Introduction: The Flying Gyro Stabilized VTOL Cardboard Box
The Gyro Stabilized Vertical Takeoff and Landing Box is the byproduct of several attempts to create an electric aircraft capable of taking off and landing vertically and controllably in all axes. Many organizations have accomplished this feat using conventional rockets however, it would be nice to see a future with completely emission free transport. This instructable is by no means a final product or close to it; It is just my go at this problem. I would like to preface this instructable with the fact that precise measurements are not needed however they will help by reducing the amount of trial and error necessary. It's the concept that I will convey truly rather than dimensions in order to not constrain creativity or variability.
The idea would be for this craft to fly in Earth's atmosphere then separate for a propellant driven rocket to carry the payload. From what I've read, The lower atmosphere is very thick and viscous compared to the upper atmosphere. Therefore, propellant driven rockets are more efficient at higher altitudes. The problem with this is that there will also be less air for the fan to push at higher altitudes as well. There's an equilibrium altitude that needs to be established for this system to work.
Step 1: The Problem
This VTOL box is meant to be a test article for the potential advancement of electric ducted fan rockets. Yes, battery technology is limited however, it's important to always consider alternate forms of access to space or general transport within our own atmosphere. Due to the flexibility of this instructable, no exact dimensions are necessary. Essentially, make sure control surfaces and frames are symmetrical.
Flight Video Links:
Trial 1: Link
Trial 2: Link
Trial 3: Link
Step 2: The Materials
To make this hovercraft, you will need a/an:
1. 18A Brushless ESC(Electronic Speed Control) (banana connectors/heat sink tubing may be needed) (2)
2. 8.4 gram Servo (3)
3. 37gram 1300 KV Motor (2)
4. Lithium Polymer Battery: 3 Cells
5. radio reciever/ transmitter
6. ~1cm wooden cylinder/rod (2)
7. 8*4 8*3.8 ( 8in diameter propeller, 4 in pitch propeller) counter-rotating props are required
8. cardboard box
9. Much duct tape
10. hot glue
11. 3-axis gyro (http://www.hobbyking.com/hobbyking/store/__38543__OrangeRX_RX3S_3_Axis_Flight_Stabilizer_V2_V2_1_firmware_V_tail_Delta_AUX_.html)
12. scissors/X-Acto cutting blade
13. clevices, control rods of some kind.
14. Zip ties
15. rubber bands
16. receiver wire y-connector
17. servo wire extensions
18. battery to esc y-connector
19. Carbon fiber rod (2)
The ESC, servo, and motor can be obtained from this link directly. Depending on stock, the battery, receiver and transmitter may be available from this site also.http://www.hobbypartz.com/60p-dy-1006.html
Step 3: Methods to Attain VTOL Trial 1
The first attempt at VTOL was most simple. 1 motor, 1 ESC, 2 servos for roll and pitch and 4 arms to increase the moment of inertia to counteract the propeller torque. The issue was that the 4 arms greatly added to the craft's weight thus reducing flight time and altitude. To create this version, refer to the materials list. All parts are swappable in accordance to my previous instructable as well.
Step 4: Methods to Attain VTOL Trial 2
In trial 2, I created a gimbal using 4 servos, control rods, a foam ball, zip ties, the motor set-up and a 3-axis gyro. A close up view of the gyro set up is seen in the 2 images. Two pairs of servos are mixed with each other so that they move harmoniously. This mix is done in the computer radio. Due to the nature of the gyro and the aircraft, it will correct for instability in the roll and pitch direction however any input by the user will supersede the gyro's inputs to the servos. Setting up the gyro is not difficult. There are several internet resources to do so. I was unable to find a way to counteract the propeller torque without using arms at this time.
Step 5: Methods to Attain VTOL Trial 3
The advancement is that there are no arms necessary to counteract torque. This is because the propellers are counter-rotating thus cancelling out any torque effects. There is a control surface for controlling yaw that is regulated by the gyro. With the VTOL Box, it is necessary to cut holes into the box itself to reduce weight. I used the mouth of a sippy cup as a stencil to cut out the 3.5 inch diameter circles with an exacto knife. The box is 9 inches by 9 inches by 14 inches. The roll and pitch control surfaces are about 1 inch in width and 7 inches in length. The yaw control surface is 2-3 inches in width and 5 inches in length. A carbon fiber rod is used to strengthen the piece of cardboard directly above the pitch control surface. Another carbon fiber rod us used to secure the yaw control surface. It is critical that the motor mount is secure. I used zip ties, got glue, a wooden dowel, a screw and rubber bands. I'm sure more secure alternatives exist. Please comment on those alternatives.
Step 6: Conclusion/Updates
This is my take at Vertical Takeoff and Landing (VTOL or VTVL). I shall continue this effort however, I need to gain more technical knowledge to improve materials and building processes which I'm in the process of attaining. The vertical takeoff and landing box addresses propeller torque issues and improves upon stability and flight time in comparison to previous trials. If any more dimensions are necessary that I have overlooked, please comment and I will provide them. Thank you Instructables for allowing the world-wide sharing of ideas!
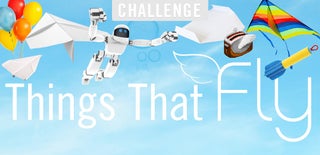
Runner Up in the
Things That Fly Challenge

Second Prize in the
Move It
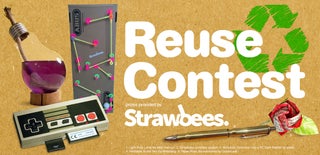
Participated in the
Reuse Contest