Introduction: Faux Polynesian Carved Wood Relief
I had been inspired Polynesian and Hawaiian art for a while. I love the geometric shapes and the worn, hand carved look of relief art from the islands. When I decided I wanted a piece of similar artwork for my house, I turned to a tried-and-true theatrical method of foam carving. I've made lots of scenic elements over the years out of foam to resemble stone, brick, wood and even dirt. I've never attempted a weathered wood carving before. It turns out that with about 5 bucks worth of materials and a few hand tools, a pretty convincing look can be achieved. Here's my experience.
Step 1: Design
The technique described here can be used for any number of relief designs. I'll detail the steps I took and you can apply them to your own creation. Start with a good idea of what your "carving" will look like. It doesn't need to be that exact at this point, though. I've found that a good amount of detail will be added as you go through the process of removing material from the foam panel.
Step 2: Gather Materials
The materials list is open to some deviation.
Grab whatever you have to cut, slice, grind and smooth the rigid foam panel.
The panel is a piece of 24" x 24" x 1" foam insulation from the home improvement store of your choice.
You'll also need some oven dry clay (not pictured) if you want to add a center medallion like I did, but certainly not necessary.
The air tool pictured is a rotary tool with various shaped grinding attachments. A Dremel type tool will work just as well.
Grab some different size paint brushes. Make sure to have one small enough to get into the grooves of your carving.
Step 3: Layout
Using basic carpenters layout tools, start laying in the basic shapes of your design. It's nice to have a large boarder with some degree of detail to add weight and set off the rest of the design.
Use a razor knife or box cutter to cut the layout lines into grooves in the foam. Angle the knife to one side at about a 45 degree angle and make a cut along one side of the layout line. I went free hand because of the hand carved and primitive look I was going for. For a more refined look, run the knife along a straight edge, again, staying to one side of the layout lines.
Step 4: Adding Depth With Applied Corners
I used a miter saw to cut some geometric corners to glue into the corners of my frame section. Hot glue a small piece of foam tp a scrap piece of wood to have something to hold while you run the saw along the foam. After cutting whatever shape you want in the foam block, remove it from the holder and glue it onto the foam panel.
Step 5: Keep Adding Detail!
Once the basic shapes are laid into the foam, goa head and get creative. A lot of the detail in my carving just came to me as I was cutting. When you have an Idea for a pattern that will repeat on other sides, take a few minutes and lay out all of them with a ruler and pencil before cutting. That will give them the best chance of all turning out the same.
Add leaves and pointed shapes by using the same "2-cut" method you did on the grooved lines. Just vary the depth and distance between cuts to get different cutouts. It's a good idea to spring for an extra piece of foam for practicing different techniques on until you're comfortable committing to the final product.
As you add detail, take time to step back from the panel to view it as a whole. turn it upside down and view it in different light. This will give you a good idea of how much or little detail you need to add to make the relief look full but not overcrowded.
Step 6: Break Out the Rotary Tool
I have to admit, I was pleasantly amused and surprised that my pneumatic rotary tool did such a great job of cutting detail into the foam. I used it for cutting round divots and tear drop shapes. Depending on what attachments you try, there are endless possibilities for carving rigid foam with one of these. Besides - it's fun!
Be sure to take it slow, though. I found that when these tools are spinning, they can make their way through 1" of foam before you knew what happened. Use light pressure and practice a little before cutting into the final project.
Step 7: Add a "carved" Texture
Once all the shapes are cut into the foam and you're happy with the design, it's time to give the remaining flat areas of foam a hand carved texture with the rotary tool.
I found that a ball attachment was the best tool for laying in a vertical pattern of subtle carve marks across the whole panel. If you're not using a rotary tool for this, a sheet of 120 grit sand paper run multiple times across the panel will create some texture also.
Step 8: Apply a Clay Medallion in the Center
Again - up to the artist - but I used a little oven drying clay from the hobby store to model a spiral design to glue into the center for added relief and a focal point. You could certainly omit this step, or plus it by adding several applied clay pieces.
Step 9: Paint
Once you're happy with everything, it's time to paint it to look like weathered wood. A nice paint job starts with primer. Choose a dark color and give the whole thing a nice even coat. Let it dry. This step is where the final product really starts to show itself!
Using a medium shade of brown, give the whole thing a coat. This coat can be thinner than the prime coat.
While it's still wet, mix a very light brown and run your large paint brush in a single direction over the surface with a light pressure. This will begin to introduce some graining into the wood.
After that, mix a watery, dark brown and load it onto your thin brush. Use that to darken the grooves of all the lines you carved. Don't be afraid to go heavy on this. It created a lot of depth and we'll smooth it out in the next step.
After that all is almost dry, take more of the light brown and run your brush in the same direction of the "grain" you started creating earlier. Keep a light touch. You just want to hit the high points of the relief.
This is just a general list of the steps involved in creating a realistic wood grain. Use your eye and as many steps and colors as you want until it works for you.
Step 10: Make a Frame
When your masterpiece is completed, go the extra step of using some scrap wood to build an art gallery style frame for it.
Cut a rabbet into 4 lengths of 1 x 2 pine. Ease the edges with a router or sandpaper. Paint a dark color.
Cut a piece of 1/4" plywood into a 30" square. This allows a 3" boarder around the foam panel. Paint it white. You could also just use a piece of white foam core for this.
Miter the ends of the 1 x 2 pieces to fit nicely around the plywood panel. Glue and nail it all together.
Step 11: Find a Place to Display!
Display your new artwork! I hung my panel on the wall of my bathroom. First, I screwed the frame/plywood assembly onto the wall. The I used double sided tape to attach the relief into it.
I hope you'll give this a try. Like I said - these techniques can be use to create all kinds of relief artwork.
The video link below shows the process in more detail.
Happy carving!
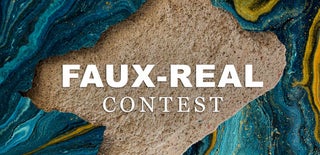
Participated in the
Faux-Real Contest