Introduction: Disney's Beauty and the Beast Miniature Rose Jewelry Box
In this tutorial, I'll walk you through the steps to making a miniature light-up version of the Beast's magic rose from Disney's Beauty and the Beast that is also a hidden jewelry box.
Step 1: Materials Needed
Materials needed for BB Rose Jewelry Box
1- 12”x12”x3/4” sheet of MDF
1- 6”x6”x1/8” sheet MDF
1- 3” x 4” glass display jar (available at amazon: http://www.amazon.com/Collecting-Warehouse-Glass-...
1- 4” diameter decorative wood base (available at amazon: http://www.amazon.com/Darice-9179-57-Wooden-Plaque-4-Inch/dp/B0085TGXG8/ref=sr_1_8?ie=UTF8&qid=1393993043&sr=8-8&keywords=4%22+wood+base+craft)
1- 1/8” brass tube
1- 1/16” brass rod
1- 3/64” brass rod
1- 2 oz package Red Premo or Kato Polyclay
1- 2 oz package dark green Premo or Kato Polyclay
1 roll of green florist tape
1- 3mm 3 volt warm white LEDs
12” of 30 gauge wire
2- 2032 3 volt button batteries
1- on/off micro switch
1 bottle white acrylic paint
1 bottle black acrylic paint
1- 2 oz bottle of water thin super glue
1 can Crystal Clear gloss spray paint
1/4” wide flat brass (optional)
2- 5/16” neodymium disc magnets
Bottle of wood glue
1 sheet of red velour paper or a similar finish paper to line the inside of the jewelry compartment
Double sided tape
Scrap of 1" thick foam (not styrofoam)
Scrap of material to cover the foam that is similar to finish paper.
One sheet sticky back black foam
Step 2: Tools Required
Band Saw or Reciprocating Saw
Finger or Belt Sander
Drill Press or Hand Drill
1-3/8” Forstner or Spade Bit
1” Forstner or Spade Bit
5/16” forstner or drill bit
220 grit sandpaper
Hot glue gun
Wire Cutter
Soldering Iron and Solder
Paint Brushes
1/16” drill bit
tape measurer or calipers
mini pipe cutter or fine tooth saw
compass
Wood Clamps
dust masks
respirator
wax paper
Compass
#11 Craft Knife
Electrical Tape
Small pliers
Hot Glue Gun
Helping hands (optional)
Shrink Tubing 1/8" (optional)
Sculpting tools (optional)
Step 3: THE BASE
Before we start it’s important to note a couple of things. Firstly, all the glass display jars are going to have slightly different interior diameters and aren’t perfectly round. When taking the measurement for the interior diameter, rotate the jar carefully to ensure you get the smallest diameter reading. Secondly, the wood base will also not be exactly 4”. It’s OD will vary as well. When we get to cutting out the storage section, you are going to want to make sure that your storage section is wider by 1/4” than the wood base. Let’s get started!
Measure the interior diameter of the glass jar and the outer diameter of the purchased wood base.
Step 4:
Now that you know the dimensions, we can start to layout the measurements for the wood. On the 1/8” MDF, draw a circle with your compass that is slightly smaller than the ID measurement of your jar. You don’t want it too loose, but you don’t want it too tight. You want to be able to slide a business card around the edge of the jar with the disc inserted.
On the 3/4” MDF draw three circles that are 1/4” wider than the OD measurement of the purchased wood base. Mine was 3.9”, so I will draw a circle that is 4-1/8” in diameter.
Step 5:
Now take your wood and cut out the circles with a band saw or a reciprocating saw. If you have a circle jig, all the better. Either way, don’t cut right to the line, always cut a little wider. You will end up sanding down to the line.
Step 6:
Since you used a compass to draw the circle, you already know where center is on the discs. Using the 1/16” drill bit, drill the center on each of the 4 discs. Use a drill press if you have one, as it’s important that the holes are centered.
Step 7:
We are going to glue the 3/4” discs together. To ensure that they are lined up correctly, we are going to use the 3/64” brass rod and insert it into the center holes when aligning them. Apply wood glue to the bottom of one disc, the top and bottom of the middle disc and the top of the bottom disc. With wood glue, more is better than less. Apply the glue and then sandwich the pieces together. Insert the 3/64” rod and then clamp it to hold it while it dries. Let it sit overnight.
Step 8:
Using your belt sander or finger sander, sand the 1/8” disc to the line.
Step 9:
Add wood glue to the bottom of the 1/8” disc and center it as best you can on the purchased wood base. Test fit the jar to make sure it looks centered. This addition will be used to hold the jar secure on the final piece. If it is centered well, clamp and remove any extra glue with a damp paper towel and let cure overnight. This will become the top part of the base.
