Introduction: Handmade Leather Wallet
Hi Everyone!
My name is Brandon and I have been doing leather work as a hobby for around 7 years and recently branded my work as Wanderer Leather Goods. Leather is such a great material to work with and I wanted to share some of the basics with you. It is such a versatile material and its great to be able to make random items that you can't just go and buy off the shelf somewhere, especially covers and cases for things. In this guide I will go over most of the basics and offer alternatives for some of the tools where I can. I also included an editable pdf pattern if you want to build along. I hope you enjoy and lets get making!
Supplies
Leather I'll go into this more in a minute.
Tools
- Cutting Tool (Make sure its sharp. Break off blade knives are great for this since you can snap off the end and have a fresh cutting edge. A dull blade is a dangerous blade, plus you have to work twice as hard.)
- Stitching Chisels or Stitching Wheel/Awl Marking and punching your stitch holes
- Mallet/Maul/Hammer for the stitching chisels
- Edge Slicker smoothing the edges
- Needle & Thread Nothing fancy but I like John James needles and Ritza thread
- Glue Weldwood glue is a great contact cement for leather and pretty inexpensive
- Metal Ruler cutting straight lines
- Wing Dividers Marking lines for cutting and stitching
Optional
- Bone Folder Breaking glue in the pockets
- Edge Finishing Compound Seiwa Tokonole or Gum Trag to make the edges smooth with the slicker
- Sandpaper To sand the edges prior to burnishing for a smoother finish
- Makers Mark or Design Stamps Brand the product or add designs
- Coin Rounding the corners
If you need help with supplies, companies like Weaver Leather Supply will have pretty much everything you need. Or if you get lucky and have a Tandy Leather near you, they are a great place when just starting out or picking up things same day
Step 1: Making a Pattern
There is an editable vector pdf pattern here for you to use if you want. This will make a 2 slot card wallet that will fit standard credit/debit cards and US paper currency folded in half. Get creative here if you want. Add outer pockets, or additional inner slots like in the last photo. You can use any pdf viewer to open and print the pattern at full size, set to US Letter size paper. It also has a test block to make sure your pattern is the correct size.
You will see a dotted line and a solid line in the pattern. This is so that once the parts are assembled, you can trim to the inner line, which is 5mm in from the solid line, and all the parts will have clean, flush edges. With out having the parts die cut, its pretty tough to get the edges exact so this just helps clean things up easily.
Once you have the pattern printed, it can be helpful to glue it to something like an old cereal box or other thin cardboard or card stock. This gives you a more ridged pattern for marking on the leather.
Attachments
Step 2: The Leather
When choosing the leather you want to use there are a ton of options out there. A vegetable tanned , or Veg-tan, leather is going to give you a good firmness and durability. 3-4oz (1.2-1.6mm) thick is a fairly standard weight for wallets. You can use thicker, but it will start to get bulky in your pocket, and thinner will start to get a bit flimsy unless you are planning to add additional pockets.
For this project I have chosen to go with red and grey pre dyed veg-tan leather to give a good contrast. I purchased this through Rocky Mountain Leather Supply. You can get small panels of almost any of their leathers which is perfect for small projects like this. You can also get most of the other supplies in this guide from them as well.
Step 3: Transfering the Pattern and Cutting It Out
Once you have the pattern cut out, choose which parts you want in which color. If your leather has marks or brands you can choose to incorporate them into the piece, which I love to do, or position the pattern around them for a cleaner look. If you are using plain veg-tan, just mark everything. You can use an awl or any similar object to transfer the pattern to the leather. You can also use a pen if you don't have anything else since all the edges will be getting trimmed in the next steps. These pieces had good square cuts already on them, so I used those to save a few cuts. For the pockets, I lined the second pockets marks up to the first to also save a few cuts. Planning out your cuts a little can help save some time and also cuts down on material waste.
Once you have your marks, use the ruler and your chosen cutting tool to trim everything out. As I said before, make sure what ever you are using is really sharp. Leather will dull blades really quickly which means you have to put more force into the cuts and they won't be as clean. Using more force can also lead to slipping and cutting into areas you don't want to or even yourself. Safety First!
Step 4: Makers Mark or Designs
This is a totally optional step. If you have a makers mark or want to do any designs on the leather, now is the time to do it. More times than I want to admit I have forgotten the makers mark until near the end which makes it a lot more difficult to do with out damaging the rest of the project. With veg-tan, you will want to dampen the leather a bit and let it soak in for a few minutes. This helps soften the leather to get a better impression that is deeper and crisper.
Step 5: The Inner Pockets
If you are just going to use the pattern as is, choose one long edge on each pocket and mark your 5mm line to trim to. Once it is trimmed you will want to finish the edge since it wont be accessible once everything is glued together. You can also leave the edge raw if you want. Its your project so make it how you want!
