Introduction: Ejection Seat From Cardboard!
Dear Instructablers,
This Jumpseat ACES II replica is completely made from cardboard and you can use it as an armchair, it perfectly suits all interiors from feng shui to victorian style , also you can build scaled model for kids and their rockets projects!
Or in case you need to eject something (or someone) annoying, this could be solution for you,
Well you should also add rockets to eject it and since it's from cardboard, you probably burn all to ash and whole the house as well, but besides this little issue, this seat could be cool looking piece of furniture at your crib. Didn't i said it yet? It is fully working seat, my 100 kg (muscles of course) can handle without a single noise.
BTW: I really need a Laser cutter and 3d printer, so please, vote for my project in Full Spectrum laser cutter contest. As you can see i need to laser cut much more cardboard, plywood and print stuff to the cockpits.
Let's jump right into first step!
What you need: Patience, some 3d modelling software, Pepakura designer,123Dmake, Photoshop, Illustrator and at the end Printing company what is able to cut lrge cardboard shapes.
Attachments
Step 1: 3D Modeling and Preparing Mesh
As first step is necessary to download or create 3D model, you can get some free models on 3d warehouse or tf3dm, or payed on Turbosquid. I needed accurate seat since i did it for simulation purpose, so I've modeled one.
When you get the basemesh, open your prefered software, I choosed 3DS Max, not because of Instructables, but because i payed crazy amount of money for license and have to use it, otherwise my otherwife kills me.
When you have opened your model, close all holes, remove all uselles monkey bussiness, for example oxygen bomb, life support hoses and wires and make single mesh from it. Also simplify the mesh a bit, because some of the curves are hard to get from cardboard. Create a copy and use Shell modifier to shrink seat 4mm less to get out thickness of material. Then you have two options, export smaller mesh to 123Make and create simple ribs there, or have more control, but spent longer time in max.
I am doing it in max by creating boxes 5 mm thin (depence on thickness of material) and placing them on right spots. After that i use ProCutter modifier to create exact shape of each rib. Also you have to make holes and locks (interlocks) to each crossection between ribs. Think twice and imagine how you will assembly whole seat to don't cry at the end!
Step 2: Pepakura Power!
Now you have basic skeleton which can carry your weight. If you did it in 123D Make, import obj back to the max and align skeleton inside the seat shell. You will need it to see where you can create folds.
Right now you should export seat mesh (smaller, as we cutted off 4mm earlier) into obj and open it in Pepakura designer. This is cool software which helps you to unfold 3d object to flat plane and you can design carefully each piece. When you will be happy with result, divide your model in same way at Max, use shell on all parts (included ribs) in thickness of material, in my case 4 mm, this is just for check how and where will be added more thickness and you can avoid too tight or too large parts.
So when you are at this stage, you should make overlaps or flaps or folds, i am not sure what is the right name of this. Like everything else, make them wisely, imagine also unwrapping of part to don't intersect each other. You always can export it to pepakura and check how it unfolds and fix then.
When its finished, just throw it into pepakura, export dxf and then open it in some CAD studio, or Adobe Illustrator. Check the scale and to be sure, export all curves from Max with line or rectangle of exact length, for example 100 cm. Then everyone can check the scale and rescale it to right size.
Step 3: Texturize Me!
Time to run around museums and make some cool hig-res photos of rusty steel, rivets and any nice used looking plane parts. Then use some magic in Photoshop and make nice textures which you can add to the Illustrator and place them under parts in curves to have a nice skin. I also have a way how to see result in Max, but it is little bit crazy and maybe hard to understand. Just in short: import dxf to Max, unfold clones of 3d parts exactly like their dxf templates, add morpher modifier on original part and use unfolded part as target. Then you can unfold original part, switch ti top view, add unwrap, and it should have mapping not deformed or scaled. Then render unwrap to texture, open it in Photoshop, place your texture under lines of wireframe, save copy to jpg in RGB, another one to Tiff in CMYK. Still following? Good! Because i am lost...
jpg file open in 3ds max material editor and assign to the part you unwrapped earlier, move back morpher to wrapped model and you should have real preview of your textured part. CMYK file open in Illustrator and place it under curves to be covered by wireframe lines on texture. Don't forget turn off wireframe layer in Photoshop when will be aligned and resave, or you will get wireframe seat heh, funny.
Don't worry if you don't understand my mad explanation, just place your textures, print small model and try it to assembly. On this you will see best what to change.
Step 4: Eject!
As you can see, i did two versions, one with cardboard skeleton and one from plywood. Currently testing
cardboard strength and it is perfect! But for sceptics, you can make it also from other materials, to have seat stronger.
And in case you don't have patience or time to do all of this, just check my website and you can order PDF's
or physical kits. Also scaled versions for kids :)
Thank you all for reading my instructable and if you can, please vote for me in Full spectrum Laser Cutter contest!
Your Lukas.
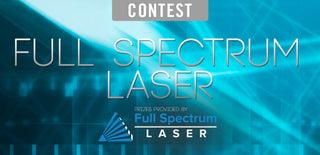
Participated in the
Full Spectrum Laser Contest 2016