Introduction: Downtown Shelter/Pedestrian Bridge
My name is Bennett Visser and I am going into grade 11 this fall in the city of Edmonton, Alberta. This is my entry for the Make It Bridge Student Design Contest. My intention was to design something that had a very specific purpose, and the answer came from a issue that is prevalent in my city; homelessness.
Edmonton has a large population of people experiencing homelessness, which is a fact I see when I go to school each day as there will be many people seeking shelter in the LRT station or on buses. In the winter the temperature can drop to -40 degrees Celsius/Fahrenheit (its the same temperature, either unit) which with inadequate clothing can cause hypothermia or frostbite. Furthering this problem is that sometimes people will get kicked out of transit stations if they are loitering. I decided to try to reduce this barrier faced by the homeless population.
Another issue that I noticed while taking the bus to school each day is that there is a lot of jaywalking across busy streets, which has caused traffic delays and sometimes accidents. There are crosswalks and even other pedestrian bridges on these roads, however, the crosswalks take a while to change and the pedestrian bridges are inaccessible from the street level. As a result, many people still choose to jaywalk.
These are social and infrastructural gaps that exist especially in downtown Edmonton, and are the ones I will be addressing with my design. With these things in mind, here is my pedestrian bridge!
Supplies
I created my bridge with specific materials in mind, which are the following:
- Precast Concrete (cast off-site)
- 30mm and 22mm thick 316 Stainless Steel (cut off-site)
- 7/16" x 4" Zinc-Plated 410 Stainless Steel Concrete Screws
- Tempered Glass Door
- 45mm Diameter 5mm Thick Pipe
The equipment needed include:
- Arc Welder
- Impact Drill with 3/4" External Hex Bit
- Mobile Crane - for moving large pieces on-site
Step 1: Choosing Location
The first order of business is selecting the site for the bridge. The bridge will take up quite a bit of space as it needs to be wheelchair accessible, which means at least 49.5 meters of ramp in order to reach the 4.15 meter minimum clearance for bridges above roads. However, the bridge also needs to be in an area where it will accomplish the intended task.
The specific site for the bridge I selected is across 99 St NW, near and entrance to Churchill LRT Station, which is beside a large road, many significant buildings, and has a lot of pedestrian activity. This area also has a large length of uninterrupted sidewalk is 5m wide, providing much needed space. Additionally, there are multiple festivals that occur in that area, giving the bridge even more use.
Step 2: Steel Supports: Overview
I really like the industrial and modern style of bridges that utilize steel I-beams and they also provide great strength. However, I did not want mine to look crude so I styled it after other pedestrian bridges that have flowing I-beams of varying curvature and distance between flanges. In this way I will also gain more structural integrity due to the arches created in this way.
Since the support structure will have varying beam height, it cannot be manufactured with the traditional hot-rolling, but will instead have to be plates welded together. This may negate the strength of an I-beam resulting from being homogenous, but it also gains some from the arches added.
Each I-beam is composed of two pieces of 316 stainless steel, which I chose for its mix of strength and corrosion resistance: a flange made of 30mm thick steel and web made from 22mm thick steel. These are to be arc welded perpendicular to each other after the 450mm wide sheets of the 30mm steel has been formed to the pre-cut 22mm steel. Then the finished I-beams are fastened to the footings.
To finish, 1/2 holes must be drilled every meter in the predetermined spots where the concrete pathway will be connected. Following this the structure would be painted, giving it more protection from salt used on the roads and precipitation. This will also make it more aesthetically pleasing.
Step 3: Concrete Pathway: Overview
I decided on concrete as the surface for the bridge and ramp. The main reason for this was that it is impossible not to take up space from the sidewalk, so I decided to make the ramp be as smoothly integrated into the path as possible so that if there is heavy foot traffic, some can even use the ramp as standard sidewalk, if so desired. One issue I ran into was that if I wanted to do this, the ramp would span 100-120m, which there wasn't enough room for. Instead I designed the ramp with a platform halfway up. Then another ramp could continue to the bridge while third went back down to the ground level, thus making the bridge accessible from either side.
In order to follow the minimum 1:12 incline ratio for wheelchair accessible ramps I had to make the arch tangent to a line of this angle. When spanning the 14m of the road (in addition to the margins along
Precast concrete was the material that I chose since it can be be shaped as I want. I decided against using prestressed concrete because I decided that the added benefits of the tension in it would not be required for the low load that the structure will see. It is ultimately meant to provide a non-slip platform that pedestrians can easily walk across and as such need hold itself together.
I made the pathway is 20mm thick throughout the entire bridge. It is 1.5m wide so as to make it compliant with wheelchair ramp regulations. Then I added a 200mm wide and 60mm deep corrugation to increase the rigidity to weight ratio. Additionally, because freezing rain is a big issue in the winter, I added a 1.5 degree chamfer to the cross section so that any water flows off the bridge.
Because the concrete is resting on top of the I-beams it only needs to be fastened strong enough to resist the shear force caused by its own weight on the inclines. For this I chose 7/16" x 4" 410 stainless steel concrete screws because of its high shear strength and ease of use, and also concrete anchors would be excessive. Unfortunately, because imperial units are more prevalent among construction grade materials and I didn't want to sacrifice selection, I could not remain consistent with my metric design. Therefore, a 1/2" hole must be drilled every meter along the bottom of the concrete pieces.
When this is complete the precast concrete parts can be pieced together and lowered onto the steel supports. Then an impact driver will be used to screw the concrete screws through the aligned holes.
Step 4: Shelter
My main goal with the shelter was to make a warmer alternative to bus shelters or transit stations. With this in mind I still opted to use concrete for the shelter. Despite it's poor insulative properties, it will give protection from wind chill and stay warmer than outside. It will also still do the job of protecting occupants from precipitation.
The shelter has 100mm thick walls and a 200mm thick ceiling. A meter tall window stretching the length of the street side of the shelter will be installed along with a glass door on the sidewalk wall. These will provide natural lighting so that no electronics need to be installed. As an added benefit, this can have a greenhouse-like effect and warm up the interior even more.
I designed the glass door to swing outward with a handle on the outside so that no one can be prevented from entering. Additionally, it provides accountability for those using the facility and also allows pedestrians to easily see if there is enough room.
Step 5: Conclusion
So that concludes my project. There where more loose ends than I care to admit, but I achieved my objectives: the final pedestrian bridge gives a safer alternative for those looking to cross the street and can shelter people against harsh weather.
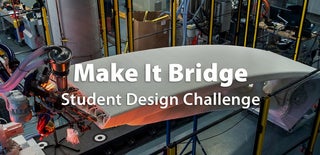
Participated in the
Make It Bridge