Step 10:
Using your belt sander or finger sander, sand the glued together base piece to the line. Rough sand it using 80 or 120 grit paper. You can use up to 220, but don’t over sand the piece yet. Wear a dust mask, as the MDF is really not good to inhale and will get everywhere.
Step 11:
**PLEASE NOTE** Using cyanoacrylate (super glue) in the volumes we will be using is not healthy to be inhaling in a closed room or during sanding. Please use a proper respirator when using. Saturate the both pieces of wood in water thin super glue. Once it penetrates the wood it will create a rock hard medium that we will later paint to look like marble. When gluing, place the piece on some wax paper and the glue will not stick to it. No need to use an accelerator on this, the porous nature of the wood will kick the super glue off pretty fast.
Step 12:
While still wearing a respirator, hand sand the pieces with 220 and higher sandpaper. You want it to be as smooth as possible.
Step 13:
Take the top part of the base and drill out the 1/16” hole through the bought wood base.
Step 14:
Measure 3/4” in from one edge and 3/8” from the opposite side of the bottom of the top part of the base and then, using the center hole, draw an intersecting line.
Step 15:
Using the 1/16” drill bit, drill the hole that is 3/4” from the edge that you just marked.
Step 16:
Set the top part of the base on the bottom part of the base and center it with the 3/64” brass rod. Using a strip of masking tape, tape the pieces together.
Step 17:
Using the drill press, drill through the hole you just made to mark the bottom part of the base. You don’t want to drill through the bottom part of the base, only about 2” down. This will serve as a pivot point to open the jewelry box.
Step 18:
Now switch to the 5/16” Forstner bit. Drill into the other hole you marked on the bottom of the top part of the base the depth of one of the magnets.
Step 19:
On the bottom part of the base, connect the dot from the pivot hole and the center hole. Now, measure the distance from the edge of the top part of the base to the center of the magnet. Adding in the 1/8” for the additional thickness of the bottom part of the base, measure the center point of where the magnet should be on the bottom part of the base.
Step 20:
Using the drill press, drill out the magnet area on the bottom part of the base. Make sure you don’t drill too deep.
Step 21:
Using the super glue, add a little glue to the hole on the top part of the base. Attach the magnets to each other and then insert the magnet until one magnet has been inserted. Then, to ensure it is flush, slide the other magnet off of the first one, leaving one magnet inside the top part of the base. Let it sit for 20 minutes.
Step 22:
Once the glue has set up, insert the pivot wire and attach the second magnet to the top part of the base. Add a drop or two of super glue to the magnet hole on the bottom part of the base, and then align the pivot wire into the hole and then press the magnet into place. This will sink the magnet flush into the bottom half of the base. Let sit twenty minutes or until glue sets.
Step 23:
Once the glue has set, push the top part of the base away from the magnet using the pivot. Don’t pull up, push it. Once the two pieces are separated, pull out the pivot pin and invert the top part of the base. Add a drop or two of super glue around the edges of both magnets to ensure they are securely glued in. Let dry twenty minutes.
Step 24:
Align your ruler to the line you drew through the three marks on the bottom part of the base. Measure 3/16” from the inner edge of the magnet, and then from that mark measure 3/4” towards the center. This is the center mark for the main jewelry compartment. Depending on how big you want the compartment here, you can draw a perpendicular line from that center mark and measure out 1” on either side. This will allow you to drill out three hole widths, creating a larger box.
Step 25:
Switch to the 1-3/8” Forstner bit and drill out the center hole to the depth of 1-1/2” to 1-3/4”.
Step 26:
Measure from the pivot hole on the bottom part of the base toward the center 1/4”. This will be the center for the battery compartment. You are going to overlap the pivot hole by 1/4”. This will help hide the battery compartment when the box is open.
Step 27:
Switch to the 1” Forstner bit. Drill out the hole using the center mark you just made to a depth of 1”.
Step 28:
Take your micro switch and draw out the width of the switch centered on the center line on the bottom of the base piece. You want the switch to be flush with the base, leaving only the toggle protruding.
Step 29:
Using your craft knife or a chisel cut out the area the switch will occupy.
Step 30:
Now connect the area where the switch goes to the battery compartment creating a channel that is 1/4” wide and centered to the width of the switch. This channel will be for the wires running from the switch to the batteries.
Step 31:
Saturate the switch cutout and the wiring channel with super glue. You can do the battery compartment and the jewelry compartment as well, but it isn’t necessary.
