Introduction: Fluorescent Acrylic Wand
I like making magic wands, and I like fluorescent acrylic. If you do not know what fluorescent acrylic is, check out the next step for more on it. A friend gave me two displays from where he works, both made from this awesome material, and I decided to turn them into something as magic as the material.
Full disclosure, the final effect is more subtle than I had hoped, but it nevertheless turned out to be an awesome piece that looks somewhat off - which is the point!
Step 1: What Is Fluorescent Acrylic?
Fluorescent acrylic is generally used in display cases and wherever you want an unexpected effect to draw the eye. It works without additional light sources or electronics, simply based on the ambient light that is already there. (It does not glow in the dark, though!).
What this does is that its edges will glow much brighter than they should, and you can get an idea of that in the pictures above. This happens because it "re-routs" a bit of the light passing through it towards the edges, while not being noticeably dark to look through.
Scientifically speaking, I do not feel competent to speak scientifically on this. It just looks cool.
Step 2: Materials and Tools
Here are the materials you will need to make this wand:
- fluorescent acrylic - This is pretty much mandatory if you want to make a wand out of this stuff
- glue - you need something that reliably bonds with the acrylic and is transparent. I recommend doing a few tests beforehand. For me, the dedicated plastic glue did not work, but ca-glue did, so that is what I used. I also used ca-glue as a finish.
- scrap pieces of wood - I used two blocks to hold the blank on the lathe, and depending on how you want to do this they come in really handy.
- sandpaper or similar - to finesse the shape as well as to prepare for the finish.
And those are the tools I used, and some that you might be able to substitute:
- band saw - read the next step regarding your options for turning sheets into turning blanks. A band saw is your best choice here, but a scroll saw or a coping saw will do the trick as well.
- clamps - to hold the pieces together while you glue them. Only necessary if the glue you use takes a while to set. The ca-glue I used set so fast a few second pressing them together was enough.
- a lathe - to hold and possibly turn the wand. I did not actually use it for turning in this project, so you could substitute it with anything that can hold the blank in place for use with the next tool, the
- angle grinder with a (coarse) flap/sanding disc - to give the thing shape.
- belt sander - to remove the wooden blocks and to finesse the shape. You can use other types of sanders or hand-sanding here.
Step 3: How to Best Turn Sheets Into Cylinders
For the purpose of this project, I want to turn sheet material into a cylinder, or at least close to it.
The easiest method would probably be to cut it into strips, then squares, and stack them. But consider that if you want something round, then all those corners will go to waste. How much waste, you ask? Well, look at the first picture in this step to get an idea.
The left pile on the right was made that way, from a piece of equal size as the stack on the left. That was made using another technique, which I will show you in the next step.
Step 4: How to Cut a Sheet Into Hexagons
The solution is cutting the sheet into hexagons! And believe me, it is much easier than it sounds. Yes, you could do it with a scroll saw or a fretsaw after tracing the full pattern on the plastic, but there is (in my opinion) an easier way, especially considering that the corners of these hexagons will be lost, anyway.
Instead of tracing the complete honeycomb pattern you only need to mark the corners of each hexagon. Then, you drill holes there with a diameter larger than your (band) saw blade. And finally, you cut from hole to hole - no curves, no awkward turns.
You can find the honeycomb pattern I used as a template on my homepage, or you can easily make one yourself, say, in Inkscape.
Step 5: Gluing Up the Pieces
For this step, you need a glue that bonds well with the acrylic. I am sure that there are specialized adhesives for that purpose, but I did not look into those but used what I had in my shop. And, after some tests on scrap pieces, I found that ca-glue did the best job connecting this kind of plastic.
I started by gluing up pairs and hold them using spring clamps, but I eventually realized that the glue works faster than I do, and started just piling them up without a lot of wait time. I started out with the red, then the orange, and eventually the yellow ones.
To finish off, I glued two blocks of softwood to the ends of the blank in order to mount the whole thing on my wood lathe.
Step 6: Turning the Wand (or Not)
With the blank mounted between the centers on the lathe - it took some eyeballing to keep the plastic blank centered rather than the blocks on the end - I tried to turn it into a nice round wand shape.
