Introduction: HOW TO MAKE a LEATHER JACKET OUT OF SCRAPS
RAGS TO RICHES
This project is heavily based on the idea of conservation. What could I make with only things I already had in the house? Items used to fabricate this jacket have been scraps of leather I had saved up over the years, some remnant cloth, and a used YKK zipper. The rivets were probably the only items used that weren't given a second life.
SEWING MACHINES
There's a misconception that you need to be rich to afford equipment that will allow you to make beautiful luxury goods. It's not necessarily true, but specialized machines do give you better results. However, you can get away with sewing lightweight leathers on your average home sewing machine. There are some long term cons in doing so, but if it's a one time project or you're just testing the waters, use what you've got. I started off with a $200 Kenmore sewing machine then went to a Singer Heavy Duty ($230). And for the people who still don't believe me, everything on my fashion Instagram page: @jessica.barter has been sewn on the Singer machine. I'm not saying the Singer Heavy Duty was an amazing machine because it wasn't. It broke 4 times in a short span of 5-6 years, but I'm also very aggressive with my tools. Anyways, what I'm trying to say is you can still get away with making a couple of intricate pieces before the timing on your machine seizes. I've upgraded to a JUKI Exceed HZL-F600 ($1049) since. Pricier, but more convenient. You don't need fancy tools, just a vision, and passion.
It's important to note, that you'll need an open-toed walking foot attachment to make running the leather through easier on home sewing machines. Teflon feet don't work as well.
Step 1: ASSESSING YOUR LEATHER SUPPLY
If you're making your jacket out of full skins, then you don't have to worry about this part. For the people who want to put their leather scraps to good use, this is the part where you get a good gauge of how large your pattern pieces can get in the drafting phase. Start sorting them into different piles by size and texture.
Step 2: DESIGN
I designed the jacket to have several seams because of the scrap sizes I had. Think of it as a puzzle. Many small pieces put together to make the overall picture.
Put your ideas down on paper or digitally. If you're going to design with versioning, doing it digitally is easier because you can make changes quickly. I generally do my comps in Photoshop, but this time I felt like I had a good idea of what I wanted to make. The level of finish on your drawing is based on the purpose of your project. If it's for fun, they can look like poop and it's all good, as long as it makes sense to you. If it's for work, I'd suggest some more refinement.
Step 3: PATTERN MAKING
This step is one of the key components to having a successful project. It's a meticulous task, but if you take the time to check your work, it'll pay off in the sewing process.
STEP 1:
Start with your basic block. If you don't have one or are new to patterning, take a basic well-fitted shirt that doesn't stretch and use it as a template. You're going to transfer the different pieces that comprise your shirt onto paper. For beginners, it's easier to deconstruct the shirt, so there's no guesswork. For more seasoned sewers, you can use a fabric weight and a tracing wheel to transfer the basic block over.
STEP 2:
Draw your cut lines onto the block. I like keeping a blueprint of the design, so I trace the pattern pieces onto a separate sheet of paper and add on the seam allowance. This method takes longer but keeps you more organized. You always have something to refer back to, in case you lose a pattern piece or forget to label/notch a piece. If you're in a hurry or this is a one-time use project, feel free to just cut the pieces out directly and tape additional paper onto the borders for seam allowance. DON'T FORGET TO LABEL YOUR PATTERN PIECES.
A general rule is 1/2" all around and 1/4" on inclosed seams like necklines and cuffs. Those guidelines can change based on your design or if you're from a different country.
STEP 3:
True up your patterns. Truing up your patterns or walking them is the process of aligning pieces that will be sewn together to check if they will sew together correctly. It allows you to see if you have an excess length on one pattern piece or not. If you do, then you're going to have to correct it, either by increasing the length on the opposing pattern piece or by finding the difference between the two. During this part, you also want to notch your pattern pieces. Notching is the act of putting visual registration marks on your pattern piece, so when you go to sewing it, you have indicators to align the seams. When you're done, it should look something like the picture with all the pattern pieces laid out on the floor.