Step 32:
Turn the top part of the base over and cut a similar wiring channel from the center hole to the pivot hole on the underside of the top part of the base.
Step 33:
Cut 3” of the 1/16” wire and feed the wire into the pivot hole on the bottom part of the base. Then feed the wire through the pivot hole on the top part of the base. Be careful not to bend the wire. Seat the top part of the base until it locks into place with the magnets. Test that the pivot works and feels tight. If it is too loose, you may want to move up to a thicker rod.
Step 34:
If you are satisfied with the pivot, mark the top of the rod where it protrudes from the top. Pull the wire out far enough that you can snip it just below the mark you made, and then push the wire back in until it is flush with the top.
Step 35:
Set the base aside. It is done until we are ready for paint and assembly.
Step 36: THE ROSE
The first thing we are going to do is create the stem. Since we need to run lights into the rose, the stem needs to be hollow. Take your 1/8” brass tube and gently bend it into the shape of the rose stem from the movie. (I don’t own those images, but the Google has plenty.) You want to keep the overall length of the stem shorter than 3-1/2” otherwise it won’t fit in the jar. Leave approximately 3/4” of the bottom of the stem straight. It will be easier to add the floating mechanism that way later on.
Step 37:
Use your pipe cutter or metal saw to cut the stem at the mark.
Step 38:
Cut a 1-1/2” and 1” section of the 1/16” brass rod.
Step 39:
Using you helping hands or a friend who has a very high tolerance for hot things, set up the 1-1/2” piece of rod at an angle to the stem for soldering. Again, use your Google’d reference here.
Step 40:
Solder on the first piece of the leaf branch to the stem. If you solder it on at an angle, you don’t have to try and bend it that way later on.
Step 41:
Now set up the second branch of the leaves at an angle to the first one. If you solder quick enough, you will be able to attach them without the leaf branch falling off of the stem. If you need to, you can set all of this up with a couple sets of helping hands before soldering anything. Whatever makes it easy for you.
Step 42:
Using a pair of pliers or your Herculean strength, add some artistic bends to the leaf branches. I find that that sadder they look, the better the overall appearance of the rose. I also give a soft bend up on the main leaf branch coming off of the stem.
Step 43:
Take your 3mm 3 Volt LED and your 12” of 30 gauge wire. Strip back a little bit (a 1/2”) of the wire coating and wrap it tightly around the LED leads as close to the bulb as possible.
Step 44:
Solder this wire onto the LED. Then trim the leg back to the solder point.
Step 45:
Now repeat with the other end of the wire and the other LED lead. Don’t worry about knowing which side is positive and which is negative, we’ll deal with that later.
Step 46:
Using a small piece of electrical tape, or shrink tubing, wrap the exposed connections.
Step 47:
Insert the wires into the stem at the top where the rose will go and feed until the LED is the only part exposed. If you can only feed it to the taped off part, that’s fine as well.
Step 48:
Take a small ball (size of a small marble) of the Red oven bake clay and knead it until it warms up. The red pigment will come off onto your hands. It won’t hurt you, but it will happen.
Step 49:
Pull off seven to nine pea sized bits of clay and roll into small balls.
Step 50:
If you have sculpting tools, great, if you don’t you can use your fingers for this next step. The important thing to keep in mind is you need lubrication. Take one of the pea-sized balls and place it in your off-hand palm. Take your finger or a rounded sculpting tool and wet it with your spit. Yep, free lubrication. Water doesn’t work as well. Flatten the ball into your palm using a circular motion. If the clay is sticking to the tool or your finger, you need more spit. We are making petals here, so they can be pretty thin, but the overall shape should be a solid “U” shape.
Step 51:
Now take your petal and wrap it around the LED and part of the stem.
Step 52:
Repeat with the next pea-sized piece of clay, but when placing it on the stem, overlap the first piece.
Step 53:
Repeat with the rest of the petals, making sure to overlap the seams of each layer. You can also flare out the tip of the petal to give it a more realistic look.
Step 54:
Once all of your petals are on the rose, make sure the LED is still visible in the center. Now, lick your index finger and your thumb and gently pinch the base of the rose to round it off and get the petals to stick to each other.
Step 55:
Now take a small marble sized chunk of the free clay and knead it until it is soft.
Step 56:
Pull off a two pea size chunk of clay and form it into a flat tear drop shape.
Step 57:
Using the same technique as the petals, flatten out the tear into a leaf shape.
Step 58:
Lick your thumb and index finger again and gently pinch the leaf up the center to create the main vein. Don’t fold the leaf. Place it flat on a finger of your off hand and pinch it while flat.