I really tried.
I have tried traditional turning tools, carbide insert tools, and, after both failed to deliver, I have even tried to use coarse sandpaper. And don't get me wrong, all those methods would probably have worked eventually, but it would have taken a lot longer to get this piece down to round.
Step 7: Shaping the Wand
Eventually, I decided not to turn this wand, but I left it on the lathe because it still works well as a mounting system. And the tool I finally had success with is the angle grinder with a coarse sanding disc. It made a mess, despite me trying to use dust collection. But it worked, and that is what sold me on the idea.
I started flattening out all the corners and edges. Once I had a flat (if not round) shape, I began to remove more material to make the "business end" of the wand.
Step 8: Making It Look Pretty
Power-sanded acrylic is not the prettiest material around, and neither is it the prettiest that acrylic can look. Especially since this material is meant to do weird things with light, I wanted the surface to be as clear as possible.
I started out sanding it with the lathe spinning, but I soon discovered that this would only sand the "high spots", i.e. the parts that were further off axis. So instead, I started hand-sanding laterally, and that did the trick. You do not need to actually get the whole thing smooth because ca glue finish.
This stuff, as nasty as it glues things together (and to the piece if you are not careful - see the last picture in this step), it gives you an awesome finish that looks, feels and is pretty much smooth. You can still "buff it out" with fine grit or polishing compounds, but ca glue is a great leap when you started with rough acrylic.
Here is how you do it. Have the piece slowly spin on the lathe (if possible). Start adding ca glue to it while you are holding a paper towel beneath it and onto the workpiece. You have a couple of seconds here. Move glue and towel laterally to cover as much plastic as you can, then remove both and give the glue time to set. A minute should do. Repeat until the whole thing is shiny.
If you are too impatient, your paper towel will stick to the glue, and you will have to sand it down and redo the process. Ask me how I know...
Step 9: Getting Rid of the Wood
I did some buffing on this, but eventually, I was happy with how it came out and wanted to remove the blocks of wood.
The top came off treacherously easily - just with a flick of the thumb. When I tried the same on the bottom, the wand came apart at a spot where apparently the glue did not cover the whole face. I managed to glue it back together and took to the miter saw to remove most of the wood.
Then I sanded down to acrylic on the belt sander where I also rounded over the tip. I then did some additional hand sanding and a spot of ca-finish on it to make it look in sync with the rest of the wand.
Step 10: Done!
While I will admit that I had hoped for something even more spectacular as far as the light bending properties are concerned, this wand still looks amazing. The camera fails to do it justice. The effect is subtle, but I think that is what sells the idea of this being magic. It is not "in your face" magic, but more of a "wait, this looks a bit off" kind. Actually, if it was too strong, I think most people would expect it to be lit using LEDs, which I think would take away from the effect.
Thank you for checking out this Instructable. Have you checked out the video linked above? I hope you enjoyed both, and if you did please let me know by leaving a comment below and by sharing it with your friends.
And as always, remember to Be Inspired!
Step 11: Bonus: How I Ruined My Wand and What I Should Have Done Differently
It is really quite simple. Do not drop it.
Seriously, it is as easy as that. That, or "make sure that you get the glue evenly distributed over the whole surface. Which I thought I had, between adding a good drop and squeezing both faces together. Looking at the finished piece, though, there are some "air bubbles" - at least they look like that. I imagine for some reason the glue did not fill the space between the slices there. That might be due to a lack of pressure or slight curvature of the pieces.
Either way, it works fine still - up to the point where you hit something hard. Like the floor. While I managed to glue the bottom piece that came off during the making of this back on without misalignment, I did not manage that here, further up the wand. CA glue does not leave you much time to realign either. And I did not feel like sanding it again, which would have been a lot of work, especially getting that section to fit with the rest. So just don't drop it.
And again, remember to be Inspired!
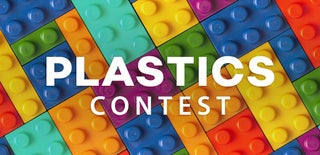
Participated in the
Plastics Contest