Introduction: Gyroman Walking Gyroscope
This amazingly clever walking toy was invented more than 30 years ago by my friend John Jameson. It consists of two feet that are geared to a spinning flywheel, so that as the flywheel spins, the feet stomp up and down. When one foot goes down, instead of tipping over, the gyroscopic action causes the body to lift up and then precess around the planted foot. When the other foot comes down, the body lifts again but it precesses in the opposite direction, and voila, it walks!
John's original version (3rd photo) was machined, but this version I designed is nearly completely 3D printable. With the addition of some ball bearings, steel rod, screws, o-rings, and also 104 pennies for the flywheel, you can create your very own copy. The overall cost is less than $10.
Step 1: Gather Your Parts and Files for 3D Printing
There are 12 separate STL part files for the Gyroman that you will need to download from the links below. You will also need the following mechanical components (I've included part numbers for ordering from http://mcmaster.com/ where applicable):
- 20 4-40 x 3/8" pan head screws (McMaster 90272A108)
- 1 4-40 x 5/8" pan head screw
- 1 4-40 set screw
- 10 3mm bore, 10mm OD, 4mm thick ball bearings (623ZZ) ......(I purchased 10 for $2.15 at http://www.ebay.com/itm/161255478926)
- 5 #4 washer, 0.22 OD x 0.031 thick (McMaster 90295A359)
- 1 3mm rod x 1.9" long (McMaster 5544T222)
- 1 3mm rod x 2.5" long (McMaster 5544T222)
- 4 O-rings 1/16" thick x 1 7/8 OD (McMaster 9452K118)
- 3ft 30# test Spectra braided fishing lines
- 104 pennies
- superglue, phillips screwdriver, 0.050" hex wrench
You should also download the file gyroman3d.pdf. This is a 3D PDF file that you can rotate in 3D, hide components or make them transparent, and is a great tool for examining how the Gyroman goes together.
3D print the number of parts indicated in the photo. Use 0.2mm layers, 3 perimeter shells, and 20% infill. To make sure that the parts print flat, it is best to use a printer with a heated bed. If you don't have a heated bed, then print the parts with a raft to reduce warping.
Attachments
Step 2: Install Ball Bearings
Start the assembly by pressing the ball bearings into the side pieces (one in the top hole, one in the center hole), the feet (1 each), and in the eccentric (2 stacked on top of each other). It is important to not let the bearings get cocked when pressing them in. Using a flat jawed vise works pretty well. You can also place a small scrap of wood over the bearing and tap it gently into place with a hammer.
Ideally, the bearings will press into the holes rather firmly. However, if they are loose, you can use a tiny amount of superglue in the bearing holes to help hold them in place. Be very careful, though, to not let any glue get into the bearings.
Step 3: Assemble the Legs & Feet
Two of the o-rings go on the feet to make them a little bit grippy. Put a dot of superglue on the rim of the foot and glue the o-ring down at one spot, then pull the o-ring into place after the glue has set. Add a couple more dots of superglue around the perimeter to keep the o-ring from slipping off.
Next, use the short 4-40 screws to assemble the leg sub-assembly as shown. Before screwing each foot to the bottom of a leg, make sure to put a washer over the screw. When assembling the bars, tighten the screws down all the way and then back off about 1/4 turn. The feet should be able to pivot up and down smoothly, but without a lot of slop.
Finally, insert the long 4-40 screw into the top of the link.
Step 4: Assemble Flywheel & Pulley
Stack 13 pennies into each pocket on the flywheel. It is best to use new pennies because old pennies (pre-1981) have a different weight. Align the retaining ring over the flywheel so that the bumps on one side of the ring align with the penny stacks. Snap the retaining ring into place over the pennies. To keep the pennies from vibrating while spinning, a few drops of superglue applied to each stack will lock them in place.
Now take the long shaft and tap it through the hole in the flywheel. One end of the shaft should stick out from the side shown by exactly the thickness of 1 washer plus 1 ball bearing. Lock the shaft in place with the 4-40 set screw. Take care not to strip the set screw threads. If you do, remove the set screw, add a drop of superglue and re-insert the set screw.
Push the shorter shaft into the pulley as shown. The shaft should stick out by the thickness of one ball bearing. Press the collar onto the other end of the shaft, and again, the shaft should stick out by the thickness of one ball bearing.
Step 5: Assemble the Body
Place a washer over the short end of the shaft on the flywheel and then insert that end of the shaft into the center bearing on one of the sides. Put an o-ring over the other end of the shaft, and then put the pulley shaft through that o-ring and into the other bearing. Put a second o-ring over the other side of the pulley as shown. Put a washer on the flywheel shaft and then slide the eccentric onto the shaft on top of the o-ring. Then put the last washer on the end of the long shaft over the eccentric. Place the other side on top, sliding the two shafts into the bearings.
Use 2 of the short 4-40 screws to screw the sides together as shown. Flip the whole thing over and use 2 more screws in the other side. Use 4 more screws to attach the leg assembly to the body (2 on each side). Use the set of holes directly under the flywheel. Again,. tighten these screws down all the way and then back off about 1/4 turn so that the feet pivot up and down smoothly.
Finally, tap the hook piece onto the end of the shaft as shown.
Step 6: Adjust the O-rings
Pull the first o-ring up over the pulley as shown. It should also be sitting in the groove on the side of the flywheel.
Take the second o-ring and hook it over the little nub sticking out of the eccentric. Now rotate the eccentric so that the o-ring is pulled up into the groove in the perimeter. This will take a bit of work because the o-ring gets stretched pretty far, and it also wants to jam up between the sides of the pulley and the eccentric. It should look like the last photo when both o-rings are seated properly.
Step 7: Install the Eccentric Bearings
First, make sure that the end of long screw in the top of the link is just flush with the side of the link. Insert a ball bearing into the groove in the eccentric. Now flip the body upside-down so that the bearing drops into the slot in the side. Screw the long screw in a little until it just enters the bore of the bearing. Insert a second bearing into the slot in the eccentric and align it under the first bearing. Screw the screw in some more until it enters the bore of the second bearing. Keep screwing the screw until it hits the surface of the eccentric, and then back off by a one or two full turns. You want to make sure the end of the screw does not rub on the eccentric during operation.
Step 8: Let'er Rip!
Tie a loop in each end of the fishing line. Thread one of these loops through the pull-ring as shown. (Caution:always use the pull-ring to pull on the fishing line - pulling on the line with your bare hands can cut your fingers!) Hook the other end of the fishing line over the hook as shown, and wrap the line to the inside of the little nub. Use your finger on the pulley to wind the fishing line up onto the shaft.
Now you are ready to go! Hold the body in one hand, level to the ground, and pull the string with a long, steady stroke. Without tilting the body, place your Gyroman on the ground and let him walk away.
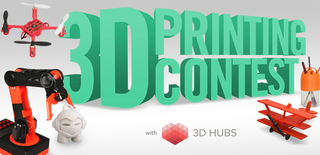
Grand Prize in the
3D Printing Contest