get right.
- First bend the tabs in a little with a hammer or pliers as you want them to go inside the safety edge
- Its now a good time to remove the paper template. ( you will now find out if you used too much glue)
- Next use some small clamps on the magna bend to hold the box down Slowly and carefully bend the side up watching the tabs don't get caught on the side. You want them to go inside the safety edge.
The spot welder is also easy to use
- The spot welder is up next and be aware if not set up correctly or if you have left paper in the welding area it can blow sparks. So best wear some safety glasses.
- The metal can be quite hot after you have welded so watch your fingers
- The two electrodes are used to clamp the join and you can push the handle down and position your box correctly with out it welding
- Once your ready to weld push the handle all the way down, for about 1/2 a second
- Welding for too long may blow a hole in your box
- Once welded up you can file off any sharp edges, and check it over.
- If you stuff it up.... Easy just print off another template and have another go.
Step 6: Skeleton Cut Dinosaur Template
For this Template we are going to Import a DXF file from the internet, and resize or scale it to suit the thickness of the material we are using. We can then print of the project and stick it onto 3 mm acrylic and cut it out with a scroll saw. There are a number of web sites to get DXF files CNC zone, and Thingyverse are quite good.
The dotted rectangle represents the edge of the paper so you may have to move the drawing around and print a number of pages to get every part.
Just a word of warning before you scale or move the drawing it is important to remove the constraints. Also after you hit OK in the scale menu, it may take several minutes to scale the drawing depending on the speed of the computer and the size of your drawing.
You will notice when the constrains are highlighted there are all these dots everywhere, that represents the end of each line. For that reason most DXF downloaded from the internet are unsuitable to cut with a laser cutter as the machine would not cut the lines in sequence. Preparing a drawing for the laser cutter requires another drawing program and will be the subject of another Instructable
As always on this set of instructables, click on the photo and use the arrow keys on your keyboard and look for the little text boxes
Attachments
biplane.dxf
3d chair.dxf
3D-Landschaft.dxf
0012.dxf
101MANTISS.DXF
0402 spinne.dxf
0410-Eifelturm-3mm.DXF
0502-Biene-3mm.DXF
0502-Biene-3mm(2).DXF
0506-Grille01-3mm.DXF
AIRCRAFT.DXF
Angel Fish - 2mm.dwg
Angel Fish - 3mm.dwg
ant.dxf
aviÃo.dxf
aviÃozinho.dxf
BAUS_OLDT.DXF
Bed and Table.dxf
BIERKRANZ.DXF
biplane.dxf
Biplane2.dxf
Blue Whale.dxf
BRONTO.DXF
BRONTO1.DXF
bunny_puzzle.dxf
Butterfly.dxf
cavalo_horse.dxf
Ceratopsier-2.DXF
Cherry picker 4.75mm.dxf
chopper.dxf
cross bow 3mm.dxf
Dino_1mm.dxf
Dino2.DXF
dinobird_puzzle.dxf
dragonfly_2mm.dxf
esqueleto.dxf
F15.DXF
F15puzzles.DXF
FDT63NUGDVYRD18.dwg
frog.dxf
FV4EBZBGDVZF630.dxf
Gesamt_Vektoren.dxf
Girl-l.dxf
Girl-n.dxf
Girl.dxf
guitaropener_redesign.DXF
Harley 1.dxf
Harley 2.dxf
Haus.dxf
Heli.dxf
Heli2.dxf
HELICOPTER.DXF
horse puzzle cleaned.DXF
JINTY WHEELS.dxf
lamp .dxf
LOBSTER.DXF
LOKOMO2.DXF
morrischair.dwg
moskito.dxf
MUEHLE01.dxf
MUEHLE02.dxf
MUEHLE03.dxf
MUEHLE04.dxf
ohiostate laser01.dxf
pitts s1c.dxf
Plane - Cessna - 2mm.dwg
Plane - Cessna - 2mm(2).dwg
pterax1.dxf
pterax2.dxf
rocking horse puzzle2c.dxf
Rooster.dxf
sanke.dxf
Schlitten.dxf
scorpion dwg.dwg
seahorse.dxf
sidecar 4.75mm p1.dxf
sidecar 4.75mm p2.dxf
sidecar 4.75mm p3.dxf
Skull-1.dxf
STEG4.75mm.dxf
tower -3mm.DXF
tower_bridge_teil1.dxf
tower_bridge_teil2.dxf
toy weapons.dxf
train 4.75mm.dxf
TRex.dxf
Tritops.dxf
Tyrannosaurus-1.dxf
Utility Truck 4.75mm.dxf
Weihnachtsbaum.dxf
Working Crossbow dxf.dxf
Working Crossbow V1.2.dxf.dwg
Step 7: Circular Templates for Drilling
Sometimes marking out a series of holes for drilling can be difficult if they have to be millimeter perfect or the piece your working on has a hole or boss in the center. This is is where a paper template can save a lot of time and you easily check your work without having to drill your material only to find that one hole is just a little bit off.
Templates can be very useful for projects that require a part your made to fit another part that someone else has made.
In my solar powered fan Instructable I use a template to get the blades mounted on the motor in the correct position.
In this step Ill show you how to mark out a set of holes around a circle, It can be any number you want.
If you have access to a laser cutter, It becomes even easier as you essentially make a gasket out of paper to check your work, before committing to drilling or cutting the part or material.
So click on the photos and follow along.
Step 8: Drawing Evenly Spaced Holes on a Line or Grid
Ok last step, some times you may want a series of evenly space holes or lines either in a grid or just a row this is the step for you. You can make your self a drilling template for 100 perfectly aligned holes.
As always with these computer based instructable steps click on the photos and follow along, don't forget to print in the correct paper size, and true scale.
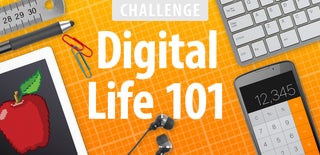
Participated in the
Digital Life 101 Challenge