Introduction: Halloween Condiment Set
At Halloween time we display the Pumpkins and with the inner flesh make soup, pies and other food items.
As a food item you will invariable add a condiment in the form of salt, pepper or some other savoury or spice.
It therefore seemed appropriate to create a Pumpkin themed condiment set for salt and pepper as a minimum.
The condiment set was designed using BlocksCAD then 3D printed.
Supplies
3D Printer
Filament (Food Safe) - Orange, Green
Food Safe Finish
Flexible Filament (TPU) or Natural/Synthetic Cork
2 part resin - Black
BlocksCAD
Cura
Long nose pliers
Cutters
Step 1: Design
Each dispenser will be made up of only three elements spout, container and stopper which can all be 3D printed and requiring no supports, simplifying somewhat post processing.
There will be two design variants, one for salt and the other for pepper.
These would be differentiated with both a facial and a spout design.
The facial designs will be included as part of the container giving the impression of being carved into the outer surface. (The only holes needed are for the spout and stopper). This will enable a resin inlay to be applied to highlight the facial features.
The spout would represent the stalk on a real Pumpkin.
In addition the bottom would have provision for a stopper.
The main facial variations would be with the eyes and the spouts with different hole counts.
The main container is based around a miniature Pumpkin variety, tending to have a more flattened top and bottom more reminiscent of a small wheel rather than a ball.
Step 2: Pumpkin CAD - Part 1
BlocksCAD only has primitive shapes and as a result we need to create the Pumpkin shape.
Based on the use of a sphere, this gives both a rounded shape and the ridges in the surface.
This is accomplished by an iterative loop which plots the sphere at a different angle around the circumference of a circle from 0 to 360 degrees based on the specified radius.
A cross section is included to illustrate the position of the spheres and intersection were the ridges are formed.
Had the code used the polar co-ordinate system the position around the circumference to position the sphere could have been calculated from the radius and angle from the centre of the circle.
However, as the code is using the rectangular (Cartesian), co-ordinate system its required to specify the x and y position.
We can relate the x, y position to the position on the circumference of our circle by using Sine and Cosine functions.
Using a unit circle with radius of one the Sine and Cosine at each angle is shown, this is multiplied by the radius of our circle to provide our co-ordinates.
The number of ridges is related to the size of the sphere and the number of steps around our circle circumference.
A step angle of 20 degrees (18 sections), was chosen.
However, this part of the process creates a solid Pumpkin which needs now to be hollowed out.
Step 3: Pumpkin CAD - Part 2
The process of hollowing out the Pumpkin requires the use of the difference function which will subtract one object from another.
This is accomplished by plotting a smaller version of the original shape inside the original. In this case the radius is 4mm smaller.
Step 4: Pumpkin CAD - Part 3
At this stage the object still appears to be solid.
In order to open up the Pumpkin the holes for the spout and the stopper need creating.
Again using the difference object a cylinder with radius 10mm and the same height as the sphere is placed in the centre of the Pumpkin object.
Applying the facial expressions is next.
Step 5: Pumpkin CAD - Part 4
The objects used to create the face are placed in such a way as to leave a depressing but not to create an excessive overhang that would create a void in the outer shell.
The nose is a triangle subtracted from the Pumpkin object.
However, the triangle is not a basic shape and is created from a cylinder using the Side transform which is set to 3.
Next we add the eyes created using the torus object in conjunction with the taper object to elongate the eye for a more sinister look.
To add symmetry include the rotate object and apply 180 degree on the X axis of the eye on the left.
The mouth is made up of five diamonds (there being no default diamond object this made up of a cylinder applying the Side object which is set to 4), applied in an iterative loop.
These facial elements are subtracted using the difference object to create a depression in the Pumpkin surface and coloured blue for contrast.
The main pumpkin design process is complete but two are required.
Therefore, a second facial variant to required were the differentiation is in the eyes.
Step 6: Its in the Eyes
A minor code change to the eye code enables a change in the existing eyes.
Step 7: Spouts
Two spouts are required one for salt and one for pepper.
Both spouts have the same basic design shape differentiated with holes.
The basic design element consists of a main long cone a lower wider code, edged with a torus and standing on a cylinder.
For the salt the basic element is used in conjunction with the difference object and a central cylinder for a single hole.
For the pepper the same basic element is again used with the difference object and the addition of an iterative loop which places a cylinder object at 60 degree intervals (6 holes), in a circle.
Step 8: Stoppers
Stoppers are created for the base to enable filling.
These are simply cylinders with a torus.
