Introduction: Harry Potter Themed Mobile
When close friends of mine were putting together a nursery for their newly born baby girl, I wanted to use my skills to make something personal that would fit into their lives and interests. As huge Harry Potter fans in need of a mobile, this kind of seemed like a no brainer.
My top priority was safety of their baby. I did not want any toxic materials around, and most importantly I wanted to ensure that the mobile was solid and that no ornament would find its way into the crib. To achieve this, I used PLA for 3D printed parts filament as it is low-order, water-based paints, used solid wire to attach all ornaments together, and constructed a stand that was self-supporting. This was also because they were uncertain of where the crib would be, and I wanted to ensure that the mobile would fit any possible scenario.
Overall I think this project came together nicely, though there were some doubts along the way. I feared it would turn out to be a little creepy or dark in comparison to some of the plush Harry Potter mobiles out there. But in the end it fits perfectly into their nursery and the baby loves it, which is really all that matters.
Thanks for reading and happy making!
Step 1: The Design
I spent a long time trying to determine which direction to go as far as what ornaments to use and how to actually incorporate the theme of Harry Potter into the mobile. There were so many big ideas to pull from (quidditch, wands, brooms, Houses, or hats). But there's also so many little things to consider too (all the animals, the challenges, trinkets, and shops).
I decided to use flying keys from the first book/movie, Sorcerer's Stone, as the "filler" for the mobile. These keys would be in majority and fill the surrounding areas of the hanging ornaments. All the keys would be the same, gold, with white wings, except one larger and more worn brass key to match the plot.
In addition to the keys, I wanted three brooms (Harry, Ron, and Hermione), the sorting hat, a time turner, Hedwig, a snitch, the deathly hallows, and the four house crests. This doesn't cover everything of course, but some of the bigger times across the books and movies. I also did not create all of the ornaments, nice quality designs of some of these files were also available on thingiverse.
I also knew I had to have a wand in there, but a hanging wand didn't really look like much. I took four elder-wands and turned them into a cross-like shape to have all the other ornaments hang from. This all would hang down from the steel stand I created.
Step 2: 3D Printing the Ornaments
As previously mentioned, I used PLA filament to 3D print all of the ornaments. Originally, I planned to use different color filament, but these became a little too tedious to manage so everything was printed in white PLA, then painted in a later step.
For printing, I used my Lulzbot Mini with a 152 mm x 152 mm print bed for everything but the elder wand cross, that was printed on my Lulzbot TAZ6 with a 280 mm x 280 mm larger print bed. For each model, I printed everything in high detail (.15mm layer height) and high fill density (80%). If you're interested in learning more about Lulzbot 3D printers or general FDM printer functionality, check out this instructable.
Most of the models were single parts, except for the keys that had the wings, snitch which also had wings, and the crests which were all glued together with 2 part epoxy. I did not try printing holes for the connecting wires, instead drilled holes into each model after printing with a 1/16" drill bit and cordless hand drill.
As previously mentioned, I did not create all of the models from scratch. These models were pulled from thingiverse:
- Brooms
- Sorting Hat
- Time Turner
- Hedwig
- Deathly Hallows
- House Crests
- Note: for each crest, I printed two copies and glued them together to make them double-sided.
- Older and biggest key
See the attached files for the models I created. All of my designs were either made in Tinkercad or Onshape. For the elder wand cross, I started with this model and then manipulated it in Tinkercad to get it to be what I wanted. I have created tutorial videos on how to use Tinkercad here, and Onshape here. These videos were designed to be short and to the point, as well as to be catered to new learners for use in my middle-school classes. I also have a beginner CAD instructable as well with further support and tutorials within it.
Step 3: Fabricating the Stand
As previously mentioned, I had concerns about the structural integrity of this mobile and the stand design is a big factor in its performance. I did not like any of the clip-on plastic stands that were out there, nor did I love the idea of a wall mounted mobile. Because my friends weren't sure about positioning or even the type of crib at the time of create, I wanted to make a floor stand that was free standing and could slide right up to the crib. I also wanted it to be height adjustable.