Step 4: CUTTING LEATHER & FUR
For larger basic pattern shapes, put a fabric weight down on the pattern pieces backside and cut it out with a rotary blade. If it's a more intricate abstract shape, trace the pattern on with a sharpie and use cutting shears to cut the piece out.
There are different methods on how to cut out leather but this method works best for me. You're welcome to cut leather out however you want. One very important note is to have sharp blades. They should slice through the hide like butter.
Step 5: LEATHER & FUR PREP WORK
FUR
I'm not familiar with how they prep fur for manufacturing, but this is what I found works. After you've cut out your fur piece, use a pair of hair clippers to shave off the seam allowance. By eliminating this bulk, it will allow you to run it through a regular home sewing machine.
LEATHER
Lightweight skins are more ideal for home sewing machines. If you're using a medium weight, you want to skive some of the thickness off the areas where the seam allowance will be. This will help prevent bulk in the sewing process and ensure it runs through your machine.
For padding detail, cut some foam out slightly larger than your pattern piece without seam allowance. Glue it on with barge, then draw your design on with a pen and sew it.
Step 6: SEWING LEATHER PIECES TOGETHER
Here's where you take the smaller pieces and sew them together to make the larger piece, much like a puzzle. Leather is tricky to work with sometimes. For lightweight skins that don't stretch, I use these red quilting clips to hold the pieces together like you would with fabric and pins. For medium weight or light stretchy skins, glue the seams together with a thin coat of barge before running it through the sewing machine. If you don't glue the seams of softer stretchy leather, you'll end up with excess seam allowance on one side when you get to the end of your sewing path. Then you'll have to trim off the excess and hope everything still fits together correctly.
Step 7: SEWING AN INVISIBLE POCKET
I've only sewn welt pockets in the past and I thought an invisible pocket would be cool, so I made this part up. I drafted the pattern to have an inch seam allowance on the inside pocket so there'd be enough room to roll the leather seam on the inside.
STEP 1:
Sew the pocket at 1/2," then fold it over and topstitch down on the front side.
STEP 2:
Now fold the remaining 1/2" down and topstitch on the front like the first step.
STEP 3:
Attach the pockets on the opposing adjacent piece. you may need to hammer down bulky seams.
STEP 4:
Place corresponding pockets together and sew your 1/2" seam allowance along the perimeter of your pattern pieces. Overlock the pockets area to reinforce the seams because there's nothing more annoying than sticking your hands in your pockets only to find a hole. Areas with excessive use should be reinforced by overlocking. When you're done, it should closely resemble the last image.
Step 8: CUTTING PLAID FABRIC
Cutting patterned fabric is tricky. I personally try to avoid using patterned fabrics when possible because of alignment issues and fabric waste. I chose to use this plaid flannel because I had about a yard+ left over from a previous project and felt it'd be comfy for a baby.
STEP 1:
Make sure to square off on one end based on a horizontal line on your fabric. Jagged ends make it difficult to gauge alignment. Fold the fabric in half on the closest vertical line in the plaid.
STEP 2:
Try to match the same lines of the fabric to the folded adjacent side and pin. The fabric will shift around, so just get it as close as possible. Pin along the length of the fabric or the amount you think you'll end up using.
STEP 3:
Place your pattern pieces on the fabric. If they're pieces that will be sewn together, try to match the visual plaid pattern along the seam allowance. This way, when you're sewing the items together, the plaid pattern will flow into the next piece without a jarring disconnect. Then pin and cut it out.
Step 9: SEWING YOUR LINING
I chose to use spandex for the lining areas where the heavy knit appeared on the leather jacket so the elasticity of the top layer would be functional. If you only want the top knit layer to be superficial and not functional, you can skip the step of drafting and cutting out the spandex gussets. Just make the front & back bodice and sleeves one piece. Now assemble the pieces from your front bodice, back bodice, and sleeves. Remember to leave a large opening in one of the sleeve seams so you can turn your jacket later on.