Step 59:
Using a toothpick, piece of the 1/16” rod, a dull knife, cut tiny notches down the sides of the leaf.
Step 60:
Test fit the leaf over the leaf stem. The area you pinched should lie over the wire. If you are happy with the fit, remove the leaf and add a little bit of super glue to the stem. Then replace the leaf. The superglue will instantly bond the soft clay to the wire.
Step 61:
Repeat with second leaf, making it slightly smaller than the first.
Step 62:
Pull out another small chunk of green clay and roll into a thin snake.
Step 63:
Take a small part of the snake and wrap it around the base of the rose like a ring.
Step 64:
Using the pinch method, smooth the clay into the base of the rose.
Step 65:
Now take four small parts of the snake and add them to the green ring so that one edge connects with the ring and the other end sticks out away from the flower.
Step 66:
Using the pinch method, smooth the ends into the green ring.
Step 67:
Now gently bend the four snakes down creating the base of the rose.
Step 68:
At this point, take a look at the rose and decide if it needs a couple more petals to make it look better. I feel mine does. If you are happy with your flower, place it and it’s holder (helping hands in my case) into an oven at 265 degrees Fahrenheit for 20 minutes.
Step 69:
Once the rose has cooled down, wrap the stem and any exposed brass with the florist tape.
Step 70: PAINTING
Assemble the base. Using the white paint, base coat the base with a few coats until it is fairly uniform in color. After the base is uniform in color let it dry.
Step 71:
Saturate the brush with water and then coat the base in a wet white base coat again. While the wet base coat is still wet, add a little black to the brush (don’t worry about cleaning it out). Tap the brush to create two medium sized veins across the base.
Step 72:
While it’s still wet, add a little more black to the brush and then paint a thinner vein on one side of the wider vein.
Step 73:
While still wet, rinse out brush and then add a little white to the brush and then tap the edge of the vein furthest from the black edge to further feather it out. Clean out brush and let the base dry.
Step 74:
Once the base is dry, saturate the brush again and mix some water with some white. From a height of about a foot above the base, tap the metal ferrel of the brush on the meat of your hand below your thumb repeatedly while aiming at the base. This will spatter tiny drops of white paint onto the base.
Repeat this step adding more black to create grey, and then again to get closer to black. Clean brush and allow base to dry.
Step 75:
Once the base is dry, separate the top from the bottom part of the base and set the top part aside. In the section of the base that has no paint, base paint it out to white without overpainting onto the previously painted base.
Step 76:
With a wet brush, add a little black to create grey and create the wide veins again. Create the smaller veins with a little more black, and then spatter again. Allow to dry.
Step 77:
Once the base is completely dry, reassemble and then spray with the gloss clear coat and allow to dry. Once that's dry, separate the base parts again and coat the top of the bottom half of the base. Allow to dry.
Step 78: Assembly
Using the 1/16” drill bit, drill out the center hole on the top part of the base to free it from any dried paint.
Step 79:
Insert the 3/64” wire into the bottom of the stem until it won’t go any further. It should make it past a turn or so. Be mindful of your wires.
Step 80:
Test fit your rose by feeding the 3/64” wire through the center hole and then placing the jar over the rose. You may need to bend the stem or leaves a little to get it to fit. Ideally, you want the stem of the rise to “float” a little above the base, held in place by the 3/64” wire. If you need to trim a little off of the stem, or if you need to resolver the leaves, just unwrap the florist’s tape and do what you need. When done, just rewrap it again with the florist’s tape.
Step 81:
Once you are happy with the positioning, mark the 3/64” wire at the bottom of the top part of the base and then pull it out and trim it. Now, insert the wires into the top part of the base first, and then thread the wire holding the rose until it is flush with the bottom of the top of the base.
Step 82:
Secure the rose and the upper part of the base upside in your holder so you have access to the wires.
Step 83:
Strip back 1/4” of the wiring sheathing. Then take one 2032 3V battery and hold it onto the wires, one on each side. We are trying to establish which side is positive. If the LED doesn’t light up, switch the wires around. Once you’ve established which side is positive, mark it with a sharpie or something so you can remember which one it is.
Step 84:
Using the leftover part of the 1/8” tube, insert the Negative wire’s exposed in into the tube and crimp it down with a pair of pliers. Then crimp the tube again until you have 1/2” of flat brass. Cut the brass tube at the 1/2” mark. You just made the negative battery contact.
Step 85:
Take your micro switch and, if you have a 3 post switch like I do, cut off one of the end leads.