This whole thing probably could have been made out of PVC with a wood base, but I had some steel around so I made it from metal. Here's the supply and tool list:
Supplies:
- 5' long hollow steel pipe 1" diameter
- 4' long hollow steel pipe 5/8" diameter
- 18" long solid steel rod 3/8" diameter
- 9" x 15" steel plate 1/4" thick
- 2x 22mm bearings
- 1.5"x0.25" eye bolt and nylon lock nut (mobile hangs from this)
- 1"x0.25" bolt and nut (to lock height)
- Cutting oil
- Hacksaw
Tools:
- Drill press with 1", 1/4", and 3/8" metal bits
- MIG welder
- Acetylene torch
- Various clamps and vises
- Various metal working tools (wire cutters, hammers, vice-grips, pliers)
- Safety equipment (safety glasses, mask, gloves, ventilation)
- Angle grinder
I also designed 3D printed a base cap to make the transition from bottom plate to vertical pipe more smooth, a lightning bolt cap for the rotating nut, and corner covers out of flexible TPU filament to avoid stubbed toes in the middle of the night. See the attached files for these modes.
To start, I drilled six 1/4" holes every 6 inches in both the 1" and 5/8" steel pipes. These holes would line up when the 5/8" pipe is placed inside of the 1" pipe and create the adjustable height feature of the stand. I then used the 1" drill bit to drill a hole into the steel plate for the large vertical pipe to nest in.
After all the drilling, I use the MIG welder to weld the 1" pipe to the steel base and the solid rod into the top of the 5/8" pipe. This gave me two parts to the stand:
- a base plate with the 1" pipe welded and extruding from it
- a 5/8" pipe with a solid rod welded into one end and extruding about 17" out of the pipe
Now, using the torch, a vise, and a friend, we slowly and gradually heated the steel rod so it became glowing amber, then gradually began to bed it approaching a soft 90 degree bed. We repeated this processes until the angle was as desired. After bending, we quenched the rod in a bucket of water.
Lastly, I took a 1" tall cut off the of the 5/8" pip and drilled a 3/8" hole into the side of it. I then slid the bent rod through this hole, and welded the ring in place. This is the base that the eye hook will hang through for the mobile. After all the welding is complete, break out that grinder and smooth over your welds! (I had a lot of smoothing to do)
Step 4: Sanding, Priming, and Painting
For the finish, I used a few different method between the 3D models and the metal stand.
3D Models:
I used a water-based paint for each model after gluing any parts that needed to be glued, and drilling all the pilot holes. After crafting a little PVC stand, I worked through painting each model to match the real things portrayed in the Harry Potter Universe. I didn't smooth the models before printing because the high detail that they were printed in left a nice surface for the paint to stick to.
Stand:
The first step in finishing the stand was attach all pieces, which included the base plate weld cover and the bearings. I then sprayed a gray a primer coat using a metal spray paint. After the primer dried, I used bondo to go over all rough welds and transitions between the steel stand the 1" pipe, as well as the 3/8" rod into the 5/8" pipe. Before adding more paint, I sanded down the bondo areas with fine 400 grit sand paper.
I chose to paint the stand white to keep the stand bright to match the light nursery and keep this mobile from looking a little dark and halloween-like. After two coats of flat white, I was happy with the overall appearance and able to glue on the flexible corner feet to the steel stand using the same epoxy used earlier.
Step 5: Lots of Knots and Final Installation
After the paint dried, the last step was to get all the ornaments tied together and hung from the stand. For each knot, I added a dab of fabric glue to seal it permanently. For the ornaments, I used a white string with gold thread laced throughout. The elder wand is actually hanging from nickel wound wire, but the wire is covered in deep red yarn and gold string for appearance purposed.
I ended up having 12 total cords, 3 on each part of the elder wand cross. The outer two cords had three ornaments while the inner most cords only had one. As far as organization goes, each part of the elder wand got a house crest, and a large item (hat, hedwig, snitch, or the time turner), then the brooms, hallows, and keys were scattered throughout.
The wound wire is knotted around the eye bolt, which threads through the bearings on the stand and is secured by a nylon lock nut. This nut is then capped by the lightning bolt topper which is adhered using epoxy. The wire also retains some spring-tension, so you are able to wind the mobile up to have it spin for about 20 minutes or so.
In conclusion, the baby loves it so I would call that a win! Overall I am happy with the appearance, as are the parents. Next step is to wire a quiet and slow turning motor to rotate the mobile automatically.
Thanks for reading!
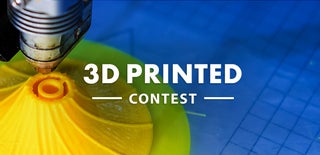
Participated in the
3D Printed Contest