Introduction: Gravity Knife USB Case
My name is Donald Nguyen, and I am a student of Piedmont Hills High School enrolled in the CTE Pathway
For this project, I will remake a 3d printed case for my USB drive by improving upon its flaws. My current case has far too much play in its action, allowing for unwanted movement that could cause damage to the drive. To solve this issue, I will incorporate a smaller, finer pin to reduce the amount of play in the operation of the case and add a magnetic tensioning system to prevent the case from opening unintentionally.
Supplies
Machines Used:
Makerbot Replicator +
Hardware:
1x Disc Magnet (3mm diameter x 2mm height)
1x Metal Round Pin (0.06 inches in diameter)
Thin sheet metal (less than 0.03 inches in thickness.
Other Materials:
PLA Filament
Superglue
Ceamere C3 16GB USB
Tools Used:
File
Hacksaw
Sandpaper
Wire Cutters
Sharpie
Calipers
Metal Shears
Step 1: Designing the Case in AutoCad
To begin this project, I first designed the case that the USB would sit in. The design is based on the Reate EXO Gravity Knife. The USB sits within a housing component with a slot cut out matching the hole in the USB. A pin is inserted through the hole of the USB and the slot in the housing component. The length of the slot determines the distance the USB can travel. To lock the USB into an open and closed position, an outer jacket is made with cutouts matching the pin. The outer jacket can pivot freely while attached to the housing component through the use of another pin. When the outer jacket swings outwards from the housing component, the USB can move freely, and when the outer jacket closes, the USB is locked open or closed. To keep the outer jacket closed and prevent the USB from moving unintentionally, a recess is cut into the housing component to allow for a magnet to be seated, and a shallower recess is cut into the outer jacket to allow for a small sheet of metal. In the closed position, the magnet will pull on the sheet and the outer jacket, keeping the case closed.
Step 2: Printing the Case
Once the case has been designed, there are three parts to print out: the pin, the outer jacket, and the housing component. I exported the Fusion 360 files as STL files, and then uploaded them to the Makerbot slicer software before printing the case on the Makerbot Replicator +. After the case pieces were printed, I removed any support material with thin wire cutters. Attached below are the Fusion 360 Files.
https://students20628.autodesk360.com/g/shares/SHd38bfQT1fb47330c99cb891ef4c4344790
https://students20628.autodesk360.com/g/shares/SHd38bfQT1fb47330c99751ef7b5d9feb9c0
https://students20628.autodesk360.com/g/shares/SHd38bfQT1fb47330c9908b3ab6ad751f26e
Step 3: Sheet Metal Preparations
Cut out a flat section of the sheet metal using the shears, then color in a section of it with Sharpie or layout fluid. Using a pair of calipers, scribe in a square roughly 0.3 by 0.3 inches. Use the shears to then carefully cut out the square, making sure to cut on the outside of your markings. The square is meant to fit into the recess of the outer jacket, so remove material as needed until the square just fits into the recess. Once you are satisfied with the fit, squeeze a small amount of super glue into the recess and place the square in.
Step 4: Pin Preparations
Take the metal round pin and slot it through the small hole of the outer jacket until it extends the jacket's full length. Mark the length of the pin with a Sharpie, then use a saw to roughly cut it to the desired length. If the pin is too long, use a file to remove material until it has reached the desired size.
Step 5: Assembly Preparations
Before the case is fully assembled, take the small disc magnet and place it in the recess of the housing component. After ensuring the fit of the magnet, remove the magnet, squeeze a small amount of superglue into the recess, then place the magnet back into the recess.
Step 6: Assembly
To assemble the case, first place the USB within the housing component, then push the plastic pin through the hole of the USB drive. Next place the housing component into the outer jacket so that the small holes of each piece are aligned, then push the small metal pin through. The case is now assembled.
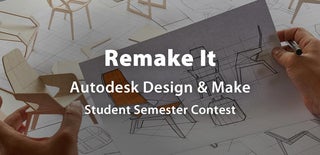
Finalist in the
Remake It - Autodesk Design & Make - Student Contest