You can also add branding or labeling detail in this step. I chose to gold foil my logo on a piece of leather. After you get a nice print, cut it to size, and sew it on your fabric.
Sew the side seams together, add the collar to the bodice, and attach the sleeves.
Step 10: ZIPPER ACTION
In most cases, you're going to have to adjust the length of your zipper to fit the jacket. I chose to use an old zipper that was taken out of another jacket, hence the gross glue marks and thread strands. Your zipper will probably look newer.
STEP 1:
Place your zipper next to the pattern piece it will be attached to. Make sure to exclude the seam allowance of the pattern piece. Mark the top of the zipper webbing where it bisects the sew line on the top pattern piece. Move the zipper pull below the lines you've just marked before you cut.
STEP 2:
Cut your zipper 1/2" above the mark. Make sure you don't run your blades through the metal teeth. This will damage your shears. Cut carefully between the teeth.
STEP 3:
Now use the nipper pliers to rip the metal teeth off the webbing above the marked line. The nipper pliers are the ones that look like a stumpy hammerhead shark. These pliers work best for removing zipper teeth. Other pliers work but aren't as efficient. For the end caps, cut as close to the edge of the caps as possible. Give it a nice wiggle or two and they should just fall out. Remove the remaining fabric strands that may have collected between the prongs.
STEP 4:
This part can be dangerous, so proceed with caution. You're going to have to open the clamped zipper ends. I like to place the zipper end on the awl tip and use a pair of flat nosed pliers to gradually widen the opening. Slowly add pressure while sliding down towards the base of the awl.
STEP 5:
Use the flat nose pliers to attach the zipper ends to the webbing. Placing the strip between the two prongs and add pressure.
STEP 6:
Run a lighter flame along the edge of the webbing until you can see it melt slightly. This will keep the webbing from fraying. Avoid holding the flame to the edge for too long or you'll end up with a plastic blob and very hot zipper teeth.
STEP 7:
Sew the zipper onto your jacket.
Step 11: JACKET & LINING
YAH! 80% there. Here's where you can start putting your hardware on like snaps or rivets. Punch a hole where you want the item to go, place the male into the female rivet/ snap, and use the appropriate setters to hammer in place. If you want the rivets to show up in both the top and lining layer, you can do this step later.
Step 12: THE UNION
I normally wing this part, but I decided to learn how to properly attach the lining for a change. I must say, I like the results, but you'll break a sweat if you don't leave a wide enough opening in the sleeve lining.
I watched a couple of Youtube tutorials prior to doing this but found it hard to follow along visually when they were explaining this process, so hopefully, I was able to simplify it for you.
STEP 1:
Think of the pieces like a couple. The leather shell represents the male and the lining, the female. Picture the man leaning forward to embrace the woman. You'll be attaching the outer perimeter of the leather shell to the lining. Use some quilting clips to get the alignment correct before gluing the seams. Then sew. When you're done sewing, it should look like photos 3.
STEP 2:
In this step, picture the couples heads against one another and holding hands from up above (photo 4). You'll be sewing the cuffs together. Clamp, glue, and sew.
STEP 3:
In the sheets. Here's where they become intertwined in one another. This step you'll have to start pulling the right side of the jacket through the opening you left in the sleeve lining. Very awkward maneuvers, just like the first time. :P
STEP 4:
This part is very much like childbirth, you get sweaty, tired, and frustrated, but once that baby pops out, it makes everything worth it. Keep pulling until you've turned the whole jacket outside in.
Step 13: THE FINISHES
Hard parts are now over, and it's icing on the cake from here on out. Topstitch desired areas, trim thread strands, and close the lining seam opening by either hand or machine sewing it.
Step 14: GO BE BADA$$
Put that baby on and go explore.
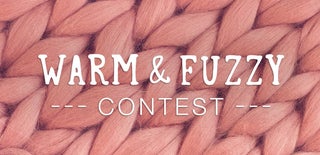
Participated in the
Warm and Fuzzy Contest