Introduction: Fiberglass Costume Helmet
This is a fairly advanced project and my first shot at making an Instructable so I hope I don't botch it too badly. It is a lot of work and I did a lot of reading and research before starting, but I got it right the first time and so can you. When you find a step that needs to be clarified, please drop me a message and I'll do what I can to update the page. In reality, each step could well be an Instructable in itself. Maybe one day it will be.
This helmet was built as part of a costume with which I applied and earned membership in the Mandalorian Mercs Costuming Club where you will find a ton of other great tutorials and people willing to help.
You will need a well ventilated space for the fiberglass part and safety says a good respirator for the fumes. Resin also needs temperatures above 15C to cure correctly so this may not be an outdoor project this time of year.
Materials:
- A model to build, either yours or one of the many found online
- Papercrafting supplies
- A computer that either runs Windows or has a Windows VM running
- Pepakura Designer - If you are using an existing model, the free version will work for you. If you created your own you might need the paid version to fine tune you model for printing.
- Printer and printer paper
- Empty cereal/cracker/etc boxes
- Glue stick
- A fast-grab tacky glue [I use Aleen's and it works wonderfully]
- Xacto-style craft knife
- Straight edge, preferably metal
- A computer that either runs Windows or has a Windows VM running
- Fiberglass Supplies
- Fiberglass cloth
- Fiberglass resin and hardener
- Body Filler [Bondo is the most commonly found brand name around here] and hardener
- The cloth, resin, filler and hardeners can be bought at Walmart and Home Depot but there are much cheaper places. Check around for autobody suppliers
- An assortment of sandpaper ranging from 80-2000 grits
- Depending on how nice of a finish you want, if you work up to 2000 will get you an auto-body smooth finish with enough effort
- Many cheap paint brushes
- Walmart sells "chip brushes" for $1 each, I buy them by the case and haven't found a better price
- Rubber filler applicators
- A package of popsicle sticks
- Some dollar-store plastic bowls for mixing
- A set of dollar-store measuring cups [these will be ruined, don't use your mom's/wife's]
- Vinyl gloves
- Paints!
- Filler primer, and paints in the colors you want.
Files / Attachments: THESE FILES ARE RELEASED UNDER A CC-NC-BY-SA-3.0 LICENSE*
I lost the final pepakura files in a hard drive crash, but I have attached a slightly older PDO model which should work for you if you want to build something awfully close this exact helmet. I have also continued to refine the model as my modelling skills improve and have attached a current blender file with a better/higher resolution and more details if anyone wants to try their hand at unfolding and starting from that point. A great deal of the original modelling was done by CyraxLionheart and he deserves a great deal of the credit for anything you make from this model.
*CC-NC-BY 3.0: You can share, modify and use the files but for non-commercial uses only, and only with credit given and you agree to share what you've done with it.
Attachments
Step 1: Make Your Plan
There are two forks to this step, pick one: A) Design and build from scratch; B) Use an existing model. Whichever route you pick here, the paths merge in the next step. It is likely best to start with an existing model unless you are already familiar with modelling.
A) [ADVANCED]
I started with many sketches, some discarded and others set aside for future revision. Ideally, you will want a sketch of the front, top, and one side. These images will be used to create a 3D model. This is a skill in itself and I won't go into details here, but there are outstanding tutorials on CGCookie.com. This one, in particular, will be of great use for this project. I had never done anything to this degree before and had a friend who helped greatly with the modelling. I have since taken to using Blender for my projects; it is free, runs on any OS and works well. If you design your own model, you will need to unfold it as well before moving to the next step. Blender has a plugin for that, or you can do it directly in Pepakura Designer.
B) [BASIC]
There are a LOT of models out there for Pepakura. Fans have made models for pretty much very movie or video game franchise you can think of, a quick search on google for "Pepakura [franchise] armor" should likely find one you can play with, or have a look over at the Replica Prop Forums.
Step 2: Build the Model
When you have your model sorted out from the previous step, it is time to bring the 3D model into meatspace!
What Pepakura Designer does is take the 3D model and unfold it so that it can be built out of paper. On a good model it will be a relatively simple process of matching numbers. Every place where two pieces touch is given a number so you find tab 1 and edge 1 and glue them together. It is an easy but time consuming process. The images in this step show my model being built. To save yourself some time and frustration, I suggest you build the lower ring first and test fit to make sure the scale is the right size to fit over your head. Pepakura Designer lets you scale the print if you need it larger or smaller.
