Introduction: Exploring the Material Rainbow: Enhancing the Mini LED Table With Polarized Light
In the recent Instructable project Introducing the Mini LED Table: Compact, Affordable, and Enhanced With Computer Vision, we presented an inexpensive, compact, and easy-to-build Mini LED Table (MLT) that is a simple and cost-effective project for a STEM activity and a tool for educational purposes. Among other applications, The device can open doors for students and educators to explore the fascinating world of material science and engineering by providing an affordable and compact solution.
In this new project, we extend the capability of the MLT by adding a device that uses polarizer filters in front of the Picamera, which will provide the capability to visualize the internal stress distribution within transparent materials. These stress patterns due to the birefringence of some materials are paramount for engineering analysis. They are significant in determining various substances' mechanical behavior and structural integrity.
To address this possible application, we will explain how to add a polarizer to the MLT, which is already equipped with computer vision capabilities. In short, the accessory consists in adding a removable polarizer filter onto the Mini LED Table and incorporating another polarizer near the Picamera mounted on a rotatable 3D support enabling the visualization and analysis of colorful stress patterns that arise in transparent plastic and other materials exhibiting photoelastic effects.
By harnessing the capabilities of MLT, polarized light, and computer vision integration, we want to provide educators and students with a powerful tool for visualizing and understanding the intricate stress patterns present in transparent plastics and other photoelastic materials.
Before delving into the details of the project, let us provide a brief overview of photoelasticity and its significance in engineering. Photoelasticity is a powerful technique used to analyze the stress distribution in materials. It is based on the principle that the refractive index of a photoelastic material changes with applied stress. By passing polarized light through a stressed material and analyzing the resulting fringe patterns, engineers can gain valuable insights into the stress distribution and behavior of the material under various loading conditions.
Photoelasticity finds extensive applications in engineering. It aids in designing and analyzing components subjected to complex stress states, such as structural components, machine parts, and even optical devices. By visualizing stress concentrations, engineers can optimize designs, identify potential failure points, and enhance various systems' overall reliability and performance. Additionally, photoelasticity plays a crucial role in material testing, prototype validation, and quality control processes, enabling engineers to ensure the integrity and safety of critical components.
Supplies
- A 3D printer.
- A Slicer program.
- The given STL files.
- Two small screws to fix the wheel to the polarizer filter holder (M1.5 x 5 mm).
- An adhesive polariser plastic film sheet filter for smartphones screens.
- A glass plate. We have used one recovered from a cheap, small picture frame.
- A microscope slide 25x75 mm.
- A diamond tip glass cutter. This is used to resize the glass plate and slide.
Step 1: Bridge Mounted Polarizer
The supplies provide three STL files for 3D printing the bridge-supported polarizer (Figure 1-3). The parts consist of:
- The support that it is attached to the cardboard bridge by sliding it inside the two brackets at the end (Figure 1).
- The rotatory holder of the polarised film filter (Figure 2).
- The wheel helps rotate the filter holder (Figure 3).
Before 3D printing, you need to scale the three parts by a factor of 1000. The screenshots of the scaling tool setup in Prusa Slicer and Ultimaker Cura are shown in Figure 4. Our prototype was printed using layers of 0.28 mm and cubic 20% infill to speed up.
Once 3d printed, use fine sandpaper to smooth the border of the cylindrical platform.
Step 2: Assembly the Polarizer
As indicated in Figure 1, assemble all the parts and secure with the two screws the wheel to the rotating platform. If necessary, add a bit of lubricating grease to smooth the rotation.
Step 3: Preparing the Top and Bottom Polarizer Filter
Cut, using the diamond tip cutter, the rectangular glass plate to match the width of the MLT bay.Cut the polarizer filter to match the cut rectangular glass and stick on it (See Figure 1).
Cut with the diamond tip of the microscope slide to fit the top slot of the rotating holder. Stick the polarizer filter on it and insert it into the slot (see Figure 2).
Step 4: Mounting on the MLT
Add the polarizer to the cardboard bridge, as shown in Figures 1 and 2. Depending on the infill used, the lateral rectangular bracket might break if excessive force is used to push the cardboard, so be careful! The final setup is shown in Figure 3.
Step 5: Take Pictures!
You can use the Python program described in our MLT Instructable to take pictures of birefringent materials. We have used transparent plastic packaging to highlight the hidden rainbows due to the birefringence.
Enjoy the project!
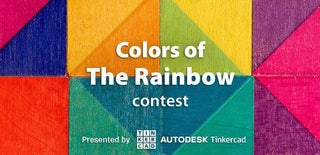
Participated in the
Colors of the Rainbow Contest