Step 86:
Cut a 3” length of the 30 gauge wire from the spool and trim off 1/4” of sheathing off each end.
Step 87:
Crimp another 1/2” section of tube to one end of the 3” section of wire.
Step 88:
Solder the positive lead from the LED to one of the posts on the micro switch.
Step 89:
Solder the exposed wire on the 3” section of wire to the other post on the micro switch.
Step 90:
Using thin strips of electrical tape, tape the leads onto the battery. Yes, you could use a button battery holder, but I’m cheap, and this works well for tiny spaces.
Step 91:
Using a hot glue gun, secure the micro switch and the wires leading into the battery compartment into the slot we cut out on the bottom half of the base. Be careful not to use too much, as any on the edges or elsewhere on the base will inhibit the rotation of the top.
Step 92:
Carefully turn the top of the base over and hot glue in the wires from the center hole to the 1/16” rod that acts as the pivot. Be careful not to use too much, as any on the edges or elsewhere on the base will inhibit the rotation of the top.
Step 93:
Tuck the battery into the battery compartment and carefully seat the 1/16” rod into it’s hole in the bottom of the battery compartment.
Step 94:
Check to be sure any wires are tucked into the battery compartment hole and then press the top part of the base onto the bottom part. Then check to ensure that the pivot is still working correctly.
Step 95:
Taking the white acrylic paint, paint over the top part of the micro switch to help camouflage it better.
Step 96:
Carefully paint the 3/64” rod that extrudes from the base to the bottom of the rose stem.
Step 97:
Using a little more of your red clay, create two small petals and bake them in the oven at 265 degrees Fahrenheit for 15 minutes.
Step 98:
Make sure the rose head of leaning toward the right, and that the with is directly behind it, so that it is hidden when viewing the rose. Use a drop of super glue to glue the two loose petals to the base below the rose head.
Step 99:
Use the Weldbond or white glue to add 8 to 10 drops around the edge of the top part of the base where the glass dome rests. Then place the jar on top and allow to cure. The reason to use Weldbond is so that, if it ever needs it, the jar can be removed to access the rose.
Step 100:
Now we will finish the interior where the ring will go. Depending on whether you went with a larger compartment or not will dictate how you finish it. I am going for a single ring presentation, so I only have the one hole. Using the red velour paper (or whatever finish paper you want to use), apply the double stick tape to the back of it. I find it is easier to apply it before I cut it from the sheet.
Step 101:
Measure the depth of your compartment.
Step 102:
Mark out the depth of the hole on the back of the finish paper (where the tape is) as well as the length. If you used a 1-3/8” Forstner, the length will be just a little under 4-3/8”.
Step 103:
Cut out the strip and dry fit it to the hole. This is why we dry fit without removing the tape cover. Even though my measurements were accurate, it still needs to be trimmed a little. Remove the piece and trim it to fit.
Step 104:
Double check that it fits (the wrinkles will disappear once the backer is removed).
Step 105:
If it fits, remove the backer paper and insert into the space. Ideally, you would want the seam where the two edges meet to be toward the front of the box (where the magnet is) so that it isn’t visible when viewing from the front.
Step 106:
Take your scrap of 1” thick foam and cut out a circle that is 1-3/8” in diameter.
Step 107:
Cut a slot that runs the length of the foam insert down 3/4”-7/8”. Don’t bisect the foam, you still want it in one piece.
Step 108:
Take some of your double sided tape and place a small piece on the lower part of both halves of the foam insert.
Step 109:
Take the scrap of fabric that matches the finish paper and set it inside the cut in the middle of the foam insert so that the pretty side of the fabric is facing itself.
Step 110:
Remove one side of the backing paper from the tape and press the fabric into it.
Step 111:
Repeat on the other side.
Step 112:
Trim the fabric to the bottom of the foam insert.
Step 113:
Fold the excess fabric to the side of the cushion and insert into the hole. A small spatula will help to force the fabric to lie flat.
Step 114:
Using the sticky back black foam, cut a circle slightly smaller than the circumference of the bottom of the piece.
Step 115:
Apply the sticky back foam and you are done!
Step 116:
Congrats! You have finished the project!!
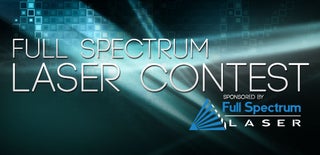
Participated in the
Full Spectrum Laser Contest
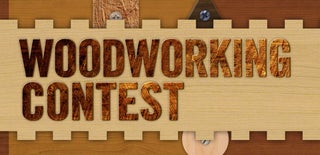
Participated in the
Woodworking Contest