Most people suggest printing to 110lb cardstock and building it from there, but since we are fiberglassing the model I go one step further. Print your model on standard printer paper and use a gluestick to glue the paper to the back of the cereal boxes. and build from there. This will give the finished model enough strength to hold up to the resin without warping too much.
When you have the model assembled you can call it a success and wear your cardboard helmet or move on to fiberglass.
Step 3: Fiberglass!
I find fiberglass to be much easier to work with than most people thing. It can be intimidating but not too difficult. It is also toxic to breath so be safe. Wear a respirator, goggles, and vinyl gloves when you do this. The fumes will be at least as bad as spraypainting so make sure you are outside and/or in a well ventilated area.
- First, your cloth likely came in a giant sheet. Cut it down into manageable strips; I use something on the scale of 3" wide by 6" long for the bulk of the work and keep some smaller pieces on hand to fill gaps.
- Read all instructions on the can for the resin. It will tell you the exact measurements of resin and harder to use, the curing time, etc which will change from brand to brand.
- Safety Third! I've mentioned this several times now. I'm not kidding. Be safe and err on the side of caution.
- You are ready to start!
My process for this is pretty straight-forward. It will take you a while to get a feel for how much resin you can apply in the working time you have before it starts to cure. Take my advice and stop when you notice it starting to gum up at all. It isn't worth that one extra brush-full to ruin your work and resin is relatively cheap compared to starting over. Start with batches under 1 cup [use the ratios on the container] until you get a good feel for it. I also throw the brush out each coat which is why I buy caseloads of the cheapest brushes I can find. I mix my resin in the dollar-store bowls. Look for a bowl that is wide, has a flat bottom, and will flex some without cracking. When a batch of resin is fully cured, you can flex the bowl and pop out the resin in one piece, similar to an ice-cube tray, and reuse the bowl.
In one of the pictures here you can see the "Hannibal Lecter" cage I built to make sure the weaker points didn't warp when they got wet. I just glued popsicle sticks to add some rigidity, just in case.
I start by giving the outside a very thin coat of resin, then once that is fully cured [an hour or so should do it, refer to your container for curing times] the inside gets a thin coat. At this point it is rigid and you can really start working it. In all, I do 6-10 coats on the outside, allowing time for it to fully cure between coats and occasionally trimming the little stalagmites of cured resin you will inevitably get the first few times before applying the next coat. You now have a paper model encased in resin. It should be pretty sturdy at this point and the outside will be a hard shell with an amber tint to it. And, if you are like me, you are pretty stoked about now. Time to move on to the inside, which is only marginally harder!
This is where the cloth comes in. You will have to move faster this time, and you will go through more resin so start mixing up double-batches. You want to give a small area a good coating of resin then take the strips of cloth and, using the brush, press them into the wet resin to embed them. I use a dabbing motion to press it in rather than a brushing motion which tends to pull stands of the cloth out and get messy. The most important parts of this step are to make sure there are NO AIR BUBBLES under the cloth and minimize overlapping the cloth. You want 100% coverage with as little overlap as possible and only as much resin as you need to saturate the cloth. It takes practice. You may want to grab some scrap cardboard to lay a couple layers of cloth on until you feel comfortable risking your fancy new helmet. Work in small sections until you get a solid feel for the process and how much work you can get done in time. Once the whole inside if covered in cloth and fully cured, do it again. The cloth is where the strength comes from and it is only on the inside so decide on your personal balance of strength, time, and cost. You get maximum strength by laying consecutive layers at an angle to each other so if you laid the strips in first layer left to right, do the second facing front to back, and the third on a diagonal, etc. For the helmet in the pictures, I did 6 layers of cloth inside plus 12 layers of resin outside and 6 more resin coats over the cloth inside for a nice smooth finish. When you move on, your helmet is as strong as it will ever be so you make the decision.
Step 4: Filling, Smoothing and Rounding
Depending on the model you used, your helmet most likely looks a lot more like your wireframe model than you would like. Where are the nice sleek curves?! It's all blocky! Time to fix that. This is the most time consuming stage and you can spend as much or as little time as you want, depending on your level of perfectionism and the look you want.
In the photos I used self-adhesive weather stripping to fill in the channels to make sure the filler I added leaves a nice, clean right angle and builds to an even height. You may want to use that trick if you have any such depressions in your design.
