Introduction: Give Your Lighting a Hand !
Today I will share an unnecessary complicated (and somewhat expensive) way to make lamp! While lacking practicality, …Uhm…, at least the process of making the lamp was interesting to me! And I love the resulting product !
The resulting lamp is about 50cm high
Supplies
Materials:
- 5V power supply (for the time being I am using a 5V, 10W, USB charger)
- Melamine wood 160cmx30cm (thickness to chose in regard to the length of your screws or vice versa)
- Screws (I chose screws 4mm in diameter and 30mm & 16mm in length with 16mm melamine)
- LED (<=5V for my use but depends on the brightness you want). I used those
- 1kg of alginate molding powder
- USB cable (only necessary if, like me, you are using a USB charger to power your LED)
- A switch (to turn the lamp on and off)
- Tubing, 8mm in diameter (or smaller) by 10cm
- 40cm of 28AWG wire (white if possible)
- Nice looking electrical wire
- Plaster (enough to fill the mold and then some)
- Water for the alginate and the plaster (maybe for you too if you are thirsty)
- Solder
- superglue
- piano hinge
Tools:
- Circular saw (not strictly necessary but a huge time saver)
- Wood file (to rework the plaster model)
- Screwdriver
- Soldering iron
Step 1: Making the Mold
The very first step in the process is building the mold, I chose to cast my forearm, but you can use any object you want, keep in mind that the geometry of the object as to be such that it is “demoldable” meaning no overhang parts which would lead to have to make the mold in even more parts. Note that small overhang are permissible given the elasticity of the alginate mold.
My choice to use alginate over other popular solutions such as silicon is purely due to curiosity toward the medium. In retrospect, I would say that alginate is not really easy to use (then again, I never tried silicon or any other solution). I had to break the mold to get to the part but, you know, that is ok ‘cause only shooting stars…
To actually make the mold, I first needed to build a box for it. I built mine out of melamine as I needed a water-resistant material. The mold is two parts so the case also has to be. I divided the case into a top and bottom part connected by a hinge and lock shut during the casting of the mold.
The seams between the different sides of the box are sealed with silicon and the opening for my forearm is naturally sealed with my skin (the hole has to be tight enough to form a seal but not so tight that it pinches the skin too uncomfortably)
The object to cast (my forearm) is not so boxy meaning that by designing the mold box in this generic shape, there is a lot of lost space that would be filled with alginate and useless, in this part, I used some water-proof volumes (cups & color-full reusable ice cubes) adding them one at a time making sure at every turn that my forearm and hand still had extra space.
Step 2: Casting the Mold
The casting of the mold was definitely the most challenging and messy part of the process, I knew that I would only have one hand to pour the alginate in the box but still. Having to carry the alginate one hand without tipping everything outside the bax mas not as easy as initially thought, but somehow, it sort of worked. By removing my hand between the two pours (between top and bottom part) I did damaged the bottom part that yield a very poor resulting casting (it all worked in the end as plaster is really forgiving as it is extremely easy to rework)
There is nothing much to add for the bottom part, for the top part, the only thing I had to remember was to press my index finger onto the tube that will later be uses as structural reinforcement of said finger (as well as serving as a channel for the wire going up the light bulb )
Step 3: Demolding of the Mold
The demolding was, weirdly enough, both easy and a little stressful, the top part of the mold was not really sticking to the side of the top box (that was an oversight on my part) but I managed to lift both the top box and the mold enough so as to being able to remove my hand out of the box.
Step 4: Casting of the Lamp
You can cast your model in whatever material you want, plaster though has lots of qualities, beyond the cheapness of the material itself, the main advantage of the plaster is the way its granularity plays with the light that will be placed later on right above it.
The very first step is to embed the wire and the index reinforcement in the mold, you also need to seal the tube in which the wire goes, for this purpose, I used some silicon that was left from the sealing of the mold box.
First, prepare a first small amount of very liquid plaster (for a mold of the size I end up using, maybe 25cl of extra liquid plaster) to get in every little details of the mold, you can spin and lightly shake the mold as you pour this first plaster preparation. Especially if, like me, you have a lot of parts of the mold difficult for a thicker plaster get to. After pouring the liquid plaster, you can directly pour the thicker (read the instruction on your plaster bag) plaster to fill the mold to its brim making sure that the wire stay out of the opening (but without pulling on it too much of course). In addition, it is a little better to use white insulated electrical wire as it will not show as much if it close to the walls of your part (disregard this tip if you intend on painting the final part).
You need to wait at least 12h for the plaster to cure inside the mold at which point the part will still be very fragile and you need to take a lot of precautions during the demolding stage. I thought that maybe the demolding would be non-destructive of the mold but it was not, I had to deconstruct the box and cut the alginate with a utility knife little by little as to not destroy the fragile fingers.
The part right out of the mold is pretty rough, but is easily reworkable with the help of some sand paper and even wood file for the parts were the plaster accumulated the most, It took less than half and hour to get to the final roughness I wanted (keeping a somewhat still rough surface and inperfections makes for very interesting looking shadows with the lamp right above). Once you get your part to the roughness you want, it time to get to the final part, the electrical part !
Step 5: Electrical Work
This part is probably the easiest of them all, no time crunch, no delicate work. However it is NOT the time NOT to pay attention (sorry for the double negative, I just needed your attention)! Electrical work does contain risks (even though we are working with low-voltage here) and we will be working with a soldering iron, processed only if you know what your are doing and/or under supervision.
First, make things easy on yourself and get a plastic lightbulb (or better a used plastic led lightbulb) as we will use the bulb only for its aesthetic quality. You can first open the bulb (in nondestructive manner) and remove the LED and power conversion circuit. You can now install your own LEDs.
Quick note on the LED you are adding: You need to consider that this lamp that we are building will not have a lampshade, it is not a good idea to put in high powered LEDs, in addition, using power LED, you will not know for sure that the casing of the lightbulb was dimensioned for passively dissipate the amount of heat you would generate, it is much safer to use the lamp with low power LEDs (or like me, under power high power LED 😉 )
In the bulb part of the light bulb, drill a 8mm hole (or a hole matching the tube you put in the index finger).
You can now put the bulb part of the lightbulb over the tube in the finger, solder the wires embedded in the forearm to your LED and then close the lightbulb with some glue, this end of the lamp is finished !
In the on other end of the lamp, drill out a cavity in which you will have the space to solder and house you wire coming from the low-voltage power supply and on the side of your lamp, drill a hole to the cavity you just made to run in the wire coming from the low-voltage power supply. You can now solder said wire to the lamp-embedded wire (careful to respect the polarity). You can now add the switch on the power supply wire (I prefer to have it close to the lamp 20-30cm). And voilà !
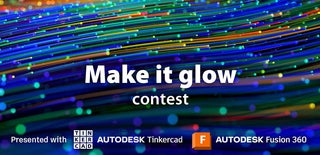
Participated in the
Make it Glow Contest