The torus to create a lip which will hold the stopper in place.
A wide thin cylinder to allow the stopper to have a smooth transition with the pumpkin and the facilitate ease of removal for filling.
Step 9: Preparation for 3D Printing
The design process is now complete and all that remains is to generate the STL files (although other file types are available), to enable 3d printing.
Prior to 3D printing the STL files require conversion to GCODE using an appropriate splicing application.
In this instance Cura is used although other applications to accomplish the task exist.
Five STL files are created 2 spouts, 2 pumpkins and a stopper.
The same slicing details were applied to all but one element and this was the stopper.
The difference is in the base adhesion and infill density.
As the stopper is to be printed in TPU which is a flexible filament and does not delaminate at the layer edges no base support is required.
If you do inadvertently print the stopper with a brim you can use a scalpel to carefully cut the brim off.
Slicing details.
Layer Height: 0.15mm
Infill Pattern: Tri-Hexagon
Infill Density: 25% (80% for the stopper)
Build Plate Adhesion: Brim (For all but the stoppers).
No supports are required.
The STL files are available here: Pumpkin Condiment Set – YouMagine 🏠
Step 10: Filament and Food Safety
As this was to be a food related project a food safe filament seemed appropriate.
However, TPU used for the stopper is not considered food safe, therefore as an alternative a natural or synthetic cork could be cut to fit.
Though, being a seasonal item it could be considered one use and/or consigned to decoration subject to the filament used and the printing process.
Even though dry contents will be used although intermittently they will be handled and as such will require cleaning at some point.
Washing has its own issues, it can warp the model or open any gaps which can degrade the model if the water is to hot.
Hand washing with soap and warm water being more appropriate and allow to air dry.
Concerns with the 3D printing process is that the object will be created using layers which contain gaps and ridges that can harbour bacteria and chemicals in the filament may affect the contents.
Therefore, rather than leaving the model as printed, coating the model is highly recommended particularly on the inside with food safe silicone, epoxy resin or polyurethane prior to use.
Further details regarding 3D printing and food safety can be found at the following:3D Printing Food Safety: Make Food Safe 3D Filament Prints - 3D Insider (No affiliation and you may have a your own sources to refer to.)
Step 11: 3D Printing
The two pumpkins could be printed separately or as a pair using an orange filament.
The pumpkins printed at 100% are 79mm x 79mm x 40mm and take ~6.63 hours each to print.
The two spouts would seem appropriate given the size to be printed together using a green filament.
The spouts printed at 100% are 24mm x 24mm x 25mm and take ~30 minutes for the salt and ~1 hour pepper to print.
If printing the stoppers these use TPU without build adhesion.
The stopper printed at 100% are 24mm x 24mm x 5mm and take ~10 minutes each to print.
Step 12: Post Processing
As with any 3D printing process some post processing will be required, be it removing the base adhesion or smoothing imperfections, this build is no exception.
Most of the work will be applied to the pumpkin to remove the stringers from the inside which can be removed with long nose pliers and cutters.
Step 13: Coatings
Prior to applying a resin inlay to the outer surface to highlight the facial elements first apply a coating to the inside.
This serves to fill in any gaps and crevices in the model to protect against bacterial build up and external transfer via any gaps and make it easier to clean.
Once the internal coating has dried its time to turn your attention to the outside.
As the resin inlay will be in a dark colour (in this case black), wicking into the model will show up around the area to be coloured unless this area is first given a clear coat which is allowed to dry.
Once the outer coat has dried the inlay to the facial elements can be applied.
Paint, nail varnish or resin can be applied to the facial elements using a fine paint brush or cocktail stick and allowed to dry before use.
Step 14: Assembly
Decide which pumpkin will be used for salt and which for pepper and push the appropriate spout into the top applying a twisting action while pushing will make the task easier and applying the reverse action for removal unless the spout is loose in the opening, in which case the application of little super glue should hold it in place.
However, applying glue will make the spout a permanent fixture.
If the spout is a snug fit it makes an alternative to filling from the bottom and allows access for cleaning from both ends.
The stopper fits flush into the bottom, fitting is easier if pushed in at an angle rather than trying to press it in directly.
To fill remove the stopper or the spout which ever is appropriate or possible.
Step 15: Finale
That's it we are all done on this project.
All that's left is to use it as a condiment set, decoration or both. The choice is yours.
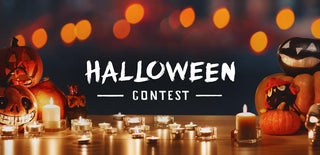
Participated in the
Halloween Contest