Here again, the process is very simple but intimidating. Read the instructions on your filler to get the exact ratios for filler and hardener. Use what you learned from the resin as far as starting with small batches and reusing the mixing bowls. The filler "spatulas" can also be reused a few times and I usually cut he larger ones in half which gives you one nice sharp corner AND a second spatula. If you look around, you can find filler with different color tints; the only difference is the color. I like to get some red and some blue and alternate layers so I can get a good feel for how much or how little is actually being added each layer, but that isn't necessary if you can only find one color.
Mix small batches of filler and spread it thinly on the areas you want to raise up. Filler is not very strong and may crack if flexed or dropped PLUS it is much heavier than fiberglass so keep all this in mind. You wan tto use as little as you can, but you also want to be happy with the finished product As always, there is a balance that only you can decide. Add as little as you can with each coat. It will take longer to add so many layers between curing, but it will save you a LOT of work on sanding later. You can also work on one area while another is curing so if you plan well you can get a lot done with minimal downtime.
You want to build up the flat areas so that when you sand they will make a nice, clean curve. I often sand with some 60grit between applications to get a solid idea of where I stand, and what needs to be done. I also think it is much easier to sand in many small steps than to pend days trying to hack away as a solid mass of filler as I have seen others do. Don't get too excited. The shape is really starting to come together but don't rush things. This is a slow and arduous process but will make the next step immeasurably easier.
Step 5: Finishing
At this point, you have a helmet as strong as you decided to make it, that looks very much like the helmet you envisioned [hopefully]. Now it is time for another decision. How fine of a finish do you want to go for? Start sanding with 60- and 80-grit sandpaper to get your curves nice and sleek. Ideally, the sharp edges of resin over the paper model will start to show through the filler occasionally, this means you haven't added any more filler than you needed to but make sure you stop sanding when you see that. You may need to go back to the previous step and build up the area a little more, that happens quite often. As your curves take shape and the helmet is finally the shape you want, start working to finer and finer sandpapers until you are happy with how smooth it is. Occasionally spray a coat of filler primer and hit that with some sandpaper in the 200+ range to see if it helps fill in some little dimples and scratches. Keep getting more and more fine paper on there until you are happy with how smooth it is. With enough patience and time you can get to a nice automotive finish, if that is the goal. Or leave some divots and nicks in the surface if you are looking for a more worn look.
In the pictures I removed the impromptu "channel protectors", sprayed the whole thing with a few coats of matte black to get a good view of the contours. I went back a few times and fixed some spots either more sanding or more filler. When it was juuuust right, I plugged up the channels again and hit it with a few coats of high-metallic bronze. Your helmet will look like it just stepped off the assembly line!
If you want a visor, have a look at welding supply shops for a "replacement face shield" which is basically a giant sheet of tinted plastic you can cut to size.
Step 6: Optional: Weathering
Your helmet looks brand shiny new. Is that a problem? I like mine to look used, but not abused so I weathered mine with a series of ink washes. The pictures above show lightly-weathered vs unweathered. If this looks like something you want, go to the dollar store and buy some acrylic craft paints in whatever earthtones you can find. I used black, brown, light green and dark green for this effect.
Mix a small dab of paint with a bunch of water. Consistency will vary from coat to coat and based on what you are looking for, but start with a thinner mix and go from there. What I did was use a paper tower to apply the watered-down paint, let it half-dry then use a clean paper towel to buff the paint off the surface. It will stay in all the little divots and imperfections and accent all the little spots. Once that is all dried, mix a slightly thicker wash and repeat. Do it with a few different colors; make sure you get all the spots that have sharp angles and "hard to clean" spots where dirt might be deposited in real life. This is entirely a personal decision on when it is "dirty" enough. When you are happy with it, hit the entire thing with a coat of satin clearcoat spraypaint to seal it. If you go too far, you can get it pretty clean with a wet washcloth, but you will almost certainly have to clean and redo the entire weathering step as you'll never get the cleaned spot to match the rest exactly. It is best, in my opinion, to just go with it if you make it "too dirty".
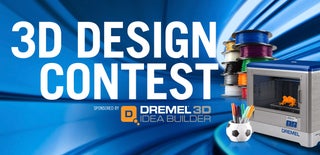
Runner Up in the
3D Design Contest
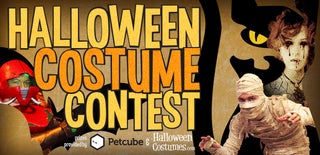
Participated in the
Halloween Costume Contest 2015
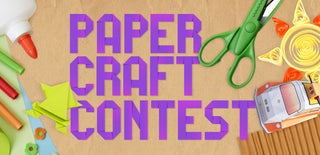
Participated in the
Papercraft Contest