Since the leather I am using is pretty thin (3oz), I am going to skip edge beveling for this guide. I am using the Tokonole compound on the edges. You can also use Gum Tragacanth or even a little dab of water. Once the edges are coated, you will use the appropriate gap in your slicker. This is more about the friction than pressure. Rub back and forth quickly with a light to medium pressure. Keep the strokes around 3-4 inches to maintain the heat you are building up. This compresses the fibers and gives a nice smooth edge. You will start to hear it squeaking a bit when the edge is getting smooth.
Step 6: Assembly
Line your pockets up with the edges of your main body panel. Put the rough sides together for this. Make sure to put the burnished edges to the inside. Once you have them lined up, make a small mark on the rough side of of the main panel so you know where to apply the glue to.
When applying the glue, remember you will be cutting off 5mm all the way around so make sure to come in far enough that you will still have glue once you trim. Apply the glue around the rough side of the pieces, also be mindful of your burnished side. Let the glue sit on the leather for a few moments so it can get a bit tacky to the touch instead of wet. Line the edges up and press everything together.
Side note on glues. Some of them have pretty strong smells, especially if you are using leather craft glues like Barge cement. Make sure you are in a well ventilated area when using them.
Step 7: Final Trimming
Using your wing dividers, mark lines 5mm in from the edges all the way around and trim to the final size. You can leave the corners square if you like or you can use a coin or any other circular object to cut round corners. If you make multiple straight cuts around the coin, it will give you a rounded final shape instead of trying to curve the cut.
Note: The dime I used left a small indention in the leather from pressing down on it. A quick rub and flexing the leather back and forth a bit will usually get rid of any marks like that in pre dyed leather.
Step 8: Stitching Pt 1 - the Marking
Close up your wing dividers a little (I usually go 3.5-4mm) and mark around the edges of the pocket for your stitching line. This helps to keep everything nice and straight. You can also stitch all the way around if you prefer that look as well. Just use the outside and mark the whole perimeter.
Once the line is marked, place the project on a punching surface. In the photos, I am using a cheap poly cutting board with a piece of scrap leather. This will help to keep from damaging the tips of your chisels. Using your stitching chisels or wheel start your line with one stitch hole over the edge of the pocket. This helps to reinforce that corner which will be a stress point. Another tip is to punch the top and bottom edges to the corners first, then go down the middle. This way you can adjust the final few marks a bit if things don't line up perfectly.
If you are using the wheel marker, once everything is marked, you can pre punch all the holes with an awl keeping it at a consistent angle as you go to keep the stitching even.
Step 9: Stitching Pt 2 - Thread and Saddle Stitch
For this project, I went with .8 mm Ritza thread in space grey. Pull enough thread to go around your stitching line, then fold that over 4 to 5 times depending on the amount of stitch holes and the thickness of the leather. More holes and thicker leather will need more thread, or less holes and thinner leather will need less thread. 4x was enough for the stitch lines I had.
I always start stitch lines like this with a back stitch. This means you start a couple of holes in, go the the beginning of the line, then work your way around. This give another layer of strength to high stress point. I when three holes back to give two back stitches.
To start the saddle stitch, put one needle through and get them even with each other. Put one needle through the next hole and pull the thread most of the way through. Do this gently so you don't pull the threads out of center and end up with one side longer than the other. Put the second needle through the same hole on the opposite side, making sure not to go through the thread. If you do, pull the needle back out an try again. Pull out the slack on both side and tighten, then repeat on the next hole. I like to leave a little slack until I have both needles through and then pull both tight at the same time, this way I can tell if I went through the thread and can fix it easier.
The biggest thing to remember when saddle stitching is to make sure you follow the same pattern on each hole to that the threads will stay in a straight line. If you go left side first on one hole, then do right side first on the next hole, you will end up with a wavy looking stitch line at the end. This is a really basic idea of the saddle stitch, and whole guides could be done on the finer points and tricks.
Step 10: Stitching Pt 3 - Finishing
Once you reach the end, do another set of back stitches like you did at the beginning. Trim off the excess thread, leaving a few millimetres sticking up. Carefully use a lighter to melt the end of the thread and press it down to lock the end.
Make sure to not put the flame directly on the thread or the leather. Get it close and let the heat do the work. It should only take a couple of seconds to melt the thread enough.
Step 11: Burnishing and Finishing
Now that the stitching is done, you can take a bone folder or any thin, blunt object and run it along the inside of the pocket against the stitch line. This helps to break off any of the excess glue and fully open the pocket up.
Follow the same steps from earlier to burnish the edges all the way around. If you want a more rustic look, feel free to skip this step and leave the edge raw.
ALMOST DONE!
Step 12: Finished!
At this point if you are using a natural veg-tan or a leather you dyed you will want to put your finish coat of your choice on the leather. I really like Fiebings Aussie Compund for this. It softens the leather a bit and gives a small bit of water proofing. If you used a leather similar to what I did, then your done. Load that bad boy up and enjoy!
I hope you enjoyed this guide. If you need some help or advice don't hesitate to reach out an keep making!
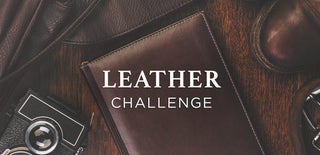
Participated in the
Leather Challenge