Introduction: Fixing a Trashed Welder
Leaving for work one morning I noticed something different than the usual cans and recycle bins. I noticed a little black box with a bunch of cords. I stopped my vehicle and when I got out I knew what it was. Not only that, but what brand it was and yes, if you know, you know!
Be that as it may, with a glimmer of hope that I could breathe new life into it, I rescued this thing from being stuck in the dump for years.
Supplies
General tooling:
You definitely need safety gear for welding operations!
Rags and cleaning fluid
Brushes, soft bristle & wire
Wire cutters & crimpers
Pliers
Stuff I bought:
New [beefy] ground clamp
6 gauge wire terminals
0.030 flux core wire
weld tips (for the 0.030 wire)
Bearing for the wire feed (I needed a 609Z bearing)
Step 1: It Needs a Bath, Bad
I had to get all of the dirt, leaves, and rust off of this unit. Luckily, when I retrieved it, the snow hadn’t started yet, nor was there any rain! That would have potentially made things way worse.
I gloved up and went to work getting all of the yucky bits off of the unit and the cords. After that it was time to go in for an inspection of why this thing was tossed in the first place. My initial assumption was, given what model it is, the person just got tired of it. Granted, that could still be true.
I plugged it in and heard the fan running which was the first sign that the electronics still worked. Yay. I pulled the trigger on the gun and...Nothing. No movement whatsoever. I realized the wire feed was the culprit that was in need of immediate repair.
Step 2: Feed Me, Seymour
Time was not kind to this old thing because the wire drive roller, the bearing, and the flux core wire itself we’re all rusted.
I removed the gun’s nozzle and the welding tip, pic 1. This proved to be more difficult than I anticipated because the old wire seemed to have (for lack of a better phrase) spot welded itself to the tip. I clipped the wire at the spool end and then threw that old spool away, pic 2 & 3. The inside of the nozzle needed to be cleaned so I just took care of that to get it over with. Then I started to remove the welding tip with the wire attached to it. I did this with pliers and very slowly and carefully removed the old wire. I didn’t want to drag potential rust through the liner and cause clogging. With a little patience the old wire came all the way out, pic 4. I replaced the welding tip on the gun with a new 0.030 tip and also bought a new spool of associated flux core wire, pic 5.
With that part done I figured it was time to feed the new wire in. No big deal except now the drive unit wasn’t grabbing it. Tensioning didn't help so my next point of action was to replace the bearing on the drive unit because it too was rusty & seized. Fortunately, I was able to see the code on the old bearing, which was Z609. These are 9mm X 7mm X 24mm (ID X H X OD). I ordered replacements which came in a pack of 10 and reinstalled it (a little bit overkill but at least I have spares).
It was time to try and feed that wire again. It did, however, this time it failed to drive at a consistent speed. I realized that the old spool was 0.035 and I bought 0.030. I had to check the drive roller to make sure that it was set to the correct wire, pic 6. After removing the drive roller, I noticed that the teeth were gummed up pretty harshly with metal shavings. I brushed its teeth with a wire brush, replaced it with the correct wire number showing on top, and locked it back into place and engaged the tensioner, pic 7. Speaking of tension, it was rising at this point. I figured if that last thing didn’t work then I may have to replace the liner...Fortunately, I did not have to and it came out smooth as butter, pic 8!
Step 3: Stay Grounded
As you can see, the drive roller wasn’t the only thing that was rusty. Exhibit B: the ground clamp.
It was disgusting and needed to be replaced. I have also heard that this clamp (even straight out of the box) is less than stellar. I replaced it by snipping off the old one, installing a terminal to the exposed stranded wire, and attaching it to the "Mr. Universe" of ground clamps.
Step 4: You May Fire When Ready
I was ready! I put on my welding safety gear, used my grinder to expose bare metal out of some spare 16 gauge, attached the ground clamp, and was ready to fire it up. Sure enough, it arced and made some spatter. Good enough for me at this point!! I was happy that it ran and that it ran consistently. It is nice to know that I saved this from a life in a landfill and that it won't rot away somewhere.
Now that I know this thing works, my plan is to mod it to run DC electro-negative (as opposed to AC).
Currently, I didn’t need a welder for my project ideas but,
A) this was “free,”
B) repair/mods are relatively cheap, and
C) there’s ALWAYS room to grow.
I just want to reiterate, yeah this isn’t the best model especially since I first learned MIG at Techshop. However, it’s better than nothing! Especially, when the machine cost me nothing.
Hopefully you will see some welding incorporated in my future projects, fingers crossed.
If you have made the mod I am referring to, let me know in the comments how it went and any tips & tricks you are willing to share. See you for the next one.
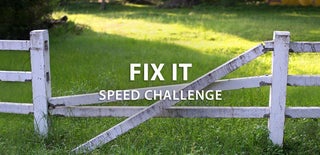
Participated in the
Fix It Speed Challenge